Final report for FNC21-1278
Project Information
Eric Jellum: I began farming in 1998 after moving to Iowa from Washington State. Prior to moving here, I worked for Washington State University for 20 years at an agricultural research station in Puyallup (near Seattle). Our research centered mainly on nitrogen, phosphorus, and heavy metal chemistry in soil, as well as cover cropping. During that time I got my Masters in Soil Science from Washington State University. I currently farm 160 acres in North Central Iowa together with my brother. We use strip tillage/no tillage, intercropping, and cover cropping to grow mainly corn and soybean in rotation.
Steve Strasheim: I have been farming since 2014, when I founded Twisted River Farm. Prior to that, I spent my career working in sales, marketing and management positions. Twisted River Farm operates a compact, one acre, greens-focused “urban style” farm in North Central Iowa, delivering year round produce to dozens of accounts across the region including grocery stores, restaurants, farmers markets and a robust home delivery service.
The primary benefits of this project will focus on improved income and profitability and improved market opportunity for local production of primarily leafy greens in high tunnels. Our strategy to achieve this end is through better control of temperature and humidity throughout the year without using expensive and fossil fuel energy intensive heat sources. The objective is to use buried water pipe to store or extract ground heat beneath a high tunnel greenhouse and water-to-air heat exchangers at the surface to convey heat to the growing space. Periodic temperature fluctuations due to changing ambient conditions including night temperatures dropping as low as -30 degrees F in northern Iowa necessitate supplemental heat or adequate heat storage and heat recovery capacity. Especially in northern climates, supplemental heat can be prohibitively expensive during the heart of winter. Reversing water flow direction for ground heat extraction from the direction used for heat storage should create a beneficial temperature gradient. Enhancing the capacity to use ground storage to buffer daily and periodic temperature and humidity swings and attain higher winter night temperatures is especially important when potentially lethal cold temperatures can occur.
The objectives are to: 1) Adequately size, creatively design, and effectively operate a system to convey heat to and from the ground beneath a high tunnel to the growing space using water pipe for the ground loop and water-to-air heat exchangers in the growing space. 2) Measure the magnitude of the heat gradient created by reversing water flow direction during storage and extraction of heat in the ground loop and the effectiveness of that gradient to buffer temperature and humidity. 3) To convey the experience and lessons learned to the public and other growers in meetings, articles, and social media.
Cooperators
- - Producer
Research
Prior to erecting a 30’ by 50’ high tunnel, foam insulation board will be buried 4’ deep under the high tunnel perimeter. Water line (1200’ of 3/4”) will be buried 3’ to 6’ deep, arranged in an inner loop and an outer loop near the perimeter. After erecting the high tunnel, cool season greens will be planted. The ground loop will be filled with water (23% propylene glycol) and connected to a pump and heat exchangers/fan at the surface. The pump and a fan will convey heat between the ground and the growing space. Heating and cooling will be controlled by separate thermostats. Excess heat will be stored in the ground, venting outdoors only if necessary or desirable. A temperature gradient will be established in the ground loop by thermostatically controlling flow direction using electric solenoid valves, one direction for heat storage and the other for extraction. In this way, the ground is warmest where the heated water first enters the soil. By reversing the flow direction during extraction, the water will be heated more by passing through the warmest soil just before entering the heat exchanger. System improvements will result from comparison trials using varying combinations of components, including: number of heat exchangers; heat exchangers in series vs parallel; fan size; isolating portions of the ground loop; water flow direction and flow rate comparisons. A third heat exchanger will be dedicated to using well-water in an open loop (emptying into a drainage tile) as needed for additional air dehumidifying beyond what can be accomplished by the closed ground loop system, especially when ground temperatures become too warm in the summer or cold in the winter. Heat storage/extraction and electricity use, temperatures, and humidity will be monitored. Trials throughout the project will be results driven from earlier trials and experience.
The project began in early summer of 2021 and proceeded according to the proposal with few exceptions.
