Final report for FNC17-1080
Project Information
I began farming in 1998 after moving here from Washington State. Prior to moving here, I worked for Washington State University for 20 years at an agricultural research station in Puyallup (near Seattle). Our research centered mainly on nitrogen, phosphorus, and heavy metal chemistry in soil, as well as cover cropping. During that time I got my Masters in Soil Science from Washington State University. I currently farm 160 acres in North Central Iowa together with my brother. We use strip tillage/no tillage, intercropping, and cover cropping to grow mainly corn and soybean in rotation. Our farm has seven 3000-bushel grain storage bins all equipped with drying floors, which is an important asset for the proposed project.
Natural air grain drying can be a cheaper alternative to drying corn using LPG but is still energy intensive because of the limited drying season in the fall before declining temperatures prevent ambient air from drying corn to targeted moisture contents. Decreasing airflow rates by extending drying over a longer period in the fall and winter can save substantial amounts of energy for fan operation but can only be done if the drying air is heated to lower the relative humidity enough to meet targeted grain moisture contents. To be economically practical this would require an inexpensive energy source for heating the air. In this project, ground-stored (geothermal) heat was used to modify the drying air temperature and relative humidity to maintain optimum drying conditions throughout an extended drying period. Because ground heat was so inexpensive to deliver to the fan and cutting airflow rate resulted in much smaller fan horsepower requirements drying cost and energy use were substantially reduced. Results of the project were presented in an article published in the January, 2019 newsletter for Iowa State University's Ag Decision Maker website. The successful results of this project can be replicated by farmers that have a good grasp of the principles of low-temperature grain drying.
Cutting drying airflow rates in half and doubling the drying period would move the same volume of air through a grain column but reduce the required fan to only 19% as large and would accomplish drying using about 40% of the energy for fan operation.
Approximate kWh to move the same volume of air at different airflow rates | ||||
cfm/bu | s.p. | h.p. | days | Approx kWh |
0.25 | 0.52 | 0.35 | 210 | 1764 |
0.5 | 1.22 | 1.63 | 105 | 4108 |
0.75 | 2.1 | 4.2 | 70 | 7056 |
1 | 3.13 | 8.35 | 53 | 10621 |
1.25 | 4.3 | 14.36 | 42 | 14475 |
1.5 | 5.62 | 22.49 | 35 | 18892 |
1.75 | 7.06 | 33 | 30 | 23760 |
2 | 8.64 | 46.13 | 26 | 28785 |
During the winter soil temperatures remain warmer than air temperatures and closer to the average annual temperature. In early October air and soil temperatures are very close. But by late December soil temperatures 4 feet below the surface in northern Iowa are 15 to 20 degrees warmer than air temperatures. This project proposed to use ground-stored heat collected by circulating an antifreeze and water solution through buried polypropylene water lines through a heat exchanger in front of the drying fan to maintain optimum drying air conditions throughout a drying period that was extended into the winter for very little additional energy cost for pumping water. The objective was to use ground heat to maintain optimal drying conditions to substantially lower fan operation costs and energy consumption by using a smaller fan during the extended period. The objective of the second year of the project was to further reduce the required fan size by extending the drying season throughout the winter, thereby further decreasing drying cost and energy use.
