Final report for FNE17-865
Project Information
We looked for ways small warm season grass growers could efficiently and easily process their grass for small poultry operations. We tried to use equipment readily available to farmers looking to meet material specifications listed in poultry bedding research. Special attention was given to dust and over-sized particles. We focused on harvesting, size reduction, dust removal, and packaging for transport.
Harvesting warm season grass is very much like harvesting hay. You can harvest in the fall after two killing frosts or in the early spring. In the spring the grass will have a 6% - 8% moisture content. Grass that is harvested in the spring can be matted by winter snow. A New Idea Cutter Conditioner works well to lift and cut the grass for bailing. Bales can be round or square.
All the processes we explored have possibilities to produce acceptable bedding material. Some would need additional modification. The only “in-the-field” processor we found was the New Idea Uni-processor demonstrated by Dr. Marvin Hall on a Penn State test field. It cut, chopped, and collected the grass in a single pass, leaving very little dust in the finished product. The unit we saw left too many long pieces. Thus not meeting the goal of pieces <1.5″. The material would function okay for a backyard operation. If we could add additional knives or insert a smaller screen this processor would be a fine choice.
The hammermill with a 3/4″ screen processed the material to the desired length. When combined with a cyclone separator and deposited into a 4’x4’x4′ super sack the material was within the desired specifications. This process is the most available combination of equipment. All four participating farmers had this equipment already.
The 4’x4’x4′ super sacks were by far the easiest containers to fill. If the “bang-the-bag” technique was used, any remaining dust from the cyclone dropped to the bottom of the bag. In addition, the material in the bag was compacted by the action. The sack weighed about 200 pounds when filled. The 16″x12″x35″ 30 gallon paper bags were the most desirable containers. They weighed around 30 pounds when filled and were easy to stack on pallets and transport. The biggest drawback was in locating an economical bag source.
We shared our experience and learned outcomes online, in Association emails, in press releases, at Association gatherings, at Ag Progress Days and the York Farm Show. We reached a large number of farmers.
If warm season grass could be chopped at the time of harvest, dust and crop litter would remain on the field rather than accumulating at a central processing location, circumventing some of the safety hazards otherwise presented. But even after processing, moving low-density chopped bedding material to an end user is difficult for the farmer to do in a logistically and economically efficient way. Strategies are needed to improve both processing and transportation logistics. Specialized baling machinery is currently being developed and tested to accomplish in-field chopping and densification of warm season grasses, but these high-tech solutions may be too expensive for smaller-scale warm season grass producers. Lower-tech, lower-cost approaches are needed for those producers to gain footholds in a promising market.
The objectives of this project were to identify, test, and evaluate strategies for processing perennial grass bedding utilizing existing equipment and accessible, affordable approaches for a small-scale farmer. We hoped to identify solutions that not only prioritize in-field chopping for the reasons outlined above, but which also eliminate the need for baling or otherwise streamline the processing logistics by reducing the equipment, time, and labor costs associated with the processing requirements for this market.
Poultry bedding is a new market opportunity for growers of perennial warm season grasses, and some research has been done and is underway that explores this opportunity. Several studies have examined the performance of warm season grass as bedding, as an alternative to traditional pine shavings. For example, in the study “On-farm assessment of switchgrass bedding’ J. R. Moyle, L. A. Brooks, B. A. McCrea and W. R. Brown studied the feasibility of using switchgrass as an alternative bedding material in commercial production houses over consecutive flocks. The use of warm season grass as bedding may have benefits over traditional sawdust bedding. J.D. Davis , J.L. Purswell , E.P. Columbus and A.S. Kiess, in their study “Evaluation of Chopped Switchgrass as a Litter Material” found that body weight, body weight gain, feed consumption, feed conversion, carcass weights and mortality were not different between switchgrass bedded poultry and traditional pine shaving-bedded poultry. However, the incidence of foot pad dermatitis was significantly decreased with switchgrass litter. In the 2016 SARE Graduate Student Grant GNE16-127 entitled “Renewable alternative bedding for commercial broiler chicken production”, Amy Meyer of Penn State compared willow and switchgrass bedding in a poultry house, with bedding processing being undertaken at the poultry farm and not in the field. Preliminary results demonstrated that chopped perennial grasses perform very well as bedding for poultry. Similarly, the University of Delaware Extension and the University of Maryland Extension, in collaboration with the Conservancy and Chester River Association (CRA), and Perdue poultry, conducted several field trials to study the viability of switchgrass as an alternative bedding material. These tests involved delivering baled, unchopped material to poultry farms, where it was ground at the point of use, resulting in significant dust generation and additional complexity to the already busy schedule of the poultry farmers.
