Final report for FNE22-017
Project Information
This project aimed to test whether 3D printed and computer routed materials are able to withstand the harshness of the marine environment and the rigors of farming. Though the end goal was to enable the fabrication of prototypes/new designs, this project tested a standard piece of equipment to separate the suitability of materials from the strengths/weaknesses of new designs
Professional fabricators attempted to replicate commercial oyster growout bags using extrusive 3D printing, laser cutting, and CNC routing. Of these techniques, only CNC routing produced viable bags. Bags made of three different materials were tested: high density polyethylene (HDPE), very-high molecular weight polyethylene (VHMW), and polyethylene terephthalate glycol (PETG).
Bags were deployed with on a commercial oyster farm and on an educational aquaculture lease and were checked for damage and fouling from June of 2022 until June of 2023.
Bags constructed from VHMW saw the least damage of the materials tested- averaging 1 instance of damage per bag compared to 1.6 instances of damage per bag for HDPE and 3.4 instances of damage per bag for PETG. None of the VHMW had a structural failure compared to 13% of HDPE bags and 43% of PETG bags.
The fabrication techniques used in this project were both time consuming and expensive for objects of this scale. Though there is promise for custom fabrication of aquaculture equipment using CNC routing and 3d printing, it does not seem practical (even for prototypes) until the technology advances.
Outreach efforts included farm tours at our partner institution (focusing on students and educators), presentation to an aquaculture co-op, and social media outreach to farmers, 3D printing enthusiasts, and seafood lovers.
This project aims to test whether 3D printed materials are able to withstand the harshness of the marine environment and the rigors of farming. Though the end goal is to enable the fabrication of prototypes/new designs, this project will test a standard piece of equipment to separate the suitability of materials from the strengths/weaknesses of new designs
Objective 1) Design/replicate oyster bags in four materials and 2 mesh sizes at Haystack Mountain School of Crafts Fabrication Lab, and at Hurricane Island Center for Science and Leadership (facilities with different fabrication capabilities)
Objective 2) Deploy bags on two field test sites- Winnegance Oyster Farm in West Bath, ME -a commercial oyster farm, and Hurricane island school- an experimental/demonstration farm that is part of a sustainability-focused non-profit and grow oysters for one season, with monthly inspection and photographs of wear, damage, and fouling organisms
Objective 3) Quantify wear through scope photography at end of season
Objective 4) Share results with farmers and educators in the region- with the hope that our materials test will aid innovative farmers as they create new varieties of aquaculture equipment.
Despite the variety of seafarms farms in the Northeast, there is a dearth of diversity in oyster farming equipment. Farms in the region vary in size from millions of oysters to tiny hobby farms, they are situated in the open ocean, enclosed salt ponds and everywhere in between, tides in the region range from 3 feet to over 20 feet. Farmers work out of enormous barges, the smallest of skiffs, or just hip waders.
Even with this wide spectrum of farms, farmers are limited to variations of just a few types of regionally available commercial equipment (slight variations of cages and bags), produced by a small handful of manufacturers. The slightly larger selection offered by international sellers usually requires ordering equipment by the shipping container, sight unseen, with unsure delivery dates (even before the current supply chain disruptions).
There is clearly a need for a means to design and test new oyster farming equipment that is adapted to local conditions- to find gear that is less physically demanding to work with, requires less labor and energy to keep clean, and promotes faster growth and/or a more desirable product for consumers.
3D Printing could allow farmers to design and test equipment that is better suited to their local environment, growing conditions, farm infrastructure, work style, and physical limitations.
The first step in this process is testing the materials that can be used by commercially available 3D printers and CNC routers. In this experiment, we have replicated a ubiquitous piece of oyster farming equipment (rigid mesh grow-out bags) to see how they hold up to the rigors of farming over the course of a season. By replicating oyster bags, we hope to decouple the effects of material viability from the potential fragility of new designs (with the intent of narrowing down materials suitable for testing of new designs in the future).
I am the owner of Winnegance Oyster Farm, located on the New Meadows River in southern Maine. The farm is in its ninth year of operation. I began harvesting in September of 2015 and switched from part-time to full-time work at that point.
My farm is comprised of four limited-purpose aquaculture licenses (LPAs) encompassing a 1600 sqft footprint. The farm produces up to 71,000 oysters a year. The majority of my oysters are sold to seafood wholesalers, though I have operated a farm-share and sold directly to restaurants in the past.
My background is in environmental biology, and I have also worked in horticulture and the seafood industry. I've received SARE farmer grants in past years: building tide-powered equipment to clean and tumble oysters, studying polyculture of littleneck clams and eastern oysters, using shading to prevent algal biofouling, and product differentiation of oysters on my farm. I’ve also worked on other grants as a co-PI, consultant, and as a participating farmer. This work has further explored polyculture (both oyster/quahog and urchin/kelp), and promoted small/family oyster farms through shared marketing & the creation of distinct oyster “growing-regions”. I am currently working on a SARE farmer grant testing bay scallops as a crop diversification strategy in warming Gulf of Maine.
Cooperators
- - Technical Advisor (Educator and Researcher)
- (Educator and Researcher)
- (Educator and Researcher)
- (Educator)
- (Researcher)
Research
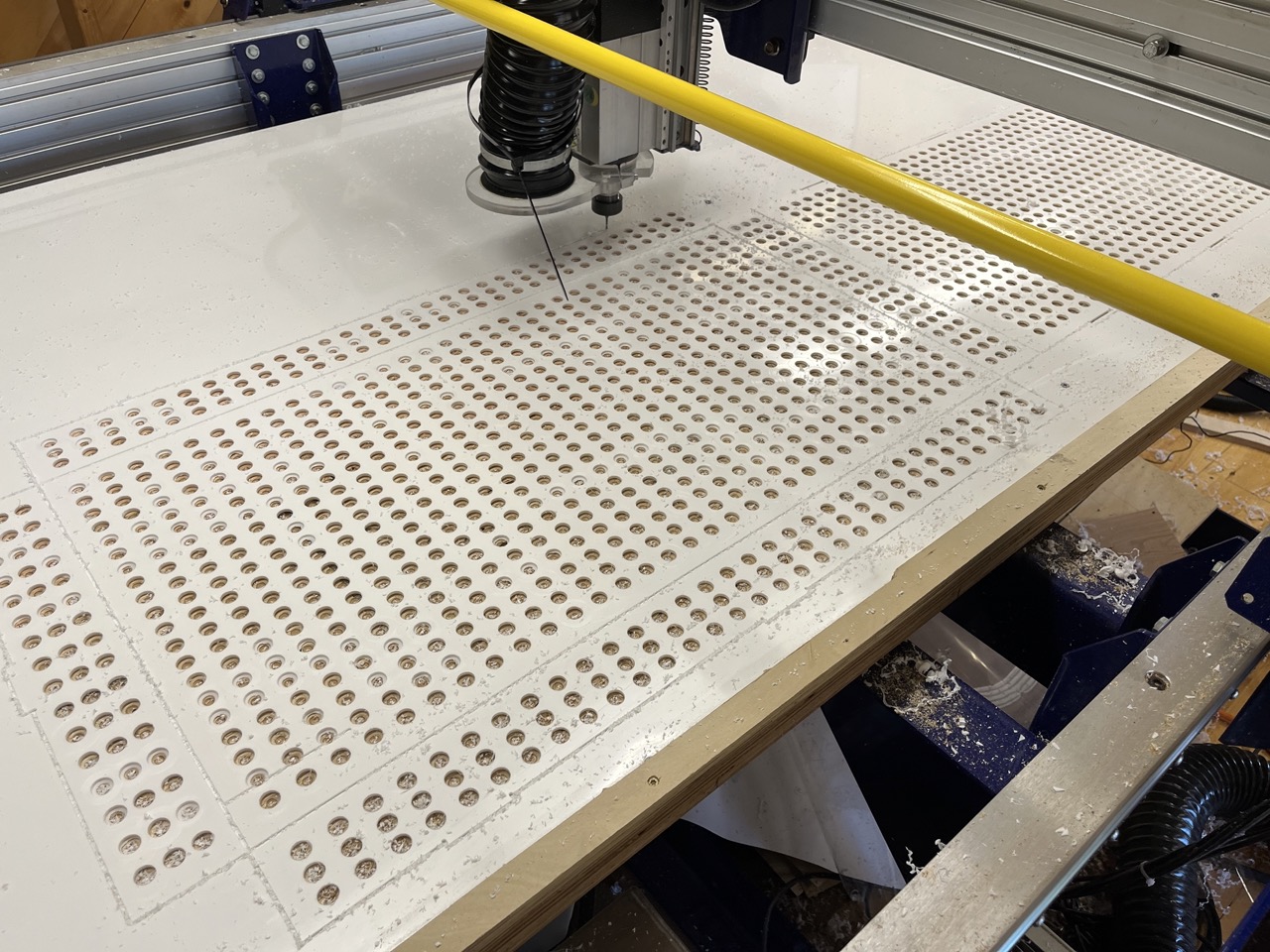
Material Selection/Design
The rigid-mesh oyster growout bags produced in this experiment were contract-built by experienced 3D fabricators: James Rutter of the Fabrication Lab at the Haystack Mountain School of Craft, and John Van Dis, of the Hurricane Island Center for Science and Leadership. Fabrication methods attempted during initial material trials included using small-format 3d printers, plastic welding pens, a computerized laser cutter, and a large-bed CNC router.
Originally, we sought to test four types of materials- three extruded: ABS (Acrylonitrile butadiene styrene ), PLA flex (flexible variant biopolymer polylactic acid), and Nylon, and one CNC routed: UHMW sheeting (Ultra High Molecular Weight polyethylene). After bag design, initial materials tests, and printing-calculations informed by these tests, it became clear that the extruded (printed) plastics would not be feasible in our timeframe and budget. Our focus was shifted to materials that could be cut with a CNC router or laser cutter. Supply chain disruptions eliminated our initial choice of sheeting-UHMW. In place of the initial materials, we chose three types of plastic sheeting; high density polyethylene (HDPE), very-high molecular weight polyethylene (VHMW), and polyethylene terephthalate glycol (PETG) for testing. These materials were picked for their safe use in food applications, durability in outdoor use, compatibility with our tools, and availability during a time of supply disruptions.
- HDPE is widely used in aquaculture applications- including the rigid-mesh oyster bags we replicated. It was chosen to test the durability of our construction techniques with a proven material.
- VHMW is similar to HDPE, but is comprised of longer hydrocarbon chains. it is denser, more rigid, and has a smoother surface that we hoped would inhibit invertebrate fouling. We chose a white variant (some fouling species preferentially adhere to darker surfaces).
- PETG was chosen for its ubiquity, easy recyclability (it is the material that soda bottles are made from), and the observed durability of discarded PETG in marine environments.
Filaments tested during material trials:
-eSUN Natural Nylon Filament - 1.75mm
-White PRO Series Nylon Filament - 1.75mm
-Taulman Nylon 230 Natural 3D Printing Filament
-Clear PRO Series Ryno Filament
Sheeting used in fabrication:
-Impact- and Moisture-Resistant HDPE - 1/8" thickness, $91.72/4ft x 8ft sheet
-Weather-Resistant VHMW Polyethylene - 1/8" thickness, $112.70/4ft x 8ft sheet
-Clear Easy-to-Form PETG - 3/32" thickness*, $118.56/4ft x 8ft sheet
*Thinner sheets of PETG were used by fabricators due to the material being more brittle and less flexible when thicker.
Fabrication
All but one of the bags built for this project were fabricated at the Haystack Mountain School of Craft using a ShopBot Alpha 96, a 96”x48” CNC milling machine (essentially a computer controlled router on a robotic arm). This machine can be equipped with drill bits or smaller cutting tools (end mills). Both types of tools were tested during the fabrication process.
- 14mm Drill Bit – Used only on the first fabrication attempt: A 14mm drill bit was used to bore out holes in the sheeting. This generated large plastic chips that were too big for the dust collector.
- 4mm End Mill – For cutting holes and grooves in the plastic sheeting. This tool has a downward cutting force (down-cut) to help keep the sheeting pressed against the table during machining and a single-flute to help with plastic chip clearance.
- ⅛” End Mill — For cutting the slots in closure tabs to fit the material thickness (⅛”).
