Final report for FNC21-1280
Project Information
We operate an experimental growing operation on 1.5 ac in southern Wisconsin (5a) in coordination with the Low Technology Institute (lowtechinstitute.org). We grow typical garden vegetables, hosting a CSA, as well as small-scale cereals (wheat, rye, corn, barley) and others (flax, peas). We primarily research market-garden production solutions that involve no or minimal fossil-fuel inputs.
Initial Concept
Imagine a cube measuring 4 ft on each side. On top of the cube is a rich bed in which edible greens are growing. The soil is watered and fertilized from below, plus carbon dioxide seeps up from the soil. The soil is warm, even though this box is in an uninsulated greenhouse. Inside the box is a cubic yard of compost, waiting for use in the spring. This is the central idea of hot box composting.
A long time ago (the 1980s) in a land far, far away (Cape Cod), the New Alchemy Institute (NAI) researched ways to live with less reliance on fossil fuels and outside inputs. They pioneered bioshelters and aquaponics before these were well known in alternative sustainability circles. They also created a composting greenhouse, which tested the premise that all of the products of compost could be used to grow plants through the winter.
Greenhouses (more technically “hothouses”) have been heated by compost for hundreds of years, as mentioned in a 1693 English translation of a French gardening manual, for example (de la Quintine 1693). At the time, they would have recognized that the moisture from the compost was also beneficial for the plants, but they would not have known that the carbon dioxide off-gassing from the pile was also helping their growth until at least the 1800s. Eventually the advent of cheap and ready fossil fuels supplanted the more labor-intensive compost heat.
At the New Alchemy Institute, they recognized that they could create a system to both compost large volumes of manure and capture all the beneficial products of that process to grow plants through the winter. The heart of their system was what is called today an aerated static pile (ASP). This type of composting set-up consists of a sealed bin with a perforated pipe below it (technically known as an “in-vessel bioreactor”). A blower pushes fresh air into the pile from the pipe (i.e., aerates it), feeding the composting microorganisms with fresh oxygen without needing to turn the compost (i.e., a static pile). Meso- and thermophilic (heat-loving) bacteria use that oxygen to break down organic compounds to create heat, carbon dioxide, water vapor, and nitrogen (although it is a more complex biological process, it is essentially: various CHO and N compounds + O2 → nitrogen compounds (NH3, NH4+, NO2−, NO3−) + CO2 + H2O + heat). With the fresh air coming in, the off-gasses must go out, and they do so through vents into woodchip beds. The shredded wood creates a biofilter by both providing carbon and an environment for bacteria that convert harmful nitrites and ammonia into plant-absorbable nitrates.
The greenhouse at NAI was custom built for this system. The 12-×-48-ft hoop house was oriented from east to west and had a 25-cubic-yard composting chamber along its north side. On top of the wood-framed, sealed chamber was a grow bed, consisting of 18 inches of woodchips under sandy loam supported by hardware cloth. As the compost chamber was filled with manure from nearby stables, blower motors pushed 12,000 cubic feet of air through the system each day (running 15 minutes every 6 hours). Much of the off-gasses went into the bed above the chamber, but another grow bed on the south half of the greenhouse was fed with underground distribution pipes and dedicated blowers. In the winters, they grew leafy greens and started seeds in this greenhouse and filled the space with cucurbits, peppers, and other heat-loving crops in the summer. The entire setup and details for their research project can be found in their third research report on their website: https://newalchemists.net/portfolio/compost-greenhouse/.
Although compost-heated greenhouses are nothing new, they require dedicated infrastructure and space in a greenhouse. This project sought to test a scalable, modular, and mobile composting box that any market gardener could build to grow greens during the shoulder and off seasons, when these products fetch a higher price.
The project ran a series of controlled tests to determine the best practices with this system, including determining the optimum aeration of the compost; ideal carbon-to-nitrogen ratio, moisture content, and free air space in compost inputs; measuring methane, ammonia, nitrites, and nitrates outputs; how to best control moisture, heat, and carbon dioxide output; and best crops to use based on available resources.
References Cited:
de la Quintine, Jean. The Compleat Gard’ner, or Directions for Cultivating and Right Ordering of Fruit-Gardens and Kitchen Gardens, trans. John Evelyn (London, 1693), 2:193.
