Final report for FNE21-986
Project Information
This project used a variety of subtidal oyster growing techniques with the aim of producing distinct varieties of oysters from a single site. Lantern nets, floating tube bags, oyster bags straddled on top of cages, and traditional floating cage culture were used to give oysters differing exposure to depth, wave action, light, and food-sources. Oyster dimensions, appearance, meat quality, and flavor were measured over the course of the growing season.
After four months there was little difference in shell or meat appearance, thought there were differences in size and variability. After a additional 2.5 months, oysters grown in bags straddled on top of oyster bags developed a distinctive smooth shelled appearance and noticeably higher salinity than oysters in other treatments, providing a potential second variety for the farm.
Infographics (included here in the results section) were produced for social media outreach - aimed at an audience of oyster growers. Details of the project were shared with members of the New Meadows River Aquaculture Co-op, of which the PI is a member.
This projects aimed to develop methods for growing multiple distinct oyster products on a single subtidal farm though the use of varied husbandry practices (tube bags, lantern nets, straddled bags, and floating cages).
Objective 1: Utilize varied amounts of wave action/turbation to create oysters with distinctive shell shapes by treatment
Objective 2: Utilize differences in depth to give oysters different food sources and shell coloration
Objective 3: Test marketability of these oysters as new/different products through taste tests, food industry outreach.
Objective 4: Demonstrate ability to farm oysters multiple parts of water column on a subtidal lease (as a potential strategy for increasing yields)
The ideal result of this project this project would give farmers tools to diversify their oyster offerings and gain market access. This information could be useful for new farmers- helping them plan leases and equipment around the ability to grow multiple oyster products.
Small oyster farms typically produce a single product- oysters with a specific flavor and shell shape defined by a farm’s location/environment and growing/handling technique. Though this model has worked well in times of robust demand, market disruptions (such as the huge drop in oyster demand caused by COVID-19) have shown the vulnerability of relying on a single product. Shellfish dealers are only able to buy a limited amount of each oyster variety. Under these stresses, farmers need to diversify in order to gain market access and insure against changes in the market.
Though a single native species of oyster is grown in the Northeast (Crassostrea virginica), some large farms have diversified their oyster offerings by holding multiple aquaculture leases in geographically distinct sites. Other farms take advantage of a very specific bathymetry that allows for oysters to be grown on the surface and on the bottom (requiring a protected shallow water lease with a firm bottom substrate). Though these approaches allow farms to produce multiple distinct varieties, both have social and environmental drawbacks. Large multi-site farms can displace or disrupt wildlife and can conflict with other users of the marine commons. Cost and regulatory barriers can make small multi-site farms impractical. Dredge-harvesting of bottom-culture has a harmful and long-lasting effect on benthic ecosystems, and diving for oysters is an expensive endeavor.
There are techniques available that could help small farms diversify by using a variety of gear types, handling techniques, and different portions of the water column on a single site. This project tested four distinct growth and handling techniques to attempt to develop distinctive oyster varieties from a single seed-source on a small subtidal oyster farm in southern Maine. These techniques aimed to take advantage of differing degrees of wave action and exposure to light to shape and color shells, and different food sources to flavor oyster-meats.
• Traditional floating cage culture (control)
◦ High density, near surface, medium degree of tumbling
• “Straddled” bags installed on top of floating cages
◦ Low density, at surface, very high degree of tumbling
• Floating tube-type oyster bags
◦ Low density, near surface, high degree of tumbling
• Lantern nets
◦ High density, deep below surface, negligible tumbling
Beyond the goal of product diversification and market access, this work also indirectly measured the viability of techniques that could help farmers increase their yields by utilizing more of the water column, and provided information that could help farmers remediate irregular oysters.
I am the owner of Winnegance Oyster Farm, located on the New Meadows River in southern Maine. The farm is in its eighth year of operation. I began harvesting in September of 2015 and switched from part-time to full-time work at that point.
My farm is comprised of four limited-purpose aquaculture licenses (LPAs) encompassing a 1600 sqft footprint. In 2021 my farm produced 60,000 oysters (down from 71,000 in 2019). This decrease was related to overcrowding-mortality caused by greatly reduced sales during 2020 COVID restaurant closures. In 2021, the majority of my oysters were sold to seafood wholesalers, though I have operated a farm-share and sold directly to restaurants in the past.
