Final report for FNE16-841
Project Information
This project tested methods for growing, storing, forcing, and marketing organically produced Belgian endive in 2016 and 2017. This vegetable is grown from the roots of plants grown in the summer, harvested in the fall, and stored in a cooler until they are ready to be forced on a weekly basis during the winter to produce high value Belgian endive chicons. They are ready for sale about 12 weeks after forcing starts. We trialed Witloof Bruxelles (Cicoria Witloff de bruxelles) an open-pollinated seed we had had modest success with in the past, and Triviso, both from Seeds from Italy, "Atlas", directly from the Netherlands, and "Totem F1", from the US, both hybrid varieties. Open-pollinated seed had zero yield for us.
Planting took place in June, harvest in October or November or at about 140 days (ideal), storage immediately in a walk-in cooler for 2-3 weeks, and forcing in a chamber for 21 days (goal). The best diameter for forcing was 1.5 inches. Being beginners, our labor was higher and yield was lower than what we expect going forward. Our yields varied from 300 to 490 pounds per 200 foot bed. Each tray of 200 pounds of roots yielded 80 pounds of chicons per tray. With all labor and expenses removed, a wholesale price of $4.50/pound, the $360 gross income per tray decreased to $29 per tray, $50.75 per bed, and $2,030 per acre. For projection's sake, just increasing the price per pound to $5, increasing they marketable chicons to $110 per tray would net $232 per tray, $406 per bed, and $16,240 per acre.
While no booklet was produced, this report is written in that form to be printed as a guide for growing and selling organic Belgian endive.
Our project tested the feasibility of growing and marketing organic Belgian Endive chicons, prized by restaurant chefs and retail customers, as a way for organic farmers on the North East to produce winter income. We documented our methods and results and had a plan to distribute them through SARE, conference presentations, on-farm demonstrations, and a booklet “How to Grow Organic Belgian endive in the Northeast”.
The principal objective for 2016 was to produce organically the quantity and quality of Belgian Endive roots suitable for forcing as called for in our proposal. A secondary objective was to upgrade our existing forcing room and purchase or build the hydroponic and soil based forcing equipment. In 2017, the objectives of our efforts were (1) to complete the first production cycle of chicons from root forcing through actual marketing and (2) to complete the second cycle of seeding, weeding, harvesting, storing, and beginning the forcing of Belgian Endive chicons.
This report seeks to fill that gap to provide organic farmers interested in boosting winter income by marketing Belgian endive with information about what it entails. It presents a detailed, step by step description of our efforts from ordering seed to marketing.
Winter Income is always problematic for produce farmer, especially in the months of January and February. Even with the use of high tunnels, fresh greens are in short supply, and Belgian endive can help fill this gap, keep customers engaged, and even create some excitement with a unique and highly unusual gourmet product. In addition, it is a good way of keeping employees gainfully occupied during the winter months, thus aiding in employee retention from season to season. Finally, it is a challenging and fun adventure!
Jade Family Farm is located in central Pennsylvania 5 miles from the Borough of Port Royal on the slopes of Tusarora Mountain. Its blessed with well drained, good soil and ample water for irrigation. We had tried growing and marketing Belgian Endive three times previously on an ad hoc small volume basis with mixed success.
A search for existing descriptions of small organic production turned up very little, and no detailed, step by step description of either how to do it or the financial feasibility doing so was found. Our grant proposal provides a more detailed account of this search.
Cooperators
Research
OBTAINING SEED
We planned to test two varieties of Belgian endive. Our search for seeds took well over two months. We learned that the folks at small seed companies were wonderful and all extremely helpful.
Several companies, including High Mowing and Johnny’s Selected Seeds offer Totem F1, but trying to locate another hybrid variety was challenging and time-consuming. Kristin Dubard at Johnny’s did everything she could to help, including giving us a list of seed companies that might carry one, and we searched the catalogues of a number of seed companies we found on-line. We were able to obtain Witloof Bruxelles (Cicoria Witloff de bruxelles) from Seeds from Italy, an open pollinated variety we tried in the past with only modest success. Dam Seed Company in Ontario carried “Flash,” one of the varieties recommended in our literature search but unfortunately we learned Canadian seed companies are prohibited from shipping to the U.S. Dan Nagengast at “Seeds from Italy: in Lawrence KS informed us of a radicchio variety “Triviso” grown just like Belgian Endive which we included in our trials. Martin Walsh at Baker Creek seeds was kind enough to request his purchaser to contact the Dutch grower (PeterPik) who supplied “Flash” to the Canadian seed company. We contact PeterPik in the Netherlands who in turn referred to their supplier. Eventually we contacted a Netherland’s producer who on their own kind initiative provided us with 100,000 seeds of the variety they recommended, “Atlas”, free of charge. As of this writing (December 2018), Totem is still the only readily available hybrid variety in the U.S. for the small scale grower.
