Final report for FNE21-979
Project Information
The farmers at Honey Brook Organic Farm sought to measure two low-tech composting systems--windrow, and low-cost/low-tech aerated static pile (ASP)--side by side and compare them, both in terms of cost (labor, fuel, equipment usage and wear and tear), time and quality of finished compost. After the creation of the second ASP, farmer James Kinsel deduced that ASP composting was not a good fit for his farm operation, as he doesn't have a need to create compost quickly, the time and cost savings anticipated were not realized and space to compost is not in short supply at his farm. However, the heat created by ASP composting can supplement fuel required for heating greenhouses in the winter for fruit tree overwintering. Outreach for this project exceeded the farmers' expectations, as collaborations were forged and another grant opportunity pursued as a result of the two tours and one workshop provided as a result of this project.
This project plans to measure two low tech composting systems--windrow, and low cost/low tech aerated static pile (ASP)--side by side and compare them, both in terms of cost (labor, fuel, equipment usage and wear and tear), time and quality of finished compost (nutrient content, biological activity, pH, moisture, etc.). Initial piles will be assembled at the same time, utilizing the same volume of materials and the same “recipe”, including C:N ratio. Our objectives are stated via the questions we seek to answer:
- What cost savings are possible with ASP versus windrow composting (labor, equipment, fuel)?
- What amount of feedstock can be processed and what quantity of finished compost can be produced in a year utilizing ASP versus windrow composting?
- What are the physical, biological and chemical properties of compost produced using ASP versus windrow composting?
Problem: The region where Honey Brook Organic Farm is located produces a lot of organic materials currently not being recognized for their value as compost feedstocks. There is an overabundance of horse manure and bedding not being managed in an ecologically sound and sustainable manner. Instead, these materials are either landfilled or stockpiled on the farms where they originate, potentially generating odors, attracting pests and contributing to ground and surface water pollution through loss of valuable nutrients.
In addition, soils in the region where Honey Brook Organic Farm is located include a significant percentage of sandy loams and loamy sands that are typically low in organic matter and Cation Exchange Capacity (C.E.C.). A low C.E.C. means the soil has reduced capacity for holding onto applied nutrients, which can lead to more leaching of fertilizers into groundwater or running off into surface water.
Honey Brook Organic Farm applies between 6 and 10 tons of compost per cropped acre each year in an effort to correct these soil deficiencies. With approximately 110 acres in production, this amounts to a seasonal need of about 880 tons of finished compost.
As with many organic farms, composting has played a critical role in the farm’s vegetable production system. The farmers have used a traditional windrow method of composting, turning piles with a large wheel loader. Compost feedstock consists mostly of horse manure in sawdust bedding but can also include municipally-collected leaves and woodchips. This material is very active, heating readily and requiring frequent turning to introduce oxygen into the system and to check excessive heat generation in the composting materials. With the demands of, at times, an overwhelming amount of other farm work and the difficulty of finding loader-savvy staff, it can frequently be difficult to turn piles at optimal times. Additionally, this composting method typically takes 6-12 months to produce finished compost, and requires the utilization of a large area (approximately 3 acres), which could be used for active cultivation. This is especially relevant since Honey Brook Organic Farm plans to decrease the acreage farmed at other sites.
Although the farm has breathable textile covers which, when deployed, shield the composting materials from excessive rainfall, the frequent turning requirement and labor shortages mean that the covers are not used until the final turning. This can result in more leachate formation than is ideal.
Solution: Kinsel proposes to pilot the development of a low cost, low tech Aerated Static Pile (ASP) composting system for processing of horse manure/bedding, leaves and wood chips. The ASP system will be compared side-by-side with the windrow system to determine which is most efficient, economical and ecological. The ASP system also offers the advantages of rapid 30 day cycle time to finished compost, on a smaller area footprint without turning that will make it easier to protect the materials from potential leachate runoff.
Beyond the benefits provided to Honey Brook Organic Farm, this project will demonstrate to the local farming community the efficiencies that can be obtained when working cooperatively to address what is essentially a solid waste problem, and opportunity. It should be noted that the area where Honey Brook Organic Farm is located contains the highest percentage of permanently preserved farmland in the state of New Jersey. New Jersey in general has a large number of horse farms, and with the average horse generating 51 lbs. of feces and manure and up to 15 lbs of spoiled bedding per day, effective manure management is a pressing issue and one that, through research for this grant it has been discovered, though acknowledged as a problem has received scant research attention.
A successful demonstration project, particularly one that is low cost and low tech, will encourage other landowners and farmers in the area to use readily-available feedstocks and to potentially install their own ASP composting systems, thereby enhancing their farms’ economic and ecological viability. Once this happens, a variety of local options will become available for producers/generators of horse manure and wood chips, solving a currently-existing logistical problem of long delivery distances via large truck. This will increase time and cost efficiencies, and also decrease carbon emissions. This management approach will also have the effect of decreasing water pollution through loss of nutrients. These are all valuable elements, particularly in light of the system vulnerabilities exposed by Covid-19 and global warming.