The application, then, is well-supported, but the logistic needs of processing and delivering perennial grass bedding are less straightforward. Commercial success of perennial grasses for bedding likely depends on the cost effective collection and delivery of pre-chopped material in a format that is easy for the poultry farmer to use, both for large poultry operations that seek to minimize labor costs and for smaller farmers who would not be able to justify the cost of large-scale chopping equipment or the associated labor and hassle. Chopping grasses is not a new phenomenon, and there is a variety of implements and devices available on the market to carry out this task.
However, chopped grasses are almost exclusively used on-site, and are generally designed for forage/animal feed systems. The unique needs for processing bedding production (typically a drier and smaller sized product) have yet to be studied, and guidance on this process would be invaluable for farmers looking to produce switchgrass bedding for poultry bedding. This need has not gone unnoticed; a recent Value Added Producer Grant awarded to Ernst Seed explores large-scale in field preparation of perennial grasses for poultry bedding utilizing high-end equipment to chop and bale warm season grass for shipment. This is a valuable study and has merit for farms with large acreage able to support the use of large equipment, but these approaches are not accessible or cost-effective for a growing number of producers that operate at smaller scales, with small plots, or on marginal lands. Thus, an opportunity and need exists to identify, test, and compare lower cost, smaller scale, and locally appropriate methods for producing this sustainable bedding material. This information would be a valuable tool for the development of switchgrass production in the region, leading to economic and environmental benefits for the region in the form of increased income to farmers and the positive impacts on water quality, soil quality and wildlife habitat that are associated with native perennial warm season grasses.
Cooperators
- - Technical Advisor (Educator)
Research
Harvesting (video)
Examining the fields of warm season grass in March I found the winter matted the crop more than usual.

Because of the matting, standard mowing equipment would not cut the grass. We used a New Deal flail cutter. The knives of the machine lift the grass off the ground and cut it into 6”-12” pieces.
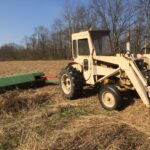
Mowing occurred from April 14 till April 16. There was rain April 17 delaying the raking process. There was rain almost every other day up through May 3. As a result raking was required numerous times to dry the material for baling.
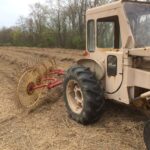
We used a three wheel "wheel rake" to rake the grass into windrows. Initially, two mowing rows were combined into a single windrow. When raking to dry the rained on grass, we waited until mid-afternoon. That allowed the material to dry on top. Raking tuned the material so it would dry on the bottom.
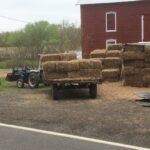
We intended to use round balers to collect the material from the field. Because of the rain and excess raking the material became brittle. It would break and not form into round balers. We used a New Holland small square baler to collect the grass. This meant an increase in manual labor. The small bales were loaded and unloaded by hand. Because of the brittle nature of the grass, more was left on the ground in the field. We were however, able to collect enough to for processing. Additional material was provided by the participating farmers.
Processing to the Proper Dimensions
We used six different methods in our attempt to process the grass to acceptable specifications.
- We used a tub grinder at the Hartpence Farm to chop material. The grinder was fitted with a 2" screen.
- Some of this material was further processed by running it through a trommel mill in an attempt to remove dust. .
- A hammer mill with a 3/4' screen at the Reggie Farm was tested.
- Some of the Reggie material was further processed with a shaker table for dust removal.
- A New Idea Uni-Processor cut and chopped the material in the field.
- At the McDonnell farm we used a feed truck.
Tub Grinding (Hartpence Farm) (video)
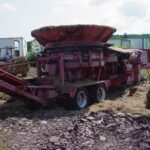
We hauled small square bales from Wood Crest Farm to the Hartpence where the tub grinder was located. Using a front end loader bucket bales were fed into the tub grinder. We were able to feed 6 bales at a time. The tub grinder was equipped with a ¾” screen. The grass was ground until it was small enough to pass through the ¾” openings. From the grinder, a conveyer moved the grass to a forage wagons. The forage wagons were off loaded into super sacks and the floor of the build housing the paper baler. Samples of the material were sent to Penn State University for particle analysis.
Hammer Mill (Reggie Farm) (video)
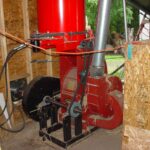

Len Reggie provided material to run this procedure. Small square bales were sent by conveyor into a small bale buster. From the bale buster they entered a hammer mill. The mill was equipped with a ¾” screen. Hammers pounded the grass until it was small enough to pass through the screen. The hammer mill used a fan to push the material to a cyclone separator. The cyclone separator moved the air and dust outside and dropped the hammered grass into a super sack. Samples of the material were sent to Penn State University for particle analysis.
