Final report for FNC21-1303
Project Information
Scott Farms is a third-generation family farm in southern Ohio. The farm’s major enterprises include: approximately 700 acres of row crops; approximately 200 acres of forages; a cow-calf enterprise with approximately 65 brood cows and a feeding operation for feeder and fat cattle; and a two-acre hop yard where the farm produces hops that are processed on-farm for direct marketing to various breweries in southwest Ohio. The processing facility is licensed by the Ohio Department of Agriculture, allowing the farm to process hops for other producers. The hop yard was installed in 2015 with processing and sales beginning in 2016. The farm is one of the larger and longer-tenured hop producers in the region. Scott Farms has a long history of using sustainable practices, including grass waterways, rotational grazing, cover crops, and, has even installed a permanent conservation easement that protects the farm’s main creek.
Hops are a recently revitalized crop in Ohio. Hop production in the state has increased over the past decade in response to rapid growth in the craft brewing industry and interest in “knowing your farmer” and local food systems. However, Ohio farmers face multiple challenges to sustainable hop production, including growing conditions. One such challenge is day length during the growing season, which is shorter than the most productive hop producing regions of the U.S. Day length is an important factor in flowering timing for hops, which is a major factor determining yield.
This project installed lighting and measured the impacts of a lighting system to extend the photoperiod for hops. The goal was to improve the pre-flowering vegetative growth of the plants in order to increase yields and hop quality in a manner that has potential to not rely on increasing amounts of synthetic fertilizers. An additional goal of the system is to improve the long-term economic sustainability of hop production in the region.
In the first growing season of the project (Season 1) using the lighting system, pre-flowering vegetative growth was increased substantially. Additionally, hop yield was substantially increased compared to the prior growing season. Fertilizer and water usage were measured for Season 1 and fertilizer use was compared to a control hop yard in the region. Additionally, electricity usage and cost were measured for Season 1 and compared to the prior year, as the lighting system added a new input cost to the hop operation. While the initial indications from Season 1 are that vegetative growth and hop yield were increased, the cones harvested in Season 1 were substantially smaller than prior seasons and had lower acid content than industry standards. Because acid content is very important to commercial brewers, these issues with quality were substantial enough that the cones harvested in Season 1 were not adequate for brewing and thus could not be sold as pelletized hops. An important learning from Season 1 was that the timing of nutrient availability will be important for increasing cone size while using a lighting system.
In the second growing season of the project (Season 2) the hops had substantial pre-flowering vegetative growth and there were many cones on each plant. However, these cones were visibly smaller than cones produced without lighting. Inputs including fertilizer, electricity, and water usage were tracked and compared to Season 1 and the 2021 production at the hop yard at The Ohio State University South Centers. Season 2 yielded a similar, although slightly lower yield compared to the control yard’s production in 2021, but used less fertilizer. The quality of the Cascade hops harvested in Season 2 were comparable to industry standards. Although there were $340 in sales from Season 2 as of this report, there are an estimated 120 lbs.- 150 lbs. of hop pellets in storage for sale from the 2022 harvest. The lighting system also allowed for control of the timing of harvest, including the ability to stagger harvest, to better match resource availability on the farm. While it appears that there are potential advantages to utilizing a lighting system in hops based on this project, there are also challenges associated with the system.
- Evaluate the installation and operational costs of an LED lighting system for photoperiod extension in commercial-scale hops production;
- Evaluate the production and economic effects of an LED lighting system for photoperiod extension in commercial-scale hops production; and
- Share findings with other producers and Extension professionals through a field day, social media outreach, a summary video, and a conference presentation.
Cooperators
- (Educator)
Research
The hop yard at Scott Farms is approximately two acres with approximately 1,800 plants. The yard includes a 12-row straight high-trellis system with 20-foot tall poles spaced every 44 feet with 16 feet between rows. The trellis system is approximately 5,520 linear feet. A 5/16-inch steel cable is run along the poles at the top and bottom of each row to hold the strings on which each plant is trained. The top cables of the trellis provided a built-in system for installing the lighting system.