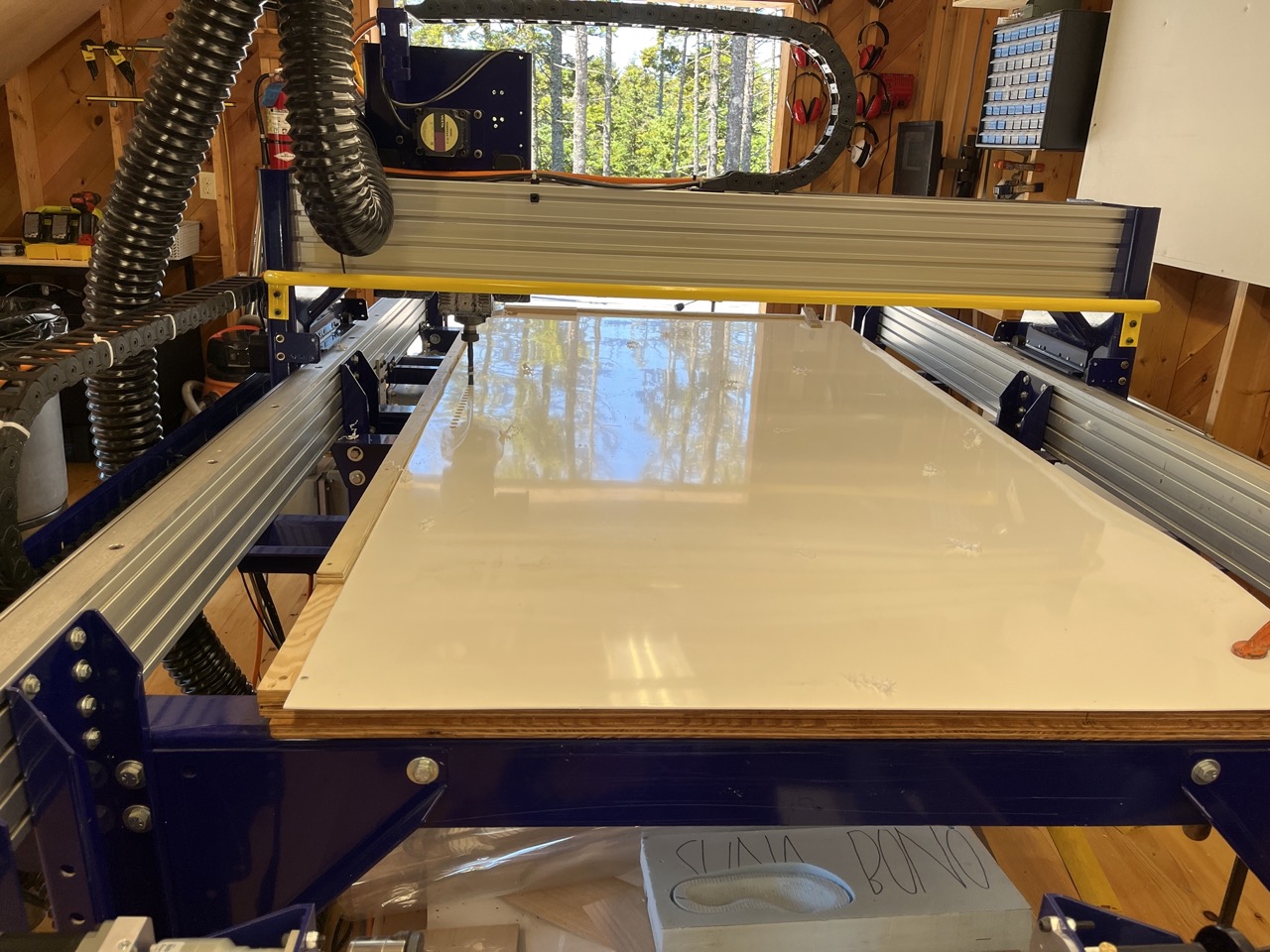
Plastic sheets were drilled into a sacrificial layer (plywood) to keep them in place on the CNC router's bed and to allow the cutting tools to fully pierce the material. This method did still allow for some warping, which prevented the milling bits from fully cutting through the plastic in some places (a problem that could be mitigated through the use of a vacuum-table- which was not available to us).
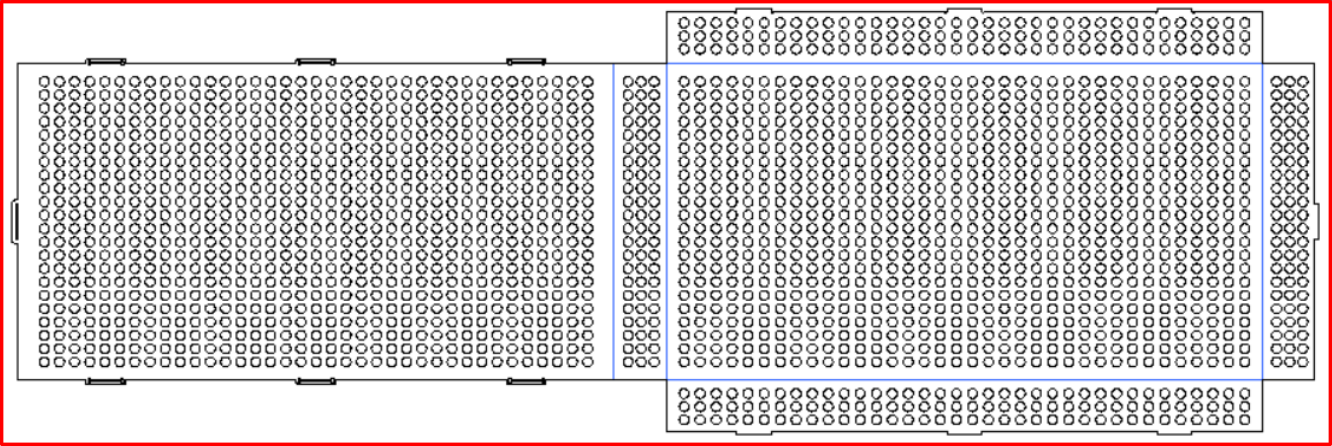
The router cut holes into the plastic to construct the "mesh" of the oyster bag. It then cut grooves/score-lines into the plastic sheeting that were used to fold the sheet into a box. "Tabs" with slots and "tongues" were cut on outside edges- and were used to fasten the box edges together.
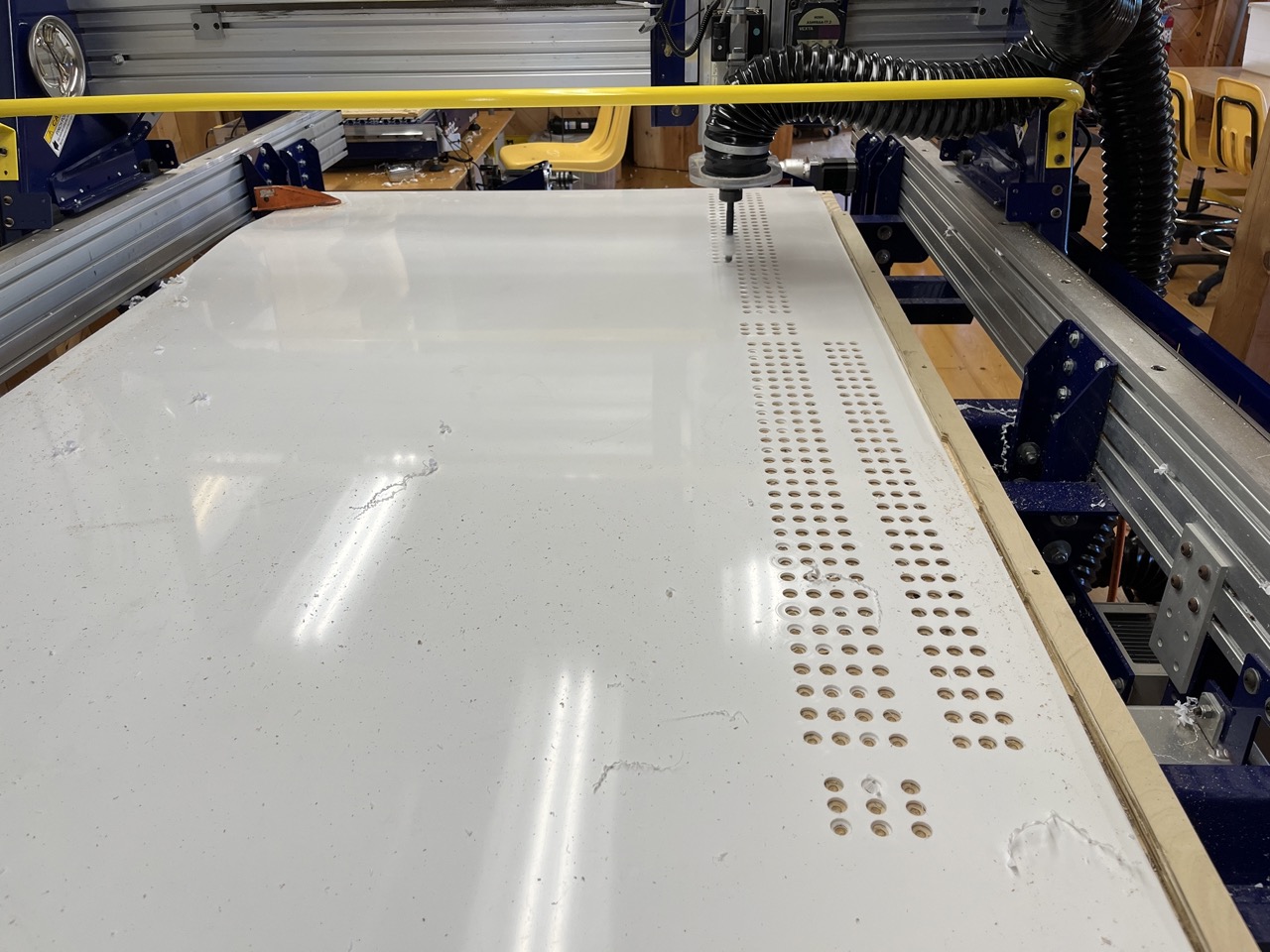
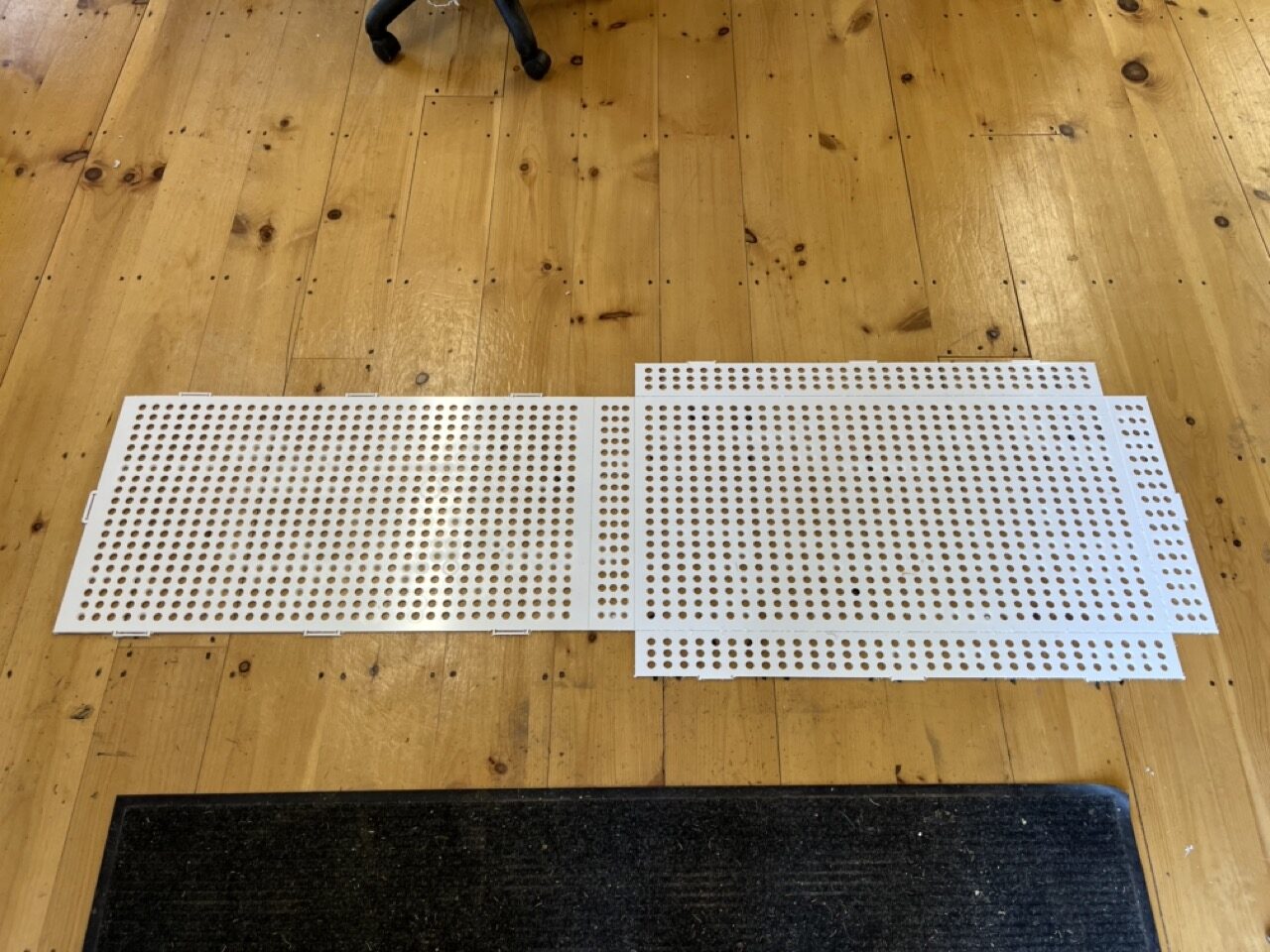
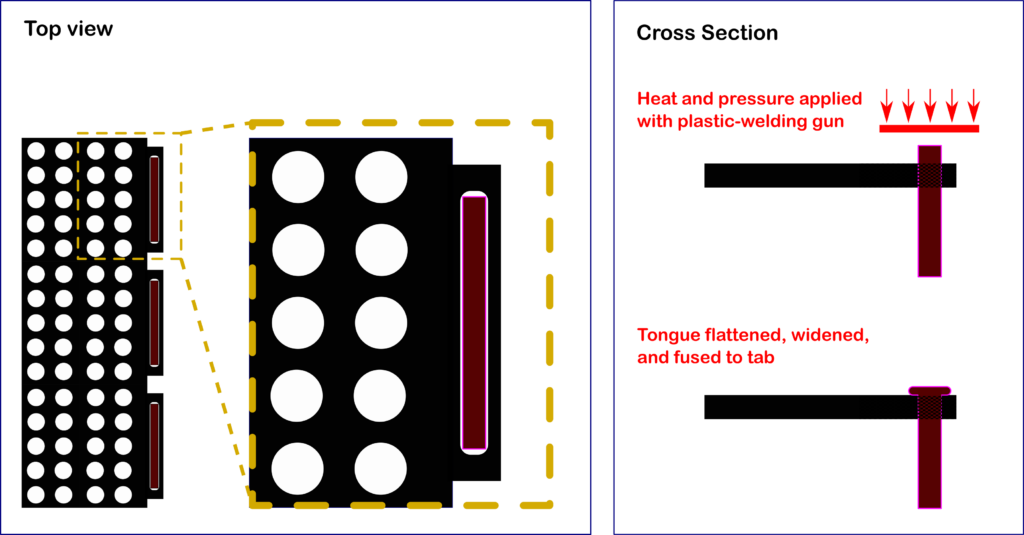
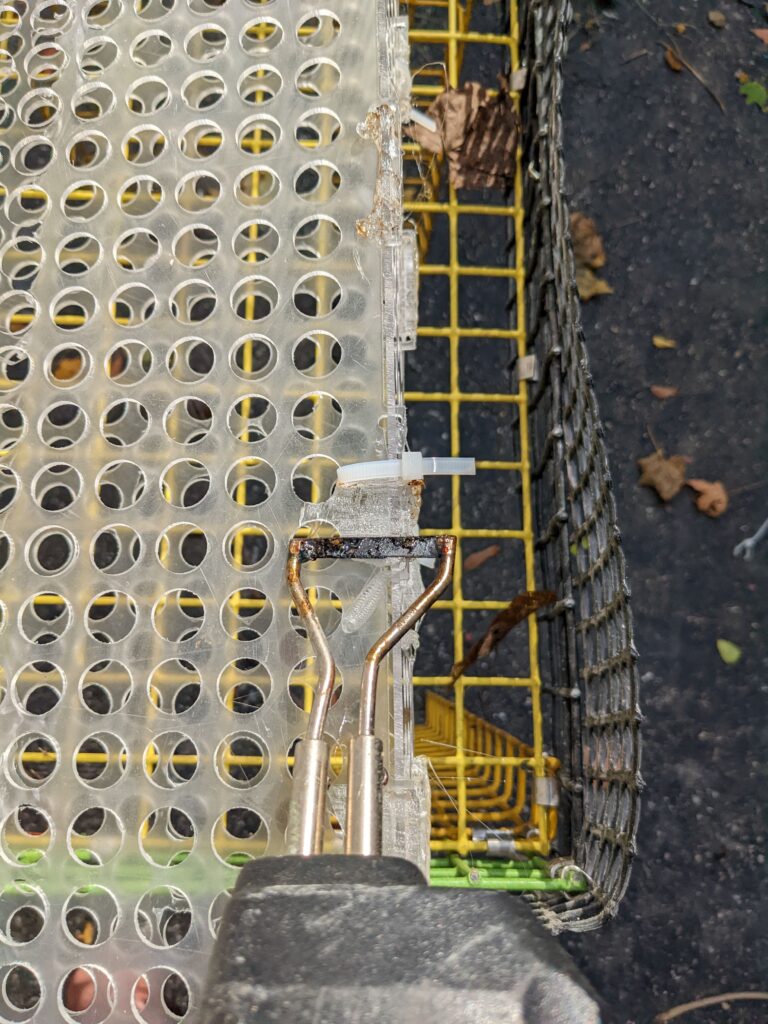
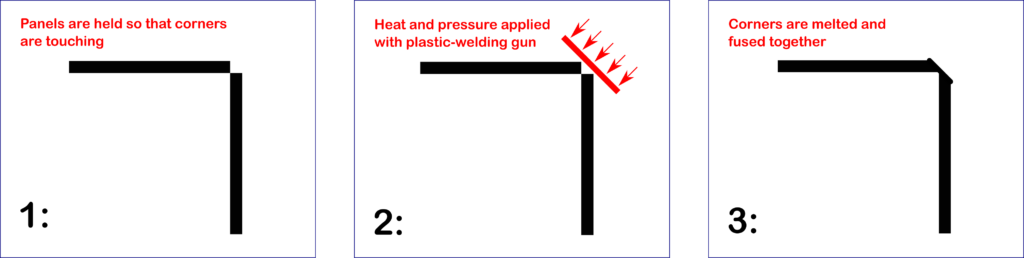
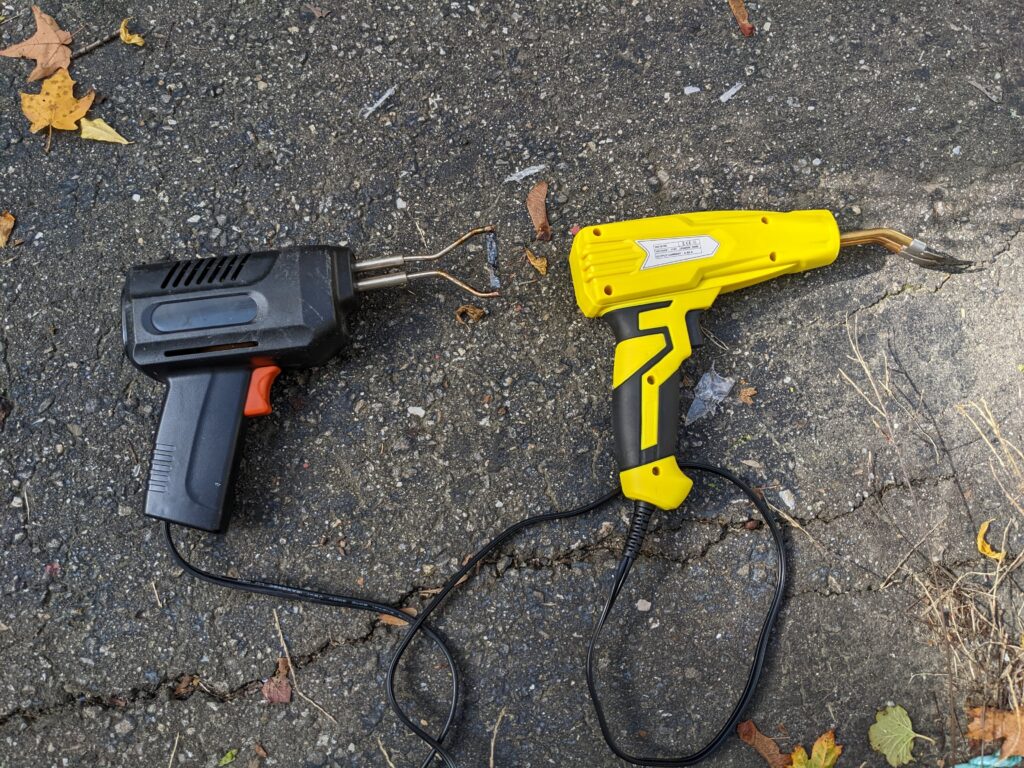