New Idea Uni-Processor ((video)
Dr. Marvin Hall, a professor at Penn State University refurbished a New Idea Uni- Processor. He agreed to demonstrate the unit in a PSU switchgrass field. Larry Hartpence and I traveled to Penn Furnace to meet Marvin. The unit is diesel powered. It cuts and processes the material into a metal bin attached to the end of the machine. The material is fed into an on board chopping chamber. Here the material is cut into smaller pieces. As it cuts and processes, all the dust and residue is left in the field. It is a very efficient method to process poultry bedding. The only negative factor was the size of the material coming from the processing. It was too large for a commercial poultry house. It would be fine for a back yard operation.
Feed Truck (McDonnell Farm) (video)
Frank McDonnell provided material to run this procedure.
The machine was designed to process grain. It is totally self-contained and portable. It will process other materials. It handled grass very well. Frank hand fed material onto the conveyor. He was careful not to load the conveyor with
too much material. It was easy to clog the opening to the machines grinder. The unit has 8 different size screens. Frank loaded a ¼” screen. Augers and air moved the grass through the machine to the discharge port. From the grinder, the grass went into a self-unloading wagon. From the wagon, a conveyor moved the grass to a suspended funnel above a super sack. The filled sack was stored indoors.
Dust Removal
Trommel Mill (Tub ground material - Brandau)
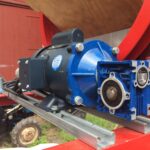
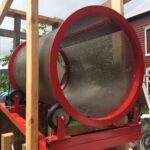
Material from the tub grinder was run through a trommel mill to remove fines and dust particles. A trommel mill is a rotating cylinder with holes allowing removal of the small material. The large material passes though the inside of the cylinder and then drops out the end free of dust and fines. The cylinder is mounted on a slight incline. Material is introduced at upper end and moves gradually to the lower end where it discharges from the device. As the cylinder turns and the material moves, the dust drops out the bottom. Material leaves the tube relatively free of dust. Trommel mills are normally very large. Too large to be practical for a small poultry bedding producing farmer. Below is the bill of materials, material source, and the engineer drawing. Total cost for materials was less than $550.
trommel-screen-processor Trommel-screen-parts-list-and-assembly trommel engineer drawing
Hammer Mill with cyclone separator
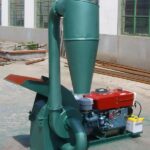
A hammer mill is a very efficient machine to reduce the size of material. It works using high speed rotation of metal bars, the hammers. These bars contact the material and break it into smaller pieces. The material "escapes" the hammering process when it becomes small enough to fit through holes in a metal plate called the screen. The holes in the screen can be any size the operator desires. We found holes measuring 3/4" were perfect to produce the desired size of material <1.5". Warm season grass is quite brittle. As a result, when hammered a tremendous amount of dust is produced. When the hammered material passes through the screen a high speed blower embedded in the mechanics of the hammer mill push it out of the mill, dust and all. If the mill has a cyclone separator attached, the material is blown into the cyclone. There the cyclone separates the material from the air. As shown in the diagram, the material enters the side of the cyclone. The heavy material drops out the bottom and the dust and air go out the top.
Bang the bag - vibration table
The easiest way we found to handle dust in a small super sack was to "bang the bag". Two or more people grab the corners of the bag, pick it up, and drop it. This is repeated a number of times. Any dust in the material drops through the bag and is concentrated at the bottom of the bag. A similar technique utilizes a vibration table. The bag is placed on the table for filling. The table vibrates while the material enters the bag. Again, the dust is concentrated at the bottom of the bag.
Shaker Table (video)
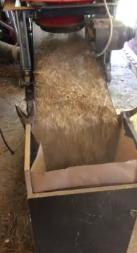
A shaker table is a flat piece of metal with lots of holes. The size of the holes determines the size of the material that can fit through the hole. A motor and pulley assembly cause the metal piece to shake rapidly. The metal is mounted on an incline. As the table shakes, the material moves down to the bottom and drops off. The small particles and dust drop through the holes and are separated from the usable material. The resulting material is almost entirely free of dust. The shaker table at the Reggie Farm is situated so as the material drops off the table it drops into a paper sack, described below.
Transport Preparation
Horizontal Baler (video)
A horizontal baler is a machine that compresses material with hydraulic pressure. The compressed material is then "pushed" from the baler chamber into a heavy plastic bag. The bags can be stacked on a pallet and shrink wrapped for transport. We were very
excited by this packaging process. We were able to insert a label inside the bag describing the material. Since the bag was clear plastic you could clearly see the enclosed material. Our enthusiasm quickly ended when we went to retrieve the plastic packages. The bags
were stored inside a dry shipping container on pallets. The bags were sealed with shipping tape. We found considerable moisture inside the bag. It was clearly visible through the clear plastic. We had tested the bales for moisture when we harvested. Moisture level measured 6% - 8%. The bales were stored inside. They must have taken on moisture from the humidity in the air while in storage. Then, when processed and packaged in a sealed container the moisture became very visible.