Lighting was installed on approximately 1 acre of the hop yard with approximately 900 plants in 2021. All plants with lighting in Season 1 were the Cascade variety. Although the yard included another variety of hops (Fuggles) of approximately 1 acre, after various production issues it was determined that the second variety would need to be destroyed and the yard replanted. The second acre was replanted with 2 new varieties in the summer of 2021, however, the company providing the new plants determined that lighting should not be used on newly planted rhizomes, so lights will not be installed on the second acre until Season 2. The lighting system utilized light-emitting diode (LED) lamps designed specifically for the regulation of flowering in plants. The system used 240 GP LED flowering DR/W/FR E26 11watt bulbs manufactured by Phillips, which are designed for short-day length plants with a spectrum rich in red light. The lamps were installed on commercial grade-electrical light strings that are attached along the top cable of the trellis system with zip ties. Lamps were placed every 20 feet in a staggered pattern. Installation of the lighting system was labor intensive, requiring 3-4 people to install, so the system installation was staggered over approximately two weeks. Lights were turned on in each row of the yard as installation was completed. The first row of the lighting system was installed and turned-on June 6, 2021. Generally, the lighting system was turned on at 7:40PM each evening thereafter and turned off about 8:00 AM each morning. The lighting system was used each night until July 31, 2021, a date determined in consultation with OSU Extension Educator, Brad Bergefurd. Although it would have been ideal to install and begin using the lighting system in May 2021, supply chain issues caused delays in receiving electric strands.
In August 2021, the part of the hop yard where lights were not installed was planted with two new varieties of hops. Approximately ½ acre was planted with Nuggets and ½ acre with Michigan Copper varieties. These varieties were chosen to replace the previously planted variety after careful consideration of the best growing conditions of the new varieties and discussions with brewery customers. Lighting was then installed in the trellis system over the new varieties and turned on May 31, 2022. This new section of lighting was installed in the same manner as those installed during Season 1 on the Cascade variety. In addition in Season 2, they were installed in the same manner as the lights previously installed in Season 1.
Based on what was learned in the 2021 growing season, the lighting period was shifted to earlier in the 2022 season. Lights were turned on overnight in late-May (May 31, 2022) through mid-July (July 19, 2022) for all hop varieties in Season 2.
The hop yard is fed with a drip-tape irrigation system from a nearby pond using a triple-sand filter pump. Fertilizer and pesticide applications were applied through the irrigation system and logged throughout the season. Additionally, use of the irrigation system was logged throughout the season to allow for an estimation of water usage for the season. Additional pesticide applications for disease or pest management were applied as necessary using different methods such as foliar application.
The hop yard is near the barnyard, which includes a small grain bin with a dryer, the hops oast house where hops are dried and pelletized, and the nearby tobacco barn on the same electric meter. The lighting system was connected to this existing electrical service. Generally, the electric use of the tobacco barn is static, changing little from month to month. The oast house is used primarily for processing hops. Electric use for processing occurs after lighting has been terminated. Although some processing of hops for other growers could make electricity for lighting and processing overlap, in 2021 there was no overlap. Electricity bills for 2021 were collected to track electricity usage and costs associated with the lighting system. In 2022 there was no overlap of electricity use at the oast house for the purpose of processing and packaging hops for other growers and electricity used for the lighting system. Electricity bills for Season 2 were collected and used to track the electricity usage for the lighting system alone.
To compare vegetative growth, yield, and fertilizer use, data were requested for the hop research plot at the OSU South Centers, which is approximately 56 miles east of Scott Farms and subject to similar growing conditions. It should be noted that the OSU South Centers uses a V-trellis system. OSU South Centers Brad Bergefurd of OSU Extension graciously agreed to allow us to use the hops yard data and information as the control site for this project. Unfortunately, in 2022 the hop yard at the OSU South Centers was not actively managed for production. Data from the site collected in 2021 was used as a control for comparison in both seasons of this project.
Vegetative Growth
Vegetative growth was significantly increased in Season 1. Pictures attached (Figure 1, Figure 2, Figure 3, Figure 4) show that many more plants grew to the top of the trellis, a height of 20 feet, than years prior. Figures 1-4 were taken in August and September 2021. The attached picture (Figure 5) from 2017 shows an example of the best height growth experienced prior to this project, while additional pictures show growth in Season 1. During Season 1, some bines even grew along the top of the cable. In addition to increased height of the majority of plants, there was also substantial lateral growth. In Season 1 lateral growth was significant. In many instances lateral growth reached the plant beside and intertwined with it. Horizontal growth between plants has a big impact on cone production. In previous years, lateral growth has been minimal at best. Vegetative growth increased again in Season 2. In Season 2, all live plants reached the top of the trellis, which is 20 ft. Many of the Cascade plants, which are older bines, even grew laterally across the top of the cable. In addition, lateral growth below the top cable increased substantially. Many lateral bines reached the plants next to each other on both sides. Again, most of the significant lateral growth was in the older Cascade bines although there was some lateral growth in the two newer varieties installed in Season 2. The photos in Figures 6, 7, and 8 show the vegetative growth in the yard as of late August 2022.
