Final report for FNE21-983
Project Information
Most agriculture works on a seasonal cycle, planting in the spring and harvesting in the summer and fall. While oyster aquaculture typically spans two or more growing seasons. From the mid-Atlantic up to the Canadian Maritimes, oysters grow during the warmer months, remaining dormant during the winter months. Winter mortality and the cost of winterizing an oyster farm is a major cost. Figuring out a method that reduces labor costs and increases survivorship is an important factor for a farm's success.
Specific to our farm in Barnegat Light, NJ, long periods of westerly winds create extremely low tides and ice flows can damage gear and kill oysters. We deployed a study group and a control group to test two groups of oysters, measuring the labor costs, survivorship, and also marketability.
The Control group was a longline of floating oyster bags. A prediction was made that these oysters would involve less labor since they were not winterized. Surprisingly, these oysters actually required quite a bit of labor since the winter biofouling was so high. Growing oysters in floating gear typically creates a more desirable and denser oyster since the wave action creates a thicker shell. Once biofouling sets in, the buoyancy of the bag decreases and biofouling becomes exponentially worse. We experienced a large blue mussel set, as well as a bloom of sessile organisms like sea squirts and macroalgae.
The study group was bottom planted directly on the substrate. We allowed these oysters to grow out into the spring and summer and they were harvested by hand. These oysters required an extra physical step since the oysters needed a day or two to purge of unintended ingested sediment (sand and mud). We experienced very limited mortality from winter. There was some predation from cownose rays, but it was sporadic.
The study group of oysters required more labor and the results were a less marketable product. Important to note is that there's a trend towards demand for smaller and denser oysters. The control group was much more desired by our target audience.
Results of this study have been shared on social media as well as in the format of a flyer that's been distributed to growers at various aquaculture meetings.
This project sought to examine the (1) survivorship, (2) marketability, and (3) cost-effectiveness of the experimental method of growing oysters using floating cages and bottom planting in comparison to the control method of using bottom cages.
- Survivorship of oysters was quantified over the winter months and quantified cownose ray predation
- Marketability was quantified in terms of shell shape, density, and height and qualified in terms of aesthetics
- Cost-effectiveness was measured by records kept of costs of materials and labor of employees to construct, maintain, and transfer oyster crop
This uncovered information will be useful to other farmers by showing them a better method of growing oysters that will survive over the winter months with decreased cost and labor, while still producing a marketable and quality oyster. If this project is successful, it will improve oyster farming by eliminating the exclusive use of bottom cages, which are popular means of oyster farming in our community, and the challenges that come with this gear type.
Coastal states have seen an enormous opportunity for oyster aquaculture in underutilized waters and have worked to capitalize on these opportunities. Our farm, as well as other farmers in our community, use intensive subtidal bottom cages to farm oysters. This gear is used from seed through harvest to grow oysters and protect them from cownose ray predation. Cownose ray predation has a large impact on the shellfish industry, costing farmers time and money to protect oyster crops. However, the gear used to mitigate cownose ray issues has its own issues in terms of cost and labor. To address these issues, we intend to create a hybrid method of growing oysters using a temporal combination of off-bottom floating gear and bottom planting oysters. Off-bottom floating bags would grow out the oysters from Spring through Fall, then the oysters will be bottom planted in the early Fall (after cownose rays migrate out of the area) to then be harvested in the following Spring (before cownose rays migrate back for the Summer). We will evaluate whether this method can produce a marketable oyster in less than 16 months. The three main obstacles we plan to address with this method are cost (i.e., gear and labor), marketability, and survivorship (i.e., overwintering, predator avoidance).
Using bottom cages in oyster farming from seed to harvest requires significant capital, as well as intensive labor to maintain and winterize. The advancement of selective oyster breeding has given oyster growers access to fast-growing oyster seed, allowing growers in the Barnegat Bay and surrounding areas to harvest oysters in under 18 months. However, as oysters grow and require more gear, the costs become a significant barrier for start-up operations and for the profitability of existing operations. To reduce stocking density, the splitting of bags is necessary as the oysters grow, which involves the laborious tasks of tumbling and grading the oysters by size and putting them into new bags. This process forces growers to constantly purchase new bag materials or risk degradation of quality and the smothering of oysters. The prevention of biofouling organisms that collect on gear and oysters is another laborious aspect of our current gear system. It involves lifting the cages and pulling out the bags to be exposed at low tide. In this drying position, the racks and bags often fall due to wind and boat wakes, increasing labor needed to collect the fallen bags off the bottom and rearrange the racks. Winterizing our current gear is also extremely laborious because the gear must be moved to a deeper protected bay, or numerous oysters would be lost.
