Final report for FNE22-018
Project Information
This project was proposed by Blue Stream Shellfish (BSS) to design and construct a remotely operated underwater vehicle (ROV) for the purpose of retrieving unmarked bottom oyster cages in waters deeper than 5-10 feet. With the assistance of a highly skilled underwater robotics engineer, BSS conceived and constructed the OysterBot, an ROV designed to assist in shellfish farm operations conducted in deeper waters. While it turned out that assembly of the ROV from component parts was beyond the skill set of a conventional farmer, the Technical Adviser was able to assemble and debug the OysterBot for application on the farm. Using the OysterBot to attach a lifting line to a bottom cage with no vertical line or surface buoy marker was demonstrated to be an effective way to retrieve ropeless cages. However, further development of using an ROV at a commercial scale on an oyster farm to retrieve unbuoyed cages remains to be fully tested in the future. In the meantime, the OysterBot has proven to be a highly useful tool on the farm for visualizing conditions on the bottom and potentially manipulating equipment in deeper water farms where visibility is limited to a few feet at the surface. Turnkey ROVs currently are available commercially that would provide these services without the hindrance of assembling the ROV from component parts. The results of this project have been presented at multiple shellfish farming and/or research sessions and to a farm tour. Additionally, a short article on the application of an ROV for oyster farm operations is in preparation for publication by the East Coast Shellfish Grower Association’s newsletter.
This project seeks to build a technology that allows nearshore oyster cages on the bottom to be retrieved without vertical lines to surface buoys. This will be accomplished by developing a tethered remotely operated underwater vehicle (ROV) that will provide a real-time image of the cage on the bottom and will attach a lifting line to the cage for retrieval. The following objectives are proposed to complete this project:
- Identify the mechanical attributes of an ROV required to achieve the goals of maneuverability underwater, identification of unique bottom cage markings, and ability to attach a lifting line to a cage harness for retrieval;
- Design and construct an ROV that meets the qualifications outlined in Objective 1 (i.e. the OysterBot);
- Evaluate the OysterBot on a commercial farm to assess its capacity to replace surface lines for cage retrieval;
- Outreach this technology to other farms that are operating in nearshore waters.
The availability of the OysterBot concept will not only aid current subtidal farms in managing cage retrieval but it will also open up new areas for oyster farming by eliminating the vertical lines that will prohibit farm development where entanglements are a risk.
Recent reports project shellfish aquaculture has and will continue to proliferate in the northeast (GMRI 2016, CEI 2018), resulting in areas currently preferred becoming limited. As concluded in an evaluation of shellfish aquaculture in the northeast, farm growth will be affected by “location expansion constraints” (GMRI 2016).
Shellfish aquaculture is a sustainable and desirable farming activity. Hilborn et al. (2018) assessed the environmental impact of a variety of animal-sourced foods, including livestock, aquaculture and capture fisheries and concluded the lowest impact production systems were small pelagic fisheries and molluscan aquaculture. Furthermore, aquaculture could play a large role in sustaining our coastal communities (Love 2016). However, in assessing expansion of coastal aquaculture in the region, CEI (2018) reported that significant resistance to expansion in intertidal and shallow areas is due to “not in my backyard” attitudes of coastal residents.
An alternate area becoming more attractive for shellfish aquaculture is the nearshore, defined as deeper water located within 3 miles of but not immediately adjacent to the shoreline (Price et al. 2016). Nearshore farms have always been in existence, particularly along those shorelines with limited intertidal areas; however, interest is expanding. For example, New Bedford (MA) recently announced 8,400 acres of municipal waters were available for aquaculture development (CEI 2018) where an estimated 90% are in water depths of 15 to 30 feet.
While out of the viewscape of NIMBY landowners, nearshore farms are influenced by the same conditions as inshore sites while being more exposed to high energy conditions (Price et al. 2016). Nearshore farm technology requires more robust and heavier cages suited for the challenging conditions and servicing heavier cages requires larger vessels deploying extensive vertical lines and buoys, similar to lobster fishing. The predominant technologies (floating, suspended or bottom tending) require an extensive array of vertical lines to anchor floating gear or to mark submerged gear. Vertical lines are a recognized risk to marine megafauna (Gentry et al. 2016, NOAA 2017); most listed as endangered or threatened and including sea turtles, primarily leatherback and loggerhead turtles (NMFS 2015); whales, with the North Atlantic Right Whale preeminent (Moore and van der Hoop 2012, Schreiber 2018, Upite et al. 2019); and, further south, manatees (Reinert 2015). Vertical lines in open waters are under intensifying scrutiny and regulation due to the risk of entanglements. Establishing a farm with vertical lines in nearshore waters will be severely limited or prohibited, as has happened with the lobster fishery (DMF 2021), unless we can develop technology to eliminate the lines, similar to attempts being made in the lobster fishery (Baumgartner et al. 2021).
