Final report for FNC17-1091
Project Information
Black Cat Farmstead: Raising primarily wool sheep for textile use, with an ongoing research project related to flax for textile use. Typical flock size about 60, rotationally grazed on permanent pasture, with hay production on approximately 5 acres.
A to Z Produce and Bakery: organic vegetable and small grain production in Stockholm, Wisconsin for the past twenty-five years. Approximately 1/2 acre of textile flax was grown on the farm in 2017, with a similar planting planned for 2018.
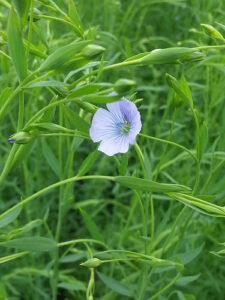
Can new technology revive an ancient textile fiber? Our project explored the feasibility of developing a small-scale, local linen industry. Over two years, we grew textile flax as part of the rotational plan on a diversified organic farm in western Wisconsin. Working in partnership with Taproot Fibre Lab in Port Williams, Nova Scotia and their newly-developed mechanical processing equipment, we turned retted flax straw into salable flax and linen products: long-stapled line flax fiber for handspinning, short-stapled tow fiber and roving for spinning, fiber blending, and papermaking, and tow linen yarns.
Linen is an ancient textile material, cultivated for more than 10,000 years. Cloth made from flax – linen – is an extraordinarily long-lasting and high-quality textile. Immigrants to the upper Midwest brought flax-growing knowledge and the tools for working flax into linen with them when they arrived here in the 19th century, but a local linen industry never took hold; flax is time-consuming to harvest and process, and cotton became the dominant plant-based textile fiber in the United States. Today, cotton and all other natural fibers represent a smaller and smaller percentage of global textile production; replaced by synthetic, petroleum-based cloth. Even so, interest in “local linen” is strong among hand spinners, knitters, weavers, and papermakers in our region. Many people have come to recognize the importance of developing (or rediscovering) options for locally-grown and processed textile materials. Flax was part of a traditional crop rotation in generations past. It grows well in our region without significant inputs, and has the potential to be a locally-grown, sustainable textile crop. Linen cloth is durable, beautiful, and versatile. Flax fiber is a primary ingredient in many high-quality handmade papers, and is valued for its strength and durability.
At this time, there is no industrial-scale or small-scale infrastructure for processing flax straw into finished linen products in the upper Midwest or the US more broadly. Very little textile flax is grown in the upper Midwest at this time, and the crop is often unfamiliar both to local farmers and to hand spinners, and other fiber artists. The small number of people who do grow textile flax are limited in their production capability by having to hand-harvest and hand-process their crop using the same simple tools their ancestors would have employed centuries ago. The lack of processing infrastructure prevents fiber flax from being grown at anything but a very small experimental scale. Lack of processing machinery has been a significant obstacle to the creation (or revival) of flax growing in our region. However, new developments in small-scale processing machinery present the potential to bring local linen production to our region. We believe that our project, using this newly developed processing machinery, demonstrates the viability of flax as a local textile fiber crop.
Our project began to explore the elements of a system of growers and potential end-users who were part of the “ecosystem” of creating a local linen infrastructure in our area. We successfully demonstrated that textile flax production can be incorporated within the existing planting regime of a small, diversified farm, and that production can be scaled to the capacity of a cottage-industry-scaled mill of the type developed by Taproot Fibre Lab. Working with the machinery developed by Taproot, the textile flax we grew was processed into a variety of value-added products which were marketed to end users who used the material in papermaking, handspinning, weaving, and knitting projects.
Our team grew a modest amount of flax; one half acre in 2017 and 2018. Working in collaboration with Taproot, approximately half of our 2017 crop was transported to Taproot's site in Nova Scotia for processing. The processed flax fiber was used for a variety of purposes; primarily handspinning, weaving, and papermaking. The purpose of the project was twofold; to demonstrate that flax can fit into an existing organic rotation on a diversified farm, and to show that flax and linen products can be produced here for a regional/national market.