Average temperature in the fall for Osage and the temperature increase required for relative humidity to decrease enough to equilibrate with 15% and 14% moisture content corn | |||||||
15% | 14% | ||||||
Temp, F | EMC RH | required temp increase | EMC RH | required temp increase | |||
15-Oct | 51 | 67.68 | 1.7 | 61.07 | 5.0 | ||
1-Nov | 43 | 63.84 | 3.6 | 57.31 | 6.8 | ||
15-Nov | 36 | 60.48 | 5.3 | 54.02 | 8.5 | ||
1-Dec | 27 | 56.16 | 7.4 | 49.79 | 10.6 | ||
15-Dec | 20 | 52.8 | 9.1 | 46.5 | 12.3 | ||
1-Jan | 16 | 50.88 | 10.1 | 44.62 | 13.2 | ||
15-Jan | 14 | 49.92 | 10.5 | 43.68 | 13.7 | ||
1-Feb | 16 | 50.88 | 10.1 | 44.62 | 13.2 | ||
15-Feb | 21 | 53.28 | 8.9 | 46.97 | 12.0 | ||
1-Mar | 26 | 55.68 | 7.7 | 49.32 | 10.8 | ||
average | 27 | 7.4 | 10.6 |
Hypothetical drying air temperature increase, based on average air and soil (52" depth) temperatures at Nashua, Iowa over the period 2014 – 2018. The drying air T assumes heat recovery of 40% of the difference between soil T and air T and includes a small increase from fan operation (¾ degree F) | ||||||
period ending | Cumulative days | 50” soil T | ambient air T | difference | Drying air T increase | Drying air T |
29-Oct | 14 | 54.9 | 45.8 | 9.0 | 4.4 | 50.2 |
12-Nov | 28 | 51.1 | 35.0 | 16.1 | 7.2 | 42.2 |
26-Nov | 42 | 46.9 | 29.1 | 17.8 | 7.9 | 37.0 |
10-Dec | 56 | 43.9 | 27.4 | 16.5 | 7.4 | 34.7 |
24-Dec | 70 | 42.4 | 21.4 | 20.9 | 9.1 | 30.6 |
7-Jan | 84 | 39.9 | 10.1 | 29.8 | 12.7 | 22.8 |
21-Jan | 98 | 38.2 | 20.5 | 17.7 | 7.8 | 28.4 |
4-Feb | 112 | 37.6 | 13.9 | 23.7 | 10.2 | 24.1 |
18-Feb | 126 | 36.9 | 21.4 | 15.5 | 6.9 | 28.4 |
25-Feb | 133 | 36.7 | 19.5 | 17.2 | 7.6 | 27.1 |
average | 42.9 | 24.4 | 18.4 | 8.1 | 32.5 | |
* Northeast Iowa Research and Demonstration Farm in Nashua, Iowa | ||||||
** Relative humidity of ambient air during this period would average about 80%. The drying air temperature increase would reduce the relative humidity of the drying air to approximately 57%, which would equilibrate with corn at a moisture content just under 15% |
Cooperators
- (Researcher)
- (Educator)
- (Educator)
Research
System design continued to evolve following submission of the proposal, resulting in some modification of the original plan. Rather than design the entire experiment based on expected results, corn was dried in a single bin to prove the proposed concept was sound and corn could be dried in the manner proposed and in accord with predicted rates and costs. Experience from the initial year would then be used to suggest the most appropriate scenarios and design changes to implement in the second year.
In July, trenches were dug for placement of water lines to a depth of eight feet.
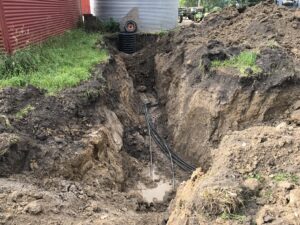
Three 3/4” high density polypropylene water lines were spaced one foot apart in the bottom of the trench. The three water lines made a circuit from the drying bin traveling out in one trench for 400’ and returning in another 400’ trench to make an 800’ loop. At the midway point the lines surfaced into a heated building where both entering and exiting water lines were individually valved before being manifolded together.
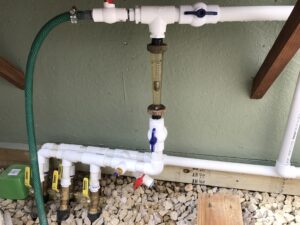
The three-speed circulating pump (Grundfos UPS15 58FC), flow meter, expansion tank, ports for measuring water temperature, and metering ports for adding antifreeze solution (23% propylene glycol) were located there. This was done in order to evaluate the rate of heat recovery and to assess in the future the number of water lines actually required. At the bin, entering and exiting water lines were again manifolded together using heat-fusion couplings before surfacing and passing through a 30” by 30” three-row air-to-water heat exchanger placed in front of a 3/4 horsepower Sukup bin fan.
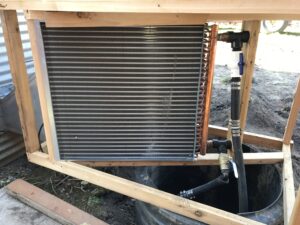
Both the fan and heat exchanger were enclosed in a cabinet and connected to an adjacent open-front building using a thirty-inch diameter corrugated plastic culvert so that incoming air could be filtered to protect the heat exchanger from plugging with dust, leaves, or snow.