Field Trial:
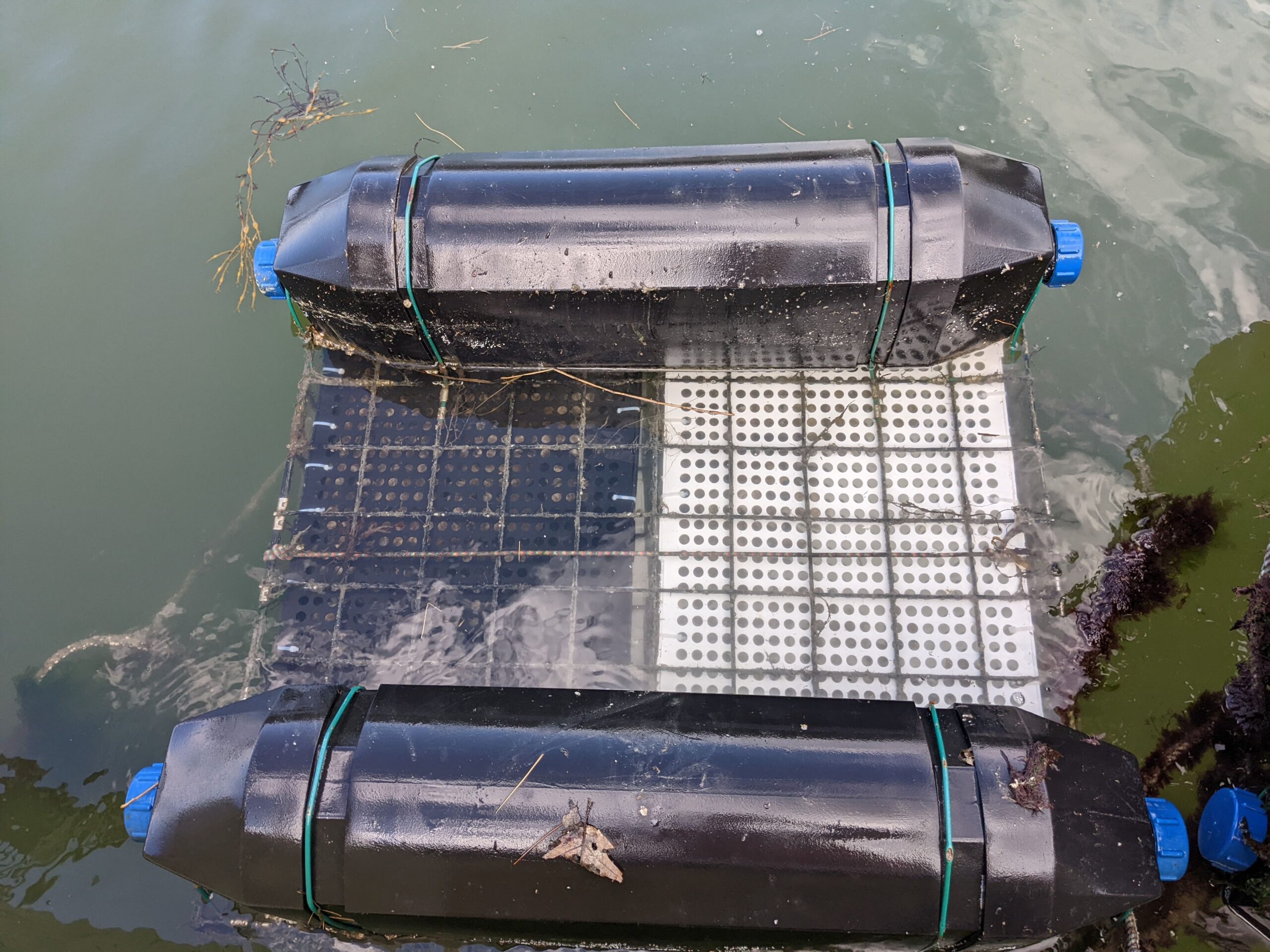
In June of 2022, the first 3D printed bags were deployed at both farms. Prototypes were finished in several waves, with the last bags deployed in early October of 2022. Bags at Winnegance Oyster Farm were situated in floating oyster cages, while bags at Hurricane Island’s experimental farm were outfitted with floats (covering the two most common types of oyster farming in the northeast -floating cage farms and floating bag farms). These bags handled twice monthly from June to November of 2022- once for maintenance handling (air-drying, culling, thinning, manual-cleaning, etc.) and a second handling for inspection, measurements, and photographic documentation. Measurements resumed in May and June 2023 for this project's extension. Field work at Winnegance was conducted by Jordan Kramer (P.I.), while work at Hurricane Island was conducted by Phoebe Jekielek (H.I.'s lead scientist) and Madison Maier (Aquaculture Manager).