-
Build twelve hot box composting units and evaluate the optimum configuration of variables of over the spring and summer of 2021 and winter of '22–'23. As these units proved inefficient, a new, bladder-based system was tested in the summer of '23 and winter of '23–'24.
-
Test the bladder system at an on-farm location over the winter of 2022–23 and evaluate performance through qualitative and quantitative recording.
-
Disseminate findings through field days, presentations to industry groups, write-ups in popular and technical publications, and digital podcasts and videos, which will be ongoing after this project ends.
Cooperators
- - Producer
- - Producer
Research
2021 Establishment
The project began in the spring of 2021 with the construction of twelve compost boxes. This was complicated by the spike in commodity prices at that time, especially building materials. By modifying the boxes slightly, we were able to build the boxes with fewer 2-x-4s. We were within an hour of the budgeted 48 hours of construction for the boxes.
We assembled a polytunnel donated to us from a neighbor to house our boxes for the summer test. The boxes took considerably more time to move than expected, although this would not be an issue for any market-gardeners who adopt this strategy as they are likely to have access to a forklift, bobcat, or tractor with forks.
We filled and cycled the boxes through three 1-month cycles of filling and emptying with compostable materials at various levels of C:N. While we got reasonable composting through the trials, they required turning and adjustment throughout each cycle. Although we recorded and tested for different compounds (CO2, temp, Ammonia, Methane, Nitrites, etc.) we did not get a good picture of predictable information due to the composting variability.
We varied feedstock sizes and found that materials of the consistency of grass clippings worked well (smaller was too fine and compacted, restricting air flow; larger was not compact enough and temperatures didn't rise properly).
Overall the summer cycles were not satisfactory in providing us with a good methodology for filling and monitoring the boxes for maximum composting efficiency or nutrient, water, and heat production. This was partly due to the wide variety of compost feedstock available in the summer and fall.
Nevertheless, we moved the polytunnel and six boxes to a sunny location for the winter trials. After a few weeks of loading the boxes with horse manure and bedding from a nearby stable, it was clear that we were having trouble getting the materials to start composting at expected temperatures. We know that larger systems of this type can function in freezing temperatures and that more troubleshooting would be necessary than expected.
At this point, we asked for and received an extension of our project so that we could have two winters to run these tests, using the winter of 2021-22 to find a way to get the boxes up and running before testing various configurations in the winter of 2022–23.
2022 Continuation
By the end of the winter of '22 I had stabilized our hot-box composting system using horse manure and bedding from a nearby stable. Each week I transported a yard of fresh manure and then emptied and reloaded one of the six hot boxes in a sunny polytunnel. By now I could consistently get the feedstock to compost, produce heat and moisture, and warm and water the beds above the compost chamber, but I realized a major design flaw: the grow-bed lid was heavy. Heavy enough that I, a middle-aged, fit person struggled to lift it in order to release the door to empty and fill the box every six weeks. By the time the attached picture was taken, it was too late to get plants growing in the bed, but temperature measurements of the bed were consistently above freezing, but probably not warm enough for all but the slowest germination.
During the early spring, I had a new idea. Instead of creating small-scale permanent aerated static pile composting boxes that could be moved by a forklift, why not create a simple compost set-up with bays and forced air floors, and then cover the whole thing with a tarp to trap the carbon dioxide, heat, and moisture to be pumped under an adjacent bed. The blower was protected in a small, weather-tight box behind the bladder. This set-up could still be modular and dismantled each summer for growers with limited hoop house real estate. Not only would this be easier to unload and reload each week, but it would be cheaper, because it would only need a dozen pallets, some hardware cloth, wood chips, and a big tarp. I was able to disassemble the existing boxes and reuse the materials to build the new design, only having to buy the new tarp.
I built a test unit in the spring of '22 and ran it through the summer, continuing to feed a yard of horse manure and bedding each week from our neighbors. I found that because the piles would reduce most noticeably in the first two weeks, every third week, the manure would be piled on top of the last two bins to be filled, creating a 6-week compost cycle. This was just a way to, forgive the adage, "carry 10 lb of manure in a 5 lb bag," that is, fit more in the bins by using the newly free space. This system functioned much easier than the boxes: the trailer could be backed right up to the installation, the bins were easy to access with a shovel, the bladder helped distribute the moisture among the bays. The most challenging part was pinning down the tarp to avoid "blowouts," where the moist, warm, carbon-dioxide-rich air would escape under an edge of the tarp due to pressure. Two solutions worked well: using stakes pounded into the tarp, covered with logs and composted manure to seal it where the tarp did not need to be opened up (i.e., the back and sides) and then heavier logs and composted manure to seal over a longer tarp "tail" (where it would be lifted up each week); and changing the blower to cycle twice as often for half the time put less pressure on the system.