My background is in environmental biology, and I have also worked in horticulture and the seafood industry. I've received SARE farmer grants in past years: building tide-powered equipment to clean and tumble oysters, studying polyculture of littleneck clams and eastern oysters, and using shading to prevent algal biofouling. I’ve also worked on other grants as a co-PI, consultant, and as a participating farmer. This work has further explored polyculture (both oyster/quahog and urchin/kelp), and promoted small/family oyster farms through shared marketing and the creation of distinct oyster “growing-regions”.
Cooperators
- - Technical Advisor
Research
Oyster Grow-out
In June of 2021, oyster seed planted in June 2020 was measured (length, width, depth) to establish baseline dimensional data. As a note: This cohort was grown during pandemic restaurant shutdowns/slowdowns- while the farm held much more inventory then in a typical season. As a result, this seed was crowded in nursery bags and much less regular that normal. After initial measurements were taken, 1500 individuals were deployed in each treatment for growout. Treatments included:
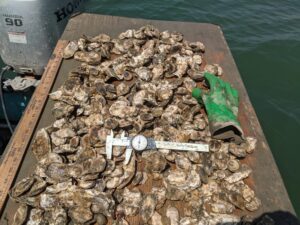
Lantern nets:
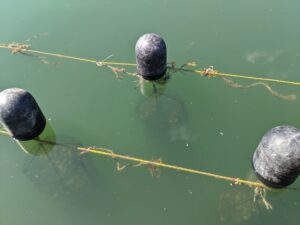
Oysters deployed in lantern nets sat at 4 to 7 feet below the surface. At this depth there was negligible tumbling due to wave action and far less light than other treatments. Lantern nets allowed for a high stocking density and experienced a high degree of tidal flow in the middle portion of the water column.
Tube Bags
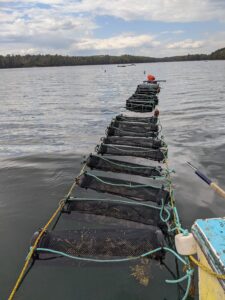
Oysters deployed in tube bags sat roughly 5 inches below the surface. These cages are designed to slowly spin or tumble with exposure to wave or wake action. These cages are small and designed for a relatively low density of oysters. Their relative lightness allows for a high degree of tumbling with wave action.
Oyster bags straddled on top of oyster cages
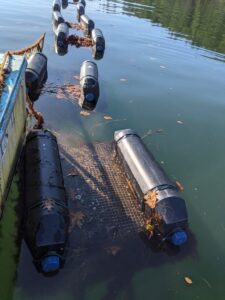
Oysters deployed in straddled bags sat just below the surface. The inertia of heavy cages held these bags comparatively still, allowing waves to directly hit and tumble oysters. This technique had the highest degree of tumbling and most exposure to light.
Floating oyster cages (control)
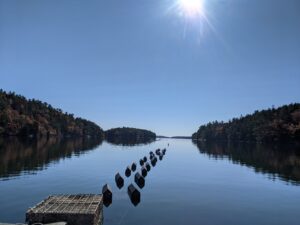
A control treatment consisted of the floating-cage grown oysters traditionally marketed by Winnegance Oyster Farm. Compared to other treatments, this technique allows for a high stocking density with a medium degree of tumbling (caused by handling instead of wave action). Oysters sat 3 to 8 inches below surface and were manually air dried several times over the course of the season (timed to the appearance of fouling-pests).
Measurements:
Shell dimensions (length/width/depth of 50 individuals in each treatment) were measured in September. Market-size oysters (3”+ shell length) were recorded to test the efficiency of each treatment (Objective 4) and were removed from the growth trial (to avoid skewing data with individuals that would not be present under normal farming conditions). Photographs were taken to record shell shape and color. A second set of measurements were taken in early December.
Taste-Tests:
Market sized oysters from each treatment were shucked for a qualitative description of meat quality and flavor by the P.I. in October and December. Food industry taste tests initially were postponed due to fall harvest closures (excessive rain) and then winter restaurant closures (COVID, holidays). A cold snap early in 2022 froze the bay, causing the loss of the 400 oysters set aside for industry taste tests
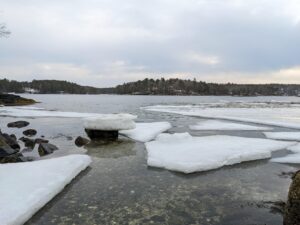
Growth
In September measurements, straddled bags and tubes had growth rates that were comparable the cage-grown control (within standard error). Oysters grown in straddled-bags were the least variable of all treatments. Oysters grown in lantern nets were on average much smaller than the other three treatments, and were also highly variable (with the largest observed individual coming from this treatment). See accompanying table, graphs, and graphic below.