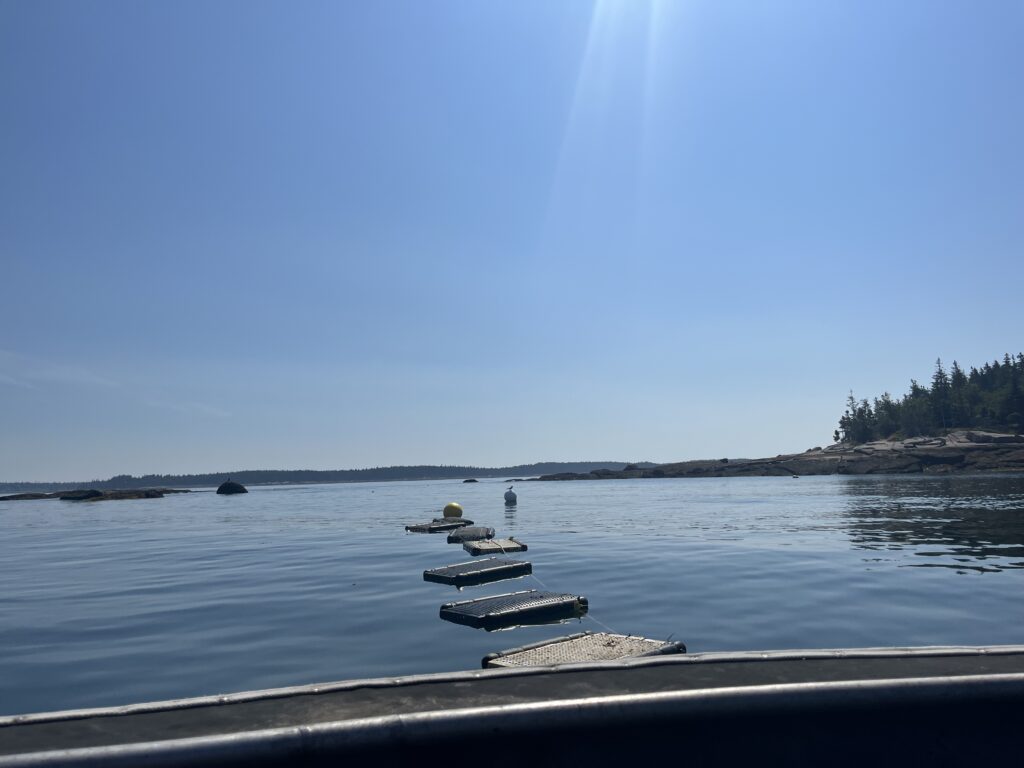
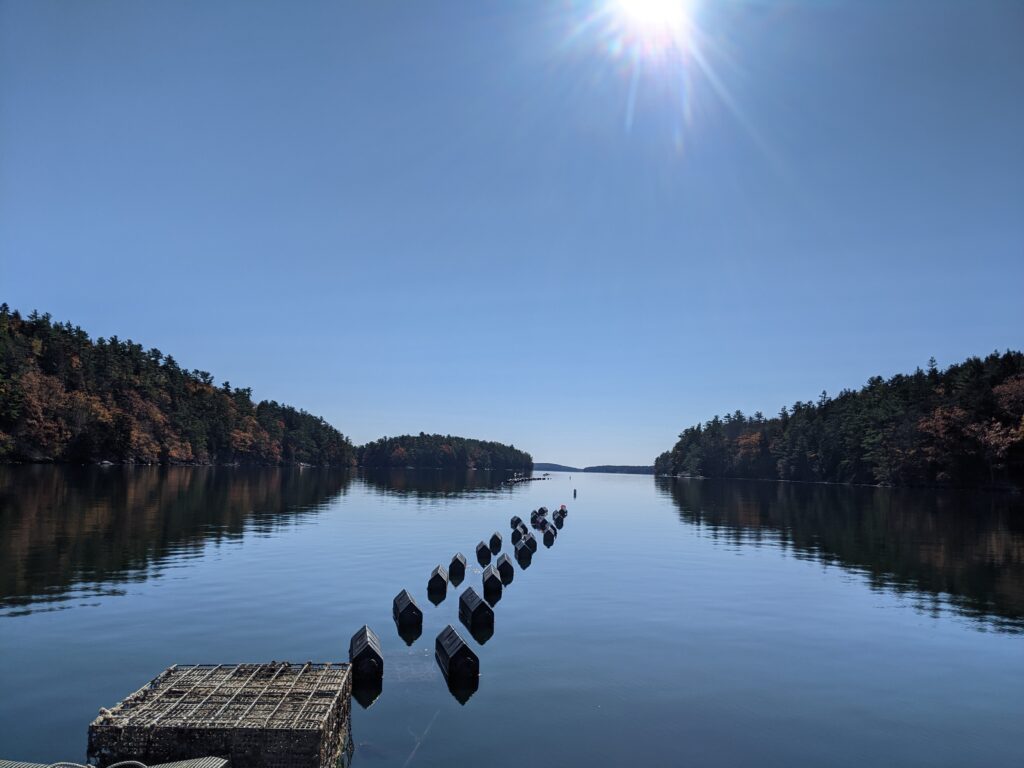
Monthly measurements were designed to categorize wear-and-tear by damage-type and by damage-location on each bag, in order to inform future prototype builders of specific weaknesses of each material.
Damage categories include:
• Chaffing/erosion (identifies friction damage)
• Cracking (identifies brittle plastic from shock, UV, or chemical damage)
• Stretching/tearing (identifies damage from weight/strain)
• Discoloration (identifies UV or chemical damage-depending on location)
Bags maintained the same orientation throughout the trial (sun-facing-bags/shaded-bags) to further test the effects of light-damage.
Throughout this experiment, we monitored several areas of potential areas of strain/damage on bags
• Top panel (potential sun damage)
• Bottom panel (friction in caged bags)
• Closure (repeated stress of handling- opening/closing)
• Folds (stress of initial bending/holding shape)
• Corners (stress of initial bending, contact with floating-cage wire)
• Float attachment points (weight stress- Hurricane floating bags only)
Fouling species were also measured each month using the Braun Blanquet percent-cover method (categorization system designed to control for multiple observers). Certain marine organisms (both algae and invertebrates) show strong affinity for different substrates. Specific plastics are used (for instance) to attract shellfish spat, or to encourage kelp settlement. When testing new materials, it is important to understand which organisms are attracted to each material in order to guide appropriate future uses. Fouling measurements were included to help future builders avoid excessive fouling on grow-out equipment, or to build more efficient spat-collectors.
Production delays (due to material availability, slow shipping times, the need to shift work between contractors, and high demand for fabrication equipment at partner institutions) necessitated a project extension into 2023 for adequate field testing of our experimental oyster bags.
Material and tool suitability
The common small-scale 3D printers originally envisioned for this project were not suitable even for small numbers of prototypes. The plastic filaments determined by project partners to be suitable for marine use required higher operating temperatures and printed much slower than more commonly used materials. After initial testing on available equipment, nylon filament was calculated to take 60 hours per bag with regular intervention required by the operator. Fabrication using this method would require far more labor than was budgeted for in our proposal and would tie up equipment and resources at partner organizations and schools. It would not be cost effective even for small numbers of prototypes.
Laser cutting was performed on PETG and a sample of UHMW polyethylene (a plastic related to VHMW polyethylene with longer hydrocarbon chains) by cooperating educator Paul Meinersmann (Technology & Makerspace Director St. George Municipal School Unit). A single PETG bag was cut and assembled, though we ruled out constructing more bags using this method and material. Cutting time alone took 4.5 hours and produced residues that would be harmful to the tool with continued use. The UHMW polyethylene took multiple passes for the laser to cut at full power (60W), and the material was also ruled out as a viable option.
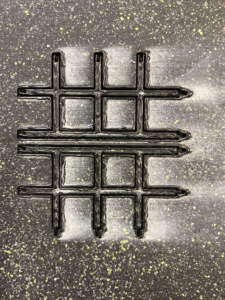
With this realization we pivoted to exclusively using CNC routing with sheet plastics at Haystack Mountain School of Craft's specialized fabrication lab (FabLab).
The additional workload at Haystack had to be fit in around existing programming at the facility, which set back our field trial. Our extension into the 2023 field season allowed us to collect a full dataset included wear, damage, and fouling caused by overwintering.
Wear and damage in the field
Damage was measured in several ways
- by material
- by location on bag
- by position on farm
There were strong differences in durability between materials. The PETG bags were far more fragile than HDPE and VHMW polyethylene. PETG was more than twice as likely to be damaged than HDPE (the standard material used in aquaculture) when built with the same construction methods (3.4 instances of damage per bag for PETG compared to 1.6 instances of damage per bag for HDPE). VHMW was even more durable, averaging only 1 instance of damage per bag.
These differences were even more pronounced when examining the number of bags that experienced some form of structural failure (requiring repair/reconstruction before being able to perform the basic function of retaining oysters). 43% of PETG bags had a structural failure over the course of the experiment, compared to 13% of HDPE bags and 0% of VHMW bags.