GROWING THE ENDIVE ROOT
We found growing the endive root to be simple and easy. We prepared the field as normal and fertilized according to a soil test (we used Kinsey Ag lab in Charleston, Missouri). We had read in many places to avoid excess nitrogen, as this would encourage excess leaf growth at the expense of root development; however, we used 400 pounds/ acre of 13% protein meal in both 2016 and 2017 and did not experience excess leaf growth at all. It should be pointed out that this protein meal—containing feather meal, blood meal, and meatmeal—is a quick release fertilizer and by the time the roots really began to put on girth in late Summer, it will have mostly have disappeared.
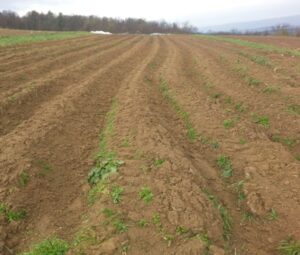
We planted on 30” raised beds made with an even-flo raised bed plastic layer, without the plastic. This created a raised be about 5 inches high. We then watered the beds, waited for the first flush of weeds to sprout (7 to 10 days) and then flame weeded the beds. Only then did we plant the endive seed. This is important because endive seed can germinate very quickly and can emerge before all but the most precocious weeds. The O.P. variety we planted had emerged from the ground in 2-3 days, while the Atlas took 5 and the totem 7. We seeded with a Jang precision seeder, xy24 seed cartridge, front sprocket 11 rear sprocket 11. This proved to be much too thick, and we subsequently spent a lot of time thinning the crop. In 2017 we switched to a xy12 cartridge, effectively halving the seeding rate. This still proved too thick for the Atlas, but the Totem did not germinate as well and so did not require thinning in 2017. We seeded two rows in two of the beds, and three in three beds. Before seeding in 2017, we did a germination test on seed held over from 2016. Atlas seed held over from 2016 and planted in 2017 suffered no loss in viability, while totem seed held over from 2016 did not germinate reliably in 2017.
The endive seed was planted in 2016 on June 4th and June 7th. This gave us plenty of time for the roots to grow to full size before the end of the growing season. Good weed control is essential in Belgian endive production as the plant does not compete well against weeds. In addition to pre emergent flame weeding, each bed required hoeing once (about two weeks after planting) and two moderate hand weedings (about five weeks and two months after planting). After that, the endive foliage formed a dense enough canopy that no new weed seedlings emerged. Due to the seeding rate being too thick in 2016, we spent a lot of time hand thinning at the time of the first hand weeding in order to attain the 4 to 6 inch spacing between each plant required for full sized roots. We also thinned part of one bed to only a three inch spacing, just to test whether the literature was correct in asserting that a minimum of four inches in necessary for full sized root development. Indeed, the literature was correct. Total time spent in 2016 hoeing, thinning and hand weeding the crop (five beds, at 200 feet long, three rows in 3 beds and 2 rows in two beds) was 26 hours! Ouch!
Endive grows slowly at first and the roots develop girth slowly.
HARVESTING THE ENDIVE ROOT AND YIELDS OF ROOTS
We harvested the roots by undercutting them with a bar attached to the tractor’s three point hitch for this purpose (the same implement we use to harvest carrots, parsnips, and other similar crops common on small vegetable farms). Roots were then pulled from the ground, the tops trimmed to within 1 inch of the root, and placed in plastic lined crates or boxes for storage. This process took some time—approximately 5 to 8 person- hours per 200 foot bed, depending on who was working. Endive root holds tight to the soil and, even after undercutting, requires some effort to pull out. Trimming the tops (we used handheld bypass pruners) seemed to take the most time. In 2017, we tried mowing off the tops both with a standard rotary lawn mower and with a high wheeled model (Billy Goat). Both machines ruined too many roots, and it became clear the machines’ time savings were not worth replacing hand trimming. Also, many of the tops were trimmed incompletely or inadequately, necessitating further hand labor. Part of the reason so many roots were damaged was due to the unevenness of the beds and the fact that neither mower was able to fully straddle a bed. Given a different planting system, (perhaps planting on narrow ridges or, given a powerful enough digger, simply planting in flat ground?) mechanical mowing might be a better option. We did, however, significantly reduce harvest time by trimming the tops with a hedge trimmer before the roots were dug. While this was a little hard on the back, it only took 20 to thirty five minutes, depending on who was doing it, to trim a two hundred foot bed (two rows in the bed).
Yields of roots per bed varied. The lowest yielding bed (200 feet long) produced 160 pounds of roots, and the most we got from a 220 foot bed was 550 pounds of roots. Why such variability? Mostly it had to do with the spacing of the plants. Too close together, and the roots do not grow big enough to produce a marketable chicon, too far apart, and the root grows extra large to no purpose. As is covered in greater detail under “Yield of Chicons”, a jumbo sized root does not necessarily correspond to a jumbo sized chicon! Therefore, to measure success merely by weight of roots harvested is misleading.