Treatment (Sept) | Average - Length | Average - Width | Average - Depth |
Cage | 82 | 57 | 20 |
Straddle | 83 | 56 | 20 |
Tube | 82 | 55 | 19 |
Lantern | 73 | 47 | 16 |
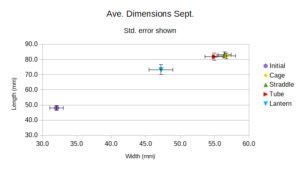
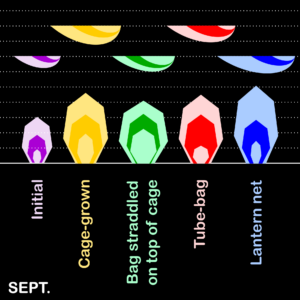
In December measurements, Tube grown oysters were the largest overall by length and width, though similar to straddled oysters in depth. Cage-grown and straddled oysters were in indistinguishable by length and width. Straddled oysters had deeper cups than cage grown oysters. Lantern net oysters were again highly variable, but on average much smaller than other treatments in all dimensions
Treatment (Dec) | Average - Length | Average - Width | Average - Depth |
Cage | 74 | 51 | 18 |
Straddle | 75 | 50 | 20 |
Tube | 84 | 55 | 20 |
Lantern | 68 | 45 | 15 |
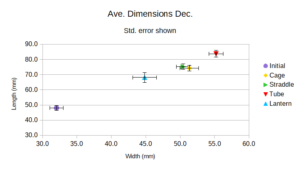
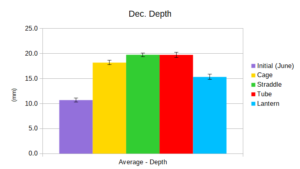
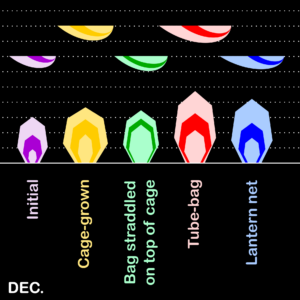
Size distribution
September
December
Time to market
Oysters at Winnegance Oyster farm take an average of 18 months to reach a harvestable size (3 inch shell length), though there is some variability between years/seed cohorts. The seed for this project was planted in late June of 2020 and estimated to be ~50% at harvestable size by December 2022.
Time to market was measured in two ways- the first was to strictly look at shell length. By this measure, all treatments exceeded expectations, with tube bags reaching 93% harvestable by December, Straddled bags 83%, cages 78%, and lantern nets 54%. Though growth across the farm was faster than typical in 2022, these figures overstate harvestability.
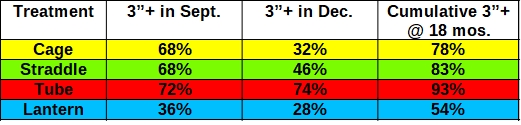
A more subjective measure was taken in September- where the percentage of oysters visually ready to harvest was tallied. This took into account width, depth, and appearance- reflecting how picking/culling of product works in practicality.
Mortality
In a typical year at Winnegance Oyster Farm roughly 3 to 5% of the crop is lost before reaching a harvestable size- with the most loss occurring over the winter. Higher mortality was observed across the farm in 2021. Oysters in experimental treatments saw higher mortality than oysters grown in cages. During warmer months, lantern nets saw very high mortality with 8% of oysters perishing between June and late September. Three percent of oysters in both tubes and straddled-bags were lost over the same time period (compared to 1% of oysters in cages). In the colder months of the growing season, both tubes (6%) and lanterns (6.7%) saw much higher mortality than straddled bags (3.3%) and cages (1.2%).
Causes of mortality were not clearly apparent. The extra turbation/tumbling seen in tubes and straddled bags was expected to cause some mortality, but fouling may have been a contributing factor as well- particularly in lantern nets. 2021 marked the second year of unusually high fouling that did not follow prior patterns seen from 2014-2019. Unlike those years, where tunicate and sea vase fouling occurred in a single wave starting in late July and continuing through Aug, the last two seasons saw multiple “sets” of tunicates from July into October. Colonial tunicates were observed on in all treatments- with the fewest seen on straddled bags. Weather conditions may have also played a part in mortality- with fall storms that brought a massive influx of fresh water. A single storm dropped 7.5inches of rain on the farm in late September, dropping local surface salinity to 11ppt (compared to a typical reading of 33ppt). This storm was followed by another 4.5 inches two weeks later. Though no mass mortality events were recorded, the salinity shock may have weakened oysters, or changed the composition or quantity of food sources.