The use of a floating bag system could reduce physical labor and increase productivity and profitability. In terms of biofouling prevention, the bags can simply be turned over when needed to expose the accumulated biomass to air. The float-bag system will naturally tumble the oysters, where tumbling in general prunes the oysters' outer growth and contributes to better shape and shell density. Once the oysters are bottom-planted following the float-bag growing season, the oysters can continue to grow to market size without manipulation or labor needed to winterize. The oysters can then be harvested off the bottom in late spring. Bottom planting oysters is an appealing method because not only does it require less labor and gear expenses, but we have observed on our farm that oysters grown on the bottom (accidentally dropped and picked up in later seasons) appear to be cleaner and have improved aesthetics (see Image 1). Oysters, if given sufficient space, will grow an appealing round shell and a deep cup, contributing to a greater aesthetic and better meat to shell ratios. Oysters grown directly on the bottom also tend to naturally exclude the biofouling that is typical in the water column, further reducing labor and improving marketability.
The methods of our proposed solution will improve farm productivity, reduce farming costs, and increase net farm profitability. Our methods could contribute to an improved quality of life for farmers and employees not only involved in the Barnegat Bay Oyster Collective, but oyster farmers in the entire northeastern region, by cultivating oysters without such costly and time-consuming methods. Finally, oyster farming is a naturally sustainable farming practice, where oysters filter the surrounding water just by feeding. Therefore, creating more productive oyster farming techniques will undoubtedly contribute to the enhancement of water quality. Attached is a letter from other farmers in our New Jersey growing community that support and have an interest in the funding of our proposed solution.
The practice of bottom planting oysters over the winter season and harvesting them off the bay bottom by hand is a known practice in New England, but it is not applied southward due to cownose ray predation issues. On an oyster farm based in Massachusetts, oysters are grown out in cages and are then planted on the bayfloor in the Fall (Tompkins, 2017). We’d like to adopt this bottom planting method in combination with a floating bag method in our community because it is expected to be less costly and labor-intensive than our current growing methods and could very well create a more marketable product.
Fisher et al. (2011) conducted a study in Virginia pertaining to cownose ray predation relative to bivalve ontogeny. It was shown that cownose ray predation on shellfish is limited by shell size and density and is related to the gape size and bite force of the ray. If an oyster was too large or required too much force to be broken by the ray, the oyster was discarded. It was suggested that farmed oysters should have some measure of protection until they reach a shell depth of 22-24 mm or are strong enough to withstand a force of 1,400 Newtons. This gives our study guidance because it shows that growing oysters to a certain size before bottom planting would provide some defense against cownose ray predation. Our oysters would be well above the 22-24 mm shell depth before bottom planting and should therefore not be affected by lingering cownose rays in the area before or after their migration.
Thomas et al. (2019) evaluated the effect of aquaculture gear on the growth and shape of oysters during a “finishing period” in the Chesapeake Bay. Submarket sized oysters had been grown-out in subtidal bottom cages and were then transferred to four different gear types over a four-month “finishing” period to evaluate how shell shape and product quality were affected. The four gear treatments assessed were: floating bags, a rack and bag system, a bottom cage placed in the intertidal zone, and the control treatment of oysters remaining in a subtidal bottom cage. Overall, it was found that the floating bag treatment produced the largest gains in growth and shell shape improvement, indicating that this system may be a valuable method of finishing oysters over a relatively short period. This is similar to our proposed study due to the evaluation of a combination of two different growing methods. Our project would build on this by using an opposite method of first growing out the oysters in the floating bags and then bottom planting them.
In New Brunswick, Canada, Mallet et al. (2013) had compared the growth performance of horizontal rope-grown oysters and floating bag grown oysters. The results had shown that after one growing season, shell growth was 60% higher and weight gain was nearly double in the rope-grown oysters. The floating bag-grown oysters were found to have grown less due to crowding and competition for food in the water column. The rope-grown oysters in this study analogize to the bottom planted oysters in our proposed study, where the oysters would not be confined in equipment and expected to be able to grow better in the open instead of being crowded in floating bags for their entire growing span. This study shows that just using floating bags would not be optimal for oyster growth, and therefore the transfer of oysters to a more spread-out growing area with less competition from other oysters would be optimal for getting the oysters to market size.