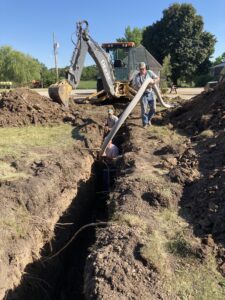
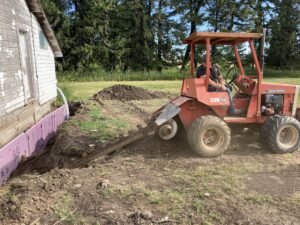
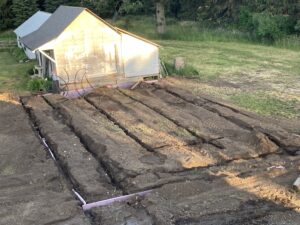
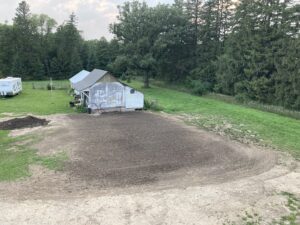
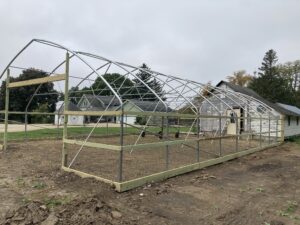
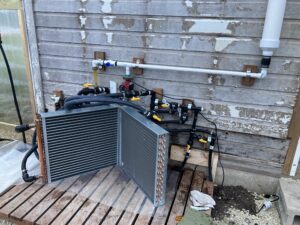
The high tunnel dimensions were 30’ by 54’, and the combined geothermal loop length was 1300’. The loops were oriented vertically in a narrow trench in a slinky pattern. The outer loop trench was about 140’ long with 700’ of water pipe. The inner loop was about 100’ long with 600’ of water pipe. Purging the system of air proved to be quite difficult because of the vertical orientation of the slinky loop. The flow rate in the outer loop was much lower than that in the inner loop for reasons that could not be determined. A loop diameter of about 42” resulted in over 100 loops in the entire system, each with the potential for trapped air at the top of the loop to limit flow rate. The circulating pump selected for the system was based on experience with a closed loop designed for drying corn (FNC17-1080) that consisted of three ¾” pipes oriented horizontally and manifolded to 1¼” at the heat exchanger and pump. Because the flow rate in the high tunnel system was substantially lower than the drying loop when the same pump was used a larger pump was purchased to increase the flow rate enough to adequately test the system. In hindsight, if the geothermal pipe slinky system had been oriented horizontally as in the drying loop, and three loops used instead of two, the larger pump and greater electricity use would not have been necessary. The larger pump in the high tunnel operating on the highest setting (about 200 watts) gives comparable flow (4.2 gallons per minute) as the smaller pump in the corn drying loop is capable of with only 77 watts. Restrictions in the above ground plumbing fittings in the system have also been identified and will be changed to increase flow rate.
Up until mid-December air temperatures were unseasonably mild. Soil temperature was maintained at a sufficiently high level to provide adequate heat at night, and produce was being harvested as needed. The system was operated manually without thermostats and without reversing flow direction in order to get some baseline experience with the system performance. On December 15th the Upper Midwest experienced a Derecho (wind storm) that affected our farm severely. Included in the damage we experienced was a large section of metal-clad barn wall that flew into the high tunnel, slashing plastic and bending some framework.
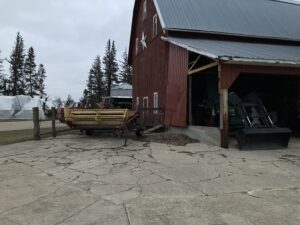
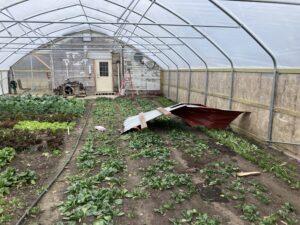
Through the remainder of the night high wind continued to expand the size of the torn area. The following day when the wind subsided, a group of helpful neighbors came to assist in putting a tarp over the damage before the approaching cold weather threatened the growing crop within. Although the tarp was quite effective, it was opaque and blocked sunlight from a third of the greenhouse space.