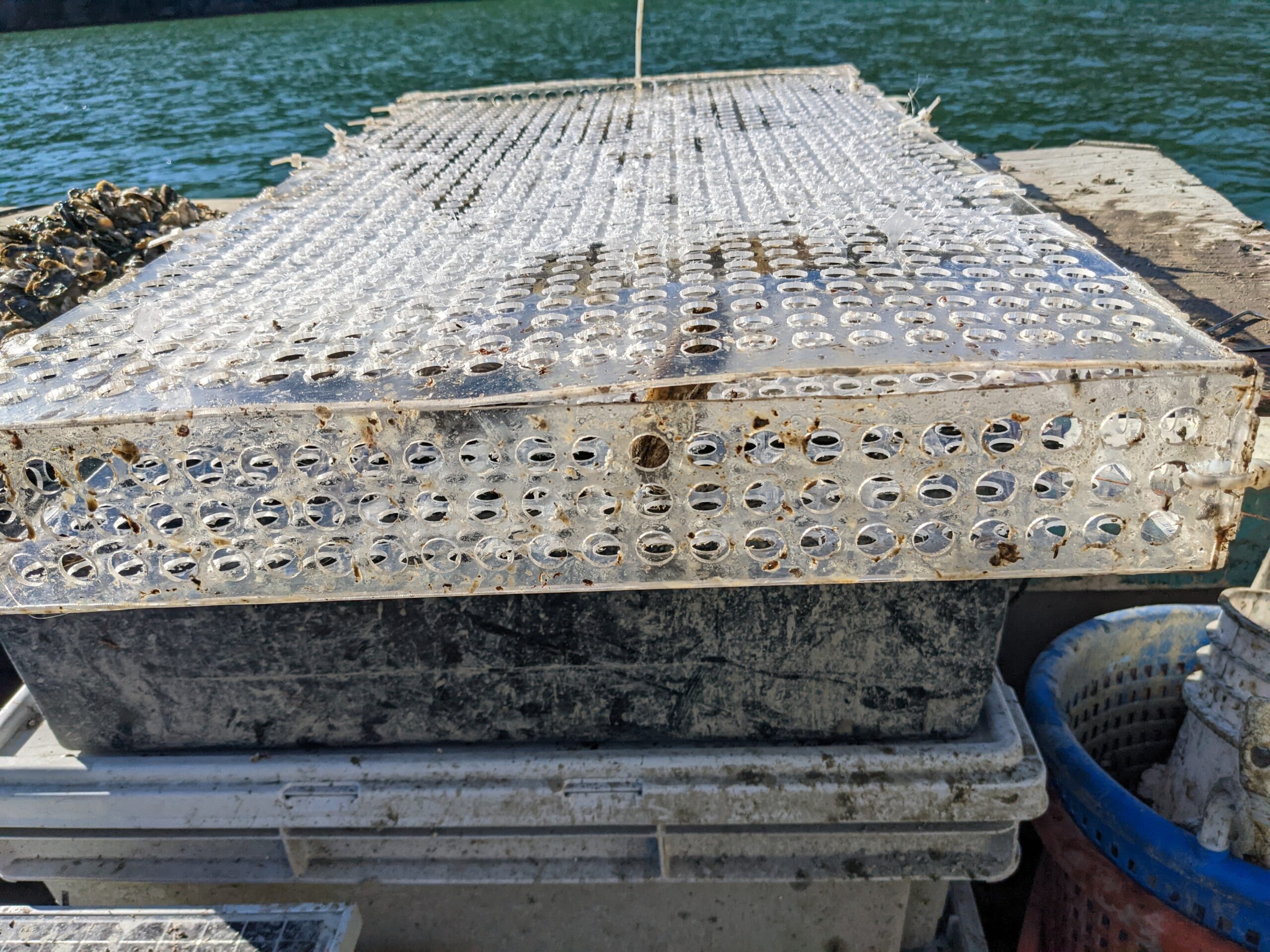
PETG was much more susceptible to cracking and tearing than the other materials, but was less likely to register chafing or erosion. It is unclear whether the the susceptibility to cracking was a product of the material, or the thinner sheeting used (though fabricators advised that thicker sheeting would be less flexible and even more brittle). VHMW saw less damage from chafing, cracking, or tearing than HDPE, but saw more discoloration. This could, however, be due to the fact we used a white variant of this material that made staining from fouling organisms more apparent. We did not see the expected sun-bleaching discoloration in any of the materials tested.
Most of the consequential damage observed on bags occurred on folds, corners, and bag closures. This damage was found on split or cracked folded-edges, on welds, or most often- on broken tabs. Though chaffing/erosion was recorded, this damage was largely superficial. There was no structural damage associated with discoloration- (which was connected to with staining from contact with fouling organisms instead of sun damage).
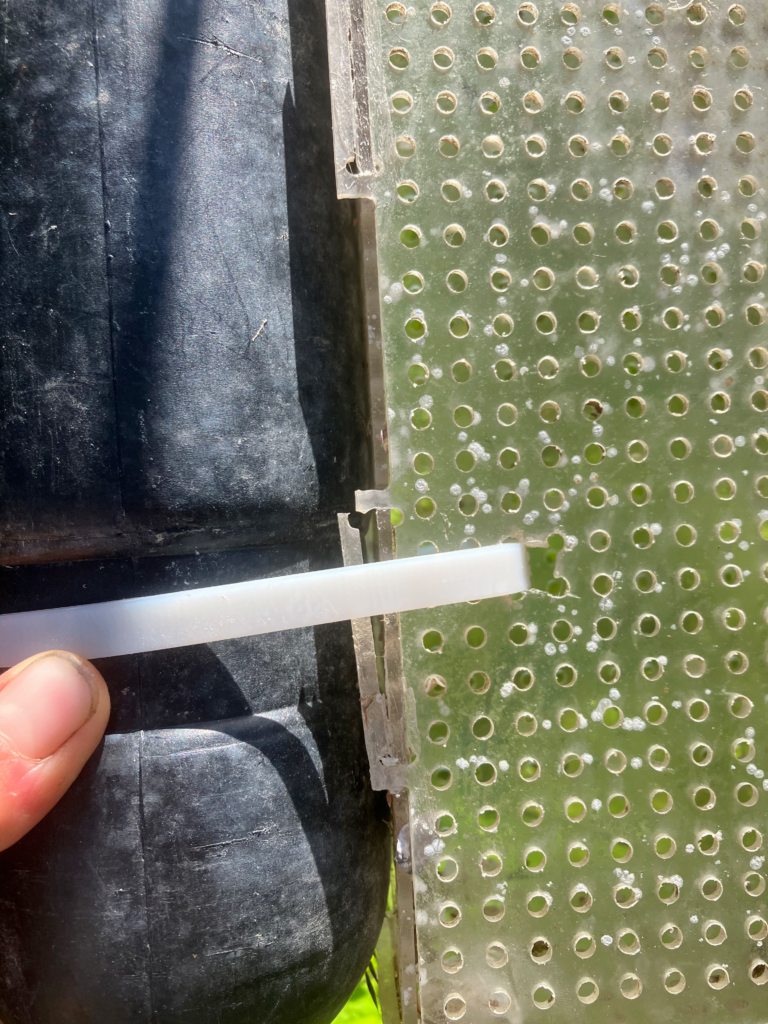
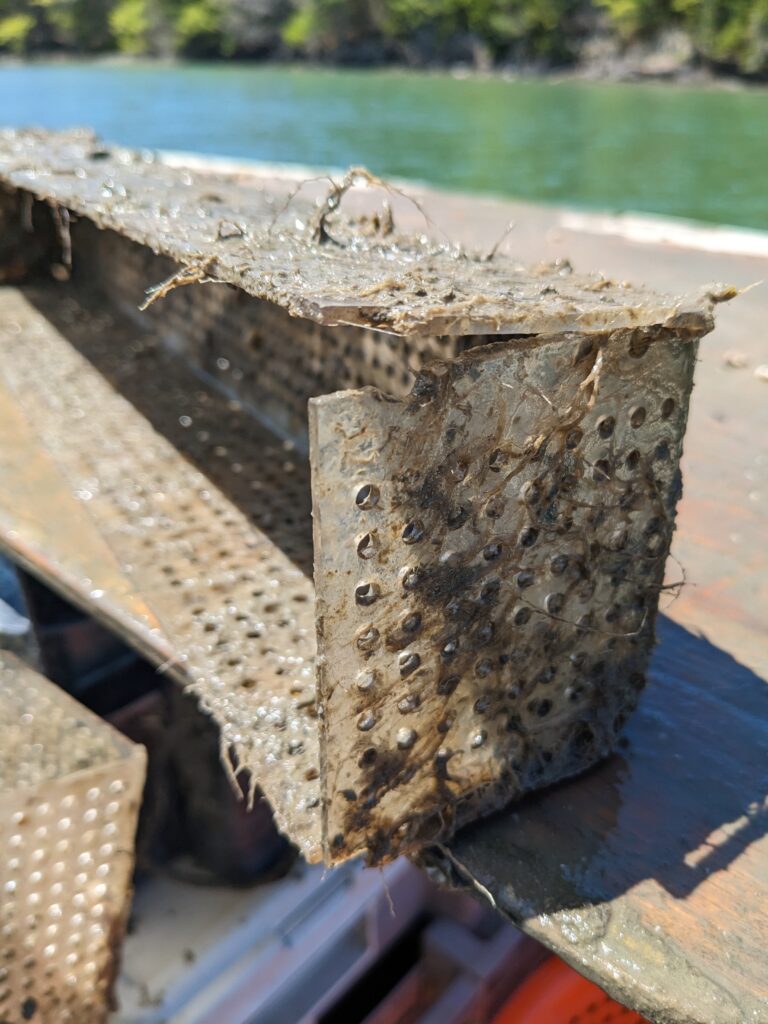
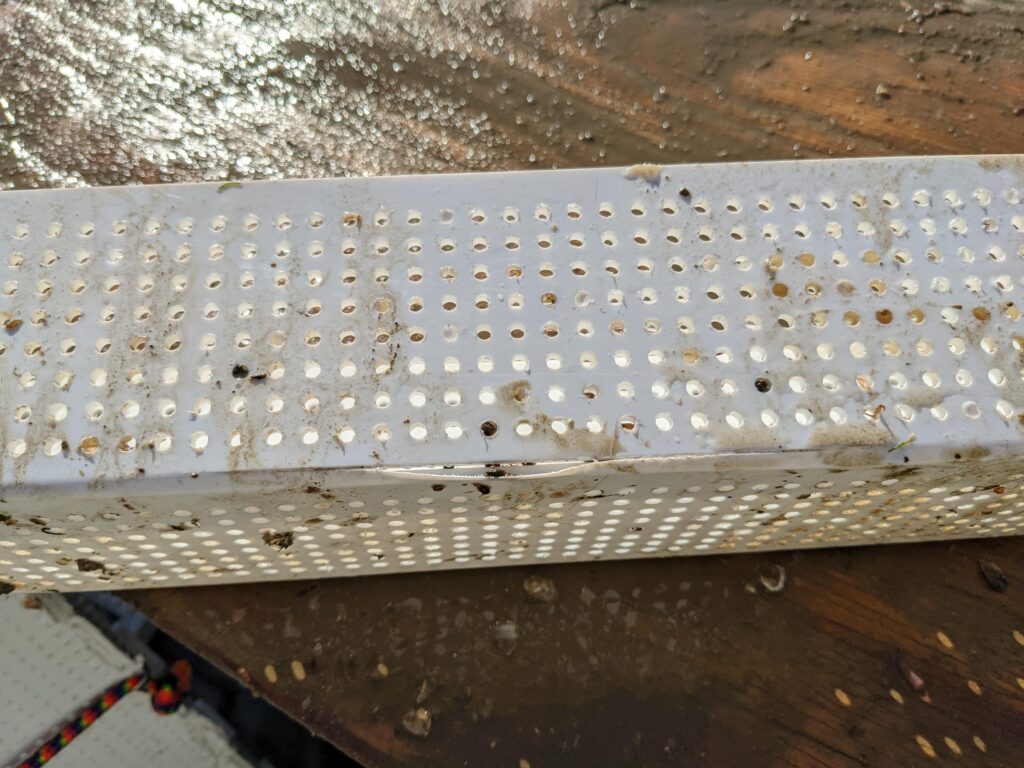
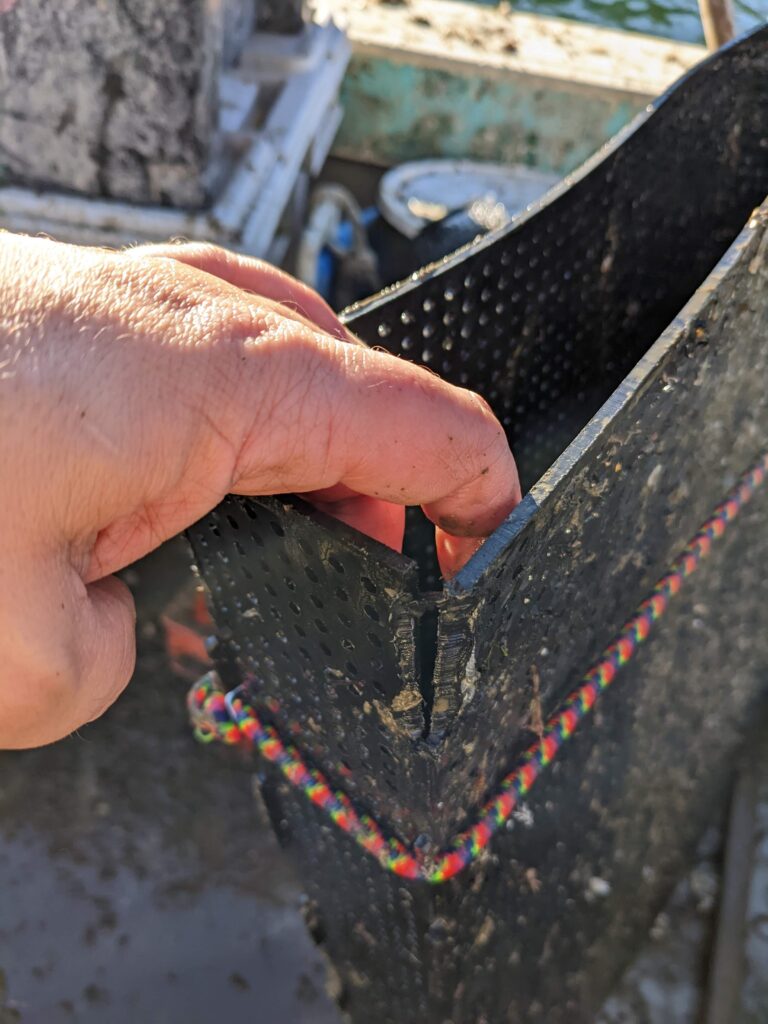
Floating bags and bags deployed in the top bay of oyster-cages saw more damage than bags in the bottom bay of oyster cages. Given the types of major damage observed in the project (broken tabs, seams and closures), this seem likely due to mechanical stressors instead of light exposure (which would most affect the sun-facing panels). The top bays of oyster cages at Winnegance are tighter than bottom bays (pontoon fasteners and structural reinforcement take up space). Tabs and edges of bags rubbed and caught-up on the edges of cages- particularly when bags were removed for handling. Floating bags faced the stress of holding oysters without the added structure of a cage- putting extra strain on weak point like scored seams, welds, and tabs.