Another aspect to vertical lines in aquaculture is the risk to the farmer. Between 1993 and 1999, seven lobstermen in the northeast drowned after being pulled overboard due to entanglement in lines on deck as the trap is released (NIOSH 2005). In a survey of lobstermen, 73% indicated that they had been caught in a trap line at some point in their careers (NIOSH 2005).
Following a “best of the worst” scenario focused on expanding into nearshore farm sites (CEI 2018), it is imperative that those farms reduce or eliminate vertical lines. This was the case when Blue Stream Shellfish (BSS) applied for a federal Letter of Permission for their Mattapoisett farm. Although right whales have never been reported in the area and sea turtles only rarely observed, BSS was required to reduce the number of vertical lines to 50% of the proposed number with the ultimate goal of removing them entirely from the site. To that end, we have been considering means to undertake ropeless shellfish farming in deeper waters. With this project, BSS proposes to develop ropeless oyster cages by retrieving them from the bottom using a remotely operated vehicle (ROV), i.e. the “OysterBot”.
In considering sustainable agriculture, this project addresses three of five SARE goals. They are:
- Reduction of environmental and/or health risks in agriculture
- Having a complex of lines on deck that are rapidly deploying with the sinking cage risks entangling the farmer and pulling him overboard. By removing the line, the risk to entanglement and drowning is removed.
- Improved productivity, reduction of costs and/or increase of net farm income
- Lines and buoys are an added expense to farm operations that can be eliminated with the elimination of vertical lines.
- Conservation of soil, improvement of water quality, and protection of natural resources
- Vertical lines in waters frequented by marine megafauna are a serious risk to the natural resource. With the development of ropeless oyster cages, that risk of entanglement is significantly reduced for those threatened or endangered species.
References:
Baumgartner, Werner, Knowlton, Moore, & Kraus. 2021. Rope-less fishing: A vision for how it can work. Ropeless Consortium Background. https://ropeless.org/background/ (accessed 7 January 2024)
CEI. 2018. Opportunities for aquaculture on the Massachusetts South Coast: a sector analysis. Coastal Enterprises. Inc. Rpt. to the Garfield Foundation and Santander Bank. https://www.ceimaine.org/wp-content/uploads/2018/04/MA-South-Coast-Aquaculture-Analysis.2018.pdf (Accessed 7 January 2024)
DMF. 2021. New protected species regulations finalized for fixed gear fisheries and industry outreach on required gear modifications. Marine Fisheries Advisory, MA DMF. Feb 19, 2021. https://www.mass.gov/doc/21921-new-protected-species-regulations-finalized-for-fixed-gear-fisheries-and-industry/download (Accessed 7 January 2024)
Gentry, Lester, Kappel, White, Bell. Stevens, & Gaines. 2016. Offshore aquaculture: spatial planning principles for sustainable development. Ecol. Evol. 7:733-743.
GMRI. 2016. Maine Farmed Shellfish Market Analysis. GMRI report with the Hale Group. https://d3esu6nj4wau0q.cloudfront.net/documents/gmri_farmed_shellfish_final_with_cover_10.13.16.pdf (Accessed 7 January 2024)
Hilborn, Banobi, Hall, Pucylowski, & Wadworth. 2018. The environmental cost of animal source foods. Front. Ecol. Environ. 16(6):329-335.
Love. 2016. Shellfish and seaweed aquaculture as a mechanism for economic diversification in Maine island and coastal communities. Report to the Casco Bay Estuary Partnership. https://cascobayestuary.org/wp-content/uploads/2016/11/Shellfish-and-seaweed-aquaculture-as-a-mechanism-for-diversification-2016.pdf (Accessed 7 January 2024)
Moore & van der Hoop. 2012. The painful side of trap and fixed net fisheries: chronic entanglement of large whales. J Mar. Biol. 2012:1-4.