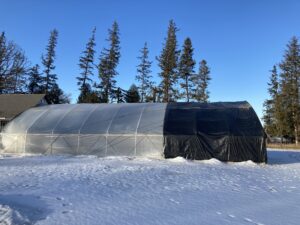
Even though it was secured tightly with ropes wind was able to penetrate all too easily. This was quite a setback for the planned evaluations. The impact of colder weather on soil temperatures was more pronounced because of the damage. On January 13th a brief stretch of sufficiently mild temperatures and low wind speed presented an opportunity to repair the damage just in time for about 8” of snow the following day.
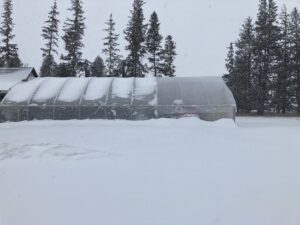
January 30, 2023 This is a progress report rather than a final report. An extension was granted to submit the final report by the beginning of July due to unanticipated circumstances. Flying debris from the Derecho wind event in December of 2021 did extensive damage to the high tunnel. Damage was repaired initially only well enough to seal the worst of the air leaks with an opaque tarp covering a third of the roof for the next month before getting an opportunity to replace the tarp with new plastic. Data was collected through the winter, but under compromised conditions. Tattered and taped plastic, mainly on the end-wall, has been replaced with twin-wall polycarbonate sheets, which resulted in a much tighter seal from ambient air penetration. A second entire winter for data collection will be possible with the extension.
In addition to storm damage repair, plumbing fittings for the geothermal system were increased in size where flow was considered to be restricted. This resulted in greater flow rates for the same pump setting. A third loop was added in October, 2022 between the inner (600' vertical slinky) and outer (700' vertical slinky) loops that were originally installed. The third loop is 110' long and was buried only 24 to 30” deep, laying flat in the trench rather than in a slinky pattern. One-inch diameter geothermal pipe was used rather than 3/4” like the original loops in order to accommodate insertion of a 1/2” PEX pipe that could be used for circulating water from the well. This makes the third loop a double acting heat exchanger that can not only exchange heat with the surrounding soil but also with well water that can be circulated through the PEX inside the geothermal pipe. Trials will be conducted during the winter.
A larger geothermal loop (240' and 8' deep) that has been used to dry corn for six years (FNC17-1080) was near enough to be fairly easily extended to the greenhouse when the trenches were open to install the greenhouse geothermal system. Since this connection was an afterthought not in the original design, both incoming and outgoing pipes to this loop were laid somewhat haphazardly without separation in the same trench and in close proximity to each other. So some heat exchange in the trench moderates the temperature of the fluid reaching the heat exchanger in the greenhouse. Despite that limitation, the dryer loop has been used as backup to add heat to the greenhouse when the greenhouse system was anticipated to be inadequate during low temperatures to keep up with heating demands. There are two air-to-liquid heat exchangers in front of the fan in the greenhouse. One is connected to the geothermal system within the greenhouse. The other is connected to the dryer loop. One or both systems can be operated independently to supply heat. The pump for the greenhouse loop has been left running both day and night during December, so that excess heat can be stored in the ground during daylight hours when air temperatures in the greenhouse are often high.
Temperature monitoring has continued through the entire period while relative equilibrium is reestablished, but soil temperatures have dropped significantly as of the time of this report. It is difficult to estimate how much of this has resulted from the damage to the greenhouse and the length of time that substantial reduction in solar gain and cold air penetration because of the tarp.