Paper Baler (Hartpence Farm) (video)
This machine is normally used to package shredded paper for shipment to a recycling facility. The grass material for this process came from Wood Crest Farm. We ran it through the tub grinder into a forage wagon and unloaded it to the floor of the building housing the paper baler. Using a front end loader, the shredded grass was loaded into the hopper of the machine. The machine compressed the grass. 6 wire ties held the bale together. The finished bale weighed 1514
pounds. Even though the grass was shredded to less than 2" in length, very little came off the bale. The fork lift moved the bale to a storage building. Bale integrity was fine. There would be no problem moving a covered bale to a poultry farm location.
Super Sacks
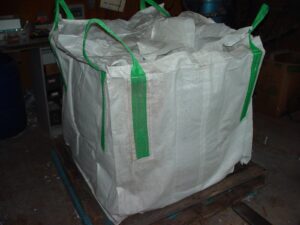
At the Reggie farm where we ran the hammer mill tests, the bales all weighed slightly less than 30 pounds. Through a process of trial and error, we learned a super sack could hold 7 hammered bales. Thus, a super sack filled with hammered grass weighed about 200 pounds. The material moisture tested at only 6.2%. Moisture was not a major factor in the weight of the bag. The first, single operator, 7 bale run took 13 minutes 35 seconds to complete. We completed an additional 6 runs. A single operator was able to process 1500 pounds of material in about 1 hour. We were not able to find a process to increase the density of the material in the super sack.
A smaller hammer mill screen will result in smaller grass particles. Smaller particles allow more material in the sack and increase the weight. A sack filled with material run through a 1/4" screen weighs in at around 500 pounds. However, the amount of dust increases dramatically.
Paper Sacks
Brown paper sacks are an excellent container for processed poultry bedding. These bags are often referred to as leaf and garden bags. With

minimal compression they will hold 30 pounds of grass. They are light enough to carry and easy to handle. We were not able to find a generic version and so resorted to bags with a "Lowes" label for our research. These became the preferred container for delivery. Even large use events chose these bags over super sacks. The bags can be stacked on a pallet and shrink wrapped for easy delivery.
Field observations and some results regarding logistic and efficiency details of processing ad bagging methods are detailed above in "methods."
Observations
Warm season grass that is matted down from the winter weather can be cut efficiently with a New Deal flail cutter. When warm season grass is rained on and dried repeatedly it becomes very brittle and difficult to bale.
The screen in the grain mill at the McDonnell Farm was too small. The inline cyclone separator was inefficient. This resulted in excessive dust in the bedding. The 4H group using the bedding complained about the dust.
A super sack of small particles will weigh more than a sack of larger particles.
Particle Analysis
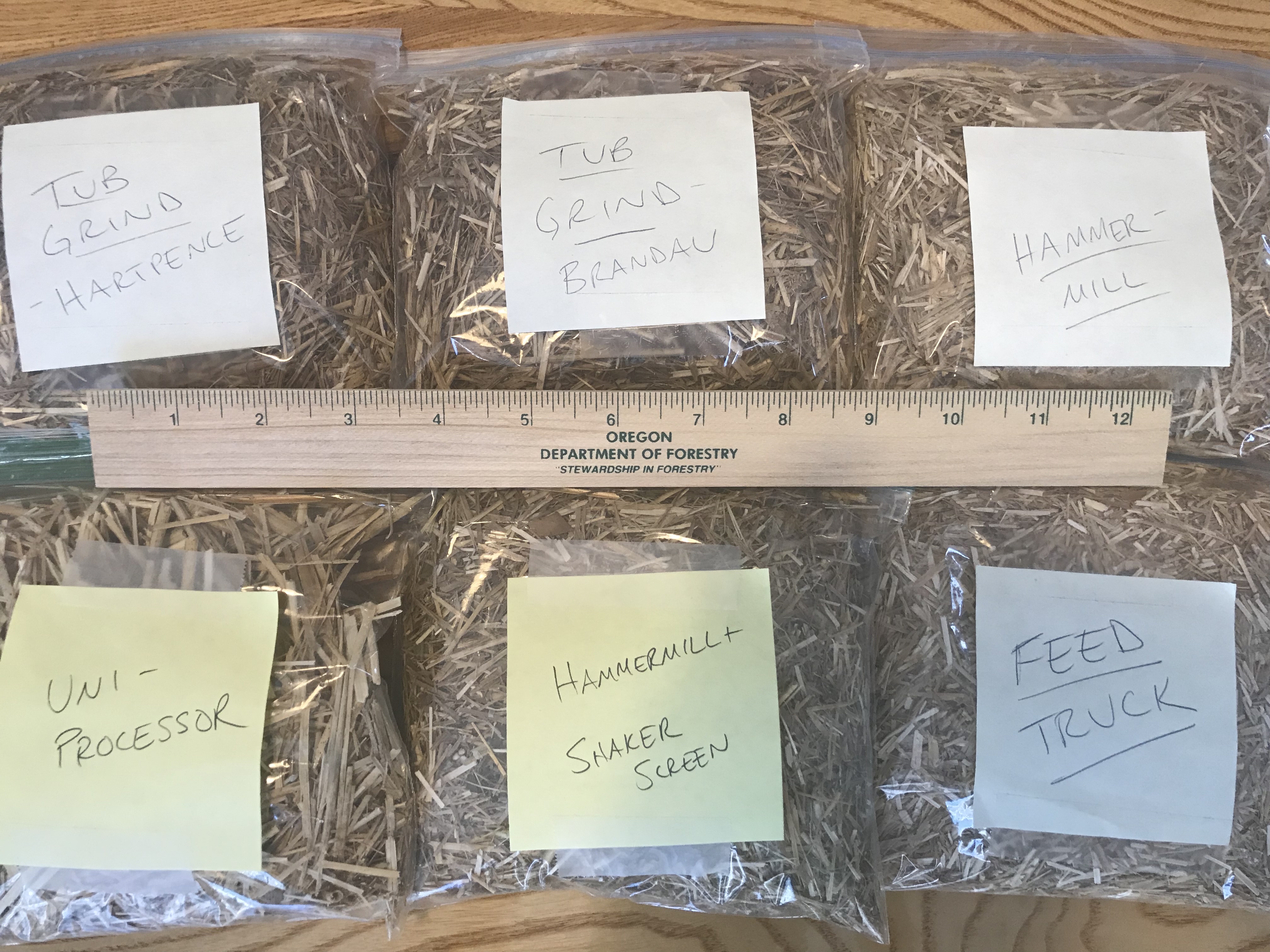
Poultry bedding suitability varies depending on the scale and system in which it is applied, but in general, material is preferred if it measures under roughly 1.5" without being too dusty (too many fine particles). Particle size analysis on poultry bedding samples involves a standard testing protocol (ASAE standard S319.3, often used for feed particle size analysis) involving timed shaking of a stack of 13 sieve screens and a bottom pan. A machine shakes the stack for 10 minutes at 120 swings per minute. Though our objective was to have particles <1.5" in length with minimal dust and minimal particles large than our target size maximum, we used this particle size analysis protocol involving a maximum sieve size of 0.5" so that our results would align with the standard used in other studies.