Based on our experiences is the forcing chamber, the ideal diameter of roots is 1 ½ inches at its point of greatest girth. We found that to achieve this, a spacing of 4 inches within the row is ideal. Less than this seriously reduces the number of usable roots, and greater than 4 inches causes the roots to grow large to no purpose, thus reducing the yield of marketable chicons (but not weight of roots). However, it is better to have the roots spaced further apart than too tight: 5 or 6 inch spacing within the row is perfectly acceptable.
We experimented with both 2 rows per 30” raised bed and 3 rows per bed. The extra row created extra work in weeding and thinning, cost extra seed, and did not yield more usable roots. Thus, two rows per bed are recommended. Growers not using raised beds will want to space the rows a minimum 18 inches apart.
We learned that it is extremely important to harvest the roots on time! (See section “Yield of Chicons”). In 2016 we harvested from 140 to 145 days after planting, slightly later than the seed producer’s recommended days to maturity, with only a few roots showing signs of overage or bolting. In 2017 harvest was delayed until mid November due to labor shortages. As will be discussed later, this extra delay in harvesting led to many over mature roots and significant losses in the forcing chamber.
2016: We monitored moisture closely and irrigated when necessary. Growth looked good, but the roots really began to size up from about mid-September to mid-October, a little later than we anticipated. We began harvesting on Oct. 24th, and finished Nov. 5th. Harvesting took place between 140 and 154 days from seeding, a little longer than the 140 day maximum time we said in our proposal. A bar digger pulled by the tractor went under the raised beds to facilitate harvest. This was very successful. Almost no roots were broken, and harvesting was easy. We discarded roots too small for forcing (i.e. less than the 1.25 inches diameter minimum required), trimmed the tops to between a half inch and an inch from the crown, packed the roots in plastic bags in wooden crates, and stored the crates in the walk-in cooler. We harvested approximately 80 boxes of roots suitable for forcing, each weighing approximately 18 pounds each for a total of 1,440 pounds. Our grant narrative spoke in terms of number of roots (not pounds) with a goal of having 2400 roots.
CONSTRUCTING THE FORCING CHAMBER
The two crucial factors in a forcing chamber are complete darkness and temperature control; therefore, we constructed the chamber with those in mind. We built the forcing chamber in a corner of our packing room. This is inside an unheated barn, originally built as a confinement veal facility. The floor is concrete and already had a drain. We framed out an area 10 feet by 19 feet and covered the inside walls with metal siding. We chose metal in order to prevent rodents from gaining entry to the forcing chamber. Fiberglass insulation was put in between the wall studs, then the entire outside walls were covered with an 8 mil sheet of black plastic, in order to exclude light from the chamber. Any gaps in the exposed framing were filled with expanding foam insulation, and the plastic edge was taped to the framing top plate, also to exclude light. The ceiling was formed by placing rigid polystyrene panels over the barn attic truss bottoms, then fiberglass insulation over that. Underneath the polystyrene, the entire ceiling was again covered with 8 mil black plastic to exclude light. The door opening was made 4 feet wide and the “door” consisted of a sheet of 3 inch polystyrene, wedged against the frame with a heavy object. Probably a real door would be better, and the farmer intends to install one later. This basic construction was effective in blocking all light from entering the forcing chamber. We also insulated the floor before commencing forcing in 2017. For our needs, this chamber was much too big. Even at peak production, we did not require more than two towers of forcing trays measuring roughly 3 ½ feet by 3 ½ feet by five feet high, usually we needed only one such tower. Add the water reservoir and piping (see below) and space to work in and our chamber was still about twice as large as it needed to be. This made constructing and heating the chamber more difficult and expensive than it should been. In year two we installed a curtain halfway across the chamber, this helped somewhat to reduce heating costs and provide an even temperature for forcing.
FORCING THE ROOTS HYDROPONICALLY
Endive must be stored for a minimum of two to three weeks before it is ready to force. Forcing must be performed in absolute darkness; otherwise the chicons will be green, hairy and unpleasantly bitter. Our measures for eliminating light (see section on constructing the forcing chamber, above) were successful and the chicons grew up pale yellow and smooth, without a hint of green.
The roots were packed tightly into three foot by three foot hydroponic flood trays. These were nestled inside stackable wooden forms, with 12 inches headspace between the top of the tray and the bottom of the next one. This gave ample headspace for packing the trays, growth of chicons, and harvest. We stacked the forms in towers of three.
We used a 15 gallon tub for a water reservoir. As the growing chicons take up a lot of water, a smaller reservoir would be inadvisable. When replenishing the water supply, we added wrist temperature water rather than using unheated well water, to avoid uneven temperatures on the roots and stressing the heating system. Into the reservoir we placed a simple aquarium pump, the outlet of which led to a PVC pipe which emptied out into the southeast corner of the top tray. We then drilled a hole in the northwest corner of the top tray, just below the lip, and inserted a vinyl tube in it. This fed into the northwest corner of the middle tray. We then drilled a hole in the southeast corner of the middle tray and inserted a tube in in which led to the corner of the bottom tray, and from the bottom tray back to the reservoir. Thus, water was continuously circulating across the trays. All the materials needed for this setup are readily available at any hydroponics supply store.