Graphed data is shown for the period following the repair (January 13th) to illustrate the ability of the greenhouse and heating system to buffer temperature fluctuations as compared to ambient air outside. Even when outside temperatures have been as low as -24 F, inside temperatures have remained above 8 F. Although this temperature is lethal to the plants within, temperature spreads from outside to inside of up to 30 degrees F and more are encouraging. The experience we are getting should help us to concentrate on improvements that can help us meet our goal of crop production through the winter with very little energy use for heating besides what is required to access and distribute the solar energy stored in the ground and incident on the greenhouse roof each day.
In the spirit of research, Steve planted varieties in the hoophouse in the Fall of 2021 which otherwise wouldn't have been considered given the crops low tolerance for deep cold: Broccoli, cabbage, kohlrabi, and 5 different varieties of head lettuce. Results through January 2022 have not been favorable to those varieties. Though, there is some potential with the lettuces if internal temperatures can be held slightly higher than we were able to in the nights that dipped into the -10 to -20 F outside temperature range. The spinach that was planted from seed had poor germination due to high fall temperatures but has performed wonderfully overall with very little leaf quality deterioration. Crop plans have already been discussed for the 22-23 winter rotation based on our findings so far.
In the second winter of the project, since the greenhouse has been growing marketable crops essentially continuously throughout the year, a strategy was adopted to evaluate the ability of the geothermal systems to meet heat demands without allowing lethally cold temperatures, if possible, and without supplying supplemental heat from a non-geothermal source. The greenhouse system alone has been relied on unless it became clear enough that it may not maintain temperatures above the critical threshold throughout the night. When each loop is isolated from the others, the three loops in the greenhouse system have flowrates that vary from less than 1 gpm in the outer slinky loop, 2.5 gpm in the inner slinky, to 4.1 gpm in the recently added horizontal loop. The new loop is one inch in diameter, but with the half inch PEX inside of it the remaining cross sectional area is about the same as that in the 3/4” pipes. The higher flow rate is likely due to the shorter length and the flatter installation of the pipe. Repeated efforts to drive air from the outer loop have failed to increase the flow rate. The flow rate for all three lines together is 5.1 gpm at the low pump setting (150 Watts). A thermometer in the manifold in which the three lines come out of the ground and another placed in the line after the fluid passes through the heat exchanger are used to measure heat removed from or deposited into the ground. Periodically, when heat is not required, the fan is turned off to prevent heat exchange in order to approximate average temperatures in the ground loops. Even when ground temperatures, as measured using fluid temperatures in the loops, are similar in the greenhouse and dryer systems, the greenhouse system is much less able to buffer diurnal temperature changes than is the dryer system, in which changes in fluid temperature are very small. Undoubtedly, this is due partially to the longer pipe length in the dryer system (2400') compared to the greenhouse system (1400'), but the magnitude of the temperature swings may also be due to drier soil around the pipes in the greenhouse decreasing thermal conductivity. Drip irrigation lines were placed above the loops in the greenhouse system during their installation, but the soil weight on top of the collapsable sable lines may be inhibiting water flow from thoroughly wetting the soil around the pipes. When falling greenhouse loop temperatures appear unable to moderate dropping night time temperatures sufficiently to prevent lethal temperatures to the plants, the dryer loop has been engaged to provide additional heat. Using heat delivered from both the greenhouse loop and the dryer loop has kept temperatures above the desired 20 degree threshold even at ambient temperatures as low as -12 degrees, the coldest so far this winter.