Appearance
September
Though size/consistency varied greatly between treatments in September observations, it was difficult if not impossible to differentiate between most treatments by shell appearance. Oysters grown in cages, straddled bags, and tubes had similar shapes, shell textures, and coloration.
Lantern net oysters had more irregular shell shapes (narrow, convex hinges, twisted looking shells) and whiter shells, and had a rougher shell texture. Though some of the fastest growing individuals were found in lantern nets, a large portion of oysters would be unmarketable to traditional half-shell dealers.
Meats across treatments had a similar appearances that was typical for a crop of at that age. Tube grown oysters were slightly plumper than other treatments.
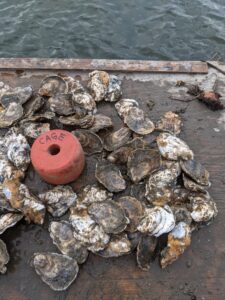
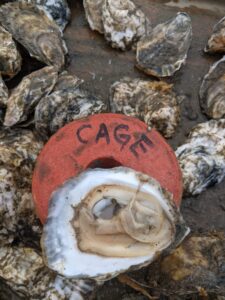
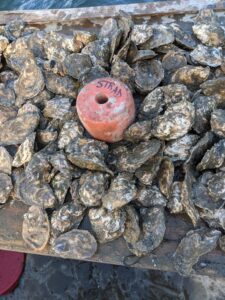

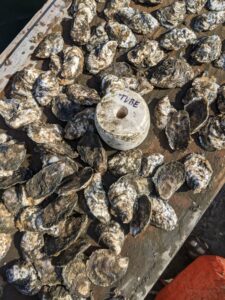
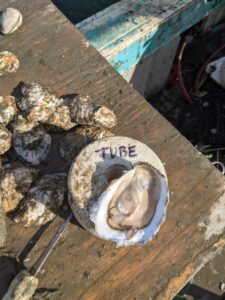
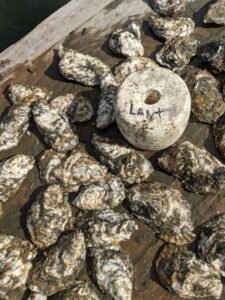
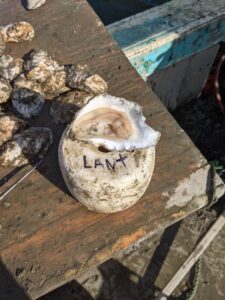
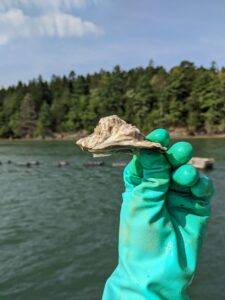
December
In December qualitative differences between oysters were much more substantial.
Oysters grown in straddled bags had a very uniform shape. They looked very different than oysters in the other treatments with smooth, worn, white, polished looking shells that looked much older than 18 months. Shells were extremely hard and lacked ridges or sharp edges. This characteristic shell texture was the strongest marketable visual differentiating trait in this experiment.
Tube-grown oysters had pleasing deep-cupped shells, though more colorful (variegated) and much less "worn" looking than straddled oysters. They resembled control oysters closely enough to make them hard to differentiate, though tube grown oysters were on-average bigger.
Lantern-net-grown oysters resembled wild reef oysters more than any of the other treatments, with sizes and shapes that were highly variable. Lantern net oysters were very inconsistent, often either too shallow or too narrow to be saleable.