I have been farming vegetable and small fruits organically since 1988. I ventured out on my own in 1991 on 5 acres rented from a local Watershed Association and established a small 50 member CSA program the first year. Over the following years, I rode the expanding market for local organic produce continuing to market almost exclusively through a CSA, growing in membership and acreage each year. With farm income we were able to purchase 2 farms in 2007 and 2008 within several miles of each other in Chesterfield Township, NJ which is located southeast of Trenton and only 30 minutes from the farms in Pennington where we started. This expansion allowed us to increase production to 120 acres of vegetable and small fruit crops on a total of 4 farms and serving around 4000 CSA customers. At our peak in 2016, we grossed around 2 million. However our peak of net income occurred in the mid 2000's when we routinely netted between $150,000 and $250,000 before taxes. It is my view the market interest in local organic was partly a consumer fad and of course there have been other major shifts in this market since I first started farming. We have experienced this shift as an attrition to the size of our membership dropping from 4000 in 2016 to 2500 by 2021. There was of course a bump in 2020 up to 3500 when the consumer was demonstrably anxious over the food supply during the Covid disruptions of 2020. As a result of my assessment that CSA was no longer viable for us and seemed to suggest a highly unstable market, we got out of farming vegetable crops completely, with the exception of 8 acres of Asparagus, perhaps a lateral move from one foolishness to another, time will tell. We are no longer doing CSA, but instead are focusing on fruit crops and the Asparagus using a combination of PYO and wholesale. We currently have established plantings of strawberries, kaki and American persimmon, jujube, hazelnuts, chestnuts, hardy kiwi, paw paw, apples and figs and are expanding our orchards to include European and Asian pears, peaches, blueberries, and unusual fruits such as Cornelian cherry, che, mulberries, etc.
While growing vegetable crops, my fertility program involved annually applying a maintenance rate of 6-8 tons/acre of compost we produced ourselves from off-farm materials. In recent years, we had relied on horse manure in sawdust bedding from a very large equine training facility several miles from our Chesterfield farms. Horse manure is abundantly available in our area, and this equine facility alone has the capacity to deliver a walking bed tractor trailer load once or twice a week if we did not set limits. With about 75-90 acres in production on our Chesterfield farms, we were producing about 720 tons of finished compost a year for these farms. To facilitate the traditional windrow composting method we used to produce our compost, a Volvo L70C loader with a 2 yard bucked was purchased. This loader as well as a Bobcat T595 track skid steer purchased in 2020 were both used on this ASP project. The Volvo loader was well suited to form the ASP piles having a large bucket and long reach, while the Bobcat was used to excavate the air pipes from finished piles.
Cooperators
- - Technical Advisor
Research
Initially, the primary goal of this project was to compare our current system of traditional windrow (TW) manure composting to manure composting done using an ASP system. According to advocates for the ASP system, switching from TW to ASP would allow the farm to utilize more of its land for crop production, save time and money on labor and fuel and to produce larger quantities of compost at a faster rate for the purpose of boosting soil resiliency.
Upon witnessing the massive amounts of heat generated by an aerated pile, we reassessed our objectives to include an investigation into the use of the ASP system and hardware to put this waste heat to work by heating a greenhouse for overwintering fig trees.
Traditional Windrow (TW)
Fresh manure is formed into long piles called windrows approximately 14 feet wide and 7 feet high using a bucket loader. The windrow length can vary according to the space available. In our case, we use a Volvo L70C loader with a 2 cubic yard bucket. The windrows are periodically turned to control the pile temperature, ensure thorough mixing of materials and to ensure that all composted materials including those on the surface of the window are exposed to the typically higher temperatures within the pile in order to reduce pathogens. The National Organic Program (NOP) Final Rule stipulates that animal manure composts must have "maintained a temperature of between 131F and 170F for 15 days . . . during which period, the materials must be turned a minimum of five times" in order to receive the special allowance for application afforded composts instead of the stricter use requirements for manures. Turning the windows is again performed with a bucket loader essentially moving the windrow a bucket at a time to an adjacent location. If the work is properly laid out and organized, turning a windrow can be fairly quick work, on the order of 275 - 300 cubic yards an hour using a 2 yard bucket. In this way, a whole field of closely spaced windrows can be systematically shifted one space over in the same direction. This works nicely for addressing the risk of cross contamination of composted material with fresh manure possibly contaminated by a pathogen. Specifically, we dealt with this concern by setting up an inlet side of the compost field and an outlet side, where fresh materials are turned in the direction of the outlet, so partially composted materials are never exposed to fresh residual materials that may be left in the spot for a turned windrow.
Long stemmed compost thermometers are inserted into representative piles and temperatures recorded to ensure compliance with the NOP rule.
We had extensive historical data from our years of TW composting the same horse manure in sawdust bedding feedstock material from the same equine facility, so this historical data was used for comparison to the ASP process using this same material.