Although there have been satisfying accomplishments so far in the project, there are important questions remaining. At present, crop quality remains excellent. This has been done solely with geothermal heat without supplementation. The backup geothermal system that has been used for corn drying has been turned on frequently to keep from jeopardizing the crop. As a result, it will take longer to determine the heating capacity of the greenhouse system when operating by itself. Even if both systems operated together continuously throughout a 100-day period in the heart of winter, the cost for pump operation on the low setting for each would be less than $50. Fan operation for heat distribution would be nearly identical. Whether or not a smaller fan might accomplish heat distribution adequately should be explored. Clearly, the operating cost of a geothermal system could be dwarfed by the capital cost of installation. The questions concerning size and design of a system still need to be addressed. The larger and deeper dryer loop does a better job maintaining heating capacity than the greenhouse loop, but will also continue to slowly cool during the remainder of winter, since it is exposed to continually cold ambient temperatures. The greenhouse system, although smaller, is a combination of solar collector and geothermal heat storage. From this point in the winter solar energy and daylength will steadily increase. The stored solar energy will increase the heating capacity of the system. The greenhouse system may prove itself to be superior to the larger dryer loop late in the winter. Also, since geothermal systems are expensive to install, heat retention alternatives for greenhouse design and mechanisms to ease nightly thermal blanketing should be considered. Benefits from flow reversal still need to be determined.
There are also vulnerabilities that should be addressed. This has so far been overlooked because we are so seldom without power from the grid. The antifreeze concentration in the system (23%) is the same as that used in geothermal heating applications that are not ordinarily exposed to ambient air temperatuers. The above-ground exposure, especially in the small cavities of the heat exchanger, leave our system vulnerable to freezing during a power outage. The freezing point of propylene glycol at this concentration is 16 degrees. This is well above the burst potential of zero degrees, but could make it difficult to resume flow necessary for heat supply if the outage was long enough for ice to block the pores in the heat exchanger. A strong enough antifreeze solution to eliminate freezing concerns (50% in northern Iowa) would be expensive and a larger environmental concern if the entire volume in the system contained a stronger solution. Another way might be to leave the geothermal system safely underground, with a short loop from a liquid-to-liquid heat exchanger to the surface air-to-liquid heat exchanger that could contain a stronger antifreeze solution. This could protect the system, although not the plants. A backup power supply that would automatically start during a power outage would be required to address this concern.
Second year results (Eric Jellum)
In the second year of the project, 2022/23, despite a warmer than normal January, the geothermal heating system was inadequate by itself to maintain internal temperatures above the targeted 20 degrees F threshold. This was partly due to the obstruction or kink in the outer geothermal loop (which comprised half the system) that virtually completely stopped flow through it. The remainder of the system in total amounted to only 700’ of pipe. The vertical slinky design, as opposed to a horizontal layout, is subject to accumulations of micro bubbles at the top of each loop, resulting in numerous air bladders in the system making flow more difficult. I have been told since the installation that this design has gone out of favor in the industry. A larger circulating pump (Grundfos UPS26-99) was installed to compensate for the design flaws in order to get a better flow rate (5.2 gpm). The greenhouse system by itself may have been adequate only when ambient temperatures were above 0 degrees F. Fortunately, the inadvertent and haphazard connection to the corn dryer loop that was done when the system was installed turned out to be fortuitous. The two geothermal loops together kept temperatures above the 20 degree threshold without supplementation from another heat source, except for one night that bottomed out at -20 F outside and 16.4 F inside. The produce quality remained high throughout the winter. From that standpoint, the project was successful in heating exclusively with geothermal heat.
Temperature graphs can be viewed here:
November 2022 - March 2023 Temperature Gradient Graphed Results
The cost to operate the circulating pump continuously was about $10/month. The cost to operate the dryer loop’s smaller pump continuously would be about $4/month. While the greenhouse loop ran continuously, the dryer loop was only on when overnight temperatures were cold enough to warrant its addition. The operation cost of the corn dryer loop was evaluated in its own project to be about 3% of what the cost would have been using LP at $2/gal. The cost to operate circulating pumps is fixed. The comparative cost with LP is a function of the differential between ground and air temperatures. While direct comparisons cannot be made between corn drying and greenhouse heating, it is probably safe to say that substantial savings of both cost and energy usage would occur in the greenhouse as well, compared to LP heating.