NIOSH 2005. Dangers of entanglement during lobstering. Workplace Solutions. NIOSH, CDC, DHHS, Cincinnati, OH. https://www.cdc.gov/niosh/docs/wp-solutions/2005-137/pdfs/2005-137.pdf?id=10.26616/NIOSHPUB2005137 (Accessed 7 January 2024)
NOAA. 2017. Entanglement of marine life: risks and response. NOAA Fish. Brochure, 19 June 2017. https://www.fisheries.noaa.gov/insight/entanglement-marine-life-risks-and-response (Accessed 7 January 2024)
Price, C.S., E. Keane, D. Morin, C. Vaccaro, D. Bean, and J.A. Morris, Jr. 2016. Protected species and longline mussel aquaculture interactions [online document]. NOAA/NOS/NCCOS, Beaufort, North Carolina. http://www.fourstarbooks.net/portfolio/design/NOAAmusselsbooklet.pdf (accessed 7 January 2024)
Reinert., Spellman, & Bassett. 2017. Entanglement in and ingestion of fishing gear and other marine debris by Florida manatees, 1993 to 2012. Endang. Species Res. 32:415-427.
Schreiber 2018. Lobster industry grapples with right whale deaths. Fishermen’s Voice. 23(4) https://www.fishermensvoice.com/archives/201804LobsterIndustryGrapplesWithRightWhaleDeaths.html (Accessed 7 January 2024)
Upite, Murray, Stacy, Stokes, & Weeks. 2019. Mortality rate estimates for sea turtles in Mid-Atlantic and Northeast fishing gear, 2012-2017. Greater Atlantic Region Policy Series 19-03. NOAA Fisheries Greater Atlantic Regional Fisheries Office. 15p. https://www.greateratlantic.fisheries.noaa.gov/policyseries/index.php/GARPS/article/view/13/12 (Accessed 7 January 2024)
Blue Stream Shellfish, LLC (BSS) is an enterprise operating two farms in southeastern Massachusetts. Seal Rock Farm is located in Buzzards Bay, 1 mile south of Brandt Cove (Mattapoisett, MA). Permitted in April 2021, Seal Rock covers 50 acres where oysters are grown in wire cages on the bottom at 20+foot depth. In August 2021, BSS took over West Island Farm, a 46-acre farm adjacent to West Island (Fairhaven, MA). BSS possesses all licenses required to buy, sell and distribute shellfish nationally and internationally.
BSS operates a 20’x60’ processing barge, an 18’x30’ working barge, three work skiffs (19’, 21’ and 25’) and a 25’ work boat. Shoreside facilities include a processing/packaging area along with office and workshop. The three members of BSS represent approximately100 years of experience in aquaculture. Dr. Dale Leavitt oversees Blue Stream Shellfish LLC's efforts. Dale is an emeritus Professor/Aquaculture Extension Specialist (Roger Williams University, Bristol, RI) with >35 years’ experience farming shellfish. Through Dale’s outreach activities, he has assisted in training members of >50 shellfish farm start-ups in the northeastern U.S. Dale also maintained an active research program in aquaculture technology, including applying solar power to shellfish and finfish systems and improving shellfish hatchery/nursery protocols.
Cooperators
- - Technical Advisor (Researcher)
Research
Objective 1 - Identify the mechanical attributes of an ROV required to achieve the goals of maneuverability underwater, identification of unique bottom cage markings, and ability to attach a lifting line to a cage harness for retrieval:
Drawing on the expertise of our Technical Adviser (Molly Curran, Engineer II - Deep Submergence Laboratory - Woods Hole Oceanographic Institution), the BSS farm team developed a list of specifications that are required in the design of the OysterBot. These will cover details such as swimming speed/power and maneuverability of the ROV, resolution of the camera under ambient and enhanced light conditions, gripping strength of the robotic arm, ease of operation and other parameters that are deemed important during the design discussions. These criteria will be applied to the purchase and assembly of the OysterBot under Objective 2.
Objective 2 - Design and construct an ROV that meets the qualifications outlined in Objective 1 (i.e. the OysterBot):
BSS assembled a collection of off-the-shelf components into the OysterBot that allows the operator to locate and lift oyster cages in nearshore waters (15 to 30 feet depth). Using the design criteria compiled under Objective 1, the BSS farm team worked with our Technical Adviser to identify and purchase the components needed to assemble the OysterBot. Based on preliminary discussions, our Technical Adviser recommended that we investigate the components available through Blue Robotics (https://bluerobotics.com/). These are inexpensive but high quality components that are easy to assemble and operate and are routinely used by institutions such as the Deep Submergence Laboratory at the Woods Hole Oceanographic Institution (DSL-WHOI), where our Technical Adviser is employed as an Engineer II.