Other damage
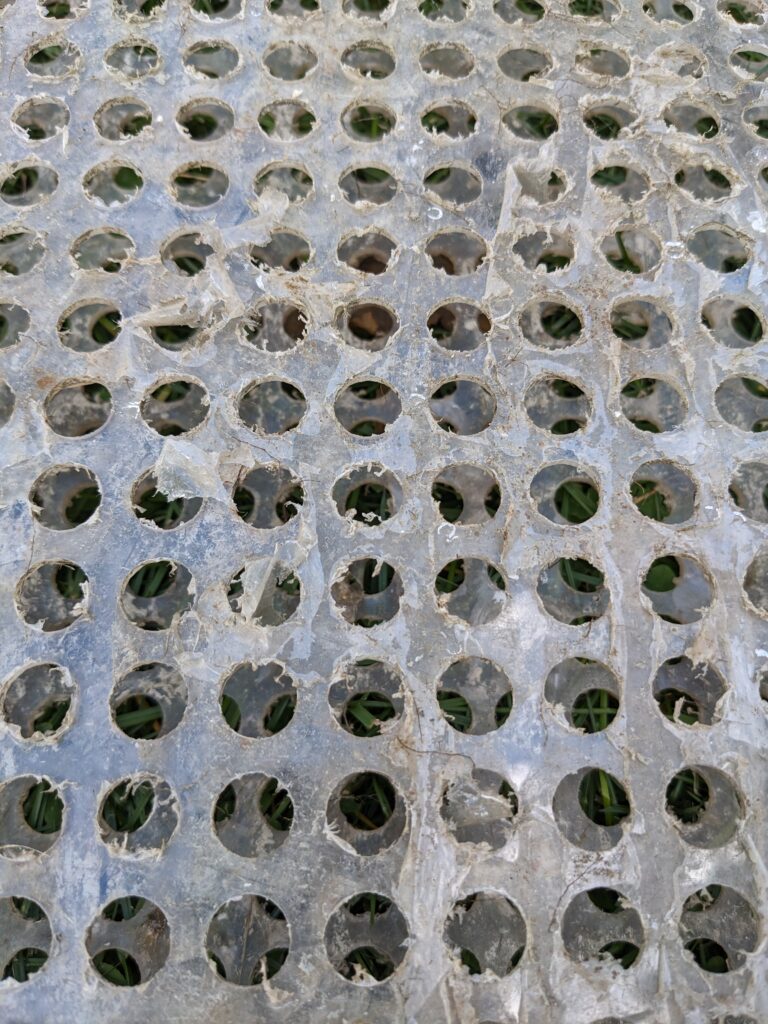
A protective film was found on some of the PETG sheets. While most of it was removeable, some bags had sections where the film was fused to the sheeting. Over time portions of this fused film began delaminating.
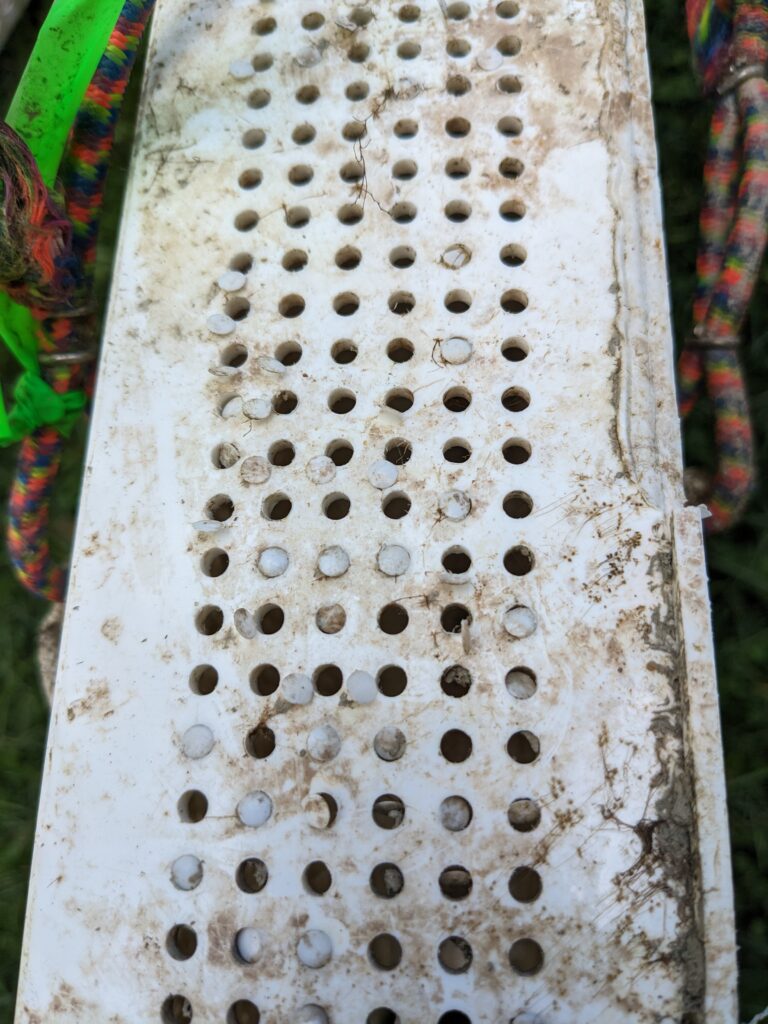
On bags with 4mm holes, incomplete routing left some small circles partially attached to the plastic sheeting. With time and handling, some of these plastic circles were shed into the water.
These material and fabrication flaws presented plastic-pollution sources that should be eliminated in future prototypes.

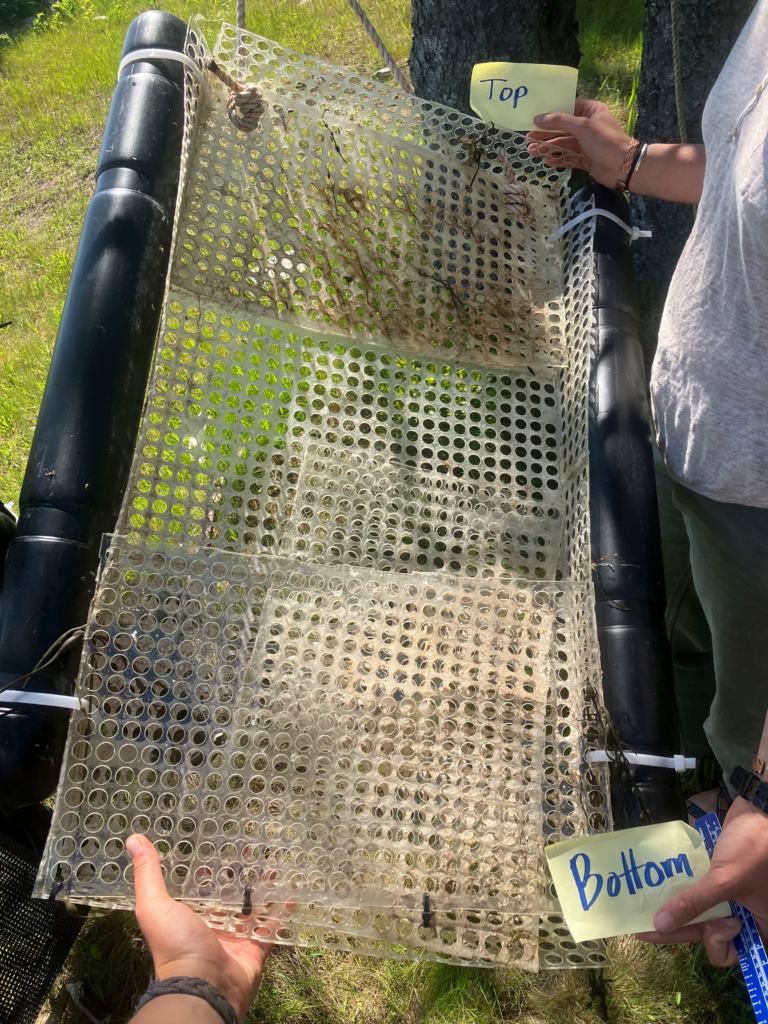
The lone laser-cut PETG bag was constructed of smaller panels of plastic which were welded together. These welds were a weak point and failed during a large storm early in the project.
Fouling
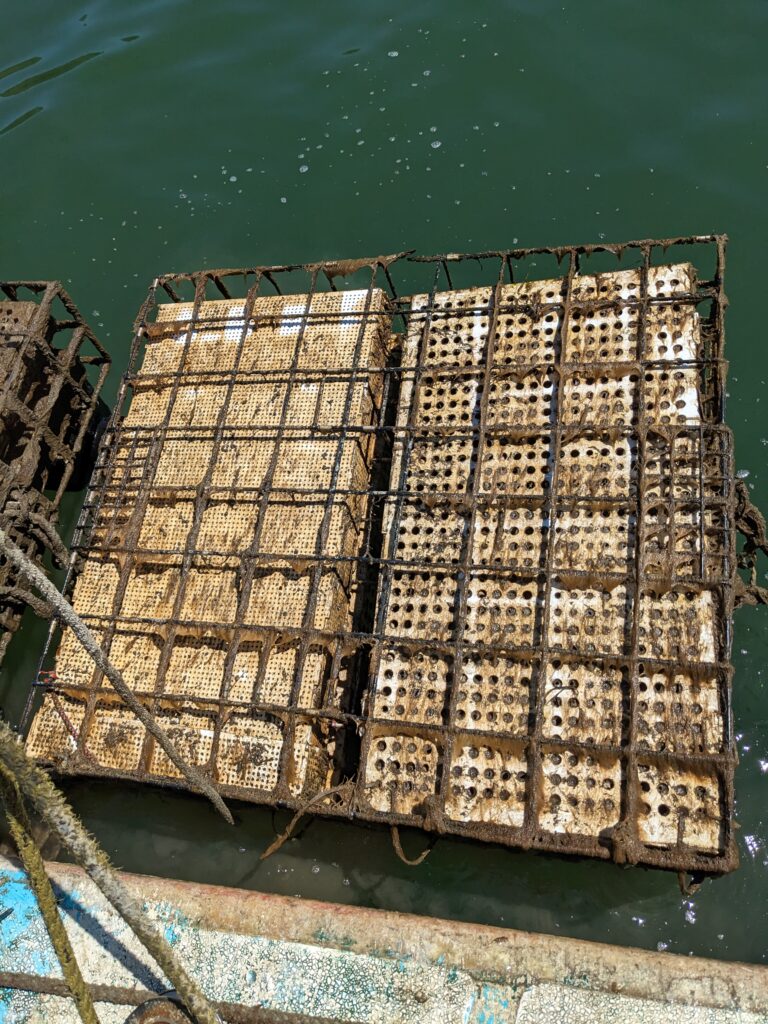
The two field sites were situated in dissimilar environments and saw very different communities of fouling organisms.
Fouling at Winnegance
Winnegance Oyster Farm- located on an inshore bay experienced an abnormally high fouling year in 2022. Bryozoans, mussels, sea vases, and barnacles were the most prevalent fouling invertebrates.
VHMW had the highest peak coverage of the most difficult to manage fouling species- mussels (7.5%) and sea vases (5.3%) - though only slightly higher than observed in HDPE (mussels 5.4%, sea vases 4.25%). VHMW also saw the highest peak fouling of crust-forming bryozoans (8.4%). HDPE saw the highest incidence of barnacles (4%) and coral-like bryozoans. Despite being deployed for the shortest time of all materials in the experiment, PETG bags had the highest peak of feathery-bryozoan fouling.