Two types of heat exchangers were involved, including the ground loop itself that exchanged heat between the ground and the antifreeze circulating through the geothermal lines. Large diurnal water temperature fluctuations in the ground loop demonstrated the poorer than expected performance of that part of the system. It is difficult to identify whether this was due mostly to inadequate size of the loop or low thermal conductance of heat through the soil to the loop. Since the outer loop was virtually nonfunctional, the system was effectively only half the intended size. When the geothermal lines were installed, a drip irrigation line was placed above the loops to be able to keep the soil moisture content high for better thermal conductance. Unfortunately, the irrigation line was intended for surface or near surface use, and it collapsed enough under the weight of the roughly 2’ of soil above it so that flow was essentially eliminated. Since surface irrigation would have leached too many soil nutrients from the plant root zone, there was no way to keep the subsoil wet. Excavations revealed how dry the soil had became at depths even well below the root zone. The spikes in daytime air temperatures on sunny days also demonstrated that ground-storage of much of the excess daytime heat accumulations for use at night was less than hoped for.
Temperature Gradient
The primary goal of the project was to establish a temperature gradient by depositing excess heat in the ground during the day that could be put to good advantage by reversing flow direction at night for heat extraction from the ground. The purpose of this goal was mainly to improve the efficiency of a good performing system so that pump and fan operation could be reduced. Although the hypothesis for this is still valid, the system performance was too poor to give it a good test.
In addition, the average temperature during the heart of winter was still cold enough that reversing flow direction diurnally might risk freezing some of the soil if the compensating and moderating daytime heat accumulations were deposited in a different location in the soil.
Since the large diurnal fluctuations in water temperature might have dwarfed this effect anyway the goal was abandoned under the circumstances we experienced. Perhaps the best indication of the establishment of a temperature gradient can be seen in the corn dryer loop. When it was established, the means were provided to monitor water temperatures going into and out of the heat exchanger in the drying air plenum as well as at a half-way point in the 800’ ground loop. The temperature drop from the inlet to the outlet of the heat exchanger for the corn dryer averages about 5 degrees F. At the half-way point in the ground loop the temperature has increased about two thirds of the way back to the inlet temperature. Since the corn dryer involves only heat extraction from the ground for drying during the winter and ambient reheating of the ground during the summer, it is not useful for demonstrating the greenhouse heating hypothesis except in demonstrating the establishment of a temperature gradient. I think the project hypothesis should still be tested in a better designed system in the future.
Design Improvements
Although the successes and mistakes in this project experience were valuable for future designs, I am left with some gut-feelings and questions that are worth expressing. My optimism for the future success of this type of geothermal heating system for greenhouses is based partly on the success of the geothermal corn dryer (FNC17-1080). It should be said at the outset that the current project’s goal involved testing the capacity to generate geothermal heat in a greenhouse application. But retaining heat at night with some kind of thermal blanket should also be a major focus to help minimize the capital cost of a geothermal system. Likewise, the high tunnel design may not be the best for heat retention if winter production is planned. There are good year-round greenhouse designs available for cold climates.
Geothermal heat is very inexpensive to access in well-designed systems once the system is installed. It is the nature of a geothermal system that the cost of it is mainly an upfront cost, and once it is installed it is hard to uninstall. I would strongly consider having another system professionally designed and installed; with input about its intended novel use helping to guide the designer since the need for summer cooling is not a major component for a greenhouse. However, a single system could be multipurpose and include a house or another building or use. I am also still uncertain whether buffering diurnal temperature swings by placing the system at a shallow depth within the greenhouse footprint is worthwhile considering the short mid-winter days and relatively minor contribution of stored solar radiation to the ground. According to current geothermal industry design standards, ground loop placement at a depth of about 15’ takes advantage of the later peak in temperature that corresponds better with the start of the heating season. A designer would help establish the best system and even determine whether well-water quality is good enough that an open-loop system (pump and dump) might be possible, which would be much cheaper to install.
Designing a system that is adequate for even the coldest possible nights is probably unwarranted. A smaller system that incorporates judicious use of some supplemental heat, whether from gas or heat pump for example, should minimize overall costs. Also, setting thermostats to extract heat only when necessary would keep from squandering stored ground heat and reduce the requirement for the size of the system.