In comparison, the maximum height of the plants for the 2021 growing season at the OSU South Centers hop yard was estimated at 15-20 ft.[1]
[1] All references to data from the OSU South Centers hop yard are from “Hop Production to Enhance Economic Opportunities for Ohio Farmers 2021” by Brad Bergefurd, Extension Educator, South Centers, Thomas Harker, Horticulture Research Associate, South Centers, Ryan Slaughter, Horticulture Research Assistant, South Centers, and Wayne Lewis, Farm Manager, South Centers.
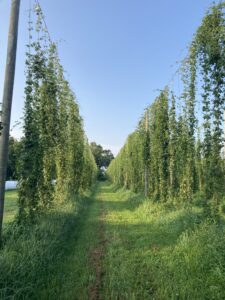
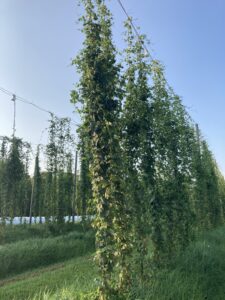
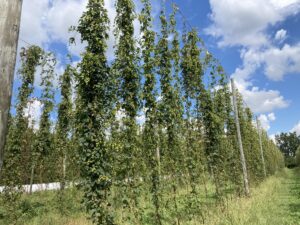

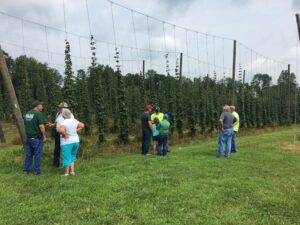
Figure 6.
Figure 7.
Figure 8.
Yield
In 2020, the estimated yield for the Cascade hops was 40 pounds of pelletized hops. Yield in Season 1 was significantly increased compared to 2020. Observationally, there were more cones per rope that were more tightly clustered together in Season 1. In Season 2, observationally there were a significant number of cones that were tightly clustered in abundance on the plants, as can be seen in Figures 7 and 9.
In Season 1, approximately half of the Cascade variety was harvested prior to quality analysis indicating that the hops were well below industry standard and not sellable to commercial craft brewers. This harvest yielded 102 pounds of pelletized Cascade hops as detailed below. This is approximately 0.83 pounds per plant.
Picked Row 1 on 09-26-21 Processed 09-30-21 37lb pellets
Picked Row 2 on 10-02-21 Processed 10-05-21 45lb pellets
Picked Row 3 on 10-09-21 Processed 10-21-21 20 lb pellets
Table 1. Harvest timing and yield for Season 1 at Scott Farms.
In Season 2, harvest of the Cascade variety of hops started about 15 days earlier than in 2021 in mid-September. The initial harvest yielded approximately 2 pounds of wet hops per plant. Harvest lasted 17 days with the yield per plant decreasing to a season total of 0.952 pounds of wet hops per plant. Table 2 shows harvest yield data for the Cascade variety in 2022. For the newly planted Michigan Copper variety, the total yield was approximately 133 pounds or 0.33 pounds per plant wet. The Nugget variety was not harvested in Season 2; this is not uncommon for a hop variety in its first season of production.
Harvest Date |
Wet Weight (lbs) |
9/11/2022 |
132 |
9/23/2022 |
80 |
9/24/2022 |
75 |
9/27/2022 |
74 |
9/28/2022 |
57 |
Season Total |
418 |
Table 2. Harvest timing and yield for Season 2 at Scott Farms.
Figure 9.
In comparison, the Cascade variety at the hop yard at the OSU South Centers yielded 1.13 pounds of wet hops per plant in 2021.[1]
[1] This weight is prior to pelletizing, while the figures from Scott Farms are for pelletized hops. Pelletizing results in loss of weight, although difficult to measure. In Season 2, dry hops will be weighed prior to pelletizing for better comparison.
Quality
Season 1 quality was mixed. As discussed above, there were many more cones produced in Season 1 than in previous crops. However, the size of the cones was much smaller than in previous years. Cones from the yard were also smaller than Cascade cones grown ornamentally on the farm away from the hop yard, as seen in the attached photograph (Figure 10 and Figure 11) with ornamental plants on the left and plants from the yard on the right. There are multiple variables that may have caused this smaller size.