Particle size analysis was undertaken by the project's technical advisor, Sarah Wurzbacher, with laboratory access, supplies, and cooperation from Dr. Paul Patterson, Dr. Hojae Yi, and Dr. Virendra Puri of Penn State University. We ran three samples each of the six total processing treatment and expressed data in terms of each size fraction's percent of total sample mass. The following figures show the average distribution of particles (shown as percent of total sample by mass) for six treatments, including standard error.
Table 1 shows summary data:
Figure 1 below shows the graphical distribution of particles (percent by mass) by screen size. The screens don’t step down in size in regular intervals, but we’ve shown the distribution with an interval of “1” between each screen; the labels on the bottom axis are titles only. Therefore, this is not a true distribution, but it is much easier to visualize than the numeric screen size axis (see scatter graph in Fig. 2). This gives a general idea of how much material went through each screen, and how it was distributed in the screen column. Standard error bars are included to show variability.
The scatter graph, Figure 2, below shows the same data as Figure 1, but instead of showing the distribution by screen (with each screen’s contents regularly distributed across the X axis regardless of screen size), it shows the distribution based on the actual minimum size of the material caught in the screen. Screen size does not step uniformly down in size at regular intervals (the first two screens were 12.7mm and 6.35mm, then the next one is 4.75mm...); this figure shows a more accurate graphical depiction of distribution by size. Standard error bars are included.
Figure 3 below shows what percentage of the sample by mass did not pass through the first screen, sized at 0.5 inches. These particles are “overs” – meaning they are larger than 0.5 inches. Again, some of these particles may be acceptable in poultry bedding as long as they are not too large or irregular; these data show only what’s larger than 0.5 inches.
Figure 4 below shows the percentage of sample particles smaller than 1mm (0.039 inches), providing an estimate of how dusty the samples were.
On the subject of oversize particles: recommendations are not strictly to achieve a target distribution between 1-1.5 inches, but rather to ensure that the bulk of the large particles after screening do not exceed this size, and that oversize particles do not poke out or mat together in "caking" behavior. It was observed during shaking analysis that even small particles relegated to the top shaker screen >0.5 inches had a tendency to form fluffy mats and therefore resulted in conditions likely to overestimate the fraction of oversize particles, but this result does not necessarily exclude them from acceptability for poultry producers. Qualitative and experience-informed, real-world observations are therefore necessary to evaluate acceptability of material. To assist, poultry professionals were consulted, sharing our results and material samples.
