Final report for FNC22-1347
Project Information
Our certified organic farming practices and direct-to-consumer marketing deliver fresh and nutritious vegetables to the eaters in Lawrence and the Kansas City area. Currently, Mellowfields Farm cultivates almost 3 acres of Kansas River bottom soil. Along with a team of 5 employees, we start, plant, cultivate, harvest and sell over 50 varieties of vegetables for sale directly to eaters through webstore and farmers market as well as through grocery stores, food hubs and restaurants.
We will be looking at how the yield of high tunnel tomatoes are affected by the use of a farm-made indigenous soil microbial inoculant similar to Korean Natural Farming methods, but simpler and cheaper to implement using locally sourced ingredients. Improving soil health in high tunnels is an on-going struggle for many. The “desert effect” from lack of rainfall in tunnels, combined with frequent tillage, can lead to the destruction of microbial diversity. Many methods of replenishing these beneficial bacteria and fungi can be expensive (purchased inoculants), tie up valuable farm real estate (covercropping), or be laborious (vermicomposting, etc.). By producing our own farm-made microbial inoculant, we hope to increase the soil’s microbial community (ecologically sound), increase yields & decrease costs (economically viable), and save the farmers’ time through this simple system (socially responsible).
Four ingredients: potatoes, leaf mold, salt, & water. ‘Wild caught’ soil microbes from leaf mold proliferate by feeding on a dextrose nutrient media (potato water). In this system, most ingredients would be available on-farm (potatoes & leaf mold). The only ingredient to purchase-in would be salt, which is easily accessible. If potatoes aren’t grown on-farm, they are cheaply accessible from any supermarket.
FINAL REPORT - Project Summary
Explanation of Problem & Solution (why & what)
High tunnels often have degraded soil health with low microbial life due to lack of rainfall and over tillage. In our project, we looked at the potential soil health benefits of using a farm-made microbial inoculant and its effect on the yields of high tunnel grown tomatoes. The inoculant recipe, called JADAM Microbial Solution (JMS), comes from the JADAM system of natural farming, which is an off-shoot of the Korean Natural Farming (KNF). It consists of anaerobically fermenting four ingredients: water, salt, cooked potatoes, and a good quality compost, and applying it diluted 1:20 to the soil.
Research & Educational Approach (how & with whom)
In Year 1, we built and tested the inoculant brewing station.
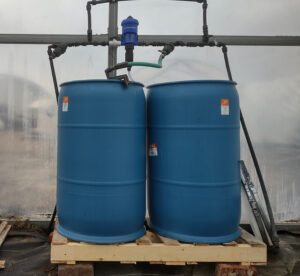
In Year 2, we ran our experiment. We made weekly batches of JMS and applied through drip tape to three successions of tomatoes. In each succession, we had an experimental row that received JMS and a control row that was irrigated separately. We recorded the harvest yield numbers from each row for all three successions to determine yield difference.
At the end of Year 2, we held a field day for a local farming group with a discussion of the project and its results, as well as a farm tour. 25+ people joined us to learn about the project.
- Develop a simple, affordable system for making and applying farm-made microbial inoculants within high tunnel-grown tomato production (Year 1)
- Determine the effect of farm-made microbial inoculant on overall yield of tomatoes through multiple successions over the course of a full season (Year 2)
- Share findings through field days and social media (Year 2)
Research
YEAR 1:
In 2022, during the first year of my 2-year SARE grant, I worked on building the system that I used to run my experiment in 2023. It consisted of the following:
- Two 55 gallon barrels
- A Dosatron siphon fertilizer injector
- An irrigation pump
- 200 mesh water filter
- Various pieces of black poly irrigation tubing and fittings
- A "bioextractor" mesh bag
- An InstantPot pressure cooker.
I set up my barrels on a stable pad in a protected location by an outbuilding near electricity. I installed the Dosatron injector on the wall behind the barrels, in a position above and between the barrels so that its siphon tube could drop into each barrel. With standard 3/4" poly tubing, I brought water from a spigot to the siphon injector, installed a cheap 200 mesh water filter, then built a bypass around the siphon injector so that I could divert the water from flowing through the injector when not in use. On the other side of the bypass, the poly tubing connected to a small irrigation pump to make sure the water pressure was high enough to get to the hoophouses where the experiment will be held. To test the system, garden hose was used to move finished and diluted microbial solution (JMS) to each of the hoophouses. I plan to use lay flat hose in the future to provide better flow. Or another version might be to put the barrel system directly in a hoophouse in order to shorten the distance the JMS has to travel and avoid extra hoses laying around. In this version the barrels would need lids of some sort to protect from direct sunlight.