The temperature of the forcing chamber is supposed to be kept between 58 and 64 degrees Fahrenheit. We used two portable electric space heaters to heat the chamber. However, we discovered that this was insufficient to maintain the temperature during very cold (below 15 degrees) weather during the first year. We had fewer problems maintaining the temperature the second year after we insulated the floor and installed the thermal curtain, but still had issues when there was even a momentary power interruption, causing the heaters to shut off, or when they did so out of mere capriciousness. The main effect of lowered temperature was slow growth of the chicons. Once temperature was brought back up, growth resumed at the normal rate, and we observed no loss in quality compared to those chicons which enjoyed adequate temperatures for their entire growth.
Much of the literature on Belgian endive production recommends keeping the water temperature five degrees warmer than the air temperature. We therefore placed a 100, later a 200, watt aquarium heater in the water reservoir. However, we discovered that this was insufficient to raise the water temperature even slightly above the air temperature. It also cost us a lot in electricity and succeeded in fusing the extension cord to the heater plug, indicating a safety hazard. After we abandoned the attempt to heat the water, no differences in chicon quality or speed of forcing were observed.
Ideally, the roots spend 21 days in the forcing chamber before the chicons are harvested. Our experiences in 2016- 17 did not bear this out, with times of 4 weeks to a month being the norm. Only by the end of the forcing season in 2018 did we achieve a 21 day time frame. Here it must be noted that, due to warmer weather, the temperature in the forcing chamber was higher than recommended, ranging from 62 to 70 degrees Fahrenheit. Surprisingly, the differences in chicon quality and yield at these temperatures were minor. In 2016-17, we experimented with adding OMRI approved fertilizer to the circulating water. We added 1 oz Neptune’s harvest liquid fish/ gallon of water and 10 fl/ gallon of Ful-power, a fluvic acid product. We saw no increase in size of chicon/ size of root, nor any increase in overall yield. We know that large scale producers do add fertilizer to their hydroponic solution, so more research in this area would be beneficial.
Conclusion: Forcing the roots was a much more forgiving process than we anticipated. That is to say, given good quality roots, sufficient water, and complete darkness, high quality chicons resulted even if the temperature in the forcing chamber was inconsistent. No added fertilizers to the forcing medium were needed.
SOIL FORCING
Traditional endive production is done in soil, not hydroponically. The available literature is very sparse when it comes to detailed descriptions of this process, but from what we could tell from the YouTube video we watched on the topic, the roots are placed in a large underground outdoor pit, then French people shovel sand on them. Presumably the climate is such in Northern France and Flanders that this creates a warm enough environment for forcing, and the sand provides both top pressure and darkness. As we do not have these conditions in Northeastern North America, we tried soil forcing the roots in boxes in the same forcing chamber we used for the hydroponic forcing. The boxes (13”x17” by 12” deep) were filled with organic potting mix and then the roots were inserted. Yields were comparable to hydroponically forced roots (8 pounds of chicons from 24 pounds of roots for Totem, 10 pounds of chicons from 26 pounds of roots for Atlas). However, it was hard to keep the soil off the chicons and trimming took longer. Also, it took time to cart in the soil and filling the boxes took longer. I do not recommend this method of forcing.
YIELD OF CHICONS
The yield of the open pollinated variety was zero, that is, we harvested no marketable chicons. Although chicons did grow, they were much too tall and loose and did not come close to commercial standards. In a traditional forcing system, where soil is placed on top of the roots, the weight of the soil pressing down on the growing chicons causes them to compact. As we did not have a system such as this in place, the chicons grew tall and gangly. However, the flavor was fine and they made for some delicious salads.
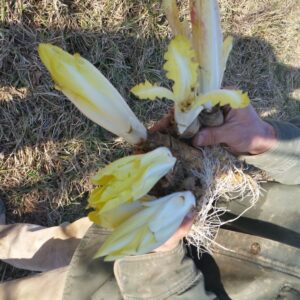
Both hybrid varieties preformed quite well. Roots were first trimmed to roughly the same length, and the tops sprayed off if they had any slimy bits on them from decomposed outer leaves. They were then packed tightly in the hydroponic flood trays. It took roughly 200 pounds of roots to fill one tray. Yield of marketable chicons varied. For chicons harvested in February and March, yield of marketable chicons per tray ranged from 80 to 110 pounds. The biggest factor in determining the total yield per tray was the number of roots in each tray, and was thus dependent on the size of the roots. Although a very small root produces no usable chicon, and the size of the chicon increases with the size of the root up to a point, a very large root did not translate into a very large chicon for us. Ideal size, based on our observations, was a maximum girth of 1 and ½ inch per root, with a weight of between .5 and .7 pounds.