It is interesting to note that two processing treatments using tub grinders yielded distributions that were different from one another (not just in smaller fine particle fractions, as hypothesized by additional processing with the trommel mill for one of the tub ground treatments), highlighting the variability and inconsistency that can characterize tub grinding processing approaches. The feed truck treatment provided what was by far the dustiest material. Poultry producers who used this material commented negatively about the amount of dust. The uni-processor, of all treatments, had the least material in smaller size classifications, lending support to our suspicion that a processing step done in the field would leave dust and fine material on-site and yield a less dusty delivered product; however, it also had the most material over 0.5 inches (refer to Fig. 3), but we believe that with knife adjustment or a screen addition to that process, the proportion of oversize pieces would be lessened, perhaps enough to reach a favorable bedding specification. It was noted that due to the lack of dust, the uni-processor approach might be a good choice to process product for small-scale or backyard operations, so long as the larger particles were not wirey and made the product difficult to work with. It was also favorably noted that the uni-processor and hammermill+shakescreen treatments both showed a high percentage of material measuring between 0.125-0.5 inches. The hammermill+shakescreen treatment also had less material below the 1mm size class than prior treatments (so it too was less dusty), but but it also had more than acceptable material >0.5 inches. Because these results are expressed in terms of percentage of total sample, higher proportion of oversize pieces between the hammermill and hammermill+shakescreen treatments may derive from the lack of smaller/dusty material due to the screening process; in practice, if the hammer mill material is acceptable in terms of large particles, the hammermill+shakescreen material should be similarly acceptable, and slightly less dusty. Repeated analysis with equal masses between compared treatments could verify.
Overall: Poultry researchers consulting on this project who looked at these results and samples of material from each treatment indicated they would likely accept all of the material except for samples from the feed truck and uni-processor treatments. There were too many small particles in the feed truck material and too many large particles in the uni-processor material. However, those approaches may still be valid with slight amendments to the process, or a differentiation between end-users. All processing methods were considered "promising" approaches for producers at this scale.
Objective
Warm season grass will grow 6' to 8' tall. Poultry farmers want bedding less than 1.5" in length. Poultry farmers want a bedding with a low moisture content. Warm season grass comes out of the field at 6% - 8% moisture content. Poultry Farmers want a bedding with minimal dust content. Because of the low moisture content, warm season grass is very brittle and can produce a large amount of dust. Transportation of warm season grass can be expensive. Processing for poultry bedding can increase bulk and add to the transportation costs. This project addressed all these issues.
Summary of Treatments/Processing Approaches
Aspects of each processing treatment are summarized below, with certain attributes being rated low, medium, or high in favorability based on the opinions and experiences of farmers working on this project.
Treatment: Feed Truck
- Bedding acceptability based on processing specification: Maybe, with tweaks to process including a 3/4" screen.
- Cost rating: Low - The unit is a diesel powered efficient unit.
- Labor/efficiency/handling rating: Medium - Material is had feed into the unit.
- Pros: Inexpensive to run
- Cons: Parts not available, dusty material
- Changes or future work recommended: Replace the 1/4" screen with a 3/4" screen
- Overall: Not Recommended with the setup used. With adjustments listed above it would work.
Treatment: Hammer Mill
- Bedding acceptability based on processing specification: Yes
- Cost rating: Low Hammer mills are readily available to farmers. The cost of a used working unit is minimal.
- Labor/efficiency rating: Medium When you hand feed a hammer mill labor is higher. Auto feed is not. We did both.
- Pros: Inexpensive, readily available, output adjusted by the screen in the machine
- Cons: manual feed can be labor intensive.
- Changes or future work recommended: Construct an automated portable system that includes a hammer mill in the process.
- Overall: Recommended
Treatment: Tub Grinder
- Bedding acceptability based on processing specification: Yes, but can yield variable results
- Cost rating: High The tub grinder we used was massive and consumed large amounts of fuel.
- Labor/efficiency rating: Low Front end loaders feed the machine. Large volume processing with a single operator
- Pros: large volume rapid processing, single operator
- Cons: not commonly available, expensive
- Changes or future work recommended:
- Overall: Recommended where available
Treatment: Cyclone Separator
- Bedding acceptability based on processing specification: Yes
- Cost rating: Low Hammer mills are easily found and normally not expensive.
- Labor/efficiency rating: Low The unit is attached to the hammer mill requiring no additional labor.
- Pros: No additional labor required. readily available Does a good job removing dust.
- Cons: None
- Changes or future work recommended: Construct an automated portable system that includes a cyclone separator in the process.
- Overall: Recommended
Treatment: Trommel Mill
- Bedding acceptability based on processing specification: Yes
- Cost rating: Low The unit is inexpensive to build.
- Labor/efficiency rating: Low Minimal labor required as the unit is part of the material flow.