Our project will also build on a study that is currently taking place on our oyster farm with Rutgers Haskin Shellfish Research Laboratory (RHSRL), funded through the NOAA Sea Grant project that is looking to optimize oyster seed strains that will grow well in high-salinity environments. With our proposed study looking to optimize the grow-out and gear methods of oyster farming, the results of our study could be combined with the results of the RHSRL findings, leading to a revelation of sustainable oyster farming using optimal seed strains and farming methods in our community. The results of this project would be impactful for farmers in our community, especially entry-level farmers because it would provide an outline to start up a sustainable and cost-effective oyster farm. This would be helpful because although NJ allocates great resources to industry development, there is not many advisories for technical help with starting an oyster farm. If funded, practical guidance would be offered to interested individuals.
Coming from a background in commercial fishing, Matt Gregg studied Marine and Coastal Policy and Aquaculture and Fisheries Science at the University of Rhode Island. After graduating, Matt founded Forty North Oyster Farms, LLC in 2011 in his home state of New Jersey. Forty North was the first commercial operation to grow oysters out of the historically significant Barnegat Bay since the mid-20th century stock collapse.
In 2016, Matt and another grower saw an opportunity to strengthen the local industry by creating a grower’s collective. Since then, the Barnegat Oyster Collective has handled marketing, safety compliance, and distribution for 14 independent oyster farms. The Collective has sold oysters all over the nation and annually exceeds $1 million in gross revenue. Their primary goal is to empower small sustainable farms and ensure they can achieve economies of scale.
Matt was named the Asbury Park Press Small Business Innovator of the Year, received the Edible Jersey Magazine Farm Hero of the Year Award, and has given Congressional Briefings about the impacts that climate change poses for the domestic shellfish industry. He is currently the NJ Aquaculture Association’s Vice President as well as a board member for New Jersey Sea Grant’s Science Advisory Board.
Forty North Oyster Farms grows oysters on 38 acres, primarily for restaurants in the New Jersey, New York, and Pennsylvania markets. Demand increases in the summer months when patrons visit the Jersey Shore.
Cooperators
- - Technical Advisor
- (Researcher)
Research
The following methods were consistent with the proposal [the only change was that the control group was left in place and not moved to a different location]:
Proposed methods:
Our project will begin March 1st 2021, where the purchase and preparation of gear will take place and seed will be obtained.
See the schematic of our proposed methods (Figure 2) and the supplied photos of gear (Figures 3 & 4) and site maps of our farm (Figures 5 & 6) for clarification.
Materials:
Our required materials for the experimental group will be longlines (Figure 3) and lateral lines made up of 250 feet of 3/8th inch thick floating polyline, two anchored poles for the longlines made up of galvanized 16ft posts, and 50 14mm ADP square oyster bags with the dimensions of 32”x3.5”x3”. Each bag will have Oyster Bag Floats attached to each side, which are made from hard plastic tubes. PVC pipe will be used to measure out the bottom planting areas. For the control group, 50 14mm ADP square oyster bags with two floats per bag will also be needed, as well as nine (9) 6-bay oyster bottom cages (Figure 4) that we use in normal operation. Costs of all materials for experimental and control groups will be recorded.
Methods:
Prior to the deployment of oysters, the 100 floating bags will be made and the anchors and longlines will be set. The area for bottom planting will be measured out at Site 1 using PVC pipe markers. The oyster seed in the nursery will retain on a 9mm screen and will be spawned in the winter of 2020-2021.
Phase 1 - Grow Out on Longlines
Beginning in late spring of 2021 (approximately June), oyster seed will leave the nursery and be deployed in the 14mm floating bags on the longlines at Site 1 (Figure 5 & 6) when they reach a size where they will not fall through the holes in the bags. The control oysters and the experimental oysters will be side-by-side on the longlines for grow-out, receiving the same treatment. There will be two longlines, with 50 floating bags attached to each line, for a total of 100 bags. There will be 500 oysters per bag, for a total of 50,000 oysters in this experiment. The oysters will remain in the bags on the lines until October 2021. During this phase, the oysters will be checked without opening the bags and flipped to reduce biofouling on the bags and oysters. All labor by employees for their manipulation of the bags will be logged.