By the fall of 2022, I was ready to install this into the hoop house of our collaborator, Terry Parisi at Parisi Family Farms. We installed a four-bin system with an attached grow bed and began to fill it each week with a yard of manure and bedding.
2023 Conclusion
The composting component of the system function perfectly at the Parisi Family Farm. Each week ("Manure Mondays") we would unload the composted material into a windrow inside the hoop house for finishing (shown in the above picture) and then load back up the now-empty bay. South of the composting unit was a raised bed that received the hot air, moisture, and carbon dioxide from the system every time the blower cycled. This was a very small bed. For comparison, NAI had 15 ft2 of growbeds per cubic yard of composting chamber. We had just 4 ft2 per yard. Mid-winter we transplanted bok choi from a nearby bed in the greenhouse. Although we took the usual transplating precautions, the bok choi wilted and yellowed (it did eventually recover and bolt prematurely). This may have been due to transplant shock, cold temperatures, or excessive CO2, but the sample size was too small to be sure. The attached pictures show the wilted state a week after transplanting, the same plants bolting prematurely, and the over-wintered bed from which they came.
Unfortunately, the engineering difficulties we ran into before getting this system functioning smoothly precluded extensive and repeated grow-bed tests. I think that the challenges of capturing the heat in this bladder and successfully transferring it to the bed are too great for a modular system, as discussed below.
Unfortunately, the harsh conditions inside the hot boxes (150°F/65°C, 99 percent humidity) killed the temperature and humidity monitors, even when they were protected in sealed bags or other containers. We have only our weekly data to build our temperature curves. The nitrogen monitoring proved inconclusive (monitoring strips and protocol were not sensitive enough), and we had to send out samples for analysis. We did measure methane, carbon dioxide, and humidity religiously every week.
Temperature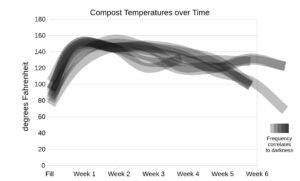
Even with the failure of the digital temperature monitors due to high heat and moisture, when they were working, I compared the monitor's temperature to an analog compost thermometer inserted in the pile each week during emptying and filling and found them to be within a degree or two of one another. Luckily, I had been recording the temperature of each pile each week manually as a back up. Instead of having data every 15 minutes, we only were able to record every week, but the temperature rise and fall were slow and steady, therefore the trend is still clear.
The system produced textbook compost-pile temperature curves. At filling, the manure was just over ambient temperature (60-80°F [15-27°C]). In the attached graph, a dozen well-documented pile curves are plotted in grey lines--the areas with darker, overlapping lines the lines represent more common occurrences (i.e., trends). In the next two weeks, the pile would hit its maximum, just under 160°F (71°C), when the bacteria and microorganisms responsible for the process begin to shut down. It would hold this temperature or just under for another week or two, before a slow fall over the next three weeks, dropping to 120°F (49°C) by the time it was time to empty the bin.
The air inside the bladder was also warm, as the piles "breathed" out into this confined space. Although the air being blown out of the piles would have been well over 120°F (49°C), it was moderated by the ambient temperature. The bladder skin, an impermeable tarp, was only insulated by the addition of a second tarp on top, so the warm, moist air coming out of the piles quickly condensed on the inside surface. The air being blown out of the bladder into the grow bed averaged between low 70°s and high 60°s F (19-22°C) compared to the ambient monthly averages dropping from the low 60°s to the mid-30°s F (18-2°C).
Humidity
Humidity data are easy to summarize: 99 percent every time, all the time. As long as compost was active, humidity was always at its maximum reading. Indeed, water was the limiting factor, and we had to pour 5-10 gal of water into each bay every week to avoid stalling the composting process. In the hot boxes, the moisture did rise up and collect in the above grow beds. In the tarp-covered model, moisture often collected on the tarp and dropped back into the compost, reducing the amount of added water required by about half. Since the microorganisms that drive the composting process had as much oxygen as they needed (see "methane" below), water appears to have been the limiting factor.