The cabinet was wood framed with cedar and skinned with twin-wall polycarbonate and designed to allow for air to bypass the heat exchanger within the cabinet to adjust air temperature without adding unnecessary static pressure which would decrease airflow. Temperature ports were placed where water entered and exited the heat exchanger to track ground heat supplied to the air stream. Incoming air temperature and plenum air temperature at the drying floor entrance were also tracked. A manometer was used to measure static pressure under the drying floor to gage airflow using the fan performance specifications. A watt-meter was used to measure electricity consumption rates for the circulating pump (87 watts) and drying fan (680 watts).
In the first year of the trial an 18' diameter bin was filled to a depth of 13' (approximately 2650 bushels) with corn (20.4% moisture content). The fan was started November 5th, and the heat exchanger employed beginning November 16th. A manometer measured about 0.7" water corresponding to an estimated airflow of 1550 cfm. The air temperature increase due to the fan motor operation was calculated to be about 1.25 degrees F. The remainder was from ground heat. The water flow rate was 6.3 gpm. Water and air temperatures entering and exiting the heat exchanger were measured almost daily and over a broad range of temperatures. The relationship (analyzed by regression analysis) between the measured drop in water temperature as it passed through the heat exchanger and the corresponding air temperature increase was used to calculate an average temperature increase of drying air throughout the drying period based on ambient air temperatures measured by the National Weather Service for our location. Ground temperatures (and water temperature entering the heat exchanger) declined over the course of the drying period. So the above relationships were determined in two-week intervals. The slopes of the regression curves changed slightly with time. The equations appropriate for each period were used to calculate drying air temperature increases from climatology data. As the end of the projected drying period approached, periodic sampling of grain at different depths from the top of the grain column were obtained to track the drying front.
Drying was continuous for the most part during the first year. However, there were two periods of interruption for cold weather. When extremely cold temperatures were encountered by the relatively warm and moist air exhausting from the grain at the top of the bin, frost accumulated to the extent that ventilation pathways were becoming completely iced shut and an ice layer on the surface of the grain began to form.
Twice during the drying period the fan was shut off because of temperatures falling below zero. The two periods were each six days in length. Opening the larger doors on top of the bin would allow ventilation when the vents frost over but would exacerbate the problem of cold air creating an ice skin on the surface of the grain that blocks air flow. This is a significant problem that needs to be addressed, although in this case it was fairly easily solved by turning the fan off during these periods.
The drying period was between 11/05/17 until 01/29/18, 85 days. With the interruptions for cold weather there were actually 74 days of fan operation, with an average ambient temperature of 25.1 F. Although the interruptible power rate was used to calculate cost, which would have required shutting power off for up to four hours per day, fan and pump operation was continuous because the small cost of drying in this trial did not warrant the monthly charge for separate metering and control of power supply. Interruption of power would have extended the drying period accordingly, from 74 days (24 hr/day) to 89 days (20 hr/day) but would have had little impact on trial results.
The conclusions after the first year of drying were that drying could be continued not just into the winter but throughout the winter into the spring and that better fan selection for the static pressure at the desired airflow rate could further reduce energy costs for drying. A quarter hp fan (Cincinnati Fan Company, 309 watts as measured by a watt meter) was purchased to replace the larger fan (680 watt) used during the first year, and a second heat exchanger was added to increase heat extraction from the ground loop, which made it possible to decrease the water flow rate by turning the circulating pump from high (87 watts) to low (60 watts). (It should be emphasized that the smaller fan was not necessarily more efficient than the larger fan, just a better match for the application. At 0.5" static pressure the smaller fan can move about 80% of the air volume the larger fan moves, but at 1.5" the larger fan's airflow rate would be over four times that of the smaller fan.) The new fan and heat exchangers were also relocated so that the duct elbow was further from the fan, in response to duct layout recommendations that placed elbows no closer than 30" from the fan in order to optimize airflow through the fan.
On November 6 the bin was filled to a depth of about 15' with corn (about 3000 bu) that averaged 18.7% moisture content. The manometer measured a combined positive and negative static pressure of about 0.5" water, corresponding to an airflow rate of about 1100 cfm. The fan was estimated to contribute about 0.75 F to the air stream temperature. Operating the circulating pump on low resulted in a water flow rate of 3.8 gpm. Entering and exiting water temperatures were recorded for both heat exchangers in order to calculate ground heat flux to the air stream. Fan operation was controlled manually to exclude periods that were too warm (upper 30s F) or too cold (below 0 F). Drying was terminated March 12, and the corn was hauled to the elevator for an accurate measure of bushels and moisture content. The ambient air temperatures during the time the fan operated was 21.4 F.