ASP
To acquire a working knowledge of ASP in order to get started, we connected with Peter Moon at O2Compost Systems & Training, Snohomish, WA. I would highly recommend Peter's package of system design and training materials, which included not only a fully designed starter system to meet our needs but also some of the hardware, a detailed list with local sources for materials not provided and an exceptional 71 page Benchmark Operations Manual for constructing and managing the ASP pile; setting up the air system, how to regulate the air flow, common problems to overcome, basically everything needed to start your own ASP project. This package also includes direct access to Peter and his years of experience which we exercised through several phone calls. Our ASP project involved a manure pile 29 feet wide, 80 feet long and 7.5 feet high (approximately 350 cubic yards), a 1 hp air blower, various HDPE 4" pipe fittings, 24 lengths of 4" X 10' HDPE perforated drainage pipe and 8 lengths of 4" X 10' HDPE solid pipe. This pipe is readily available off the shelf at a building supply store. However, this choice of pipe dictated the process necessary to deconstruct the pile when finished to extract and reuse the pipe for the next pile. A continuous length of pipe would allow pulling the pipe out the end of the finished compost pile using a tractor and a special clamp attached to the end of the pipe. The 10 foot lengths we acquired could not be attached to each other in a way strong enough to support this method of extraction, so instead the finished compost was carefully removed from the pile to expose the pipe using a Bobcat skid steer.
The construction process is outlined below and shown in an accompanying sequence of photographs in the Education and Outreach section of this report.
- A 6" base layer of wood chips is laid down over an area 14' wide by 60' long to serve as part of a "plenum" diffuser for the the air pipes laid directly on this layer. It should be noted that the diffuser layer does not extend to the edge of the fully constructed pile, since this would short circuit the effort to move air into the compostable materials.
- The 10 foot sections of 4" pipe are connected to form 80' long pipe assemblies consisting of a section of solid pipe at each end with 6 lengths of perforated pipe in between. The four pipe assemblies are laid 4' apart onto the plenum diffuser layer of wood chips with the regularly spaced perforations or holes opening down into the chips. In the case of the Home Depot pipe, the holes are about 5/8" in diameter, spaced 3" apart in two rows which are oriented at 4 and 8 o'clock when set on the chips. Faced down, the pipe has little potential to fill with leachate or wood chip fines.
- On top of this, another 6-8" of wood chips are applied to complete the plenum diffuser, which functions to distribute the air blown into the pipes over a larger area than would occur if compostable materials were directly applied around the pipe.
- Compostable materials are now added to form a windrow over the plenum diffuser and pipe to form a completed pile with the dimensions provided earlier. A large loader is best suited to this purpose with the ability of reaching into the center. The loader is also used to push up the materials as needed into its final form. Some final hand work may be necessary to complete the aesthetics of the pile if this is a concern when photographs are to be taken, but is unnecessary for production focused composting.
- The pile is then covered with a "biofilter" layer about 12" thick of previously finished compost to screen out any odors that may occur but this layer also functions to insulate the active material in the pile so it is more evenly heated and every molecule of manure is guaranteed to receive the necessary 132 degrees F for a minimum of 3 days to ensure sterilization of pathogens.
- A manifold constructed of this same 4" pipe with the blower on the opposite side is now connected to the 4 pipe ends which are intentionally left exposed. The ends distal from the blower are also left exposed and end caps are connected.
- All that is left is to run a modest power cord to a cycle timer also provided in the O2Compost package which in turn is connected to the 1 hp inflatable kiddy toy blower and hit the "on" switch. The cycle timer is critical to the pile management and basically consists of two knobs, one for setting the "time on" and the other for "time off". With these two timer parameters, the aeration of the pile is managed and controlled. These parameters repeat continuously until set to a different value. The blower is oriented to provide positive air flow into the pile system. In other words, it is blowing air into the pile rather than pulling air out of the pile. This difference is critical to the design, since a positive air flow is much less demanding on the blower. Pulling air out of the pile (negative air flow) will achieve the same pile aeration and will produce the same compost in the end, but is much more demanding on the blower, which now must deal with temperatures in the range of 150 - 165 degrees F as well as the moisture saturated exhaust.
- 5 compost temperature probes with stems from 30" to 48" are installed in various representative locations in the pile to monitor and assess that the Process to Further Reduce Pathogens (PFRP) threshold of 55oC (131oF) or higher for a minimum of 3 days, is achieved.
- Temperatures were monitored and recorded several times a week and are shown here, along with the cycle timer settings (ASP COMPOST LOG).
Exploring the Use of ASP for Heat Extraction
At the end of 4 weeks with an average pile temperature of 149 degrees F, I purchased a larger capacity 300 cfm inline blower to explore pulling heat from the pile. After installing the exhaust blower, I observed that the pile was generating exhaust temperatures of around 150 degrees F. After operating for 6 days the exhaust blower failed, most likely a casualty of the high heat and humidity. A month after trying this experiment and with average pile temperature still at 137 degrees F, I decided to experiment further with heat extraction from ASP piles.
I decided to experiment with two methods for pulling heat from an active ASP pile.
Closed system
This approach basically involves embedding a separate tubing system into the ASP compost pile and circulating air from an adjacent greenhouse through this array of tubes and back into the greenhouse. This avoids issues with the high humidity that would have to be dealt with if the ASP exhaust was used directly for heat.