Carbon Dioxide
As with humidity, carbon dioxide levels under the bladder and being blown out to the grow beds always maxed out the monitor at 10,000 ppm (twice the ppm of OSHA's exposure limit). As long as the compost piles were fully functioning (once the initial learning curve, flow rates, etc. were figured out), carbon-dioxide production was plentiful. During build-up phases or when something wasn't right (i.e., not enough water, air, feedstock), carbon dioxide measured between 4,000 and 7,000 ppm.
Methane, Ammonia
Methane was never present. Whether the composting process was not yet fully heated up or functioning at full tilt, more than enough oxygen was permeating the pile to prevent anaerobic composting, which produces methane. By having a fully aerobic composting pile, we produced less of the more harmful greenhouse gas (methane is 25x more potent than carbon dioxide). But this complete composting also meant that less nitrogen was being delivered to the grow beds through the forced air.
pH
The pH of the compost was measured each week as the bin was emptied and refilled. Every single reading was between 7.5 and 8.0, well within the healthy range for composting bacteria, which prefer 5.5–8.0 pH.
Nitrogen, Compost Quality
Since the composting system didn't go anaerobic, where nitrogen can be lost by turning into ammonia and other gasses, the nitrogen was converted into plant-available nitrates in the soil. The UW Soil & Foraging Analysis Lab (lab no. 1332, report no. 1461) analyzed our composted manure, showing we had created 0.4-o.3-0.4 fertilizer. Furthermore, their analysis showed that we had fully composted the feedstock (no change in nitrogen over time nor was NH4- present).
Maintenance, Monitoring: Blower Settings, Water Input, Etc.
The settings for our blower (B-Air, 1HP, 1170 cfm) varied by season: Summer, 30 sec every 20 min; Fall/Spring, 25 sec every 25 min; Winter, 20 sec every 30 min. If the winter air could be warmed before entering the compost, more air could be pushed in, but too much cold air retards the compost cycle. This volume of air worked for us, but each system requires independent analysis to arrive at its optimum settings. At NAI, they were pushing 465 cf per day per cubic yard of compost (190 cfm × 60 min ÷ 25 yd3) compared to our 4,680 cf per day in lowest winter setting (1170 cfm × 16 min ÷ 4 yd3). This ten-fold increase in the amount of air moved through the system may account for why we had no ammonia or methane build-up. See below for further discussion of this point.
Educational & Outreach Activities
Participation Summary:
We hosted a Wisconsin Farmers' Union tour with eight participants to view the study in the summer of '23.
We filmed the entire process and have created a video to share on our social media: https://www.youtube.com/watch?v=x1exnZCT-5I. The video audio was also disseminated through our podcast: on on iTunes, Spotify, Google Podcasts, TuneIn Radio, Stitcher, and others.
We have written a summary of this study (included with this report and also available here) and will be submitting it to Mother Earth News.
Our local paper, the Edgerton Trading Outpost, carried a short story and photo of the project being set up, but they have no online presence to share.
Learning Outcomes
Although we are only at an interim point in the study, a few lessons are already apparent:
Small aerated static piles are harder to start and maintain, as the small amount of material must be more closely monitored to maintain optimum conditions.
Compost feedstock size is an important factor in effective system function, as small materials compact and prevent airflow, while large materials allow too much. Grass-clipping size for plant material appears to be about right.
The boxes are heavy to move and also to open with the grow bed supported on top of the box. A modification is needed to make them more user friendly for those without significant strength to open them.
We abandoned the high-flow settings, which we had planned to test throughout, as the high through-put of air cooled the piles too much and composting activity ceased prematurely.
Project Outcomes
Although the grow beds were not greatly successful, the aerated static pile compost systems are still being used at both test sites.
The goal, though, of this system was to capture all of these composting products and use them directly for growing plants in the off season. NAI's custom-built greenhouse and initial hot-box systems certainly did a better job of this than the more user-friendly bladder version. Heat seeps easily into a grow bed installed above the compost piles, while pushing it down a pipe into a grow bed is significantly less efficient. With the gas-trapping tarp and transmission tube exposed to cooler air, moisture condensed on the surface. When water condenses, it gives up heat and the moisture can no longer travel through air, meaning neither heat nor moisture are not transferred to the grow bed but rather stay trapped in the composting chamber. The few bok choi that we were able to transplant into the study grow beds in the winter did not do well, but because the sample size was small, we could not tell if the withering of the hardy winter green was due to cold temperatures, transplant shock, or excessive CO2. The bottom line is that although they are modular and easier to use, neither the boxes nor bladder system effectively trapped and transferred the heat and moisture to grow beds.