HDPE | |||||||
Sampling period | Bryozoan (feathery) | Blue Mussel | Orange tunicate | Sea_vase | Bryozoan (coral) | Bryozoan (crust) | Barnacles |
1_July | 9.5 | 0.0 | 0.0 | 0.0 | 0.0 | 0.0 | 0.0 |
2_Aug | 15.5 | 0.0 | 0.3 | 0.0 | 0.8 | 0.0 | 0.0 |
3_Sept | 0.0 | 0.0 | 0.0 | 1.0 | 0.3 | 0.0 | 4.0 |
4_Oct | 0.0 | 0.0 | 0.0 | 0.0 | 4.3 | 0.0 | 0.0 |
5_May | 25.0 | 1.1 | 0.0 | 0.0 | 0.1 | 0.5 | 0.1 |
6_June | 24.0 | 5.4 | 0.8 | 4.3 | 0.5 | 0.5 | 1.1 |
PETG | |||||||
Sampling period | Feathery Bryozoan | Blue Mussel | Orange tunicate | Sea_vase | Bryozoan (coral) | Bryozoan (crust) | Barnacles |
1_July | |||||||
2_Aug | |||||||
3_Sept | |||||||
4_Oct | |||||||
5_May | 35.1 | 1.3 | 0.1 | 0.0 | 0.0 | 6.1 | 0.0 |
6_June | 32.1 | 1.1 | 0.5 | 1.9 | 0.0 | 8.0 | 0.8 |
VHMW | |||||||
Sampling period | Feathery Bryozoan | Blue Mussel | Orange tunicate | Sea_vase | Bryozoan (coral) | Bryozoan (crust) | Barnacles |
1_July | 7.5 | 0.0 | 0.0 | 0.0 | 0.0 | 0.0 | 0.0 |
2_Aug | 15.5 | 0.0 | 0.0 | 0.0 | 0.8 | 0.0 | 0.0 |
3_Sept | 8.8 | 0.0 | 0.0 | 0.0 | 0.0 | 0.0 | 0.8 |
4_Oct | 2.0 | 0.0 | 0.0 | 0.0 | 2.5 | 0.0 | 0.0 |
5_May | 28.1 | 7.5 | 0.4 | 0.0 | 0.0 | 0.0 | 0.1 |
6_June | 16.4 | 3.3 | 0.3 | 5.3 | 0.1 | 8.4 | 0.1 |
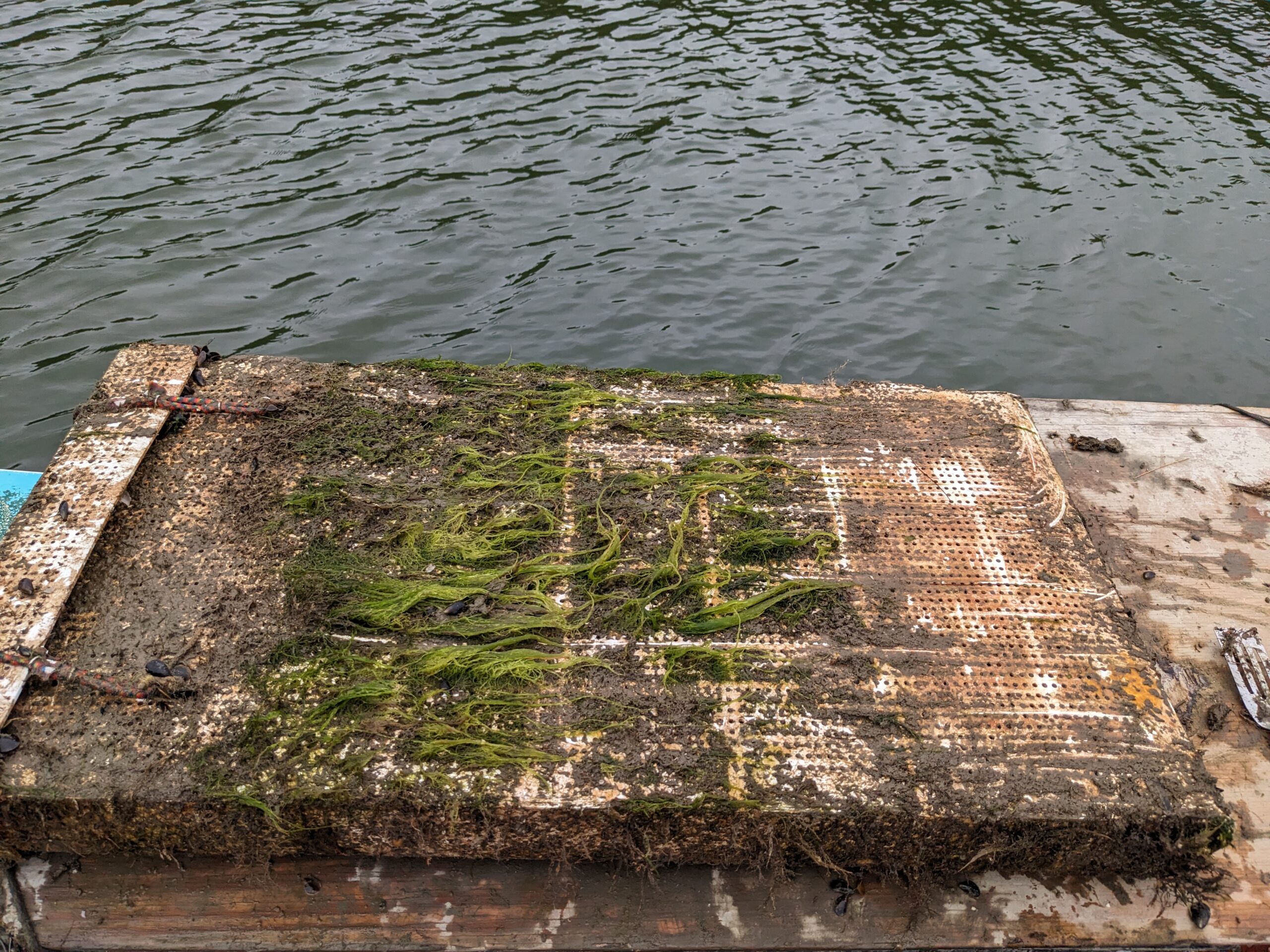
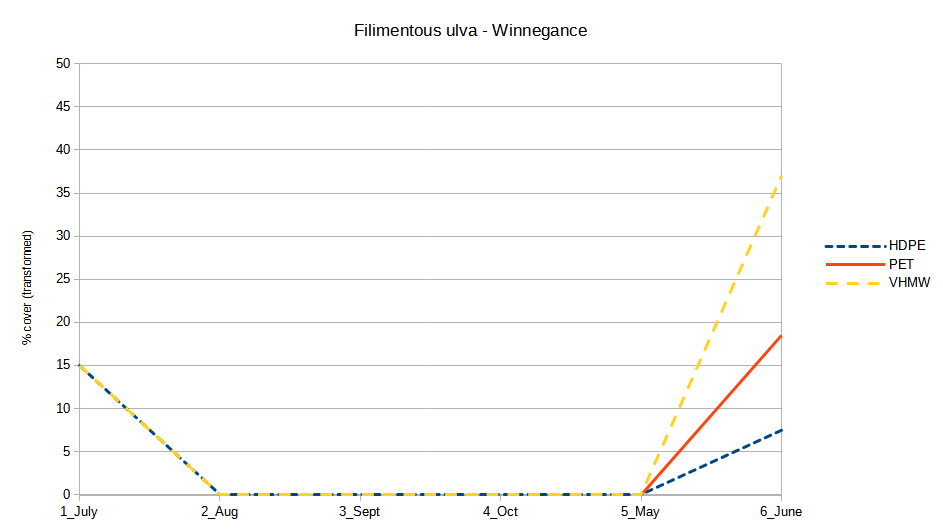
Filamentous ulva fouling was similar across materials until the final set of measurements in 2023 when much higher levels were found on VHMW (37%) compared to HDPE (18.5%) and PETG (7.5%). VHMW also saw fouling from filamentous red algae (7.5%) in September of 2022. It is unclear whether the higher fouling on VHMW sheeting was a product of the material or its color.
Sampling period | Ulva (filamentous) | Ulva (sea lettuce) | Brown algae (non-kelp) | Kelp | Red algae (filamentous) |
1_July | 15 | 0 | 0 | 0 | 0 |
2_Aug | 0 | 0 | 0 | 0 | 0 |
3_Sept | 0 | 0 | 0 | 0 | 0 |
4_Oct | 0 | 0 | 0 | 0 | 0 |
5_May | 0 | 0 | 0 | 0 | 0 |
6_June | 7.5 | 0 | 0 | 0 | 0 |
PET | |||||
Sampling period | Ulva (filamentous) | Ulva (sea lettuce) | Brown algae (non-kelp) | Kelp | Red algae (filamentous) |
1_July | |||||
2_Aug | |||||
3_Sept | |||||
4_Oct | |||||
5_May | 0 | 0 | 0 | 0 | 0 |
6_June | 18.5 | 0 | 0 | 0 | 0 |
VHMW | |||||
Sampling period | Ulva (filamentous) | Ulva (sea lettuce) | Brown algae (non-kelp) | Kelp | Red algae (filamentous) |
1_July | 15 | 0 | 0 | 0 | 0 |
2_Aug | 0 | 0 | 0 | 0 | 0 |
3_Sept | 0 | 0 | 0 | 0 | 7.5 |
4_Oct | 0 | 0 | 0 | 0 | 0 |
5_May | 0 | 0 | 0 | 0 | 0 |
6_June | 37 | 0 | 0 | 0 | 0 |
Fouling at Hurricane Island
Hurricane Island's offshore field site saw a different collection of fouling species. Tunicates and jingle-shells accounted for the majority of invertebrate fouling at this site.
At peak, HDPE saw more fouling by both orange tunicates (15.5%) and red tunicates (7.5%) than observed on VHMW (5%/0.8%) and PETG (0%/0%). Jingle shell fouling was most prevalent on PETG (4.5% at peak) than on HDPE (2.4%) and VHMW (0.3%)
HDPE | ||||||
Sampling period | Jingle shells | Bryozoan (crust) | Red tunicate | Barnacles | Orange tunicate | Sea vase |
1_July | 0.0 | 0.3 | 0.0 | 0.0 | 0.0 | 0.0 |
2_Aug | 0.0 | 0.0 | 0.3 | 0.0 | 15.5 | 0.0 |
3_Sept | 0.0 | 0.5 | 0.5 | 0.0 | 3.8 | 0.0 |
4_Oct | 0.0 | 0.3 | 7.5 | 0.0 | 0.0 | 0.0 |
5_May | 2.4 | 0.0 | 0.0 | 0.0 | 0.0 | 0.1 |
6_June | 0.0 | 0.0 | 0.0 | 0.1 | 0.0 | 0.0 |
PETG | ||||||
Sampling period | Jingle shells | Bryozoan (crust) | Red tunicate | Barnacles | Orange tunicate | Sea vase |
2_Aug | 0.0 | 0.0 | 0.0 | 0.0 | 0.0 | 0.0 |
3_Sept | 0.0 | 0.0 | 0.0 | 0.0 | 0.0 | 0.0 |
4_Oct | 0.0 | 0.0 | 0.0 | 0.0 | 0.0 | 0.0 |
5_May | 4.5 | 0.0 | 0.0 | 0.0 | 0.0 | 0.0 |
6_June | 0.2 | 0.0 | 0.0 | 0.0 | 0.0 | 0.0 |
VHMW | ||||||
Sampling period | Jingle shells | Bryozoan (crust) | Red tunicate | Barnacles | Orange tunicate | Sea vase |
1_July | 0.0 | 0.3 | 0.0 | 0.0 | 0.0 | 0.0 |
2_Aug | 0.0 | 0.0 | 0.0 | 0.0 | 5.0 | 0.0 |
3_Sept | 0.0 | 1.0 | 0.2 | 0.0 | 5.0 | 0.0 |
4_Oct | 0.0 | 0.0 | 0.8 | 0.0 | 0.7 | 0.0 |
5_May | 0.3 | 0.0 | 0.0 | 0.0 | 0.0 | 0.2 |
6_June | 0.0 | 0.0 | 0.0 | 0.0 | 0.0 | 0.0 |
Algal fouling at Hurricane Island was dominated by brown algae (recorded as a group, with the exception of kelp which was recorded separately). Ulva lactuca (sea lettuce) was also abundant on PETG during October 2022 measurements.