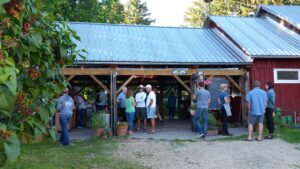
Our project emphasized robust outreach to educate the public and potential end users about flax production, processing, and its potential for this area. Outreach was accomplished digitally, using our websites and social media platforms, and in-person, through presentations at regional events focused on agriculture and local fiber/textile production, and regional history.
This project was intended to begin a process exploring the feasibility of building a local linen mill in our area using Taproot's machinery.
Research
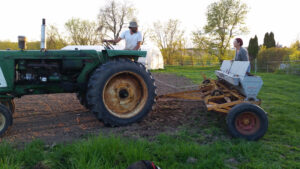
Two, ¼-acre adjoining fields, 3a and 3b, were chosen for planting three varieties of Belgian flax; Melina, Calista, and Vesta, at a seeding rate of 60 pounds/acre. All three varieties were planted in each section. In 2016, 3a had been used for sweet corn, peanuts and summer squash. It had an over-wintered crop of crimson clover. 3b was in white clover and had been grazed in 2016. We treated the textile flax like any small grain. It was planted in the first week of May; a bit later than we would have liked because shipment of our seed was delayed.
We grew the same cultivars Taproot grew in 2017, and ordered our seed through them. We discovered that the seed, because it was shipped first to Canada, required a second round of sanitary certification. Several weeks passed while the seed was inspected and a Canadian phytosanitary certificate was issued. To avoid the potential for this issue arising in 2018, we ordered our second year seed early; a Dutch cultivar called “Avian.”.
Sourcing textile flax seed in the US is challenging. The most commonly available cultivar is “Marilyn.” We were pleased to be able to try new cultivars as part of our project, and to see how each performed during the 2017 and 2018 growing seasons.
While we definitely had favorites among the cultivars grown, weather/growing conditions proved to be the strongest determiner of flax quality and yield over the two years of the project. Vesta yielded the finest fiber, but was most prone to lodging. Melina grew well and resisted lodging, but was the most coarse of the three. Calista fell somewhere between the two. A 2017 test plot of Avian was similar in height, yield and texture to the others grown in 2017. Growing conditions in the first year of our project were excellent for textile flax production; although our crop was planted somewhat later than we'd wished, spring rainfall permitted strong, even germination of our crop, and conditions for harvesting, retting, and storage at the end of the growing season were ideal.
The 2018 growing season could not be in greater contrast to the 2017 season. An April 15th blizzard dumped 11.5” of snow that kept us from getting into our fields until April 25th for our first tillage. Though we planted flax on May 7th, we were unable to do the multiple rounds of pre-tillage that gave us such a lovely seed bed in ’17. All the moisture from a winter of snow quickly dissipated as we received only 1.95 inches of rain in May mostly as one rain and 8 straight days over 85 degrees. Not the kind of weather that favors small grains that like a cool start! June followed with no rain until the 16th and then a deluge for two days with very little rain to follow. Our flax germinated unevenly and the under seeding of clover never really got a foothold. As the flax germinated unevenly, so it grew unevenly and flowered unevenly. Even the tallest of “Avian,” the Dutch cultivar we grew in 2018, did not meet our shortest “Mellina” from 2017.
Since the under-seeded clover never took off, warm season weeds got a hold in between rows. This certainly affected the ease, quality and quantity of harvest. As a vegetable grower, flax presents the challenge of harvest at a very busy time of year. At the time of harvest, our 2018 crop was noticeably thinner (both in the number of plants per square foot and the diameters of individual stalks), weaker, and had fewer seed heads. Many seeds germinated quite late, and short, immature flax plants were visible in the understory as we hand-pulled the 2018 crop. Our total yield was approximtely half of that in 2017. While this was disappointing from a production standpoint, it was very useful to see how dramatically different growing conditions affected our yield.