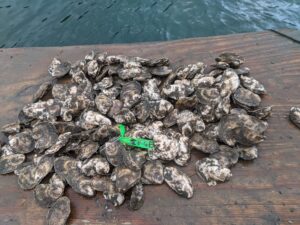
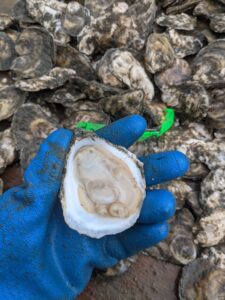
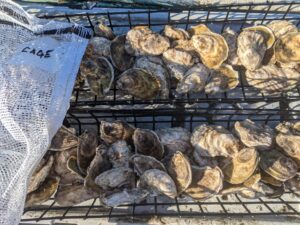
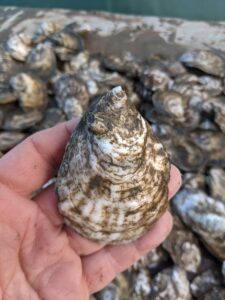
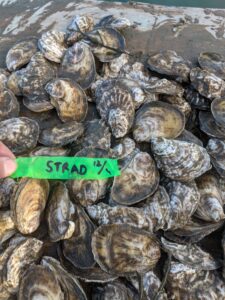
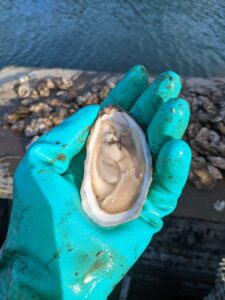
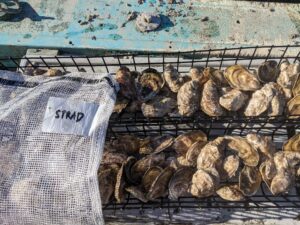
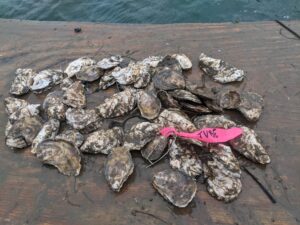
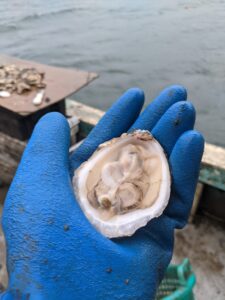
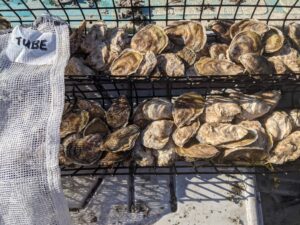
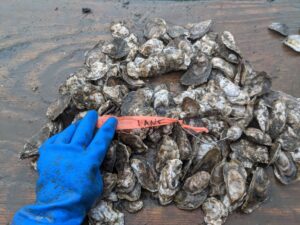
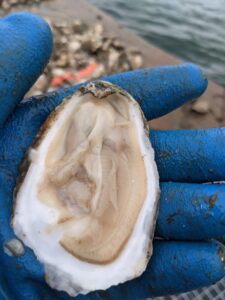
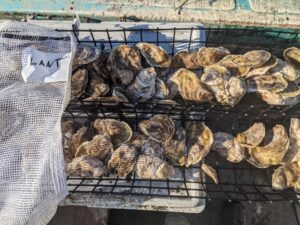
Meat quality & Flavor
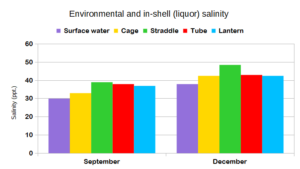
In December taste tests, Tube-bag oysters had the largest shells and plumpest, firmest meats in the study. Taste was not discernable from our normal cage-grown oysters in the control treatment- characterized as medium brine, mildly sweet, slightly seaweed-y, with a strong savory/meaty finish. Cage grown oysters were the second plumpest treatment.
Straddled-bag oysters had slightly smaller (but still plump) meats that were bracingly briny. There was still a savory finish, but the main note was "refreshing brine". These were by far the most easy to distinguish of the treatments. There was not the "sweet" tasting note seen in other treatments. Average in-shell salinity was the highest and very noticeable in meats (even if "liquor" was discarded).
Lantern net oysters had thinner, more tender meats, though taste was quite good- very slightly sweeter and more savory/broth-y than the other treatments.
In September taste tests, differences were much less pronounced. Salinity variation was measurable, but much less noticeable on the tongue. The most prominent difference was that lantern net oysters were slightly sweeter than other treatments, though in my opinion not different enough to market as a separate product. At this point in the experiment, oysters had spent less time in equipment and were potentially still diverging.
This project aimed to use experimental equipment and techniques to produce oysters that were different in taste and appearance from the standard oysters grown on my farm. One experimental treatment achieved this aim: straddled bags. Over the course of the fall, straddled bags produced oysters with smooth, hard, thick-walled shells that were much brinier than my typical crop (though this effect was not seen earlier in the season). These oysters could provide an additional marketable product during these months that could expand overall demand.
The production of this alternate product did had a cost- additional mortality. Though relatively low (~3%), it was still much higher than observed in the control (~1%). There was very little labor or energy associated with adopting this technique, and fully utilizing the tops of oyster cages would increase my farm's capacity by 25%.