- A test location was chosen for a second ASP pile 30 feet from a greenhouse used to overwinter figs at a temperature of 26 degrees F. The plenum layer was partly constructed as above, the pipe recovered from the first ASP pile and then installed at this new location. Instead of topping the pipe with 6-8" of additional wood chips to complete the plenum diffuser, a thicker layer of 12-14" was applied in the hope that upon the completion of composting, the same plenum layer with pipe intact could be reused for additional composting cycles.
- Eleven 1" diameter HDPE black tubes were run the length of the pile and spaced 1 foot apart on top of the wood chip plenum diffuser.
- Two identical manifolds were constructed from 4" PVC sch 40 pipe, a 4" end cap, a 4" elbow, eleven 1" plastic threaded hose barbs and hose clamps. The 4" PVC pipe was drilled and then tapped to receive the 1" NPT end of the threaded hose barbs.
- 4" supply pipe was used to connect the manifolds into the greenhouse.
- To insulate the supply pipe connecting the manifolds to the greenhouse, both lines were amply covered with horse manure.
- A decision must then be made regarding positive or negative blower attachment to one of the supply pipes.
- Temperatures were recorded several times a week at the inlet and outlet supply pipes.
Open System
This approach offers the promise of greater efficiency, meaning more heat extracted from the compost. It is integral to the ASP aeration system in that the exhausted air has passed through the heated pile using the ASP pipes. What must be overcome is higher heat and humidity, which pose challenges to the blower and the greenhouse environment if directly vented into the greenhouse.
To deal with both the heat and humidity, we constructed what is essentially a giant radiator out of 40 foot lengths of damaged 2" irrigation pipe. The radiator is located inside the greenhouse and functions to cool the exhaust gases before reaching the exhaust blower. When cooled, the exhaust gases also drop moisture content inside the radiator unit. This radiator is constructed in such a manner that condensate can flow through the unit and drain as water at the bottom.
More specifically, the radiator was constructed as follows:
- Pipes were chosen that were catastrophically damaged, meaning that the female ends were damaged beyond repair. Couplers were removed and damaged female ends were cut off, leaving approximately 40 foot lengths of 2 aluminum pipe.
- We had several aluminum shelving frames left over from a previous project which up to this point had no purpose. The frames were 4' long by 5' high, with five 7/8" aluminum angles at 11" intervals running lengthwise and rectangular aluminum tubing at both ends and in the middle. These frames essentially served as rigid structures for mounting and holding the 5 lengths of aluminum pipe using U-bolts. Pipes were spaced at 11". An aluminum frame was used at both ends of the assembly as well as one in the middle. After attachment to the frames, the whole pipe assembly was oriented vertically and secured in the upright position to the greenhouse frame with a 2-5 degree pitch toward the end opposite from where we intended to attach the blower.
- Two manifolds were constructed using 4" sch 40 PVC, a 4"-2"-4" PVC Tee, a 4" elbow, a 4" end cap, short 6" lengths of 2" PVC sch 40 pipe, and rubber pipe connectors with stainless steel hose clamps which attached the aluminum pipe to all this PVC.
- The manifolds are oriented vertically as are the aluminum pipe.
- At the bottom of each manifold, a small 1/8" hole was drilled to allow water to escape the system during the blower off phase of the cycle timer. Such small holes should not impact the air flow drawn from the ASP pile.
- A heavy duty 2.0 hp blower designed for children's bouncy toys was purchased and the inlet modified using a 4" PVC toilet flange. This served as the high capacity exhaust blower.
- At a convenient height on the manifolds, a small hole was drilled to receive an inserted temperature probe. Inlet and outlet temperatures as well as ASP pile temperatures were recorded several times a week.
Farmers traditionally compost what is readily and cheaply available. This will impact what farmers are prepared to do to optimize the parameters (ie C/N ratio, porosity, density) that influence the compostability of feedstocks. The ASP project was conducted in Chesterfield, NJ where the farmers have been receiving what appears to be consistently uniform horse manure in sawdust bedding from a large equine training facility for several years. To date, the farmers composted this material without any additions using a traditional windrow system which involved turning the piles several times over the course of a 10-month period and then making field applications at the end of that time. The windrows typically heat to an excess of 160 degrees F fairly quickly and then stay above 150 degrees for an extended period, with the temperature dropping as the material dries out during the late summer. The farmers do not irrigate the piles, but instead wait for fall and winter precipitation to reactivate the piles, which they do and heat again to 140 degrees F. The windrows dry down in late summer despite longitudinally overlapping the windrows during a late summer turning to capture precipitation and minimize any leachate formation.
The farmers constructed the ASP pile according to Peter Moon's specifications except the feedstock was not saturated with the addition of water before forming the pile. This meant the ASP pile would most likely dry out before finishing. Although Peter Moon advised against the efficacy of attempting to irrigate the feedstock during ASP composting, the farmers did make the effort using multiple runs of drip irrigation with partial success. One notable trick for those attempting ASP composting: when applying the biofilter to the completed pile, the farmers used a side delivery spreader. This spreader did not throw material high enough to uniformly cover the top of the pile until the farmers noticed that they could make a later pass and use the embankment formed by the side of the pile to pitch the angle of the spreader upward.