In 2019 we plan to plant a relatively small plot (Robbi plans to process her flax by hand, start to finish. Andrea will send some of her 2019 crop to Taproot for processing, and keep some for use in teaching). Robbi could envision growing textile flax for other spinners with an interest in hand processing. We suspect that a locally-grown fiber market will take off in coming years, led by people growing hemp, and that the hemp industry will jump start innovation in both harvesting equipment and processing equipment that could be used for both fibers.
Detailed timeline of 2017 growing season:
4/9/17 Dug fields with a field digger.
4/23/17 Second digging.
5/4/17 Third digging before planting
5/5/17 Planted 15ft swath of each variety with a 10ft grain drill. Under-seeded with white clover
6/23-30/17 Flax in FULL Bloom
7/5/17 A sea of green seed heads
7/6/17 Tried cutting flax with a swather used for small grains; it cut well, but the flax was immature at 60+ days.
7/17/17 Melina flax (the earliest-maturing of the three cultivars grown) leaves yellowing about 50 percent. We attempted to cut the flax with the swather, but it totally bogged down and it became clear we will have to hand pull to harvest the crop.
7/17/17 Start pulling with a crew of 4 for an hour just to get an idea of time. As it is harvested, the flax is laid on the ground in orderly rows and the process of dew retting begins.
7/18/17 Stan and Andrea pull Tuesday night for 3 hours and get the first 5 ft swath down.
7/23/17 Group of 10 volunteers pull for 2 hours.
7/26/17 Group of 6 students from Macalester College in St Paul pull flax for 1 hour after a large rain event, leaving large clods of mud on the flax roots.
7/27-8/4 Pulling, pulling, pulling Robbi, Stan, Andrea.
8//5/17 All flax from 3b pulled and on the ground. Flax in plot 3a was abandoned (see RESULTS and DISCUSSION for additional notes).
8/5-19/17 During the dew retting process, the flax is turned over as deemed necessary to facilitate an even breakdown of the stalks. When retting appears to be adequately advanced, the Flax is turned one last time, and bundled when it is as dry as possible.
8/20/17 Last bundles of retted flax straw tied and stored out of the weather.
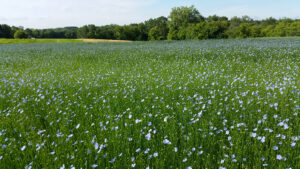
We planted the flax a little later than we might have liked, but there may have been some weed control advantage in the multiple cultivations which were done while we waited for the seed to arrive. We certainly would not want to plant any later as that would push harvest into September, when the days are too short for efficient dew retting and drying. May 1st might be a good target date in our area.
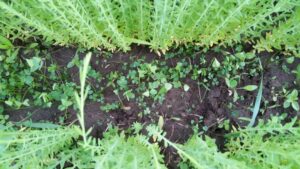
Under-seeding our flax with white clover worked beautifully. This may not be surprising as that is what you would do with wheat or oats, but the clover took a lot of abuse walking on it, pulling the flax roots around it, and then laying the flax on top of it.
As the flax matured, was pulled, retted and bundled, Andrea was our main counsel. She has grown small plots for several years and directed us on the process of harvesting. Each variety of flax was pulled as it matured. It was a pretty seamless succession over 2 weeks. We would just finish up one and it would be time to start the next. We began on section 3b because it was the most weed-free across all varieties.
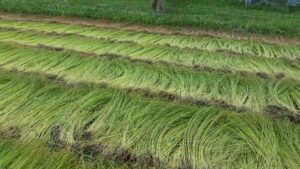
Judging the completion of retting is tricky. Sometimes it was really obvious and sometimes less clear. Impending weather would push us to bundle flax for fear of over-retting. By the end of August there was a small window during the middle of the day when the flax was dry from morning dew and before the afternoon dampness began. Noon to 2pm became the magic hours for bundling and storing. The flax we sent to Taproot for processing included straw that was somewhat under-retted, some that was very well-prepared for processing, and a limited amount that was over-retted. We intentionally included these retting variations in the material we sent to the mill, so that we could get a sense of how the machines handled straw of different qualities. In general, the machines encounter the same concerns a human processing flax by hand does in this situation: under-retted flax was more difficult to clean, over-retted flax generated large quantities of tow and little line, and well-retted straw yielded the best quality fiber; of maximum length, shine, fineness, and strength.