We did notice a gradual decline in yields as the forcing season got later and later. By mid April the yield per tray had slipped to 55 pounds per tray, and the tray we harvested at the end of April yielded 20 pounds. While most of the roots were still alive for an April forcing, the chicons failed to form properly, with the leaves in the center of the chicon failing to grow, thus resulting in a hollow hearted head.
Our experiences in 2017-18 in the forcing chamber were a disaster. We did not harvest the roots on time, and therefore the chicons did not develop properly. We averaged 30 pounds of marketable chicons per tray of 200 pounds of roots, and most of these chicons were small, .2 pounds or less. While this was truly disheartening, we took some solace from the belief that anyone reading this report will be sufficiently aware of the importance of harvesting the roots promptly so as not to make that same mistake!
HARVEST AND STORAGE
Harvesting the chicons is fast and easy. They simply snap cleanly off the roots. After harvest, the chicons must be trimmed, with any loose or brown tipped leaves removed. We found out the hard way that the outermost layer of leaves (usually shorter than the rest) must be removed no matter what, as they quickly brown in storage. We also found that harvested chicons should be moved quickly to cold storage, or discoloration may occur. Like the forcing chamber, the storage facility must be completely dark, or the chicons will turn green and bitter. Chicons should store 2 to 3 weeks with no loss in quality.
We read in numerous sources that the roots leftover after the chicons are removed make a healthy and delicious livestock feed. However, evidently the swine, cattle and goats we tried feeding them to were unfamiliar with these sources, as they were all utterly disinterested in eating the spent roots.
MARKETING AND SALES
The biggest challenge in marketing Belgian endive is, that for all the most sophisticated markets in the U.S., most consumers are unfamiliar with the product, or, if familiar, not in the habit of consuming it regularly. We sold the endive in three ways. The first was at a farmers’ market in State College, Pennsylvania. Sales there ranged from 10 to 15 pounds a market, at a price of $6/ pound. Attendance at that market in the winter months averages around 300 customers. Although we thought this price was too low, given the wholesale price (see below) and the price of salad mix and other bagged greens, we didn’t think the market would bear much more. We also sold directly to one retailer specializing in locally produced food in Harrisburg, Pennsylvania. This accounted for 5 to 10 pounds a week at $5/ pound.
Given the weak retail sales in most markets, even moderate producers of Belgian endive will want to consider wholesale options. We sold the bulk of our endive through a regional co-op, Tuscarora Organic Growers Co-op (TOG), which sells in the Washington D.C. market. TOG sold most of the endive for $6.40 a pound, of which we received $4.48. One large sale (for 150 pounds of endive) went through at a price of $5.80/ pound, of which we received $4.06. Due to this large bulk sale, TOG was able to move most of the endive we could ship (a total of 315 pounds over 8 weeks) although we did lose a few cases to shrinkage.
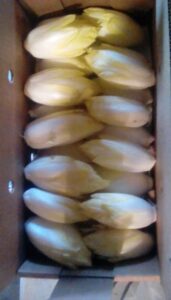
We learned several important lessons the new producer would do well to mind. If it is a new product for the distributor, as was the case with TOG, the marketing and sales staff may be unfamiliar with it and misunderstand it to be a form of green leafy endive, like frisee. It would have been wise for us to have sent the co-op a few boxes prior to the beginning of the main harvest, as they will need several weeks to plan adequately their marketing and sales efforts. While this hold true for any seasonal produce, it is especially important for a niche crop like Belgian endive. Finally, sales decrease dramatically, and become much harder, in March when other greens become plentiful. Growers should be advised that wholesale sales through a distributor will almost certainly require GAP certification.
One potential marketing venue we did not pursue was a CSA, our own or others, nor did we try selling directly to restaurants.
PROFITABILITY
One of the major goals of this study was to assess the possibility for a profitable winter crop for small to medium sized family farms. The difficulty with Belgian endive, as opposed to many other vegetable crops, is that the double process of growing the roots and then forcing the chicons gives larger producers two chances to take advantage of economies of scale and industrial processes not feasible on a small scale. This makes it doubly hard for the small scale producer to compete.
Obviously, profitability will vary greatly based on efficiency of operations, yield, sales, price obtained, and access to markets. Therefore, the following analysis is intended to serve as a departure point for the profit potential, not as a benchmark or, much less, an upper limit.
Assumptions: 350 pounds usable roots from one 200 foot bed. Actual yields in our trials ranged from 300 to 490 pounds per bed.
200 pounds of roots fill one tray. Actual numbers were consistently close to this.
We recorded total labor in 2016 at $534 before forcing—10 hours at $20, and 33 at $10 an hour. This would translate into $106.80 per bed, or $61.02 a tray. This includes the hours worked by the business proprietor.