Phase 2 - Wintering of Experimental and Control Groups
Once water temperature in the bay falls below 60 degrees Fahrenheit (October), we will begin winterizing the control and experimental groups. Oysters from both groups will be removed from the floating bags. The winterizing process for each group is as follows:
Experimental: The oysters in the 50 bags (25,000 total oysters) from the longlines will be removed from the bags and broadcasted onto the bottom of the bay at Site 1 in a 5,000 square foot area. The oysters will be dispersed in a density of approximately 5 oysters per square foot. All hours of labor by employees to complete this process will be logged.
Control: The 50 bags will have the floats removed and will be put into the 6-bay bottom cages that we use for normal operation. The cages of oysters will be moved to Site 2, a deeper and more protected bay, for their winterization until March. All hours of labor by employees to complete this process will be logged.
Phase 3 - Harvest of Control and Experimental
Phase 3 will begin in March 2022
Experimental: Oysters will be harvested by hand off the bottom. During harvest, numbers of alive and dead oysters will be counted. Missing oysters numbers from the initial 25,000 planted will be assumed to be taken by cownose ray predation. Harvest of the oysters will take place over the span of March to June 2022. Labor will be logged for how long it takes to harvest the oysters by hand.
Control: The bottom cages containing the control oysters will be brought back to Site 1 in March, to continue growing until their harvest in June 2022. The normal operation of splitting the bags will be done to reduce stocking density, as well as the normal process of drying the cages for 18 hours once a week to reduce biofouling at Site 1. Survivorship of the oysters will be counted when the oysters are removed from the bags for harvest. All labor time in this phase will be logged.
The marketability of the harvested oysters from both groups will be measured at the end of this phase. A ranking system will be used to rate marketability on 50 randomly pulled oysters from both the control and the experimental groups. The following metrics will be used:
- Biofouling conditions on the shells will be measured using an aesthetic scoring of 1-4, 4 being the least amount of biofouling and the most aesthetically pleasing, and 1 being the most amount of biofouling and the least aesthetically pleasing
- Shell shape will be measured using an aesthetic scoring of 1-4, with the rounder and more appealing shell shape being a 4 and the least appealing be a 1
- Oyster density will be measured using displacement in a graduated cylinder
- Shell height will be measured in centimeters
Harvesting of oysters should conclude by the summer of 2022, where the rest of the time allotted for our study will be used for data analysis and outreach activities of our results.
Research Activities 2021
So far in our projected study, off-bottom floating bags have been used to grow out the control and experimental oysters from Spring 2021 through Fall 2021. The experimental oysters were then bottom planted in Fall 2021 (after cownose rays had migrated out of the area) and are to be harvested in the following Spring and Summer of 2022 (hopefully before cownose rays migrate back). The control group oysters were left in the floating bags on the line for the duration of the winter. The control oysters will be tumbled and split into more bags to reduce stocking density as needed until harvest. We will evaluate whether our experimental method can produce a marketable oyster in less than 16 months as compared to the control group.
Research Activities 2022
Oysters from the control and experimental groups were harvested in the Spring and Summer of 2022, and data on oyster mortality, appearances, marketability, labor, and cost of the control and experimental methods were collected. Results are still being analyzed and will be included in the final report.
Pictures of our project so far:
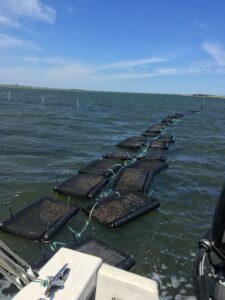
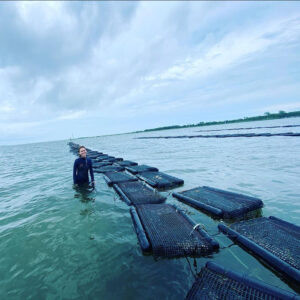
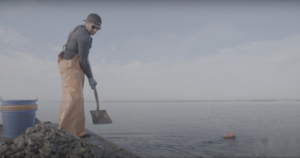
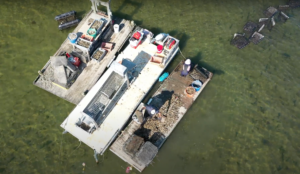
All oysters from the study have been harvested.
Numbers of alive and dead oysters were counted from random samples of the control and experimental groups throughout the study. The following data shows survivorship data at the time of harvest for each group:
Control group:
By March 2022, the mussels had clogged the bags and bound oysters together. Bags were picked apart and each bag had an average of 72 dead oysters, 123 too small, 147 petite, 38 medium, 17 large. The petite, medium and large were harvested. The dead were discarded. The oysters that were too small were returned to the bags for further growth. Harvests were done in two phases, the second harvest was all market oysters with virtually no mortality. The total harvest count from floating bags was 16,250 oysters.