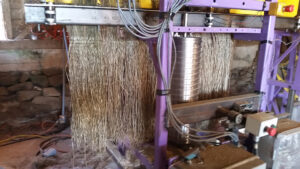
One advantage of the machines over a human flax dresser: mechanical processing equipment doesn’t tire, and can break, scutch and hackle as long as necessary to remove the boon/shive (the pithy core of the flax stalk) and comb the fiber into usable condition.
We were not able to harvest all the flax that we planted. Section 3a had multiple problems. A significant amount of the flax in this plot (mostly Vesta, the tallest and latest-maturing of our three cultivars) lodged under heavy rains before it matured to the point it could be harvested. Part of the section 3a (Melina, the earliest-maturing of our three cultivars) was pulled when the ground was too wet from a large rain event. Muddy roots dried to muddy clods which were time-consuming to bundle, and sanitary concerns demanded that the clods of dirt be removed before the straw was transported to the mill. Weed pressure from lambsquarters in late-maturing cultivar forced us to roll the crop down before the weed seed matured.
Time constraints and a lack of hands to pull flax kept us from harvesting some of the flax in 3a when it was at an ideal state of maturity. There came a moment when it just became clear that we could harvest ALL of 3b or parts of both, and we chose to gather all of 3b.
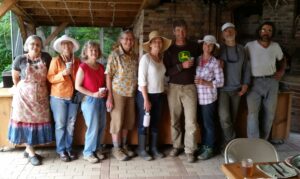
Even though Ted and Robbi do lots of hand work with vegetable crops at A to Z, they were not prepared for how much time it would take to harvest the flax by hand. We had two work days with volunteers, an hour or two at a time. The rest was pulled a couple hours here, a couple hours there until it all got out. Andrea pulled on Pizza Nights in order to engage the public. Both Andrea and Stan pulled multiple other times. Ted pulled some, but Robbi did the majority of pulling and was not prepared for how physically arduous the work is when done at the scale we planted. If flax was going to go into a long term rotation at A to Z, finding a a way to harvest mechanically (perhaps by building a puller) would become a high priority.
The section of 3a that did not get fully harvested was a useful control. One part was left to fully mature the seeds. We harvested that seed and then mowed the area. As one might imagine given the fiberous nature of the flax stalks, it is not easy to mow, leaving behind a tangle of fiber. We did graze sheep on it after it was mown, and the animals were able to disrupt it, but there was certainly material there going into winter. We’ll see in the spring what it is like to incorporate. The portion of plot 3a that we pulled and left lay on the ground served as a useful reference to understand what true over-retting looks and feels like. The lodged and mown flax was still there when winter came and it will be interesting to see what is left in the spring. We expect that nearly eight months of what amounts to a natural process of over-retting will have significantly broken down the fiber. The weedy mess of 3a that was grazed and mowed will be cover cropped in 2018. Though the whole section was under-seeded in white clover, the fact that it wasn’t harvested really kept that clover from flourishing.
Section 3b did have a small area that lodged, but overall looked good all season. The clover under-seeding did just great. As we were pulling it didn’t look like much but it really took off even as the flax was laying on the ground and we did graze it in September. As was noted in the beginning of this part of the report, 3a had been used for sweet corn, peanuts and summer squash. It had an over-wintered crop of crimson clover. 3b was in white clover and had been grazed in 2016. 3b was by far the better of our two plots in 2017, suggesting that a rotation from white clover and grazing to flax might produce a better yield than going from a vegetable crop to flax.