The one unknown in assembling the OysterBot was the design and operation of the robotic arm that attaches the line to the lifting bale on the submerged cage. It needed to securely hold the lifting line in position as it descends to the cage, attach the lifting line to the cage and subsequently release it from the ROV to allow the cage to be hoisted to the surface without tangling the ROV in the process. There were a few design options that were considered and a final design was selected in consultation with our Technical Adviser.
Objective 3 - Evaluate the OysterBot on a commercial farm to assess its capacity to replace surface lines for cage retrieval:
Initial training on operating the ROV took place at the shoreside processing barge facility at the BSS West Island Farm. Training included “how to” complete routine maintenance on the ROV, practice piloting the ROV and assessing its capacity to identify a marked cage and attach the lifting line to the cage bridle.
Evaluation of the OysterBot occurred at a BSS farm site. The site was an open nearshore farm in >10 feet of water. Initially, the general cage location was identified using a down/side looking sonar on the vessel. The sonar-based fish finder has been successfully used to locate bottom cages on BSS farm sites as part of a SARE funded Farmer’s Grant in 2021 (SARE Project Number FNE21-989). With the sonar, we located cages placed on the bottom as a preliminary indicator of the area for deploying the OysterBot retrieval system. We were able to clearly demarcate the location of large oyster cages on the bottom and, with integrated GPS, the precise location of bottom cages was observed and recorded.
The cages consisted of large wire mesh structures populated with 9 or 18 stocked oyster bags and initially weighing in the vicinity of >150 lbs. The cages were deployed in a set trawl line array on the bottom with approximately 20 feet of space between adjacent cages. In addition to those set up for OysterBot collection, we proposed to install an equivalent set of identical cages with conventional surface marker buoy. We proposed to install a minimum of 10 cages of each design to allow a comparison between the technologies in a replicated manner.
Once the location was identified by sonar, the surface vessel will deploy the OysterBot to identify a specific cage and attach a lifting line to the cage. The OysterBot provides real-time video imaging to allow the on-deck operator to read the cage identification on the marked bridle to assure that the correct cage is being retrieved. Once confirmed, the OysterBot will attach a lifting line that it carried from the surface and hook it to the short lifting bridle thus allowing the surface vessel to hoist the cage to the surface for maintenance or harvest. The handling of the cages will be completed with the BSS vessel (M/V Phoenix), a 18' x 30' powered work barge equipped with a hydraulic crane and a 10” electric pot hauler. The cages will be retrieved and handled approximately monthly to allow for maintenance on the oysters.
The goal for this study was to develop a ropeless retrieval system for oyster bottom cages in nearshore waters that works under all conditions. The successful completion of retrieving a bottom cage by ROV is the ultimate measure of success for the project. However, a primary consideration in comparing the two technologies (OysterBot vs. vertical line with buoy) is the time and ease of handling of each of the systems, from first identification of the cage to landing it on deck following retrieval. We will measure elapsed time for the full process of detection and retrieval for each of the cage systems for comparison between technologies. We will also maintain a log of observations in terms of ease of placement of the cage arrays on the bottom and ease/risk of handling while on deck with and without attached lifting line.
Objective 4 - Outreach this technology to other farms that are operating in nearshore waters.
BSS outreach effort targets new and existing farmers. Dale Leavitt is a retired Aquaculture Extension Specialist, formerly with Roger Williams University. In that capacity, for 24 years Dale has trained individuals associated with shellfish companies in the northeast through his annual Applied Shellfish Farming course. The course is offered online and attracted 100+ participants annually. This project will be featured in the oyster culture section of that course in March 2024. Additionally, Dale has collaborations with aquaculture extension agents and farmers throughout the region. He has gained these contacts through personal interactions over the past 30 years.
Our outreach will be introduced to farms in the region as BSS presents details of the OysterBot to industry members attending popular aquaculture meetings in 2022-24, i.e. the Northeast Aquaculture Conference and Exposition (NACE), the Milford Aquaculture Seminar, and/or the National Shellfisheries Association annual meeting (NSA). Dale will also prepare an article for inclusion in the East Coast Shellfish Growers Newsletter, published quarterly. Following those introductions, we will demonstrate the OysterBot and test the technology on a variety of farms in the northeast. BSS will visit any nearshore farm from Maine to New York that shows interest and invites us for a demonstration.bluerov2_datasheet_rev2022-R4ROV
Objective 1 - Identify the mechanical attributes of an ROV required to achieve the goals of maneuverability underwater, identification of unique bottom cage markings, and ability to attach a lifting line to a cage harness for retrieval.