Experimental Group:
In June of 2022, oysters were retrieved by hand. The bottom planted oysters were planted in a sticky bottom, causing silting and sanding that led to increased mortality. Three bushels of the bottom collected oysters were sampled and the average was 337.6 alive and 71 dead (bushel 1: 303 alive / 52 dead) (bushel 2: 345 alive / 97 dead) (bushel 3: 365 alive / 64 dead). All of the living oysters were extremely uniform and fit the large category. The dead oysters showed no signs of predation, they looked like they died from natural causes or were silted over. The total harvest count from the bottom was 14,600 oysters.
As a part of our marketability tests for the control and experimental oysters, we sent a sample of each to a restaurant owner and oyster sommelier for a blind comparison. Here’s a summary of their feedback:
Biggest differences in feedback were in the interior cleanliness, shell appearance, and meat quality.
When shucked, the control group oysters had a cleaner interior, whereas the experimental group had noticeable traces of mud and silt.
Feedback showed that the experimental oysters were larger, had more variability in shape/meat quality, and a few were slightly dry. The control oysters were smaller, but deeper cupped. The experimental oysters had smaller meats though the texture was overall firmer while control oysters were softer and slightly creamy. As for taste, feedback showed that both oysters were briny and similar in taste.
Both sources of feedback seemed to agree that they strongly prefer the control group oysters due to shell uniformity, cleaner shell interiors, meat content, and mouthfeel.
Both groups required 50 floating bags with lateral lines to be constructed, each taking about 10 minutes to make. 100 floating bags x 10 minutes = about 16 and a half hours. Longlines for the floating bags had to be installed on the farm, bags had to be deployed, and light general maintenance was needed, totaling 40 hours. This had resulted in about 56.5 (16.5 + 40) labor hours total, divided by 2 equaling 28.25 hours for each group.
Both groups used mesh oyster bags, galvanized anchors, line, bag floats, hog rings, round rings, and bungy in the same amounts in Phase 1, totaling $2,319.42 ($1,159.71 for each group).
The differences between the control and experimental group costs are as follows:
Control group: Oysters stayed in bags for the winter, so there was not too much winterization labor besides some light maintenance of the bags ~ 5 hours. When is came time for harvest, it took about 27 minutes to process a bag to separate marketable from dead and submarket oysters, and 6.5 more minutes to process the fully marketable bags after more growth time. Overall labor hours resulted in 32.9 hours.
Experimental group: To winterize the oysters and broadcast on the bottom, it took 15 total hours for 4 farmhands, resulting in 60 hours of labor. Collection of the bottom planted oysters at harvest time took 4 people 150 minutes to fill 13.5 bushels, on average 45 minutes to fill 1 bushel per person. Approximately 43.2 bushels were collected (14,600 oysters divided by 337.6 average alive per bushel), resulting in 32 hours to collect bottom planted oysters. Overall labor hours resulted in 92 hours.
While results show that the control group had more success, a bumper crop of bottom planted oysters could be a good idea. Oyster farming is site specific and labor costs, survivorship and marketability will fluctuate based on conditions.
Education & Outreach Activities and Participation Summary
Participation Summary:
On January 6th 2023, we posted an informational Instagram post to our @fortynorthoysters account, with 8k followers.
This instagram post was informational, included pictures and a description of our project so far. We did not include results of our project in the post, as we are yet to come to a conclusion.
We are in the process creating an informational pamphlet outlining our project and results, planning a NJAA Growers meeting to discuss our project and results (Spring 2023, date still TBD), and a Youtube video of our project and results.
Instagram post:
Learning Outcomes
Amelia, a farmworker who has been helping with the study since the beginning phases, has gained immense knowledge and skills in aquaculture and how research studies are carried out. Amelia has a background in marine science and through this study has been able to not only learn about how to plan and conduct a research project but also gain skills and knowledge in the farming of oysters.
Project Outcomes
One of the greatest challenges that northeast oyster farmers face is the winter. There's increasing data that helps guide decisions but it's unknown what the best solution is. A second challenge is the understanding necessary to properly populate gear. This study helped to realize some core principals that other farmers can benefit from.
One of the challenges we faced was seed availability. We amended the study to use overwintered seed (13 months old) because early season seed was not available. While this amendment is practical, it's not always an option and is certainly an increased cost as older seed costs more. Seed availability remains a focus for our industry and we've seen some small improvements.