And lastly, perhaps 1/2 acre is too much to harvest inside a very busy time of year on a vegetable farm, unless provisions are made to recruit additional hands at harvest time, or a means of mechanical harvest is devised. We decided to plant a somewhat smaller area in 2018 - approximately 1/4 acre, hoping that we would be more easily able to harvest all of the crop. Growing conditions were much less conducive to good flax in our second year, and our yield was lower.
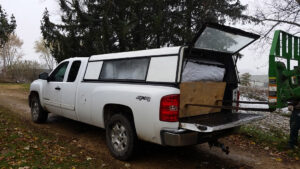
We harvested approximately 1,200 pounds of flax straw from the area we planted in 2017. We were able to carry 480 pounds of retted flax straw to Taproot in the back of the Black Cat Farmstead pickup truck, packed in three bulk storage totes. This retted straw yielded 65 pounds of line flax and fine tow, with an additional 100+ pounds of rough tow fiber left behind at Taproot’s mill for additional processing into clean, picked tow, tow roving, and mill spun tow linen yarn. We have retted flax harvested in 2018 in storage which has not yet been sent to the mill for processing.
The line flax we processed in Nova Scotia is suitable for hand spinning into linen yarn/thread for weaving or knitting. The very long staple length of these fibers (30”+ in our crop; Taproot's engineer was quite complimentary of length and quality of our fiber) precludes their use in a mechanical spinning frame designed for shorter-stapled fibers like wool.
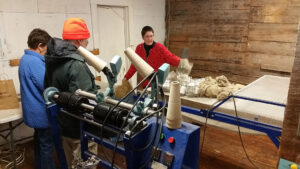
Tow flax fiber, the shorter, more irregular fibers generated during the processing of line flax, were processed into roving and mechanically spun into town linen yarn. The tow roving can also be hand spun, or the clean tow fiber can be used in papermaking, or blended with other fibers for handspinning.
The line flax, picked tow, tow roving, and millspun tow line yarn processed by Taproot were packaged by Andrea and sold at regional fiber festivals, art fairs, at a local gallery and were available online via Etsy. Tow roving sold briskly to handspinners, at both in-person venues and online. Line flax (bundled as traditional flax "strick") also sold well. The millspun tow linen yarn was less readily embraced by end users. Samples were provided to a regional production weaver and a machine knitter to use in their projects. Andrea warped and wove yardage using the tow linen yarn spun at Taproot. Taproot's spinning equipment (manufactured by Belfast Mini Mills on Prince Edward Island) was not adaptable to spinning of fine line flax, and their tow linen singles in 2018 were somewhat coarse and irregular. While this yarn softens substantially after washing, its handle is somewhat unappealing in its raw state. As we complete this final report, Taproot is in the process of installing new spinning equipment, which they hope will permit wet line spinning at their facility.
The flax we made available for sale as part of the project was priced in a manner that did not appropriately reflect its cost of production. Similar line flax, grown overseas, mechanically prepared, and imported to the US, is generally priced at $4/ounce. We priced our locally-grown, organic flax fiber at $5/ounce. Picked tow and tow roving were priced at $4/ounce, and mill spun tow linen yarn was priced at $24 for a 200 yard skein. In November of 2017, our truckload of approximately 480 pounds of flax straw represented Taproot's first custom processing order, and both we and Patricia used the work as a learning opportunity. Our total processing fees paid ($3,250), fell short of Taproot's actual cost of production. We paid approximately $30/pound for processing, but Taproot's actual processing costs were significantly higher than this. Patricia and the staff at Taproot are working to make their machinery, work flow, and facility more efficient, and our expectation is that processing costs will drop as their mill equipment moves from a research to a production footing.
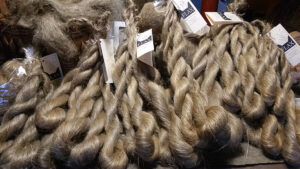
We documented our trip to Taproot and the processing of the flax on our farm Facebook page. During our time in Canada, our academic partner, Mary Hark, traveled to Nova Scotia and held a papermaking workshop for thirteen participants from both the US and Canada, at Taproot, using flax fiber and other plant materials to make a variety of handmade papers.