- The plants were not exposed to the lighting as early as they should have been. As discussed above, supply chain issues created delays in the installation of the lighting. Based on this factor, the lighting period was shifted in 2022 and in future years would likely be shifted even earlier.
- The plants may not have had enough nutrients to last through the growing season. Plants may not have had enough nutrients to sustain the additional vegetation and produce larger cones.
Additionally, hop quality is measured based on lab analysis of the acid contents of cones using a mass spectrometer. The industry standard for Cascade hops is alpha acid content of 4.5-7.0% and beta acid content of 4.8-7.0%.[1] Analysis of Cascade hops from OSU South Centers in 2021 indicated alpha acid content of 7.8% and beta acid content of 5.0% prior to pelletizing. Analysis of Scott Farms pelletized Cascades in Season 1 indicated alpha acid content of 3.2% and beta acid content of 2.5%. As discussed previously, this rendered the Scott Farms Cascades from Season 1 not sellable for use in commercial brewing. This analysis was completed on hop pellets, the final product from Scott Farms. However, it is possible that quality issues could be the result of processing rather than growing conditions. Experience from prior growing seasons indicates that this could be the case.
The quality of hop cones harvested in Season 2 was substantially improved compared to Season 1. A lab analysis of four samples of wet Cascade hops conducted on September 19, 2022 showed the hops alpha and beta acid levels as detailed in Table 3. These alpha and beta acid levels were largely within or in excess of industry standards. However, in Season 2, the cone sizes remained smaller than expected. Again, cones from the yard were smaller than Cascade cones grown ornamentally on the farm away from the hop yard, as seen in the attached photograph (Figure 12) with ornamental plants on the left and plants from the yard on the right.
Analysis ID |
Alpha Acids, % |
Beta Acids, % |
AZ32579825 |
8.1 |
5.3 |
AZ11679825 |
6.8 |
4.7 |
AZ35679825 |
7.9 |
3.7 |
AZ20779825 |
10.5 |
4.6 |
Table 3. Lab analysis results of Cascade hops harvested in Season 2.
[1] Variety Manual: 2016 Update (n.d.). Hop Growers of America. Retrieved from https://www.usahops.org/cabinet/data/2016_VarietyManual%20%281%29.pdf
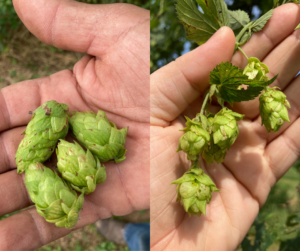
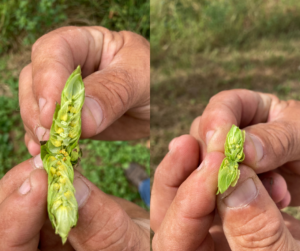
Figure 12.
Income
Season 1 income to date is $0 because of the issues with quality discussed above.
Season 2 income for 2022 was $340 total as of the writing of this report. After processing and packaging, hops are shelf stable and can be sold throughout the year. Additional income is expected throughout the year as sales continue to occur. There are an estimated 120 lbs.- 150 lbs. of hop pellets in storage for sale from the 2022 harvest.
Fertilizer
Table 4 below details the fertilizer applications to the hop yard at Scott Farms for 2020, 2021 (Season 1), and 2022 (Season 2). In total, fertilizer application in 2020 was 215.2 pounds of Nitrogen actually applied per acre. In total, fertilizer application in Season 1 was 265 pounds of Nitrogen actually applied per acre. Using dry and liquid fertilizer in the irrigation system, 247.44 pounds of nitrogen was applied over the course of Season 2. In comparison, the hop yard at the OSU South Centers received 300 pounds of Nitrogen fertilizer (28% UAN) per acre through the drip irrigation system over a seven-week period in the 2021 growing season.
Compared to 2020, fertilizer use increased in Season 1 while yield increased significantly. Fertilizer use decreased in Season 2 compared to Season 1, while yield increased slightly.
As previously discussed, lack of some nutrients and the timing of nutrient availability may be one reason for the reduced size of the cones produced in Season 1 and Season 2.