- Pros: Less air born dust, minimal labor, inexpensive to build
- Cons: small scale units not common. Must be custom built
- Changes or future work recommended: Construct an automated portable system that includes a trommel mill in the process.
- Overall: Recommended
Treatment: Uni Processor
- Bedding acceptability based on processing specification: Maybe, with tweaks to process (more knives, additional screening).
- Cost rating: Low Single pass operation.
- Labor/efficiency rating: Low Single operator driving machine.
- Pros: Dust expelled in the field rather than during packaging or end use/delivery. Very low dust is attractive for small-scale applications. There is a FaceBook user group and parts are available.
- Cons: The New Idea Uni-Processor is no longer manufactured. Will not process matted grass.
- Changes or future work recommended: A member of the Association of Warm Season Grass Producers is getting a used unit to refurbish.
- Overall: Recommended with tweeks
Treatment: Shaker Screen
- Bedding acceptability based on processing specification: Yes
- Cost rating: Medium Small unit availability unknown. Can be custom manufactured at minimal cost.
- Labor/efficiency rating: Low Unit is positioned in line with the process and requires no additional labor.
- Pros: No additional labor, Minimal air born dust, very good dust removal
- Cons: availability
- Changes or future work recommended: publish bill of materials and assembly plans
- Overall: Recommended
Bottom Line: Recommended Techniques
Harvesting warm season grass is very much like harvesting hay. You can harvest in the fall after two killing frosts or in the early spring. In the spring the grass will have a 6% - 8% moisture content. Grass that is harvested in the spring can be matted by winter snow. A New Idea Cutter Conditioner works well to lift and cut the grass for bailing. Bales can be round or square.
All the processes we explored have possibilities to produce acceptable bedding material. Some would need additional modification. The only "in-the-field" processor we found was the New Idea Uni-processor demonstrated by Dr. Marvin Hall on a Penn State test field. It cut, chopped, and collected the grass in a single pass, leaving very little dust in the finished product. The unit we saw left too many long pieces. Thus not meeting the goal of pieces <1.5". The material would function okay for a backyard operation. If we could add additional knives or insert a smaller screen this processor would be our first choice.
The hammermill with a 3/4" screen processed the material to the desired length. When combined with a cyclone separator and deposited into a 4'x4'x4' super sack the material was within the desired specifications. This process is the most available combination of equipment. All four participating farmers had this equipment already.
The 4'x4'x4' super sacks were by far the easiest containers to fill. If the "bang-the-bag" technique was used, any remaining dust from the cyclone dropped to the bottom of the bag. In addition, the material in the bag was compacted by the action. The sack weighed about 200 pounds when filled. The 16"x12"x35" 30 gallon paper bags were the most desirable containers. They weighed around 30 pounds when filled and were easy to stack on pallets and transport. The biggest drawback was in locating an economical bag source.
Education & Outreach Activities and Participation Summary
Participation Summary:
On going; www.awsgp.org is the web address of The Association of Warm Season Grass Producers (AWSGP). Information about the SARE project is presented there. Details about the project are included in emails sent to Association participants.
April 12, 2017 International Biomass Conference; Minneapolis, Minnesota I did a presentation at this event. The presentation included a portion on the SARE project. There were about 65 in the audience.
June 24, 2017 Wood Crest Farm, Wapwallopen, PA AWSGP Annual Meeting; I did a presentation discussing the state of the Farmer Grant, explaining the challenges and successes to date. I listed the additional tasks required to complete the process. There were 20 in attendance. June-24-Membership-Meeting
.August 15, 16, and 17, 2017 Ag Progress Days, Pennsylvania Furnace, PA; Members of The Association of Warm Season Grass Producers (AWSGP) participating in the SARE Project spoke with attendees describing warm season grass poultry bedding. They reported talking to over 150 attendees.
September 12, 2017 Wood Crest Farm, Wapwallopen, PA; I hosted a MABEX tour group at the farm. I spoke about the many uses of warm season grass including a description of the SARE Project and our progress to date. There were 14 on the tour.
September 13, 2017 MABEX Conference, State College PA; I did a presentation describing The Association of Warm Season Grass Producers (AWSGP). As part of that presentation, I discussed the SARE Project and the advantages of warm season grass poultry bedding. There were about 70 in the audience.
June 16, 2018 AWSGP Annual Meeting I did a presentation to the group describing the Farmer Grant results. About 25 in attendance.
August 14, 15, 16, 2018 Ag Progress Days; I manned a booth at the event. I had other members from AWSGP in attendance. We handed out the SARE flyers, showed samples of the processed bedding, and gave away sacks of poultry bedding. We talked to over 250 people. August 15, I presented my final report to an open audience of APD attendees. There was a small audience of only about 15. The following morning I did an abbreviated presentation at a conservation group breakfast with 150 in attendance.