James Kinsel's preliminary assessment of the ASP system was that ASP may be more appropriate for some high density, high moisture feedstocks like food waste and some animal manures without bedding and leaves (for ensuring a high enough temperature to kill grass seeds). However, the horse manure in sawdust bedding which is available to us at no cost composts readily using the traditional windrow system with periodic turning. We do this turning using a 2-yard loader, which staff has been easily trained to use. The feedstock is also so forgiving that these turnings can occur when time is available, which eases labor management. ASP requires much tighter management and greater expertise, which complicates labor management. Since we have accepted and planned that finished material will take 10 months to finish, this means the faster composting time for ASP is not an asset to our operation. There is no discernible difference in compost quality. Space for composting is also not a constraint for us.
LABOR AND MACHINE TIME COMPARISON
The following details the labor and machine time spent constructing a 348 cubic yard ASP pile as per Peter Moon's specifications, ie 8.5' high x 80' long x 29' wide for an approximate volume of 348 cu yd:
1) Setting up base plenum layer of woodchips: 5.25 hours labor (1 machine hours)
2) Installing reused air pipes, reusing existing manifold: 1.5 hours labor
3) Cover pipes with wood chips: 4 hours labor (1 machine hours)
4) Form manure pile using loader: 5 hours labor (5 machine hours)
5) Add biofilter: 1.5 hours (3.0 machine hours, 1.5 for loader and 1.5 for tractor with spreader)
Total Hours Required: 17.25 hours labor (10 hours machine)
Using the traditional windrow system, the farmers can turn windrows at a rate of 250 cubic yards per hour. Initial windrow formation is slower at about half this rate at 125 cubic yards per hour. So for a comparable volume of manure of 348 cubic yards, the time required to form the initial windrow is approximately 2.78 hours and each subsequent turning requires 1.4 hours. Windrows are turned 4 times after formation, which means it takes about 8.38 hours to compost 348 cu. yd. of this material using traditional windrow composting which is half the labor hours of the ASP system, in the farmers' early experience. All of this 8.38 hours is also machine hours, so the traditional windrow system is comparable to the machine hours required with ASP, again in the farmers' early experience.
Some caveats are in order before coming to any definitive conclusions, of course, since James Kinsel has extensive experience using traditional windrow composting and the horse manure feedstock is ideally suited to windrow composting. ASP construction times could be reduced with efficiencies gained by experience, but exactly how much is uncertain. Mr. Kinsel wishes to make the point that it is not a slam dunk that ASP is a better composting method in all cases. For sure there are feedstocks that cannot be composted effectively using traditional windrow, as pointed out earlier, but there are also feedstocks where excellent results can be achieved with fewer headaches.
Aside from the compost itself, one obvious observed benefit to ASP composting for HBOF is the potential use of the massive amounts of heat over a prolonged period generated by the process. Kinsel experimented with an inexpensive higher-volume inline blower which pulled heat through and out of the pile with impressive results, although the blower failed from the heat and humidity in less than a week.
Kinsel is changing the farming operation to include high tunnels of in-ground cold-tolerant fig trees as well as figs in media-filled Macrobins which will be overwintered in a greenhouse at 27 degrees F with propane heat. He would like to minimize propane use for environmental as well as cost reasons. He ran a secondary experiment with an ASP located close to an overwintering greenhouse where he constructed the pile using 2 different approaches to extracting heat:
The first method involved using the existing ASP aeration system to pull air through the pile and exhausting into the greenhouse. Peter Moon's design involves blowing air into the pile, which is technically easier and not as demanding on the blower. Exhausting air though the ASP aeration pipe is more demanding on the blower, since it will directly experience the hot and quite humid air coming through the pile. Kinsel tried a higher flow rate blower set up to exhaust from the pile and, as mentioned previously, although an impressive amount of heat is available, the blower failed in less than a week. Heat and humidity are the culprits. To remedy this challenge, he sought to design an inexpensive "radiator/dehumidifier" on a large scale located inside the greenhouse and upstream of the blower which would not impede airflow but would effectively pull enough heat and humidity from the air stream that the blower could enjoy a more favorable operating environment. This "radiator/dehumidifier" was constructed from used and damaged 2" x 40' irrigation pipe with 4" PVC manifolds at both ends serving as the inlet and outlet. The outlet manifold is connected to the blower, while the inlet manifold is connected to the aeration system of the ASP pile. Since the ASP pile is about 40 feet from the greenhouse, he covered the 4" pipe leading from the pile to the greenhouse using fresh manure to serve as insulation. The manifolds of the "radiator/dehumidifier" are both oriented vertically with a small condensate drain hole at the bottom of each. Additionally, the manifold is slightly elevated at the outlet end, so condensate has some incentive to flow back to the inlet manifold and then drain from the bottom of that manifold. The blower protocol for the ASP system calls for repeating on/off cycling of the blower, so Kinsel's thinking was that during the off part of its cycle, condensate would have the opportunity to flow back to the inlet manifold and out of the system. He observed a 6-8 degree F temperature drop from the inlet to the outlet temperature, with outlet temperatures still in the 88 to 97 degree range in April. Humidity was still a problem. Since Kinsel is a farmer and not an engineer, he approached the problem through trial and error rather than calculation, so he intends to double the number of irrigation pipes to 10 and see what happens. If not satisfied, he can easily add another 5 pipes. Although HBOF staff may excel in many things, preserving irrigation pipe is not one of them, so Kinsel has plenty of damaged pipe from which to choose. He will also simplify the manifold to 6" PVC pipe with 2" holes cut to receive the inserted irrigation pipe firmly sealed with caulking material. Care must be taken in properly grading the pipe connecting the ASP manifold at the compost pile to the "radiator/dehumidifier" manifold, since condensation will occur once the hot, humid air is drawn from the compost pile into the somewhat cooler connecting pipe. Kinsel had the airflow choked to a halt by condensate build-up after operating for several days. To remedy this problem, he more precisely graded the connecting pipe so it graded down to the connection with the ASP manifold, which also was the system low point. He then drilled a small 1/8" hole at the bottom of the pipe at this point so water could drain out of the system.