80 pounds of marketable chicons per tray
All the chicons are sold at $4.50/ pound (the price we got from TOG)
Four hours to fill one tray at $12 an hour (I gave everyone a raise) or $48
1 ½ hours maintenance hours per tray or $18
Harvesting and packing the chicons at 30 pounds an hour, or 2.67 hours per tray, or $32
$.20/ pound packaging or $16/ tray
$.10/ pound for transportation to sales point or $8/ tray
$58/ tray for fertilizer, seed, drip line, fuel, other supplies. Seed was a good part of this- hybrid seed is expensive!
$20/ tray for heat in the forcing chamber
$10/ tray depreciation of forcing chamber and supplies
$20/ tray for mortgage payments, taxes, insurance on the land
Gross/ tray $360. After all the above is taken out, we’re left with $29 a tray, or $50.75/ bed, or $2,030 an acre.
This looks pretty paltry, but it should be remembered this assumes 80 pounds of chicons per tray. Our maximum yielding tray produced 110 pounds of marketable chicons. In such a case, profitability would go up to $177/ tray, or $309/ bed, $12,390/ acre
Or, at a price point of $5/ pound, 80 pounds of chicons/ tray nets $69/ tray, or $120/ bed, $4,830/ acre
And, at $5/ pound and 110 pounds of chicons/ tray would net $232/ tray, $406/ bed or $16,240/ acre.
Furthermore, this assumes only 350 pounds of roots per bed, and as stated above, root yields can be significantly higher. Also, although I am good to my friends and kind to children, I’m not the best at designing efficient processes. Labor hours could doubtless be reduced, and simple arithmetic will demonstrate that even a labor savings of ½ hour per tray translates into an extra $420/ acre. Also, each farm will have different numbers for taxes, mortgage payments, et cetera. We were heating the forcing chamber with electric space heaters, probably there are better options. Calibrating the seeder properly would save significantly on seed costs as well as labor to thin the crop.
DATA COLLECTED FOR ECONOMIC ANALYSIS
2017
Total hours spent harvesting in 2017 was 34 hours total compared to 32 hours in 2017, even though we harvested considerably more roots by weight in 2017. The total harvest of useable roots in 2016 was 1480 pounds, compared to 2253 in 2017, and the 2016 harvest included the open-pollinated variety that failed to produce chicons. The increase in yield at harvest (by weight) of roots from 2016 to 2017 can be explained in large part because we did not thin adequately in 2016, so many undersized roots were left in the field. In addition, delayed harvesting in 2017 may have resulted in many oversized roots which though heavier, do not result in larger chicons. Also remember the planting area in 2017 increased by 10%. See the Table “2017 Planting and Harvesting Records” for documentation of 2017 growing and harvesting activities.
2017 Planting and Harvesting Records
5 beds, 220 feet long, two rows per bed (2200 feet of row, 2.5 plants per foot, ~5500 plants)
Task date done hours Pounds of Useable Comments
Root Harvested
Field Preparation; 5 raised beds |
Mid-May |
2 |
|
|
Flame weeding before seeding |
Early June |
1 |
|
|
Seeding Totem & Atlas varieties* |
Early June |
1 |
|
3 beds Totem, 2 beds Atlas |
Cultivate for weeds between beds |
June |
.33 |
|
|
Total for prep prior to weeding |
|
4.33 |
|
@ 1 hour per 220’ bed, 2 rows per bed, = 0.27 hours per foot, @ 16 seconds per foot of bed with two rows of plants per bed |
Weeding of beds |
June 25-26 |
5 |
|
|
Weeding of beds |
7.17 to 7.26 |
13.5 |
|
|
Thinning seedlings |
7.27 to 8.2 |
13 |
|
|
Total weeding and thinning |
|
31.5 |
|
6.3 hours per 220’ bed, 37.8 minutes / 220 feet = @ .17 minutes per foot for a two row bed |
|
|
|
|
|
Harvest Totem in beds 4 & 5% |
10/28/17 |
16 |
718 |
Yield bed 5, 277.5# (15 CSA boxes @ 18.5#/box = 277.5#). Yield Bed 491# (19CSA boxes =351# + 4 1&1/9th wood boxes @ 35# per box= 140#) ; total weight 4 & 5 = 227.5 +351..5 + 140 = 718 pounds. |
Harvest bed 3 Totem and beds 1 & 2 Atlas |
11.22,11.7 & 11.4 respectively |
18 |
1535 |
Bed 1, 30 CSA boxes (555#), Bed 2, 25 CSA boxes (462#), Bed 4 28 CSA boxes? All three beds harvest Total 83 CSA boxes @ 18.5 # per box = 1535 lbs. |
Total planting & Harvesting |
|
34 |
2253 |
2253 pounds useable roots total (compared to 1480 pounds in 2016). Assuming 18.5# per CSA box |
*Totem seeds from Johnny’s, $314. Used left over Atlas seeds donated by grower in 2016. No open pollintated planted due to very poor results in 2016.