Testing my system went smoothly once it was installed. I filled a barrel with untreated well water (probably 50 gallons full) with a garden hose and dissolved 1/2 lb. of salt by stirring in with a shovel. I checked to make sure the water temperature in the barrel was above 65 degrees F before beginning the process. At that point, I cooked potatoes in the InstantPot and mashed them up in the pot after they were cooked. I added the mashed potatoes (1 lb) and leaf mold compost found on the property (1/2 lb) in a "bioextractor" mesh bag. I put the mesh bag in the water and gently massaged the contents to encourage them to dissolve into the water. I placed a rock in the bottom of the bag and hung it on a tool handle positioned across the barrel's top so that it was suspended right below the water's surface and couldn't accidentally float up.
After a couple of days (1-3 days depending on water temperature), bubbles begin forming on the water's surface, which indicates microbial activity in the water. When the bubbles thicken into a disc, the JMS microbial solution is at its peak. A clear ring begins to form around the outside of the bubbles to indicate that microbial life is beginning to run out of food and die off, which is the sign to use all of the solution while it's still teeming with life.
When the solution was ready to use, I placed the siphon tube in the finished barrel of JMS, turned both shut-off valves on the bypass to open the siphon injector, and turned water on at the spigot. The injector was set to 20:1 dilution rate (water : JMS), drawing the solution out of the barrel, into the irrigation line, out to the hoophouse. I applied the inoculated water directly and deeply to the roots of the plants using drip tape.
The goal of the system was to be quick and easy to use, and after the initial setup, I found it to be very simple to operate. After the potatoes are cooked, it takes about 10 minutes to get a batch started. I would check it a couple times a day to see if the JMS was mature and ready to apply. With the use of a float valve for filling the barrel, and an irrigation timer for shutting off the irrigation at the end, it was a very "set it and go" system. When I use farm-grown b-grade potatoes as my starter, it costs less than $1 per 50 gallon batch (only paying for the salt), which seemed to be enough JMS to apply to all three hoophouses each week. My estimation is that this will amount to about $20 per season of total cost for all 3 hoophouse successions of tomatoes. Cheap and easy, I hope. I'm looking forward to seeing what the experiment results reveal!
YEAR 2:
In order to inoculate the soil before we transplanted tomatoes in the ground, we made and applied a batch of JMS using the above process. We planted our first succession of tomatoes in late April, the second succession roughly one month later in late May, and the third succession roughly one month later in early July. We kept up weekly applications of JMS throughout the 2023 growing season before the last planting was killed by a hard freeze at the beginning of November. We harvested tomatoes twice a week for each planting throughout the growing season and recorded the harvests each time. We removed the first planting by the beginning of September when the yields had dropped to negligible amounts, and the second planting was removed by the beginning of October, to make room for our fall lettuce successions.
We recorded in our farm's Harvest Log the yield for the control plantings and experimental plantings separately with each harvest, in order to make calculations at the end of the season easy. In the end, our Control plantings yielded a total of 1863 lbs of tomatoes (at an average of 621 lbs per succession row).
Our Experimental plantings yielded a total of 2173 lbs. of tomatoes (at an average of 724 lbs per succession row). That is an average yield increase of 16.6% in the rows that were applied with JMS, compared to those that were not.
For us, these results clearly suggest there are real benefits of using this farm-made inoculant. We believe there is a need for additional research in this area!
Educational & Outreach Activities
Participation Summary:
The bulk of our outreach was done in the second year of our grant project.
On October 4, 2023, we held a field day tour and group discussion with members of our local growers association, Growing Lawrence. The event was advertised on our social media, as well as to the Growing Lawrence membership. We had more than 25 farmers and extension professionals attend. We had an engaging conversation about the role of microbial diversity in soil health, and explained our project and its results. We gave the attendees a tour of the farm and showed them the system we set up.
Learning Outcomes
Research Conclusions & Farmer Learning Outcomes (how it went & what we learned)
- Our results showed that the experimental rows had 15% higher yields than the control rows. Though this was not a perfectly controlled scientific experiment, we believe these findings suggest that this topic is worthy of further investigation.
- A challenging aspect of this project was timing the JMS applicatoins at the optimal time, when microbial life was at its peak and before it started to decline. Because of this, we didn't always receive the maximum benefit of each application. This suggests that weekly applications are not necessary to receive some soil enhancing benefits.
-
This batch of JMS was near optimal timing for application. The bioextractor bag and a thermometer wire hang down into the barrel from a short piece of lumber. - The 55 gallon batches were larger than we needed for our project, even when all three successions of tomatoes were being fertigated at the same time.
Farmer Adoption Actions (what we'll do differently moving forward)
- In the future, we will continue to make and apply JMS in our high tunnels for all crops, not just tomatoes.
- We may reduce applications to only a couple times a month, rather than weekly, to see if there is any noticeable difference.
- We would like to experiment with field application of JMS, and not just in the high tunnels.
- We are also interested in applying JMS to our compost piles before spreading it on the field or in the high tunnels.
- The most expensive part of the system was the Dosatron fertilizer injector. If we were to do it again, we might look for a cheaper Venturi type injector that would work similarly.