There was far less divergence in the shape (Objective 1) and color (Objective 2) of oysters than I expected- with the major visual differences coming from shell texture and thickness. Lantern net oysters skewed whiter/lighter than other treatments earlier in the season- but this was not a consistent effect. The three additional treatments had a similar coloration to each other through September measurements, after which the straddled oysters diverged. As the fall worn on, straddled shells became lighter through wear and erosion, but did not develop the greenish hue I’d seen in any informal proof of concept test I conducted the prior season.
Though tube-bags and lantern nets didn't meet Objectives 1 and 2 for visual differentiation , they did show that different equipment and portions of the water column could provided additional space to grow oysters (Objective 4). Results from the tube bag treatment suggest that they may have a use for producing fast growing oysters late in the season, as growth is slowing down across the farm.
Education & Outreach Activities and Participation Summary
Participation Summary:
A project overview was presented to the New Meadows River Shellfish Co-op in a monthly meeting, and other local farmers in informal personal communication. A detailed project description was given to 3 agricultural service providers (from non-profits), and 4 farm visitors.
As of 3/28/2022 on social media social media outreach (Instagram and Facebook) was interacted with by 1979 accounts and (was liked/commented on by 251 users). Of these interactions 90 went on to seek more information from my website. Seven farmers contacted me directly with questions about the project (primarily focused on gear and rigging). Farmers, seafood dealers, retailers, and restaurants make up more than 1/3 of accounts engaged (these numbers were not added to the "farmers participated figure"). Social media outreach will continue- directing viewers to the final report. Graphics for social media outreach were based on photos included in Methods section.
Formal tours and talks were not conducted due to COVID 19 safety precautions.
Learning Outcomes
16 Farmers requested information on gear design and technique- suggesting they may try to experiment on their own farms
11 Farmers in the New Meadow River Shellfish Co-op requested details on the project during a monthly co-op meeting (PI is a member) [Brunswick, Harpswell, Phippsburg, West Bath, ME]. Of these farmers 4 requested more information on tube bags (source, rigging) along with 2 additional farms [Phippsburg, ME & Wellfleet, MA]. Three of the co-op farmers requested more info about straddled bags, along with one additional farmer [Stevensville, MD.
Two farmers requested additional information about lantern nets (how they were used/results). [Deer Isle & Yarmouth, ME]
Project Outcomes
Findings from this work (both direct and indirect) will change practices on my farm in a number of ways.
I intend on using straddled bags to produce a separate late season variety of oysters on my farm, marketed as a seasonal, premium product.
Using the straddle space between the pontoons of my oyster cages will increase the carrying capacity of my farm. I will cautiously test this to see if I can increase my seed order in future seasons.
Straddling bags could have other shorter term uses on my farm- for instance temporarily straddling bags to thicken shells - a replacement for tumbling oysters that lacks the substantial labor/energy inputs that are traditionally involved in the process (an environmental and quality of life improvement).
Tubes-bags also showed utility-driving late-season growth.
Outreach did seem to drive change on other farms- seen by inquiries about gear (most commonly) and techniques.
If repeating this experiment, there are a number of changes or additions I would make.
I would like to see if these treatments would produce similar results with less variable seed-oysters. The seed used in this experiment was far less regular than typically handled on my farm. Using irregular seed showed the potential for high-tumbling treatments (straddle-bags and tubes) to remediate shell shape, but may have put lantern nets at a disadvantage. Seed that was initially more consistent could potentially grown more evenly in lantern nets.
It would also be interesting to try this work with multiple lineages of seed, to see the role of genetics in shell appearance/reaction to disturbance/tumbling, and at multiple sites.
Conducting the experiment over multiple seasons could also be illuminating- and could better account for the wildly fluctuating weather (early season drought, abundance of late season rain, early heavy freeze).
In terms of equipment, I would be interested in seeing if tubes with greater floatation produced a more highly tumbled oyster. In a previous SARE project (FNE16-848- Using tidal energy to clean and tumble oysters) homemade tube cages with larger floats produced very narrow shelled oysters- visibly different from the oysters I grew in this project.
Most importantly, I would would like to run this experiment in conditions that would allow for an industry taste test (without the extreme rain events, COVID closures and the bay freezing over). Though I am an experienced taster- having worked in gourmet foods (cheese and wine), it would have been ideal to have many more people involved.
I believe small-scale shellfish farmers will benefit most from this work. Small farms have the most incentive to utilize a greater proportion of their farm footprints, both for yield and the ability to offer multiple products in the fall without having to farm a larger area.