Delivering ground heat to the dryer air stream was even less expensive than it was projected to be. During the first year of the trial heat supplied by the fan together with ground heat increased drying air temperatures an average of 7 degrees F. Ground-heat provided about 32 million BTUs over the drying period using a quantity of electricity for the pump (136 kWh) that alone would have supplied only 0.463 million BTUs (1.4% of the heat provided). The ground-heat supplied to the air stream was estimated to cost 2% of what it would have cost using LP (assuming an electricity rate of $0.064 cents/kWh and 383 gallons of LP at a cost of $1.25/gal). Electricity used by the fan (680 watts) was by far the greatest fraction of the energy used.
Another surprise was how far into the winter drying is possible in this manner. Since the difference between air temperature and soil temperature becomes bigger as winter progresses, winter is even more optimal for drying in this manner than fall. By the end of January ground temperatures as measured at the heat exchanger inlet had declined about 12 degrees F since the start of the drying period, but the drying airstream temperature could still be increased 10 degrees F on a day of average temperature.
After the first year the corn was hauled to the local elevator in early March. Below the drying front the measured moisture content was 14.4%. Because the drying front had not completely moved through the top of the grain mass the overall average moisture content of the corn was 15.0%. There was a total of 2659 bushels. The energy cost of drying was determined by multiplying the kilowatt-hours used (1356 kWh) times the local electricity rate ($0.064/kWh for the interruptible rate). The cost for electricity used by the fan and pump was $85. The energy cost for drying was $0.006/point of moisture removed. For comparison, LP drying at $1.25/gal LP would cost $0.0275/point of moisture from each bushel.
The drying period in the second year of the experiment was 127 days, with an average temperature of 17.8 F. The fan operated only 90 days during this period, mainly because of extremely cold weather. Average air temperature during the time the fan operated was 21.4 F. An unanticipated problem developed as a result of a power interruption resulting in freezing in the heat exchangers before power was restored. The extended cold period without a good means of artificially heating the exposed components of the ground loop resulted in more down time of the system than would have been necessary based simply on extremely cold temperatures. (Better enclosure to allow artificial heating or perhaps a solar operated pump to ensure continuous pump operation even during power outages would be a good idea.) The drying period was terminated earlier than desirable (March 12) because of a warm extended forecast. The average temperature increase from ground heat was 9.2 F. As determined after hauling the corn to the elevator, there were 2930 bu of corn averaging 15.3% moisture content. The drying front was evident in the upper third of the bin. The dried corn in the lower part of the bin averaged 14.4% moisture content. The average BTU/hr value from ground heat was 12,144, requiring only 60 watts costing $0.0038 using $0.064/kWh electricity. This is equivalent to $0.181 worth of LP using LP at $1.25/gal but costing only 2.1% as much.
The ability to use climate normals for air temperature and relative humidity, fan performance specifications, and psychrometric equations or graphs to predict costs, energy use, and rates of drying under different drying scenarios has been corroborated in this experiment. Air volumes and time requirements for drying were initially estimated using psychrometric and climate data for the appropriate time periods. The close correspondence between estimated and measured time needed for drying provides a basis for cost comparisons under different methods and exploring different scenarios.
For the second year of the trial, the cost of drying was anticipated to be reduced from $0.006/point used in this years trial to $0.0031/point of moisture removed from each bushel. The beginning corn moisture content in the second year was 18.7% rather than 20.4% as in the first year. Although a smaller air volume is required to dry fewer points of moisture from corn, at this moisture content a higher air volume/point of moisture is required because the drying air removes less water per volume of air. In addition, the deeper grain column in the second year made drying somewhat more energy intensive by comparison with the first year since fan horsepower requirements increase exponentially as depth and static pressure increase. So although the anticipated cost reduction after the first year to $0.0031/point was not achieved, the cost was reduced to $0.0051/point and would have been close to the anticipated cost given the same corn moisture content, depth, and climatic conditions as in the first year.