Learning Outcomes
I made contact with the folks who manage the poultry barn at the Bloomsburg Fair. They agreed to replace traditional wood chips with our warm season grass bedding. They had over 900 bird cages. Barn management, bird owners, and the birds all loved the material. They want the material for next year's fair.
Having success at Bloomsburg, I contacted the management of the poultry exhibit at the Harrisburg Farm Show. They had over 800 bird cages. They also agreed to replace the wood with grass. The results were the same. Everyone loved the bedding and management ordered it for next year's show.
We reached a lot of farmers and the feedback was overwhelmingly positive. Based on the number of birds at the combined shows, 200 may be a low number.
Small producing poultry farmers found warm season grass had many advantages. It does not pollute. The birds like it. It helps control aroma. It absorbs moisture. It dries out quickly. Wherever we introduced the bedding, farmers wanted to know where they could buy it for themselves.
Grass harvested in the late fall or early spring has the lowest moisture content. Using a 3/4" screen in a hammer mill or a 2" screen in a tub grinder produces the ideal bedding material with most particles <1.5" in length.
30 pound paper bags or 200 pound super sacks were the easiest to handle.
Project Outcomes
Utilization of material processed into poultry bedding
In the past, the cages at County Fairs utilized wood products for bedding material. In recent times, sawdust and wood shavings have become more difficult to obtain and increasingly expensive. Disposing of wood based bedding is difficult as it produces acid as it decomposes. Land fills don't want it and it is not good to spread it on a farm field. With the availability of warm season grass bedding 5 County Fairs changed from wood based products to warm season grass poultry bedding for their 2018 fair event. All 5 fairs reported positive results.
The same thing is true for the Bloomsburg Fair and the Harrisburg Farm Show. In the past, they both used wood products in their poultry cages. With the availability of warm season grass bedding both events agreed to try this bedding. 900 poultry cages at the Bloomsburg Fair utilized warm season grass for poultry bedding. 800 poultry cages at the Harrisburg Farm Show utilized warm season grass for poultry bedding. Both events reported positive results and want the bedding for next year. Tom Topper, Poultry Chairman at the Harrisburg Show wrote: Everyone was very happy with the performance of the warm season grass as an ammonia controller and as a moisture dryer. It took all the moisture from the pens and kept the birds dryer and odors to a very minimum. Even the concerns with the white birds being discolored proved to be non founded. Very pleased with the overall performance of the product.
The Association of Warm Season Grass Producers has as a goal to develop the warm season grass market. Early on in the poultry bedding project we realized the market potential for warm season grass bedding. Mike Palko led the effort applying for an additional grant. He secured funding for SARE Project number ONE18-320 - Developing Markets for Warm Season Grass within the Pennsylvania Farm Community. Many of the same people who worked on this grant are helping Mike develop the grass bedding market.

We planned to use a garbage truck to experiment with material transport. We thought the compression capabilities of a garbage truck would allow us to carry a tremendous amount of material in a single load. We contacted 3 garbage truck owners. When we described what we wanted to do and the characteristics of the material, none of them would allow us to load their trucks. They were, as were we, afraid the material would not come out of the truck completely. Processed warm season grass has a tendency to "bridge" and stick in place. It would cause a major problem for a garbage truck if that happened. We substituted a horizontal baler for the garbage truck component of the project.
The horizontal baler had both advantages and disadvantages. We used clear bags. That may have been the cause of the condensation. A black plastic bag may not have the same moisture issues. That is an area for further study.
The automated process farmer Len Reggie developed is a very efficient way to process and bag warm season grass bedding. The disadvantage of the system is it is only available at the Reggie farm. Transporting material from other farms for processing at the Reggie farm is not cost effective. If the Reggie equipment was mounted on a trailer and moved from farm to farm, bedding could be processed at any time of year. Such a unit could possibly service up to 8 farms. This is a possible area for additional study.
A goal of the project was to process in the field. We fell short in this area. The New Idea Uni-processor was the only "in-field" processing technique. It did all the processing and left all the dust in the field. The unit is no longer manufactured. I have since learned of other equipment that will process in the field. One of the Association members has a new round baler that will chop the material with 17 knives and produce a plastic wrapped bale. This is a possible area for additional study.
The company Foampack had committed to helping us with super sack loading. Due to a change in staffing from the time we wrote the grant to the time of the research they were unable to assist. We were able to load 200 pound in a super sack. This filled the bag and was very manageable.
Every time we showed people warm season grass poultry bedding they wanted to know where they could purchase some. We currently have a limited number of farmers processing bedding for sale. Unless the material is available to poultry farmers for purchase the market will never develop. This is a possible area for additional study.
Because warm season grass is a new bedding material for poultry operations, there are numerous areas for additional study. I have identified a few. There are many more. The endorsement by top people in the poultry field and the wide acceptance at fairs and agriculture shows demonstrates the need for further study and process development.