The second method involved a closed air system of pipes embedded in the ASP and located just above the ASP aeration pipes. This "heat extractor" consisted of 11 runs of 1" PE pipe running the full length of the ASP pile with 4" manifolds at both ends with each manifold conducting through 4" pipe into the same 30' x 96' greenhouse with an attached blower in the greenhouse. This system also had its challenges. It seemed to work best when the ASP part of the system was pulling air down through the pile and exhausting into the greenhouse. This is not surprising, since the 1" PE tubes were set on top of the upper woodchip layer covering the ASP aeration pipes. Periodically to test the system, he had the ASP system blowing into the pile and this seemed to lower the temperatures experienced by the PE tubes located just above the ASP pipes. Since both manifolds run via 4" pipe into the greenhouse, the same air is recirculated. The decision had to be made whether to blow into or exhaust through the system. In the former scenario, the system is slightly pressurized, in the latter it is slightly depressurized. Kinsel decided to set the blower blowing into the system so any leaks would mean a loss of air rather than the potential for leachate getting drawn into the system and interfering with airflow. This "heat extractor" system typically boosted temperatures by about 25 degrees F. For example, on the evening of 4/4/22, the inlet temperature in the greenhouse was 50.5 degrees and the system exhausted that air back into the greenhouse at 80.8 degrees. The advantage of this second method of heat extraction is that humidity from the composting feedstock is not an issue and anything potentially noxious emitting from the composting materials is not drawn into the greenhouse. Although we have yet to extract the runs of 1" PE tubing from the finished pile, Kinsel expects they can be withdrawn easily by first removing most of the compost on top and then pulling them out of the pile individually after the manifolds are uncovered and disconnected. There were over time issues with this system, which seemed to have airflow losses. Kinsel suspects one or more lines may have become disconnected from the manifolds. The 1" PE was attached to hose barbs with SS hose clamps, the hose barbs threaded into 1" NPT tapped into Sch 40 PVC pipe at regular intervals. Kinsel plans to investigate before the next heating season.
James Kinsel did conclude that ultimately the ASP system was not a good fit for his farm, so he did not create any additional ASPs after the first two. There simply was no reason to continue to create piles that were composting at a faster rate than he had the need to apply (the farm ceased being primarily a vegetable farm during the course of this project, so the need to land-apply compost quickly did not exist).
The biggest observation made was that while the ASP system does indeed create usable compost faster than traditional composting, the complexity of system set-up, monitoring and management outweighed the potential benefit of creating compost faster. In addition, since the farm is permanently preserved, the deed on the farm restricts sales of finished compost so there is no economic advantage to create compost that can't be sold off-farm for additional income.
However, there is a benefit to managing horse manure in any compost system on an organic farm to ensure the material does not go to a landfill or otherwise be stockpiled in a way that would compromise water quality. Compost does sequester carbon so there is that residual benefit to composting. There is an additional benefit for using residual ASP heat for greenhouse supplemental heating.
There were no changes to the farm's profitability as a result of this project, or greater efficiencies realized. There was a slight lowering of inputs with respect to the propane heating of one greenhouse.