This negative result does not condemn this system, however, as we have learned lessons that would help anyone interested in using compost to increase their growing season. Let’s move from general to specific recommendations based on this study.
- This system is difficult to make modular, as the physics behind transferring the main benefits (heat, moisture, CO2, and nutrients) require a dedicated set-up. It may not be necessary to build a new greenhouse from scratch, although that would be easier. An existing greenhouse could be retrofitted with composting bays along the northern side. In designing a system, one has the obvious things to consider, such as weight of the grow beds on top of the compost chambers (figure at least 100 lb per square foot) are worth highlighting.
- This system creates a huge amount of moisture in the composting chamber, which will wreak havoc on any wood or metal that is not moisture resistant. Even pressure-treated and galvanized building materials exposed to this high-heat, high-moisture environment will break down more quickly than expected (not to mention the introduction of the chemicals from those treatments into the food chain). Sealing the chamber with rigid poly sheets (and sealing the seams) to direct the moisture toward the beds is a worthwhile investment.
- Both NAI and LTI researchers noted the labor involved in sourcing and moving yards of manure regularly. A minimum of one yard of feedstock should be added each week (after removing the composted equivalent). In the winter, at least up here, the only ready source of compostable material is animal manure. Since a yard of horse droppings and bedding weighs about 1000 lb or more and a horse produces about 50 lb of waste (feces plus urine), two or three horses would supply the needs of a small system, for example. A cow produces more per day (ca. 65 lb) but it needs an equal amount of carbon added to the mix for the N:C ratio to work. If you do not have animals, a regular source of this much manure should be identified before construction. Even with access to manure, moving literal tons of this stuff around requires a trailer plus a loader (whether that is a person with a shovel and lots of time or powered equipment).
- It is important to make the manure bays accessible. This means a way for your vehicle and trailer and/or loader to drive right up next to the hatches. Plus they have to be easy to dig out, which requires an insulated, full-height hatch that opens to the ground and is high enough dig out and fill back up, whether by hand or with a bobcat bucket.
- The bottom line is to ask oneself whether the investment is worth it. If one has animals and is already dealing with manure, this may be a good way to get more out of the local resources.
- The study results also give us a few specific suggestions to improve these systems.
- One is to install a watering system. Whether this is a drip hose installed on the ground under the compost (where it dries out most quickly) or an overhead sprinkler system, this will save hauling buckets of water or dealing with a hose in the winter. A moisture meter installed on the floor could help assess when more water is needed.
- Each system requires fine tuning as to the amount of air being fed into the system. We found that our 1170 cfm, 1-HP blower was more than enough, and we set it for 30 sec every 20 min in the summer, 25 sec every 25 min in the fall and spring, and only 20 sec every 30 min in the winter because introducing cold air chilled the compost bacteria. We never had methane or ammonia build-up, so we had more oxygen than the system needed. Based on the fact that NAI was using a tenth of the air, we could probably have reduced our blower load and thus energy use. For best results, one could reduce the air intake until these products of anaerobic digestion appeared and then raise the blower levels a little bit to give the system enough oxygen. We tried to use a thermostatically controlled blower, with a sensor above and in the compost through the winter (it would turn on the blower when a high temperature threshold was met, but keep it off if it cooled down too much), but we could not find a consistent enough temperature reading to keep the system functioning smoothly.
- A carbon-dioxide detector set to go off if the air within the chamber drops below 10,000 ppm would alert the operator to the fact that something in the system is off. It would then be easy to find out if a blower adjustment, need for new compost feedstock, or more water was needed.
Harnessing all the outputs of a compost system by combining an in-vessel aerated static pile with forced-air grow beds has been shown to produce excellent four-season growth in a cool climate, but my attempt to create a modular system was not successful. This easiest way to use this forward-thinking concept is to build a greenhouse with dedicated, permanent infrastructure, coupled with ready access to a source of winter manure. While it is likely possible to create a mobile version of this system, the amount of insulation and engineering involved would be significantly more trouble than the benefit of being able to gain a little space back in a hoop house for the summer.
Information Products
- Compost Study Infographic (Fact Sheet)
- Compost Study Bulletin (Bulletin)