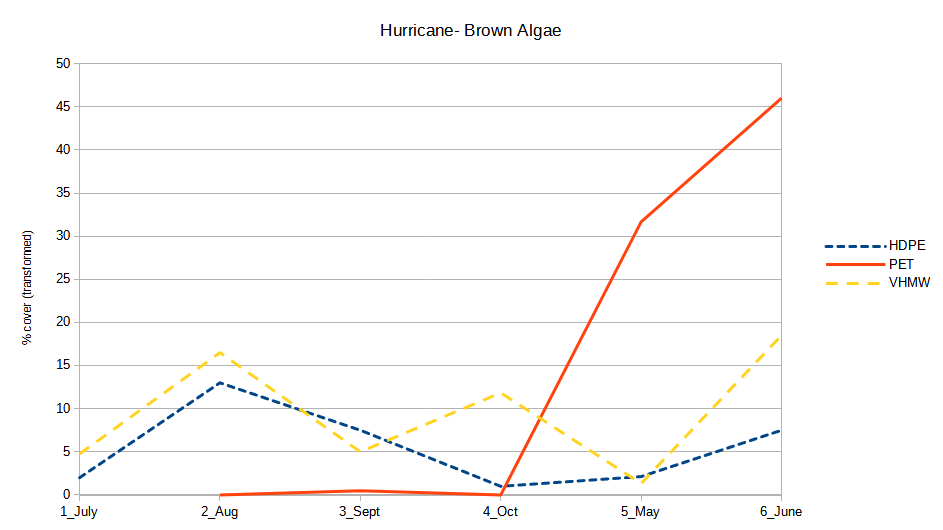
HDPE | |||||
Sampling period | Ulva (filamentous) | Ulva (sea lettuce) | Brown algae (non-kelp) | Kelp | Red algae (filamentous) |
1_July | 0.0 | 0.0 | 2.0 | 0.0 | 0.0 |
2_Aug | 0.0 | 0.0 | 13.0 | 0.0 | 0.0 |
3_Sept | 0.0 | 0.0 | 7.5 | 0.0 | 0.0 |
4_Oct | 0.0 | 0.0 | 1.0 | 0.0 | 0.0 |
5_May | 0.0 | 0.0 | 2.1 | 1.3 | 0.0 |
6_June | 0.0 | 0.0 | 7.5 | 0.0 | 0.0 |
PETG | |||||
Sampling period | Ulva (filamentous) | Ulva (sea lettuce) | Brown algae (non-kelp) | Kelp | Red algae (filamentous) |
1_July | |||||
2_Aug | 0.0 | 0.0 | 0.0 | 0.0 | 0.0 |
3_Sept | 0.0 | 0.0 | 0.5 | 0.0 | 0.0 |
4_Oct | 0.0 | 18.5 | 0.0 | 0.0 | 0.0 |
5_May | 0.0 | 0.0 | 31.7 | 0.0 | 0.0 |
6_June | 0.0 | 0.0 | 46.0 | 0.0 | 0.0 |
VHMW | |||||
Sampling period | Ulva (filamentous) | Ulva (sea lettuce) | Brown algae (non-kelp) | Kelp | Red algae (filamentous) |
1_July | 0.0 | 0.0 | 4.8 | 0.0 | 0.0 |
2_Aug | 0.0 | 0.0 | 16.5 | 0.0 | 0.0 |
3_Sept | 0.0 | 0.0 | 5.0 | 0.0 | 0.0 |
4_Oct | 0.0 | 0.0 | 11.8 | 0.0 | 0.0 |
5_May | 0.0 | 0.0 | 1.3 | 0.2 | 0.0 |
6_June | 0.0 | 0.0 | 18.5 | 0.0 | 0.0 |
Handling
The experimental gear had some immediate benefits. The flat, drilled surfaces of CNC routed bags (versus the woven texture found on commercial gear) prevented oysters from clumping and from getting stuck in bag corners. Flat surfaces were also far easier to effectively clean with a paint-scraper compared to woven-texture commercial bags. This easy manual cleaning made air-drying even more effective.
VHMW bags were exceptionally rigid for their thickness, making them easier to handle when holding a heavy load. The rigidity of this material could allow thinner sheets to be used, which could potentially reduce both costs and fabrication time.
Clear PETG sheeting made it easy to observe oysters in bags without having to handle them (though this benefit may diminish if bags discolor over time).
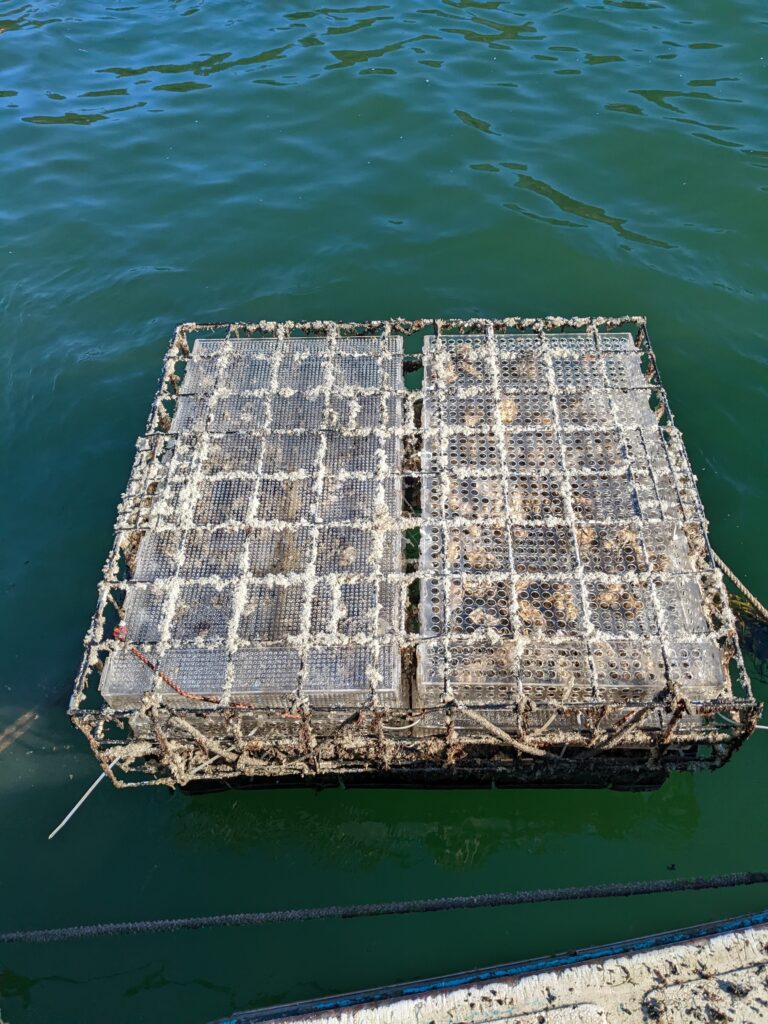
The experimental bags had some major handling drawbacks as well. Bags were heavier than standard commercially available equipment and were much more slippery. Bag closures required additional fasteners and were difficult to use in the field. The tabbed construction protruded from the edge of bags and caught on the wire mesh of oyster cages. Making removal from cages difficult and caused damage to tabs.
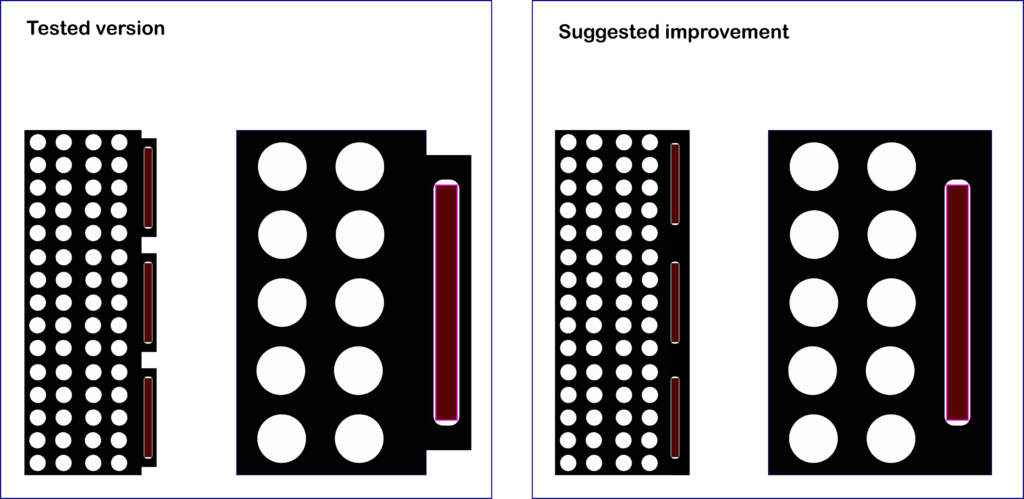
This project sought to test the viability of 3D printing/routing techniques and materials to determine their suitability for prototyping new gear designs. We hoped that farmers could design and build prototype gear to suit the unique needs of their operations using what is now an easily accessible technology.
The design and materials testing phase ruled out a number of techniques and materials that utilize consumer grade extrusive 3D printers. High costs for safe and seaworthy materials, lengthy real-world fabrication times, and small project formats that require lots of post-printing welding made conventional printing impractical, even for one-off prototypes of full-scale farming gear. This may change as 3D printers continue to evolve and improve.
CNC routing proved a much better option than printing, but was neither cheap nor fast. Routed bags did have some interesting benefits over traditional bags, as well as many shortcomings. With the limitations and costs seen in this project, one contractor suggested that prototypes would be better and more cheaply made at a conventional machine shop using a die press. The fabrication methods and materials used in this project do not seem ready for wider application.
Going forward, I hope to build some of my own experimental designs using a blend of conventional and printed/routed construction (with the latter limited to small-scale parts that would be difficult to build with conventional means and that require limited welding- if any at all).
The flat mesh used in this project does show some promise as a bag material if manufactured by conventional means. Flat panels were much easier to clean than traditional basket-weave mesh- letting scraping tools fully excise colonies of invertebrates or mats of algae with a single stroke. If a commercial version of this mesh were available (and was able to be securely assembled into oyster bags) cleaning labor on farms could be significantly reduced.
I think that VHWM polyethylene warrants further investigation as a material in aquaculture application. Its durability and rigidity could potentially lead to less waste, less replacement, and more repairable gear. This assessment would have to include an examination of the consequences of VHMW gear breaking or breaking-down, and the potential for more persistent plastic pollution.
Education & Outreach Activities and Participation Summary
Participation Summary:
On May 24th, 2022 an overview of the project was presented during a webinar hosted by the Herring Gut Coastal Science Center to 35 participants. Backgrounds of attendees varied from farmers, prospective farmers, agricultural service providers, marine educators, to the general public.
A project overview and field updates were shared with 11 members of the New Meadows River Shellfish Co-op. Three members visited the field site over the course of the project.
Hurricane Island's researchers led farm tours throughout the field trial. This included 100 6th to 12th grade students, 35 parents, 12 individuals in the aquaculture industry, and 12 staff members from other programs at Hurricane Island.
At the time of writing, social media outreach has been seen by 1939 accounts. 250 accounts have engaged with the content. Social media outreach will continue and will link to the final report.
Learning Outcomes
Farmers reported awareness of the limitations of traditional 3d printing and interest in using non conventional materials- with particular interest in the more durable plastic tested (VHMW polyethylene).
Project Outcomes
This project taught me new techniques for mending equipment using plastic welding. This will allow me to keep damaged conventional oyster bags in service longer, reducing waste.
The techniques tested in this project will also guide me as I develop and test new types of equipment on my farm - helping me avoid fabrication dead ends and excess expense.
If re-imagining the project, I would try reduce the number of variables measured. Tracking multiple types of damage on every surface of the experimental bags complicated analysis.
I think that further testing of VHMW polyethylene is warranted (given its durability). I would be particularly interested in looking at the effects of color on fouling to see if material or color led to the differences seen in this study.
I hope to test prototypes of experimental bags of my own design in the near future- though will likely hire a traditional machine shop (unless new computer controlled fabrication techniques come to light).
I hope that other farmers do not overcommit to these techniques until the technology advances (though I think the rapid evolution of 3D printing and CNC machining will make further testing of custom fabrication worthwhile).