%Yield from top two beds lower due to damage from attempt to mow tops off roots.
Total time spent weeding and thinning in 2017 was reduced by nearly 20 percent from 38.7 hours to 31.5 hours despite sowing 1100 feet of 2-row beds 2017 vs. 1000 feet in 2016.
2017 saw the first effort to produce marketable Belgian Endive chicons from organic roots grown in 2016 in our project to assess the feasibility of selling them for winter income in the Northeast. We sowed, harvested, and stored a second crop of roots during the 2017 growing season and began the forcing process this December.
We have learned a whole lot about how to produce quality chicons and will be outlining the process, including what to do and what not to do, in our final report. This 2017 annual report will provide a general overview, reserving a more detailed description in the final report which will fully document our methods and results for distribution through NE SARE and through a booklet “How to Grow Organic Belgian endive in the Northeast” for wide distribution. We are presenting a workshop at the 2018 Pennsylvania Association for Sustainable Agriculture (PASA) on Feb. 9th ,at the Mid Atlantic Vegetable Growers Association Conference in January, and at an on-farm demonstration publicized through PASA in early 2019.
We succeeded in accomplishing nearly all of the tasks in 2017 needed to complete the project in early 2018 as detailed below. Because the production of chicons for sale in 2018 was begun in mid-December, 2017, we cannot report the results of the harvest to marketing that will take place beginning in early January, 2018
With all the controversy over the certification of hydroponic production as “organic,” it is essential to point out that even though we force some of the chicons hydroponically, the roots are grown organically and the nutrients producing the chicons come from the organically grown roots, not from fertilizers added to water.
The open pollinated roots, Cicoria Witloof de bruxelles variety, did not produce any useable chicons. The leaves were loose, not tight, and we found it impractical to apply top pressure to produce tighter chicons because trimming the roots to the same size was very time-consuming and difficult.
We produced a total of 427 pounds of potentially sellable chicons, but as the “2017 Chicon Sales Records” table below shows, we ultimately sold only 340 pounds, 80% of those produced. We delayed putting some into the cooler so we could weigh both the root and chicon to get a root to chicon ratio, and the delay probably accounts for why many of these chicons turned brown. It took our wholesale cooperative a while to learn how to market the chicons, and by the time they did, sales began to fall as early spring greens came in. Finally, we ran out of other products and stopped going to our indoor farmers market at the end of February, reducing sales there. We will be selling our first chicons in early January in 2018 compared to late February in 2017, so the percentage of chicons produced that are sold should increase. As the table shows, the 340 pounds of chicons sold returned $1,628 in income.
2017 Chicon Sales Records
This table documents chicons actually sold. Not all chicons harvested were sold, some because there were problems one week with the leaves turning brown, some due to our wholesaler (Tusarora Organic Growers) learning how to best to market them, some unsold in March as wholesale demand dropped with the arrival of early spring greens, and some because we stopped going to the indoor market.
Date Sold to TOG Amount Delivered Price per pound $Total Sales TOG price to customers
2/27-2/28 |
15pounds, 3 five pound cases |
4.48 |
67.20 |
$32 pound box, $6.40 per pound |
3/1-3/ 5 |
30 pounds, 6 five pounds cases |
4.48 |
134.40 |
$6.40 per pound |
3/13-3/19 |
20 pounds, 4 five pound cases |
4.48 |
89.60 |
$6.40 per pound |
3/27-4/2 |
145pounds, 29 five pounds cases |
4.058 |
726.38 |
$5.80 per pound (bulk sale) |
4/3-4/9 |
55 pounds, 11 five pound cases |
4.48 |
246.40 |
$6.40 per pound |
4/10-4/16 |
35 pounds, 7 five pound cases |
4.48 |
156.80 |
$6.40 per pound |
4/17-4/23 |
5 pounds, 1 five pound case |
4.48 |
22.40 |
$6.40 per pound |
4/24-4/30 |
10 pounds, 2 five pound cases |
4.48 |
44.80 |
$6.40 per pound |
Feb. Farmers Market |
15 pounds |
6.00 |
90.00 |
$6 per pound to market customers |
Feb. Radish & Rye retail vegetables |
10 pounds |
5.00 |
50.00 |
|
Totals |
340 pounds |
|
1,628 |
|
2016
We described above the generally good success we had in producing a good harvest of roots suitable for forcing. Growing a good number of roots organically in the North East is feasible.
We have an inkling of what some of the most important lessons we have learned that will be part of our final report. 1. The basic practices we used to produce suitable roots for forcing work pretty well. 2. Seeders need to be set to avoid sowing too thickly to cut. We will be looking into a different cartridge for next year’s crop. 3. Just as many useable roots can be grown with two rows rather than three rows in each 30 inch bed. 4. Plants need to be thinned to four to six inches consistently, something we did not always do. 5. Our estimates of how long very thorough weeding and thinning were spot on, but harvesting took almost four times as long as we estimated (30 hours, not 8). Harvesting time can be reduced in the future by sowing more thinly, by thinning to 4 to 6 inches, and by seeing if we can mow the tops mechanically before harvesting.