Fertilizer Usage |
|
|
2020 |
|
|
Application Date |
Fertilizer type |
Rate |
3/15/2020 |
19-19-19 |
600 lb/acre |
5/1/2020 |
28% UAN |
15 gal |
5/28/2020 |
28% UAN |
20 gal |
5/28/2020 |
20-10-20 Pro Sol |
10 lb |
2021 (Season 1) |
|
|
Application Date |
Fertilizer type |
Rate |
3/8/2021 |
19-19-19 |
600 lb/acre |
4/12/2021 |
28% UAN |
15 gal |
5/8/2021 |
28% UAN |
10 gal |
6/1/2021 |
28% UAN |
10 gal |
6/14/2021 |
28% UAN |
12 gal |
6/28/2021 |
20-10-20 Pro Sol |
20 lb |
6/30/2021 |
20-10-20 Pro Sol |
20 lb |
7/27/2021 |
20-10-20 Pro Sol |
20 lb |
2022 (Season 2) |
|
|
Application Date |
Fertilizer type |
Rate |
4/17/2022 |
6-24-24 |
450 lbs total |
5/10/2022 |
28% UAN |
13 gal |
6/1/2022 |
28% UAN |
10 gal |
6/25/2022 |
28% UAN |
15 gal |
7/8/2022 |
19-19-19 |
600 lbs total |
Table 4. Fertilizer applications in the hop yard at Scott Farms 2020-2022.
Electricity
The lighting system in this project added an additional input to hop production – electricity. To understand the use and cost of this additional input, electricity usage and costs were tracked and compared to electricity use in 2020. Table 5 includes these details.
|
Electricity Usage 2020 |
|
|
|
|
Bill Date |
Service Date |
kWh |
Cost |
|
|
June |
May - June |
688 |
$96.37 |
|
|
July |
June - July |
283 |
$45.56 |
|
|
August |
July - Aug |
1094 |
$148.14 |
* |
|
|
|
|
|
|
|
|
Electricity Usage 2021 |
|
|
|
|
Bill Date |
Service Date |
kWh |
Cost |
|
|
June |
May 24 - June 23 |
441 |
$62.92 |
|
|
July |
June 23 - July 23 |
1418 |
$182.35 |
|
|
August |
July 23 - Aug 23 |
652 |
$89.08 |
|
|
|
|
|
|
|
|
|
Electricity Usage 2022 |
|
|
|
|
Bill date |
Service Date |
kWh |
Cost |
|
|
May |
Apr 23 - May 20 |
238 |
$40.89 |
|
|
June |
May 21 - June 22 |
913 |
$132.29 |
|
|
July |
June 23 - July 22 |
1576 |
$215.51 |
|
Table 5. Electricity use and costs 2020 - 2022 at Scott Farms.
* this period included Oast House electric for hop harvest, including extra drying and heating cost.
The best month for understanding the change in electricity usage and cost attributable to the lighting system in Season 1 was July. In Season 1, lights were started on June 6, 2021, so the cost of the system would only appear for a portion of the June billing month. Lighting was active for the entire July billing period. Thus, for Season 1 it was estimated from the July billing for 2020 and 2021 that the lighting system utilized 1135 kWh of electricity with a cost of $136.79.
In Season 2, the best month for estimating electricity cost on a kWh basis was June because the lights were started in May and turned off in July. In addition, there were no hops processed for other growers in June. Again, using electric bills for the Season 2 compared 2020 - the year before the lights were installed - the lights used an estimated 660 kWh of electricity for a cost of $98.62 in Season 2.
Water
The hops at Scott Farms were generally watered every 7 days in Season 1, depending on the rainfall during the preceding week as well as nutrient, insecticide, or herbicide applications needed for insect, fungus or mold pressure.
The total amount of water used in Season 1 was estimated at 203,655 gallons. This estimated to be close to the same amount used in the preceding year.
The 2022 growing season was wet with just under 25 inches of rain at the farm from May through August and 30 days with recorded rainfall. Thus, irrigation was not utilized as heavily in Season 2, with only five irrigation sessions over the course of the season using an estimated 68,000 gallons of water.
[1] All references to data from the OSU South Centers hop yard are from “Hop Production to Enhance Economic Opportunities for Ohio Farmers 2021” by Brad Bergefurd, Extension Educator, South Centers, Thomas Harker, Horticulture Research Associate, South Centers, Ryan Slaughter, Horticulture Research Assistant, South Centers, and Wayne Lewis, Farm Manager, South Centers.
[2] This weight is prior to pelletizing, while the figures from Scott Farms are for pelletized hops. Pelletizing results in loss of weight, although difficult to measure. In Season 2, dry hops will be weighed prior to pelletizing for better comparison.