Drawing on the expertise of our Technical Adviser, the BSS farm team developed a list of specifications that were deemed important in the design of the OysterBot. These specifications cover details such as swimming speed/power and maneuverability of the ROV, resolution of the camera under ambient and enhanced light conditions, gripping strength of the robotic arm, ease of operation and other parameters that were suggested as important during the design discussions. These criteria are included in Table 1.
Table-1_OysterBot-specs
Following evaluation of the OysterBot, which was constructed to meet the specifications outlined in Table 1, it was determined that the criteria established under Objective 1 were sufficient to produce a field ROV that was capable of providing the services required to complete this project.
Objective 2 Design and construct an ROV that meets the qualifications outlined in Objective 1 (i.e. the OysterBot);
In collaboration with the Technical Adviser, BSS assembled a collection of off-the-shelf components for the OysterBot. Using the design criteria compiled under Objective 1 (Table 1), the BSS farm team worked with our Technical Adviser to identify and purchase the components needed to assemble the OysterBot (Table 2). The bulk of the components were available through Blue Robotics (https://bluerobotics.com/) (Figure 1).
Figure 1 Blue Robotics ROV2 description.
The ROV components arrived in May/June 2022 and the vehicle was assembled, primarily by our Technical Adviser, through the summer/fall of 2022. Since late September 2022, the OysterBot has undergone a series of test dives in the ROV test tank affiliated with DSL/WHOI. Numerous operational bugs were corrected as a part of the testing series. In December 2022, the OysterBot was tested at a BSS farm site for further debugging (Figure 2).
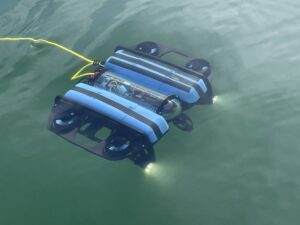
A critical factor in designing and assembling the OysterBot is the installation of the robotic arm that will carry the lifting line and attach the line to the bridle on the submerged cage. To allow the cage to be hoisted to the surface without tangling the ROV in the process, the arm will need to securely hold the lifting line in position as it descends to the cage, attach the lifting line to the cage, and subsequently release it from the ROV. Blue Robotics offers a gripper arm for their ROV2 and we purchased and installed it on the OysterBot.
During the process of identifying and ordering the components required to build a functional ROV and assembling the ROV, it became clear that this endeavor required extensive technical expertise and engineering skills. Considering that one is assembling a piece of equipment that is entirely dependent on electronic components then submerging that unit in highly damaging seawater at pressure, it is critical that every step in the assembly is not only meticulously completed but then tested to eliminate the risk of flooding by seawater. Often, the testing requires specialized equipment and/or test tanks for submerging the ROV at specific build intervals. Without the expertise, skill set and experience of our Technical Advisor, BSS would not have been able to design and construct the OysterBot from individual components as proposed. This does not preclude an oyster farm from utilizing an ROV for work on the farm as there are numerous preassembled models that are commercially available but it is not practical for an oyster farmer to design and assemble an ROV from scratch, as was successfully undertaken with this study.
Objective 3 - Evaluate the OysterBot on a commercial farm to assess its capacity to replace surface lines for cage retrieval.
Field evaluation of the OysterBot was completed at the BSS West Island Farm in Fairhaven, MA. This site is a nearshore farm in ~12 feet of water. Initially, a general cage location was identified using a down/side looking sonar on the vessel. The sonar-based fish finder has been successfully used to locate bottom cages on the BSS farms as part of a SARE funded Farmer’s Grant in 2021 (SARE Project Number FNE21-989). With the sonar, we were able to locate individual cages placed on the bottom to identify the area for deploying the OysterBot retrieval system. The cages consist of large wire mesh structures populated with up to 18 stocked oyster bags initially weighing in the vicinity of 200 lbs. and have been deployed in a set array on the bottom. We could clearly demarcate the location of large oyster cages on the bottom and, with integrated GPS, the precise location of bottom cages were observed and recorded.