Education & Outreach Activities and Participation Summary
Participation Summary:
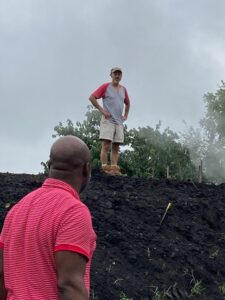
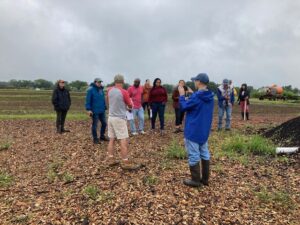
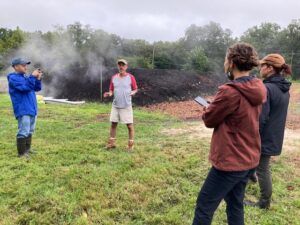
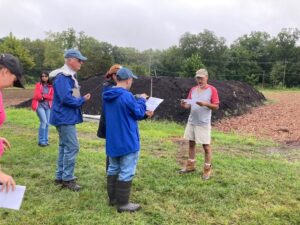
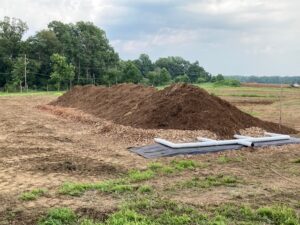
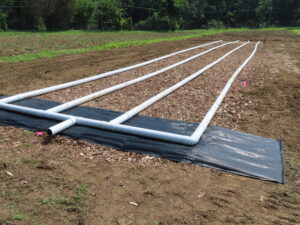
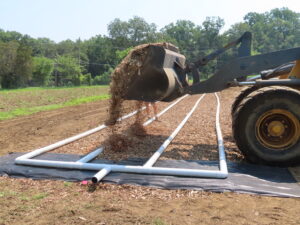
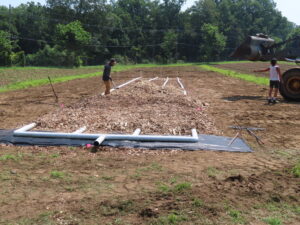
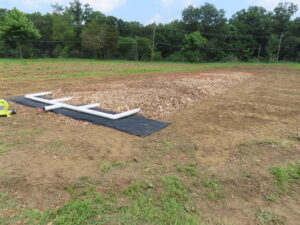
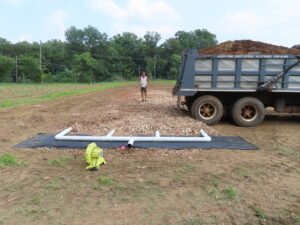
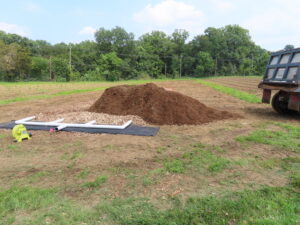
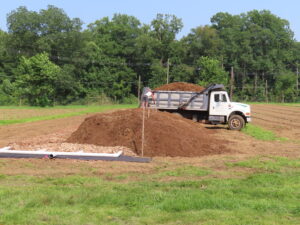
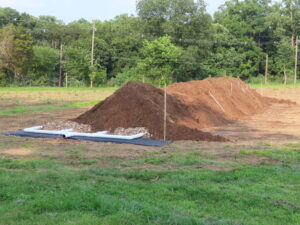
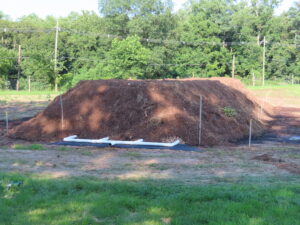
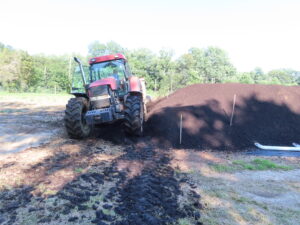
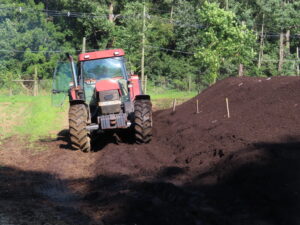

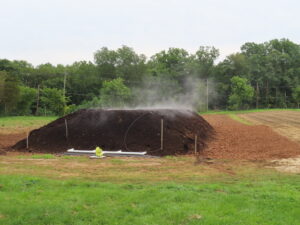
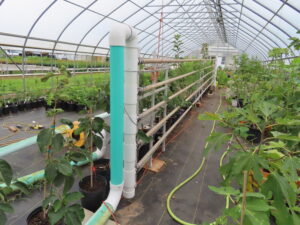
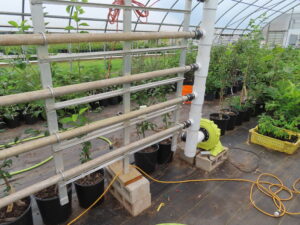
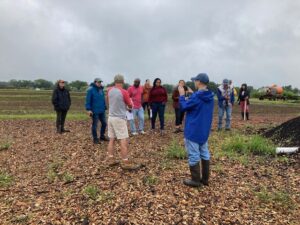
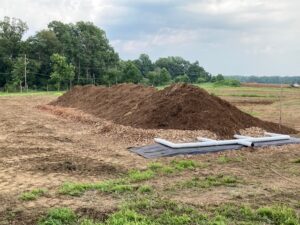
The first educational session after the first ASP was created at Honey Brook Organic Farm was at the New Jersey Compost Council's "Fundamentals of ASP (Aerated Static Pile) Composting" course on September 9, 2021. The course was designed for farmers, compost operators, municipalities, consultants and others and allowed participants to understand if ASP was a good fit for them, how it works and what is needed to either get started or improve their current processes. A hands-on site demonstration was conducted of HBOF's ASP composting project.