These lessons will help us calculate the financial return for the effort required, providing other growers with information they can use to decide whether to undertake producing Belgian Endive for winter income.
For Jade Family Farm, the biggest benefit in growing Belgian endive was providing income generating work in the months of January and February for those employees who wanted it, thus aiding in employee retention. Weather conditions do not often permit outdoor work in these months, and production in high tunnels is limited. The process itself is straightforward and not overly difficult, although, like all crops, there are certainly challenges and it requires a certain amount of attention. It is an especially good choice for the organic grower, as invertebrate pest and disease pressure seem to be modest at worst. While it was very rewarding introducing this gourmet product to many new palates, the challenges of sales and marketing are formidable. We look forward to growing Belgian endive in the future and anticipate the profitability to improve as we refine our techniques and improve our efficiencies.
LESSONS LEARNED
Our experience in 2017 confirmed the findings of the 2016 growing season that producing organic Belgian Endive in the North East is feasible.
Some of the most important lessons we learned in 2016:
1. The basic practices we used to produce suitable roots for forcing work pretty well.
2. Seeders need to be set to avoid sowing too thickly, requiring time consuming hand thinning.
3. Just as many useable roots can be grown with two rows rather than three rows in each 30 inch bed.
4. Plants need to be thinned to four to six inches consistently, something we did not always do. Given that larger roots do not produce larger chicons, 4 inch spacing seems ideal, as this limits the size of the roots somewhat, while still giving the plants enough space to produce a useable root.
5. Our estimates of how long very thorough weeding and thinning would take were spot on, but harvesting took almost four times as long as we estimated (30 hours, not 8). Short of investing in a major upgrade of harvesting equipment (this year, we cut off the tops with pruning shears first, used an undercutting bar attached to the tractor’s 3 point hitch to loosen the topless roots from the soil, then pulled the roots by hand, shook the soil off, and placed them in boxes for cold storage), the only easy way to reduce harvesting time would be to mow the tops off mechanically. But as it only took 30 to 40 minutes, depending on who was doing it, to cut the tops off with the pruning shears, it is doubtful whether this innovation alone would have much of an impact.
Add several additional lessons learned in 2017:
1. Adjusting the seeding rate can reduce the time spent in thinning.
2. Seeding should be done several weeks later in mid- to late-June to anticipate the heavy time demands fall harvesting takes. By the time we were able to harvest, the roots were larger than ideal. In addition, it appears that leaving the roots in the ground past maturity can cause the roots to narrow and elongate at the top (likely in preparation for flowering), which results in a significantly smaller chicons. Farms which don’t have as much to do in early October won’t have this problem, as they would be able to harvest promptly
3. Our open-pollinated variety, “de Bruxelles”, did not perform well during forcing in 2016. We did not plant it in 2017 and don’t recommend using it in an indoor forcing system such as ours.
4. Larger roots do not produce bigger or better chicons. It appears the ideal girth of the roots (at the top) is about 1 ¼ inches with a weight of .4 to .5 pounds. Larger roots- some up to 1 pound-, unless displaying the morphological changes described above, produced chicons about the same size and weight as those roots weighing .4 to .5 pounds. A graph displaying the relationship between root weight and chicon weight will be included in the final report. Planting later will reduce the number of the unsuitably large roots harvested, as will a more precise spacing at 4 inches.
5. Adding approved organic fertilizer to hydroponic production does not improve yield. The energy stored in appropriately sized roots is sufficient. 6. Planting in raised beds and using a digging bar is essential for any size commercial planting. Endive roots are very difficult to dig by hand. Using pruning shears to remove tops from roots before digging saves time, as compared to removing the tops after the roots are out of the ground (although it is harder on the back!).
7. It is worth trying to devise ways to cut plant tops from roots mechanically by taking care to keep beds and spaces between beds level.
8. Potential growers need to invest in a properly functioning forcing room. Hydroponic production is less time consuming and avoids the problems associated with keeping soil forced roots properly moist. However, it requires a somewhat larger initial investment. New growers may want to start small, using soil based methods if so desired.
9. Harvested chicons should be put in a cooler without delay.
Education & Outreach Activities and Participation Summary
Participation Summary:
We demonstrated our progress in the summer of 2016 to our technical advisor, Elsa Sanchez, and Northeast SARE Farmer grant program coordinator, Carol Delaney.
Learning Outcomes
We have learned the basics of growing and forcing organic Belgian Endive as well as a little about how to sell them at Farmers' Markets and by wholesale. We would like to try offering them in our CSA and direct sale to restaurants may be a good avenue for some chicons.
Project Outcomes
We grew more endive in 2018 and plan to continue doing so. Once we properly share our results through more workshops and presentations, we expect other organic farmers to take a look at this winter crop.