During a routine field test, a cage location was identified by sonar and the surface vessel deployed the OysterBot to locate the individual cage. Because the OysterBot provides real-time video imaging, the on-deck operator was able to "fly" the OysterBot to the cage location and survey the cage positioning on the bottom (Figure 3) as well as trace the lifting bridle suspended at the top of the cage (Figure 4), to allow for attachment of a lifting line.
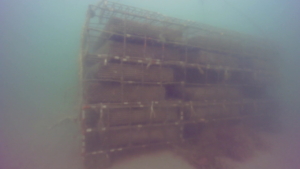
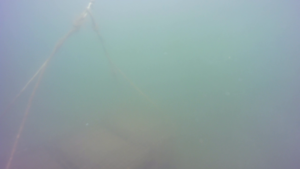
During the initial field test, it was extremely difficult to observe the video output of the OysterBot on the topside computer screen in an open boat under sunny conditions. During the initial trial, it was necessary to shroud the operator and laptop with a curtain to allow for adequate visibility of the screen. Subsequently, a set of VISIONHMD BIGEYES H3 head-mounted video glasses were evaluated for observing the video output of the OysterBot under daylight conditions. The video glasses interface with the computer control via a conventional USB port thus were simple to use and proved to be effective in allowing the ROV pilot to observe the scene projected by the OysterBot in open sunlit conditions.
In addition to locating individual large bottom cages, the OysterBot was also successful in locating a series of smaller oyster bags that had been accidentally lost overboard due to cage damage following a storm (Figure 5). In a third effort (Figure 6), the OysterBot was able to provide images of a series of derelict cages discovered when surveying the farm site with sidescan sonar, thereby allowing us to retrieve those cages as we were able to discern their positioning and accessibility.
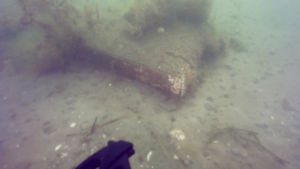
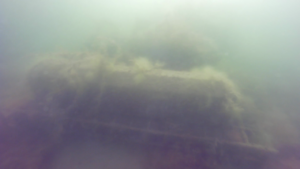
Initial field testing uncovered a few more bugs (e.g. the auto-depth setting on the ROV) that were corrected by our Technical Adviser at the DSL-WHOI test facility during the winter/spring of 2023. Subsequent tank and field testing through the summer of 2023 led to the final debugging of the mechanics and control of the OysterBot. As part of final testing, the OysterBot was loaned to the Sea Education Association to be used as a training platform for high school students interested in marine robotics (https://sea.edu/news-post/sea-teams-with-whoi-for-high-school-robotics-cruise/). The end result of that week-long training session at sea was an informational video outlining the session and featuring the OysterBot (https://youtu.be/ucOhXB63NdY).
Final training for operating the OysterBot occurred in the fall of 2023 where both proper handling and piloting of the ROV as well as required maintenance was covered by our Technical Adviser. As a part of the training, the final aspect of field evaluation included assessing the capacity of the OysterBot to carry an attachment line from the surface to the submerged cage and to attach it to the lifting bridle on the cage. To that end, a simple J-hook (Figure 7) was attached to a 3/8” Dyneema® line for lifting the cage. Dyneema® was selected because of its high tensile strength (3/8” Dyneema® has a tensile strength of 13,900 lbs. and is slightly buoyant). The J-hook was gripped in the arm of the OysterBot and carried to the cage where the J-hook was carefully engaged with the bridle of the cage. With a slight tension placed on the Dyneema®/J-hook line, the OysterBot gripper was released from the J-hook and the ROV was carefully reversed away from the bridle/lifting line combination. Subsequently, the cage could be lifted to the work barge for maintenance or harvest.
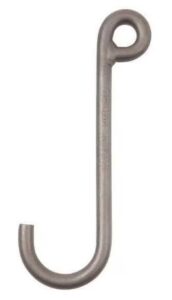
Due to unforeseen circumstances, the final testing of the OysterBot with retrieving cages at a commercial scale and comparing the performance of the OysterBot retrieval system to the conventional buoyed line could not be completed. The oyster survival and growth performance at the Seal Rock site proved to be subpar over the previous two years of using a bottom cage growing strategy. Because of that observation, the immediate use of the Seal Rock site was discontinued in the summer of 2023 to allow the owners to focus on maximizing the output of the floating cage system at the West Island Farm. BSS will revisit the Seal Rock site during the spring/summer of 2024 to continue research on making that farm site a productive oyster site. Currently, BSS is using the Seal Rock Farm to evaluate kelp culture.