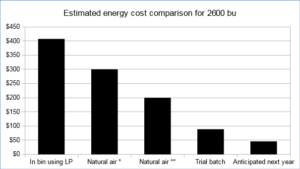
Educational & Outreach Activities
Participation Summary:
A suggestion was made by Ann Johanns, Iowa State University Extension Program Specialist that I write an article for the Ag Decision Maker Website monthly newsletter (an Iowa State University publication). The article I wrote, Rethinking Corn Drying: Drying Throughout the Winter Using Ground-Stored Heat; A Summary of On-Farm Research Funded by USDA-SARE, appeared in the January 2019 newsletter (https://www.extension.iastate.edu/agdm/articles/others/JelJan19.html) as one of the two articles for that month. She indicated that the newsletter went out to 8,125 email recipients. Someone who read the article passed the information on to the Executive Director of the Iowa Geothermal Association, resulting in an invitation from them to give a presentation on the project at their Annual Meeting in Des Moines March 12. The presentation sparked a lively discussion with a group that was very knowledgeable about geothermal energy use for heating and now is aware of the potential for grain drying. Currently, the project has caught the attention of and elicited a contact from the Director of the Economic Development Council for Mitchell County, Iowa. I am in the process of following up on that contact.
Learning Outcomes
The bottom line lesson from this research is that corn can be dried in the manner demonstrated with much less energy use and at lower cost than it is when dried conventionally. A small farm like ours can make best use of this concept since savings are proportional to grain depth and bin size, the smaller the better. The disadvantage of implementing this research into practice too soon is that I am still on the steep part of the learning curve. Improvements in design of systems that implement the concept could be rapid as research continues. Waiting a while might be worthwhile. On the other hand, those farmers that have already had similar ideas might include these results to forge their own versions of the concept. I am impressed as I visit with farmers individually how much ingenuity there is among them that doesn't usually see the light of day. At this stage in the research I would expect that the synergy of thinking resulting from exposure of this research to other farmers of like mind could advance the application of the idea.
Project Outcomes
After years of cloistered rumination and calculation this SARE grant has allowed me to test my calculated conclusions in reality. The article I wrote for the Ag Decision Maker newsletter exposed the concept for drying corn to over 8,000 people resulting the invitation to the Iowa Geothermal Association Annual Meeting to present the project, and now the Director of the Mitchell County Economic Development Council is anxious to visit with me. The idea is getting exposure. Although this concept is a marriage of two sets of well-established principles and practices, that for low-temperature grain drying and that for geothermal heating, it is the marriage that is unique. Widespread adoption is not likely to happen unless agricultural professionals have digested the concept and given it tacit approval. It seems to be embarked on that path now.
I did not attempt the estimate of capital cost promised initially. Although I know what the ground loop installation cost, I do not know yet how many bushels of corn that size loop will dry since the one I installed is oversized for the size bin connected to it. I felt it was better to ensure that it was large enough to provide proof of the drying concept efficacy first. So I installed it 8' deep instead of shallower, which would have been less expensive to install but would have cooled faster. And I made an 800' loop, equivalent to a ground loop for a 3-ton heat pump system, instead of shorter for the same reason. I feel fairly safe in estimating that capital cost should be less than $2/bu, mainly for the ground loop, which should have a lifespan of 50 to 100 years. My feeling is that I reduced soil temperatures only a little compared to ambient cooling from the soil surface, which also makes me think it was quite oversized. In short, it will take more work to establish capital cost/bu.
The second heat exchanger that was used during the second year of the experiment was eye opening. As expected, the cold air hitting the first heat exchanger had the biggest impact on water temperature in the heat exchanger. But the water temperature in the second heat exchanger was reduced an average 77% of the reduction in the first. With only a small contribution to static pressure, it makes me wonder what the heat recovery and temperature elevation would be if several more heat exchangers were included in the stack. Along with higher water flow rate this could make it possible to get the desired temperature increase of drying air with a smaller spread in ambient air and ground temperatures.
Making use of solar energy for heating air, especially late in the winter and early spring when solar energy is more available, and reheating or superheating the ground during the summer for use in the fall seems to have a lot of potential as well. But cost analysis is necessary for this as well.
Also, since cost and energy benefits are inversely proportional to grain depth, the research as reported in this project is more beneficial to small farmers. But shallow grain columns could be used by any size farmer if the concept was applied to flow-through dryers. This might involve bypassing a high-capacity dryer in the fall and putting wet corn up to 20% moisture (perhaps up to 22%) directly into storage after harvest with airflow to chill it, then cycling through a dryer that operated throughout the winter at low temperature and airflow rate. Although this would require more grain conveyance during the winter it would minimize energy cost for fan operation since the grain depth would be less than six feet, and the harvest pace would not be impeded by the need to dry the grain in the fall.
All this to say that this is results driven research that is in its infancy. It has been very successful but has not reached its full potential yet.