Second year production experience (Steve Strasheim)
Crops in the geothermal-heated tunnel were mostly transplanted on Oct 10th, with the exception of the spinach and arugula which were direct seeded. In the tunnel this year my strategy was to lean into a bit more tried and true crops vs the highly experimental ones used in 2021-2022. Four varieties of lettuce were used for our Spring Mix, 3 varieties of romaine head lettuce, arugula, winter variety kale, and lacinato kale. Overall the crops selected performed very well. There are a lot of resources out there on winter trialed varieties, so our crop plan wasn't completely throwing darts at the wall. We started harvesting on Thursday, Nov 24th, 2022 and completed more or less our final harvest on March 1st, 2023.
Winter conditions, especially January 2023, were mild and made this winter growing season a lot easier than the previous winter, not to mention our December, 2021 derecho catastrophe. That event, plus our differing crop plan makes a complete apples to apples comparison of the two growing seasons impossible. But this past season we had a great opportunity to kind of A/B compare two identical tunnels at the same time because of my identical non-heated tunnel in Mitchell. In the non-heated tunnel, even covering the crop with triple layers of agribon 30 the leaf quality would degrade on a significant portion of my crops when temperatures would get into the single digits over night. So 50% at minimum, if not complete loss, of marketable product has been experienced in all four winters at my non-heated tunnel when we start getting those temperatures regularly. This has improved over time with experience in management and variety selection, but I have yet to experience a perfect crop in my tunnel from Jan 1-Mar 1. In the geothermal-heated tunnel, when we got good germination, we experienced nearly perfect crop harvests in 2022/2023. Insect pressure in early spring was the factor that prevented us from having a perfect winter season.
The biggest labor factor in winter growing, besides harvesting, is the two-times-daily need to cover and uncover more crops, even the very cold hardy varieties. At our non-heated tunnel in Mitchell, I would cover the crops at around 3pm daily and uncover them around 8-9am. That process of tucking the agribon fabric around all edges of the beds can be very cumbersome, especially twice a day. I was able to harvest good quality spinach and lettuce up until Thanksgiving in the non-heated tunnel. The lettuce didn't make it through the winter. The spinach sat dormant until about March and then started to regrow. So I didn't harvest anything out of that tunnel from Thanksgiving to April. The geothermal system nearly eliminated the labor component completely. I only covered the lettuces on our extreme cold nights, when outside temps would go below -5 degrees or so. Most likely the crop would have been fine without the cover, but I felt the need to hedge the bet against the system on that particular crop, specifically the romaine head lettuce, which we only get a single harvest from and leaf quality appearances are crucial. I timed the process of covering the Mitchell tunnel beds at about 30 minutes; so an hour per day, for a single layer of agribon. I would estimate another 10 minutes to add a second layer. It was very nice not having to worry about the covers at the geothermal tunnel for a majority of the winter and only having to visit the tunnel once weekly for harvest.
Obviously there is an easily calculable difference between having product availability and not, which is what what we experienced in the winter 2022/2023. But after four winters of growing in my non-heated tunnel I feel I have enough experience and data to put a finer point on it. And since there is a definite learning curve to winter growing that is not as intuitive as in the warm season, I am much more skilled now than I was at the beginning of the project. Monetarily, if each bed is worth an average of $400 from a single harvest, or $3200 per tunnel, with some crops having the possibility of a second harvest in late winter (at a reduced yield of 50%) the tunnels should be able to generate $400-600 per bed in winter months or $3200-4800 per tunnel (at North Iowa market prices). This assumes a crop mix of spinach, baby leaf salad mix, head lettuce and Bunched Kale. Other crops could be grown at a lower revenue and perhaps lesser market demand. Apples to apples, the geothermal system has the potential to increase revenue by 25%-100%. That calculation is influenced by whether the tunnel is used on its own or in tandem with another tunnel, like I have done. Using the tunnel singularly, you would most likely experience a lower percentage of increase because you would be harvesting product out of it earlier in the winter and using the tunnel to keep crops viable for a second harvest in spring. My strategy was to use the geothermal tunnel as a cache to not dip into until as late in the winter as possible. So in our context, that percentage is closer to 100% because it allowed us to have product deep into the winter when we might otherwise not have it.