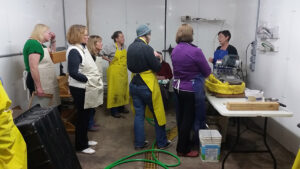
The workshop highlighted the variety of uses for flax fiber and generated a lot of interest in the project on the part of hand papermakers across the US, who have expressed interest in purchasing domestically-sourced tow fiber as soon as it is commercially available. We are scheduling a similar workshop to take place here in Wisconsin during 2018.
Our trip to Taproot’s mill in Port Williams represented their first custom processing order. As Taproot shifts their focus from the design and prototyping of their machinery to building both the machines for sale and producing flax and linen items, they are now creating the larger organization of the machines, training staff to operate them, and hiring a manager to run the adjacent carding and spinning mill. When we arrived in Nova Scotia, the machines were freshly-installed in what will become Taproot’s primary processing facility. New walls were literally being built around us as we worked to process the straw from our 2017 crop! We look forward to seeing the results of the additional processing work we will have done in 2019.
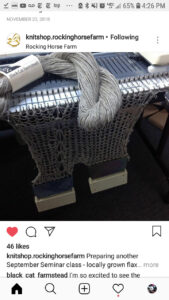
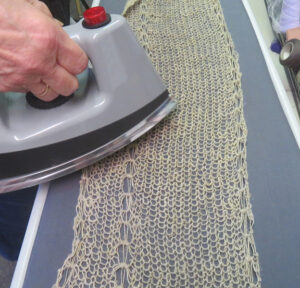
During 2018, our outreach included working with a regional machine-knitting designer, Jason Wurst, who used skeins of our organic tow linen yarn to produce a machine knit cowl. He featured our local linen yarn in a seminar in his classroom and featured the work on his social media feed and newsletter. Marian Dahlberg, a local production weaver who works in linen, producing high-end household linens (luxury kitchen and bath towels), also has samples of our tow linen yarn she will be using in upcoming weaving projects.
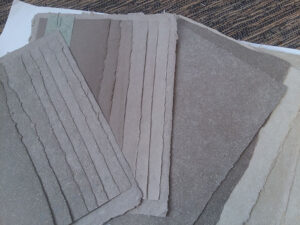
Mary Hark created a series of handmade papers using flax fiber from both Black Cat Farmstead and Taproot Fiber Lab, creating a variety of colors and textures:
At Black Cat Farmstead, we used millspun tow linen and handspun line linen from the project in weaving projects on both a 4-shaft counterbalance loom and a drawloom. The tow linen yarn was very strong, and yielded a heavy, highly textured cloth:
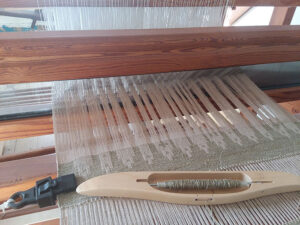
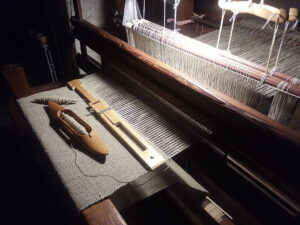
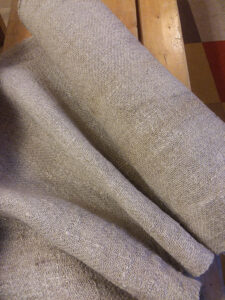
Educational & Outreach Activities
Participation Summary:
Education and outreach activities through 2017 included:
March 2017: Presentation of a project overview to the Lake Pepin Local Food Group, Stockholm, Wisconsin.
April 2017: Presentation of the project and an introduction to linen production to a tour group from the Minnesota Textile Center visiting Stockholm, WI.