Overall, the utilization of the OysterBot to carry forth and attach a lifting line to a submerged cage proved to be a successful effort. With that come a few caveats in terms of practicality for application in a farm setting. While we were able to detect cages from the surface with the sidescan sonar and subsequently place the ROV at the cage site, reading the tags attached to the submerged cage worked well until biofouling proliferated. To ensure long-term readability of the cage tags will require either routine cleaning of the cage tag, which may be a problem depending on the frequency of handling of an individual cage, or devising a tag label that has antifouling properties built into the tag. For example, fabricating tags of plastic and printed using an antifouling paint may keep the tag clear of fouling and readable by the OysterBot for an extended period of time.
Another consideration is the arrangement of cages on the bottom. As originally proposed, we anticipated dropping the cages along a trawl line in a somewhat straight line configuration. This proved to be more difficult than anticipated as the initial strategy was to use the trawl line as an anchor line with the barge holding tension on the trawl line as the cages were dropped heading down wind. However, two problems arose. First, if you have an array of multiple trawl lines on the bottom then you can only deploy lines when the wind is in the specified direction thus limiting your opportunity to place trawl lines in high density to only that time when the wind direction is favorable. Secondly, by using the trawl line as an anchor for deploying subsequent cages on the line, we discovered that we were flipping previously deployed cages onto their side and upside down with the drag from the surface vessel. While we could detect this event after happening with the sidescan sonar, it required us to remove and redeploy the trawl line to correct the situation. Subsequent to this realization, we dropped cages in groupings rather than straight lines where the trawl line was not used to anchor the surface vessel during cage deployment. However, that made it more difficult to identify specific cages from the sidescan image and subsequent ROV detection as numerous cages were grouped randomly in a relatively compact foot print.
Objective 4 - Outreach this technology to other farms that are operating in nearshore water.
As this project has progressed, the Principal Investigator has made presentations on the development and application of ROV technology for deeper water oyster farms. The presentations have included at the National Shellfisheries Association annual meeting in Baltimore, MD on 27 March 2023 (Title: Developing the OysterBot for oyster cage retrieval) and at the 2023 Smart Shellfish Aquaculture Summit in Grasonville, MD on 24 August 2023 (Virtual presentation title: Fun on the Farm). Additionally, the PI will be showcasing the OysterBot at a farm tour associated with the Northeast Aquaculture Conference and Exposition in Providence, RI on 10 January 2024. An article outlining the application of the sidescan sonar and the OysterBot is in preparation for publication in the newsletter of the East Coast Shellfish Growers Association and is anticipated to be published in the spring/summer of 2024.
At this point, the OysterBot is available for demonstration at individual farms upon request. That information will be included in upcoming presentations and discussions on the application of technology on developing shellfish farms.
In constructing and evaluating the OysterBot, we proposed to assemble a technology that would be available to any nearshore oyster farmer that wishes (or is required) to utilize a ropeless technology for their oyster cage retrieval process. With an initial cost of under $10,000, as a onetime expense, it is significantly less expensive than the pop-up buoys currently being proposed for trap fisheries. If it is regulated that ropeless technology will be required for oyster cages in nearshore waters in locations where there is a risk of megafauna entanglements (essentially the entire coastline of the northeast), this may be a viable alternative to other technologies.
In addition to the intended use for retrieving ropeless oyster cages from the bottom, it has turned out that BSS has identified numerous additional uses for the ROV on our farm site. We have used the instrument for locating derelict gear on the bottom, for locating lost bags of oysters that were dropped either accidentally or from storm related damage, for assessing the orientation of bottom cages that may have been flipped due to mishandling or storm impacts, for visual inspection of mooring chains/lines for corrosion/abrasion and assessing need for replacement, and for other activities requiring visualization of conditions in deeper water sites where direct observation from the surface is not practical. The OysterBot has become a valuable addition to our toolbox for managing our deeper water oyster farm.