Overall, I think this project has been very successful in showing what this system could mean in reduced labor and energy savings vs using a singular propane or natural gas heating source. I think as we continue to refine our winter market demand against our crop plan, we can continue to grow sales. I think there is more to be found in optimizing the system and I look forward to continuing to find those answers.
Educational & Outreach Activities
Participation Summary:
Steve Strasheim -- Steve has been a guest on five podcasts since Nov 2021 talking about his farm, but making sure to mention the project and it's importance to the future of the operation. One show in particular, The Shark Farmer podcast, which aired on SiriusXM ch 147 in November 2021 took particular interest in the project and spent a few minutes asking questions about it.
Looking ahead a few months, Steve has also secured speaking opportunities at two separate events, one in the early spring and one in the late spring of 2022, to talk specifically about the project and our findings through the 1st winter of the study.
The outreach portion of this project has largely been achieved through social media, the www.twistedriverfarm.com blog section of the website and through word of mouth at various conferences and community events. Since our data was compromised in the aforementioned storm damage, we felt that postponing a proposed field day to the spring of 2023 was appropriate. We’ll continue to post updates on our Social Media and Website as there is a lot of interest in what this system is able to do.
I’m also trying to arrange a few speaking slots at two 2024 winter conferences. From the agronomy perspective-This winter has been far more favorable to our crops than last year. Lettuce, which is our highest demand leafy green, is quite frost tolerant down to 22 degrees (Winter vegetable killing temperatures. Adapted from Pam Dawling, Storage of Vegetables for Off-Season Sales, 2017 ). Through careful variety selection we have found that lethal threshold to be closer to 12 degrees, with leaf quality staying close to pristine down to 20 degrees. So far this winter, we have been able to keep the ambient temperature right around that 20 degree threshold that we feel is ideal for keeping leaf quality in pristine condition. In a typical winter season we would hope for a pristine lettuce crop up until around Jan 1. Our lettuce crop as of this writing is still in top quality condition, and is extending our sales period far longer than we had hoped for that product. Spinach and kale have a much lower temperature threshold, and typically are not as susceptible to leaf quality issues, thus our spinach and kale crops look as expected.
In the second year of our project we focused on social media and in person outreach, but included a Practical Farmers of Iowa field day on June 18th, 2023. Our social media posts were heaviest during the winter so we could show viewers real-time conditions and crop development.
We are adding to our blog series on www.twistedriverfarm.com about the second year and will add the project final report to the link so that our project work can live permanently. Over the course of 2022 and 2023 I had the opportunity to bring about a dozen interested people, including visiting farmers from out of the area, to see the tunnel in person. I also had the chance to speak about it at three different local service club breakfast/lunch meetings in the winter of 2022/2023. I was able to give an impromptu presentation on it at the Great Plains Growers Conference in St. Joseph, MO in January 2023 in front of approximately 100 fruit and vegetable growers. Based on that, there will most likely be an invitation to present about it formally in 2024.
Learning Outcomes
The lessons we learned from this valuable experience included lessons learned from mistakes, as so often happens. There is a lot of potential to make use of geothermal energy in a variety of ways that include greenhouse heating. A description of this learning is included in the Results section of the report. Steve Strasheim is well connected in social media and grower networks through his business, Twisted River Farms. The lessons learned in our research are extended mainly through those channels.
Project Outcomes
Recommendations for future work were covered in the report, but include especially better automated means for nighttime heat retention. A thermal curtain easily drawn across the bottom of the trusses in the tunnel would not only reduce the surface area for heat loss, but would better concentrate the heat distributed from the fan near the plants and isolate it from the ceiling.