May, 2017: Presentation of the project and an introduction to flax and linen processing via demonstrations at the Shepherds Harvest Festival over Mothers Day weekend.
May 2017: installation of informational signage about the project at both of our planting sites: Black Cat Farmstead Fiber Studio, and A to Z produce and Bakery, Stockholm, WI.
June 2017: Tours at Black Cat and at A to Z, with papermaker Mary Hark, during the flax blossom time, are shared on social media.
July 2017: Information about the project is shared at our booth during the Stockholm Art Fair, and in demonstrations at Nordic Fest in Decorah, Iowa. Our first field day is held in late August, with 14 participants who came to learn about the project and help with the harvest. A group of approximately 12 students from Macalester also visit during this time and help to harvest flax.
July-August 2017: Harvest takes place from late July to early August, followed by retting. I did a lot of my harvesting and other field work on Tuesday afternoons/evenings so that I could interact with people visiting A to Z for Tuesday night pizza. The project was visible to many hundreds of visitors during that time, and I spoke with dozens of people on those evenings. A few even wanted to jump in and try harvesting some flax themselves.
October 2017: The project is presented at our local public high school by our daughter. Our preparations for the trip to Canada are documented on Social Media. We present the project during the Fall Art Tour and the North Star Farm Tour, two regional events which drew approximately 500 people to our farm over 2 weekends.
November 2017: The processing trip to Taproot is documented on Social Media. Mary Hark joins us in Nova Scotia for a papermaking workshop at Taproot with thirteen attendees from Canada and the US.
December 2017: An open house at the Back Cat Fiber studio draws 40 people from the Minnesota Weavers Guild to learn more about the project, and generates a contact list of 40+ people interested in staying informed about the project and assisting in 2018.
January 2018: Presentation about Flax to an audience of 78 people at Livsreise, the Norwegian Heritage Center in Stoughton, WI.
2018 activities:
February 2018: presentation of the project as part of the annual fiber celebration at the Chippewa Valley Museum, Eau Claire, WI, and a one-day workshop at our local school via our community education program (my 15-year-old daughter also presented the project to her high school class).
March 2018: I joined Patricia Bishop of Taproot Fibre Lab at her informational booth at an industrial hemp conference in Madison, WI, and met with her and members of the School of Human Ecology and Engineering faculties at UW-Madison to discuss the project.
April 2018: Presentation of the project to multiple groups at UW-Madison, with Mary Hark (presented to Mary's classes, and gave a speech to an audience from the School of Human Ecology and Engineering departments).
April 2018: travel to Livsreise - Norwegian Heritage Center, Stoughton, WI. Presentation of the project in a historical context, with a discussion of the tradition of flax production among immigrant communities from Scandinavia in the upper Midwest during the late 19th century.
May 2018: Presented the project at the 21st annual Shepherds Harvest Festival in Lake Elmo, MN
July 2018: the project was presented at the Stockholm Art Fair, Stockholm, WI.
August 2018: Flax class taught at the Vesterheim Museum in Decorah IA, which included a presentation of the SARE project.
September 2018: The project was presented at the Laura Ingalls Wilder Days festival in Pepin, Wisconsin.
October 2018: The project was presented at the regional Fall Art Tour and the North Star Farm Tour.
In 2018 we documented the project at each of our sites in a similar manner to 2017, with field signage, information on our websites and social media, and one-on-one interactions with visitors to our sites. These listings represent formal presentations of the project. Many hundreds of informal interactions and conversations about the SARE grant took place over the course of the project. Our posts about the project on the Black Cat Farmstead Facebook page routinely engage 500+ people.
Learning Outcomes
At the conclusion of this project, we are taking stock of what we've learned. We successfully grew and harvested a beautiful crop of textile flax. The depth of experience Ted and Robbi brought to the project was key to the success of our harvest in 2017 and 2018. The amount of handwork the flax required was significantly more than expected because we were not able to mechanically harvest our crop, and had to rely instead on hand labor to manually pull the flax, as people have done for millennia. Taproot's machinery is beginning to overcome the technological hurdles which have held back small-scale flax production, but in many ways, the work we did in Wisconsin and Canada simply opens the door to new questions and challenges in all aspects of production of local textile fibers.