As the project has developed, there have been a few observations that seem relevant at this point in time. It is important to note that the components to be used for assembling the OysterBot are off-the-shelf technology that is non-proprietary in its application and readily available. However, it became obvious that assembly of an ROV from component parts is not something that can be routinely completed by an individual with limited experience in mechanical and electronic assembly. The levels of cleanliness and attention to detail required during construction may be problematic for an inexperienced assembly person. Furthermore, debugging the assembled OysterBot has proven to be necessary as mechanicals, firmware, and software controls need to be adjusted for the individual build. While these tasks are not insurmountable, it does take a technical person to make these final adjustments and, again, are probably not achievable by an inexperienced assembler.
As an alternative, there are a number of off the shelf ROV units that are commercially available and that would be a viable substitute for the OysterBot. One that was initially considered for this project is the Deep Trekker DTG3 (https://www.deeptrekker.com/) with two-function grabber arm. While these ROVs may be more expensive than the component-built Blue Robotics derived OysterBot, a turn-key ROV will sidestep the need for assembly and testing.
Education & Outreach Activities and Participation Summary
Participation Summary:
- Conducted a tour of the farm and discussed OysterBot application with NOAA Northeast Regional Aquaculture Extension (Zach Gordon) and MIT Sea Grant Aquaculture Extension (Danny Badger) on 9 November 2022.
- Discussed project with University of Maryland Shellfish Aquaculture Technology Specialist (Allan Pattillo). Dr, Pattillo invited us to present at the upcoming Robotics in Aquaculture session at the National Shellfisheries Association annual meeting in Baltimore, MD in March 2023.
- Presentation at the National Shellfisheries Association annual meeting in Baltimore, MD on 27 March 2023 (Title: Developing the OysterBot for oyster cage retrieval)
NSA 2023_Developing the OysterBot for oyster cage retrieval
Slide deck for the NSA 2023 presentation.
- An informational video highlighting a robotics for high school SEA cruise and featuring the OysterBot.
(https://youtu.be/ucOhXB63NdY).
- Presentation at the 2023 Smart Shellfish Aquaculture Summit in Grasonville, MD on 24 August 2023 (Virtual presentation Title: Fun on the Farm)
Slide deck for the Smart Shellfish Aquaculture Summit
- Will be showcasing the OysterBot at a farm tour associated with the Northeast Aquaculture Conference and Exposition in Providence, RI on 10 January 2024.
- An article outlining the application of the sidescan sonar and the OysterBot is in preparation for publication in the newsletter of the East Coast Shellfish Growers Association and is anticipated to be published in the spring/summer of 2024.
Learning Outcomes
The outreach associated with this project provided an awareness of ROV technology and the potential uses of this technology on a working oyster farm. Following every presentation that I made , I was approached by attending shellfish farmer's inquiring about the technology. While the technology may not be appropriate for all shellfish farms, the growers were made aware of the technology and were able to judge whether this was something that they should incorporate into their normal operations.
Project Outcomes
With the availability of the OysterBot on BSS farms, we have used the ROV for numerous applications over and above the original intended purpose of retrieving ropeless bottom oyster cages. While BSS is not currently deploying bottom cages at its Seal Rock site, we anticipate that we will recommence placing them on the farm during the spring/summer of 2024. At that time, the OysterBot will be evaluated for its application in retrieving bottom cages along with the multiple other uses already instituted on our farms. Overall, the OysterBot has evolved into a “must have” tool for BSS as it manages its deeper water farms.
As suggested above, proposing to construct an ROV from component parts turned out to be much more involved than the Principal Investigator initially envisioned. In retrospect, it would have been more practical to purchase a turnkey ROV with the attributes listed in Table 1. Having the ROV ready to go at the start of the project would have left more time for evaluation and less time expended for assembly and debugging the systems. This is especially true during the interval when this project was undertaken (COVID years) where supply chain issues delayed the program on a number of fronts. Additionally, it would have required much less involvement of our Technical Adviser, who committed significantly more time and resources to the project than was budgeted and paid for. Molly Curran was and continues to be a huge support to our continued operations of the OysterBot on the farm.
Having an easy to use ROV on shellfish farms that exist in deeper waters is turning out to be a valuable asset to farm operations. Given the myriad of uses conceived for the ROV, mostly centered around visualizing conditions on the bottom of the farm, it has become an important tool for our operations. It precludes the necessity of placing SCUBA divers in the waters, which is always a risky proposition especially under winter conditions. An unmanned vehicle to observe and potentially manipulate apparatus on the bottom of the farm, when in 10 to 20 feet of water, simplifies our ability to better manage the farm. I would envision the application of ROV technology, either individually on deeper water farms or collectively available in a region, becoming a standard practice in future years.