Participants earned Rutgers Continuing education credits and USCC Compost education credits and was live-streamed over Zoom. The course lecturer was Peter Moon, our ASP composting consultant. Peter has over 35 years of consulting experience, over two decades of which is specific to organics waste management. Peter started O2Compost in 1996 and since that time, has designed and constructed over 500 aerated compost systems for municipal, institutional and agricultural facilities. He is a licensed civil engineer in the State of WA. O2Compost has evolved over the years to become a recognized leader in training owners/operators on the ASP method of composting. Course participants were also entitled to a free consult with Peter Moon to answer any additional/specific questions they hadn't had the opportunity to ask during the course. Peter provides lifetime consulting services to anyone who purchases his ASP designs.
As part of its monthly Grower & Farmer Speaker Series, Jim Kinsel shared information about our ASP demonstration pilot for composting of manure, wood chips and leaves on our certified-organic produce farm. The October 18, 2021 NOFA-NJ tour was posted on YouTube, which can be viewed here.
James Kinsel and Sherry Dudas of HBOF partnered with the New Jersey Farm Bureau (NJFB) and other collaborators (see below) to offer an "On-Farm Composting Workshop: Fertilize with Locally-Available Compostables" on the farm. This involved several virtual planning meetings and procuring a commitment from NJFB to sponsor the workshop as well as to market it to their substantial Central New Jersey membership, which they did. The Northeast Organic Farming Organization-NJ also marketed the opportunity to their membership. The June 28, 2022 workshop agenda is here workshop6-28-22 and the description agenda is below:
This free workshop will prepare participants to safely and efficiently compost manure, wood chips and/or tree leaves via traditional windrow and Aerated Static Pile (ASP) composting. ASP composting optimizes the composting process and allows for operational efficiencies, saving time and money for farmers. With the cost of fertilizer and fuel escalating, this may be the time to figure out whether on-farm composting is a good fit for you and your farm!
Learn the basics of on-farm composting including:
- what makes compost great as a fertilizer;
- how to obtain free/cheap feedstocks;
- how to make sure you don’t contaminate food crops with feedstocks/finished compost;
- why you don’t need a DEP permit to compost or land-apply on your farm;
- how to use common farm hardware and equipment to get started; and
- how to use excess heat to warm greenhouses or high tunnels!
Lunch and coffee will be provided at no cost and the workshop is provided by the New Jersey Farm Bureau and a SARE grant.
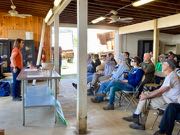
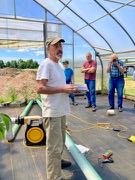
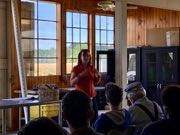
This ASP COMPOST LOG was discussed and provided to attendees.
Several unexpected results of the collaboration between the farmers of HBOF and Virginia Lamb, Sandy Howland, Ashley Kerr and Meredith Melendez in preparing for this workshop occurred, including an identification of the need for a revised on-farm composting fact-sheet for New Jersey farmers (which is now a "spin-off" project for this group), Sherry Dudas of HBOF was asked to be a farmer-partner on a USDA-NRCS Conservation Innovation Grant award which the NJ Department of Agriculture will receive to develop a system/database to match livestock farms' manure with producers who could utilize the nutrients in their operation and it was realized that NJ Department of Environmental Protection (NJDEP) and NJ State Agriculture Development Committee regulations may be routinely misinterpreted, disallowing farmers from selling finished compost from farms not preserved through the state's farmland preservation program. The realization of this misinterpretation and its subsequent correction will allow farmers to sell finished compost as long as they meet the NJDEP's permit exemption. Another residual benefit of the several educational events HBOF's farmers offered was the opportunity to enhance our side gig of offering farm consulting services.
Lastly, American Farm Publications published an article in its January 15, 2022 edition about HBOF's ASP composting system.
Learning Outcomes
We did not specifically request that participants to either of the two tours or one workshop report feedback, however two farmers who farm for a non-profit organization offered that they hadn't previously realized how easy and inexpensive the ASP system could be.
James Kinsel, the lead farmer in this project, came to appreciate the following:
- The extended period of high temperatures generated by the composting material.
- The difficulty of achieving proper moisture content for the duration of the composting period.
- The special equipment requirements for drawing hot humid air from the pile instead of exhausting air into it.
- The simplicity of simple windrow composting and forgiving nature of the compost materials when composted using the simple windrow method.
Project Outcomes
We are still evaluating ASP composting for the feedstock available to us. The ASP pile was still very hot and active after two months, which is a much slower turn-around than anticipated.
James Kinsel's preliminary assessment of the ASP system was that ASP may be more appropriate for some high density, high moisture feedstocks like food waste and some animal manures without bedding and leaves (for ensuring a high enough temperature to kill grass seeds). However, the horse manure in sawdust bedding which is available to us at no cost composts readily using the traditional windrow system with periodic turning. We do this turning using a 2-yard loader, which staff has been easily trained to use. The feedstock is also so forgiving that these turnings can occur when time is available, which eases labor management. ASP requires much tighter management and greater expertise, which complicates labor management. Since we have accepted and planned that finished material will take 10 months to finish, this means the faster composting time for ASP is not an asset to our operation. There is no discernible difference in compost quality. Space for composting is also not a constraint for us.