The machinery at Taproot, while filled with promise, is still in its infancy. The ripple, break, scutch, and hackle which comprise their line yield a beautiful line flax suitable for hand spinning. Taproot's mill equipment produces high-quality line flax fiber, clean, picked tow (for spinning or papermaking), and tow roving, all of which found eager buyers in both regional and national markets via in-person and online sales. Tow linen yarn was produced, and the quality and variety of linen yarn being spun at Taproot will likely improve with new spinning equipment presently being developed and installed. Our transportation costs for the project (carrying flax straw to the mill in Nova Scotia, and shipping some in 2018) were significant, and were supported by funding from the grant. The small-scale machinery developed by Taproot would be best utilized if it could be located near where the flax is grown, to minimize transportation cost of the flax straw. Local/regional milling capacity is aligned with our project goals of exploring local textile production.
Flax grew at our farms in both 2017 and 2018. 2017 was a perfect growing year; 2018 less so. Nonetheless, a usable crop was produced in both seasons from a variety of cultivars, and we gained a real appreciation for the optimal growing conditions we experienced in 2017. Now that effective, small-scale machinery has demonstrated its capacity to process textile flax fiber, hand-harvesting of flax emerges as a new challenge to be met. Small-scale mechanized harvesting equipment for textile flax was in use in parts of North America during the the 20th century (we are aware of examples from Oregon and Quebec), and work on the development (or redevelopment) of small scale harvesting machinery is taking place right now, as far away as Egypt. Our hope is that the "reinvention" of this machinery will help make small- or community-scaled flax production more efficient for growers everywhere.
Throughout the two years of the project, we encountered people who were eager to learn about flax and all stages of its production. We fielded questions from local land owners wanting to put acres into cultivation (please don't plant any more than you can harvest by hand!), spoke with folks who were interested in multi-purpose crops (fiber and seed), and discussed the project with many people whose interest emerged from concerns about sustainability, climate change, and rural economic development. We had to tell papermakers, hand spinners, weavers, clothing designers, and other fiber and textile artists who contacted us, that no, unfortunately we did not have significant quantities of locally-grown flax fiber, yarns, or linen yardage available for purchase at this time. The modest supply of line flax, picked tow, tow roving, and tow linen yarn that were produced as part of the grant sold briskly. Based upon our experience of the past two years, there is a real hunger for natural, locally-grown fiber and textile products, and people embraced the project.
In many ways, we feel that our work over the past two years has had the primary effect of telling us how much more needs to be done to begin the process of (re)creating local systems of textile production. Every step of the way, from plant cultivation, harvesting, processing, product development, and market development, is interconnected and interdependent. To succeed, it is possible that all of these tasks must be undertaken at the same time; a daunting challenge indeed. It feels essential that those of us with an interest in the revival of regional textile production find ways to share our experiences and communicate both our challenges and successes to each other. We hope that our experiences, as documented in this reporting, will prove useful to others who are also engaged in this work, and will help to illuminate the next steps on this long path.
Project Outcomes
Taproot's machinery is beginning to solve the challenges of small-scale mechanical processing of flax fiber for textile use. This is a very welcome development, but opens the door to new sets of questions: Is there a way to mechanize the harvest of textile flax at the small scale we are exploring? Or, is there a model by which hand harvesting can be more effectively accomplished?
Given the rapidly changing political climate regarding another textile fiber suitable for growing in our region, we strongly recommend that additional study take place using Taproot's processing machinery for another bast fiber: Hemp. During our trip to Nova Scotia, we learned that Taproot's processing machinery has been successfully tested on hemp fiber for textile use. Now that Wisconsin and other states have begun permitting the growing of industrial hemp for textile and other uses, Taproot's equipment could be very helpful to researchers working with hemp.