[3] Variety Manual: 2016 Update (n.d.). Hop Growers of America. Retrieved from https://www.usahops.org/cabinet/data/2016_VarietyManual%20%281%29.pdf
Educational & Outreach Activities
Participation Summary:
To share information about this project and outcomes, activities were documented with photos and videos. Throughout Season 1, photos and videos were shared regularly on Scott Farms’ social media, along with information about the project and progress. Ten Facebook posts and 6 Instagram posts shared information such as the purpose and goals of the project, growth and progress of plant and flower development, and learnings from Season 1. Facebook posts reached an average of 1,143 users per post. The reach of all 10 Facebook posts was 11,436 as of this writing. Facebook posts were shared 39 times, commented on 54 times, and had 704 total likes and reactions. Instagram posts had 84 likes and 6 comments as of this writing.
On January 29, 2022, Erik and Hannah presented “Farm to Glass: Growing and Marketing Hops for the Craft Brewing Industry,” at the Ohio Farm Bureau Federation’s Winter Leadership Experience for young agricultural professionals. The presentation included an overview of the farm’s experience with hops as a unique crop in Ohio and shared information about this project, including goals and initial observations from Season 1. Approximately 15 people attended the presentation. The outreach opportunity was also shared on the Scott Farms Facebook page in December 2021, reaching over 520 users. Slides for this talk are included as a work product in this report.
Throughout Season 2, photos and videos were shared regularly on Scott Farms social media, along with information about the project and progress. In 2022, nine Facebook posts and 4 Instagram posts shared information such as the purpose and goals of the project, growth and progress of plant and flower development, and learnings from the first growing season. Each Facebook post reached an average of 1,253 users. The reach of all 2022 Facebook posts was 11,284 as of this writing. Engagement with Facebook posts included shares, comments, likes, and reactions. Facebook posts were shared 47 times, commented on 16 times, and had 301 total likes and reactions. Instagram posts had 244 total impressions as of this writing.
On August 13, 2022, a “Hops Field Night” was hosted on the farm as an opportunity to showcase this project in partnership with James Morris an educator with OSU Extension in Brown County, Ohio. Twenty-three people attended the field night where James and Erik Scott provided an overview of hops production as well as this project and initial learnings. Participants came from five different counties in southern/central Ohio and reported managing over 1,500 acres currently in agricultural production. Evaluations from attendees indicated a positive gain in their understanding of photoperiod manipulation in hops.
With the videos, pictures, and information gathered throughout this project, we created a multimedia video explaining the project and its initial outcomes. The approximately 11-minute video, “Enhancing Midwest Hop Productivity Using Photoperiodism: An On-Farm Research Project,” discusses the project’s rationale, methods, and learnings in an engaging manner using photos, videos, and narration. The video is housed on the Scott Farms website where it will continue to be available for public who are interested in the project. The video was also shared via social media. At the time of writing, it has been viewed approximately 50 times. The video can be viewed at: https://www.scottfarmsohio.com/hops.html
On February 19, 2023, Erik Scott shared learnings from this project at the 2023 Ohio Hop Growers Guild Annual Conference. The conference is intended for current and aspiring hop growers across the state and region. Approximately 20 people attended Erik’s talk called, “Enhancing Midwest Hop Productivity Using Photoperiodism: An On-Farm Research Project,” with extended question and answer following the presentation. Additional resources, including the project video and ways of accessing the project report via SARE were shared with audience members. Slides for this talk are included as a work product in this report.
Learning Outcomes
While it appears that there are potential advantages to utilizing a lighting system in hops based on this project, there are also challenges associated with the system.
First, the yield and quality of hops in Season 1 did not meet expectations and underperformed compared to the yard at the OSU South Centers where lighting was not used, but Season 2 yielded a similar, although slightly lower, quantity of hops that exceeded industry standards for quality while using less nitrogen. In the future, more rigorous statistical analysis could help better understand these differences.
The lighting system was time and capital intensive to install, but it was relatively inexpensive to operate and had an added benefit of allowing more control in predicting and staggering the timing of hop harvest to better match resources on the farm. In 2022, yield data from this project helped clarify the timing windows for harvest that will be used in future growing seasons, including that harvest needs to occur within an approximately two week window before yields drop off noticeably. Growers interested in such a system will need to carefully consider ease of access to electricity infrastructure and the potential engineering needs to operate the lighting system, both electrical considerations and the trellis considerations.
We also learned that the timing of the lighting is extremely important. While earlier in the season seemed to perform better, there are still questions about the best time in the season to start using lights, the optimal time to stop the lighting, and the right timing for fertilizer applications when using lights. All things to consider for future growing seasons in which lights will likely continue to be used.