Final report for FW18-028
Project Information
The objective of this research project is to test and measure the energy impact of capturing excess daytime heat within a greenhouse and transferring it through an air-to-water exchanger to then store the thermal energy in water. Solar collectors will also be implemented to boost the heat that is stored. This same system will provide cooling during the day and heating at night for the greenhouse. The stored heat will be used to help reduce costly energy consumption that negatively impacts the environment and decreases farm profitability.
- To research the process of capturing daytime air heat of a greenhouse and exchanging and storing it into water.
- To research the effects of solar hot water collectors in combination with the heat exchanger to increase the temperature of water storage.
- To research the effectiveness of using the stored heat in water as a heat source during the night.
- To visualize the system with sensors and data logging technology.
- To publish findings of this research and encourage its adoption.
Research
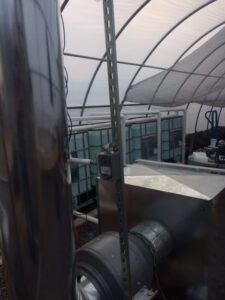
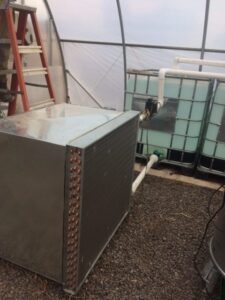
2018
To start this project, we installed a 3x3 ft. air-to-water heat exchanger and a 12 in. centrifugal fan rated at 2,050 CFM within our 20 x 48 ft. arched greenhouse (9,048 cubic feet). A custom duct was built from sheet metal in order to house the air-to-water heat exchanger and the centrifugal fan.
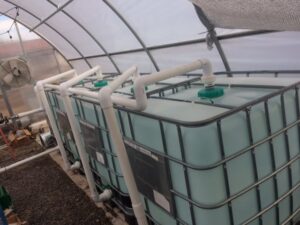
A 1/25HP circulation pump was installed to cycle the water between the storage tanks and the exchanger. The four IBC totes full of water were initially installed in serial so that water would cycle through the heat exchanger and all the tanks.
An off-the-shelf weather station was setup outside the greenhouse which allowed for additional wireless thermometers to monitor the system for both air and water temperatures within the greenhouse. The wireless sensors had difficulty communicating to the weather station because of interference created by the sheet metal of the ducting and the metal (copper tubing & aluminum fins) of the heat exchanger. The entire weather station’s receiver later failed so no data was able to be captured in 2018.
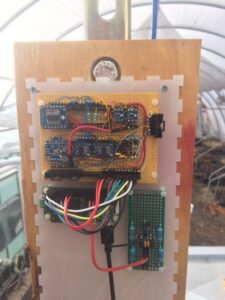
2019
After dealing with these issues with the wireless weather station, it was determined that the best approach would be to use wired sensors. The cost of many of the available commercial sensors and data loggers were cost prohibitive to the project so it was determined that it would be best build our own with the help from electronic specialist. A new monitoring system was developed using electronic parts and a Raspberry Pi for the data logger. The data could be seen in real time and graphed by downloading the database from the Raspberry Pi.
The initial plumbing in a serial setup for the tanks created a vacuum that crushed one of the tanks so the plumbing was modified to a parallel setup with valves to control the water flow into each tank to get the flow evenly distributed. The plumbing was put together with a combination of PVC and polyethylene irrigation tubing.
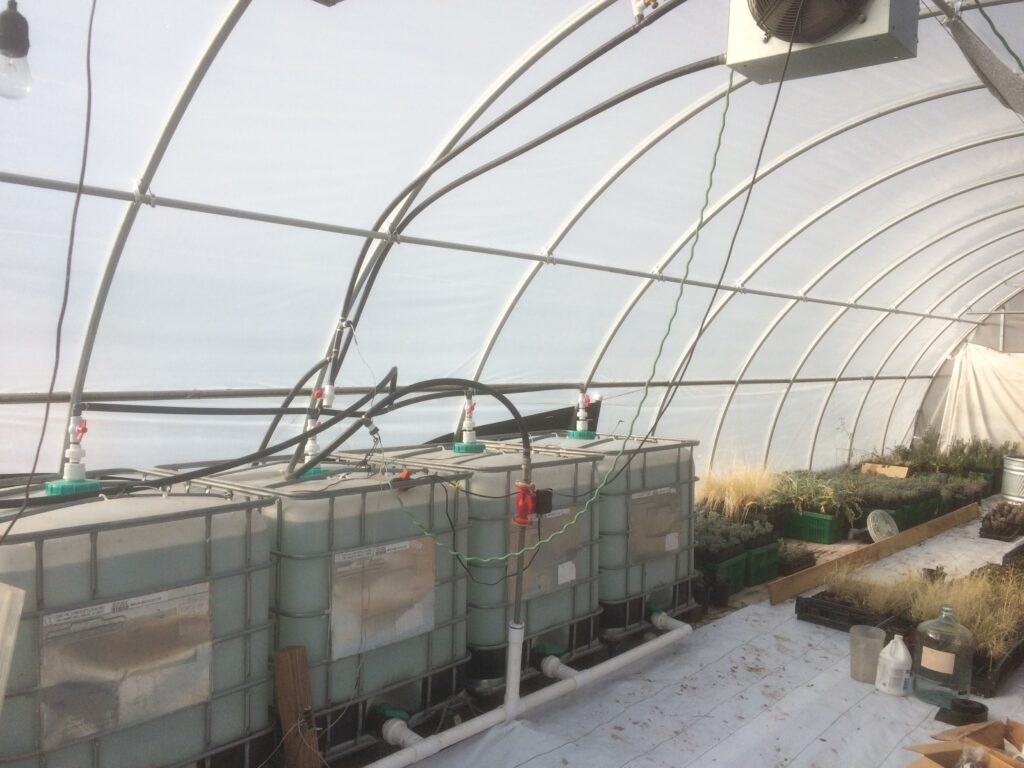
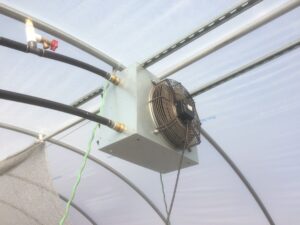
During the setup process for the new sensors the greenhouse was inadvertently left without power during the Winter which allowed the 3x3 heat exchanger to freeze overnight. The damage to the copper tubing was too extensive to repair so the unit was replaced. In talking with a company that sells air-to-water heat exchangers they recommended replacing the duct work and fan with a combined unit rated for 100,000 BTU which could be mounted at the ceiling of the greenhouse.
The solar hot water collector for a pool was installed but had warnings about freeze damage and because the system was using water instead of an anti-freeze it was decided to setup the collectors within the greenhouse. This reduced their solar capacity because of the plastic covering of the greenhouse diffuses some of the solar energy. They did still provide heat generation to the water which improved the night time heating capacity but at the same time it reduced the daytime cooling capacity of the air-to-water exchanger. We didn't find these to be vastly beneficial to the system.
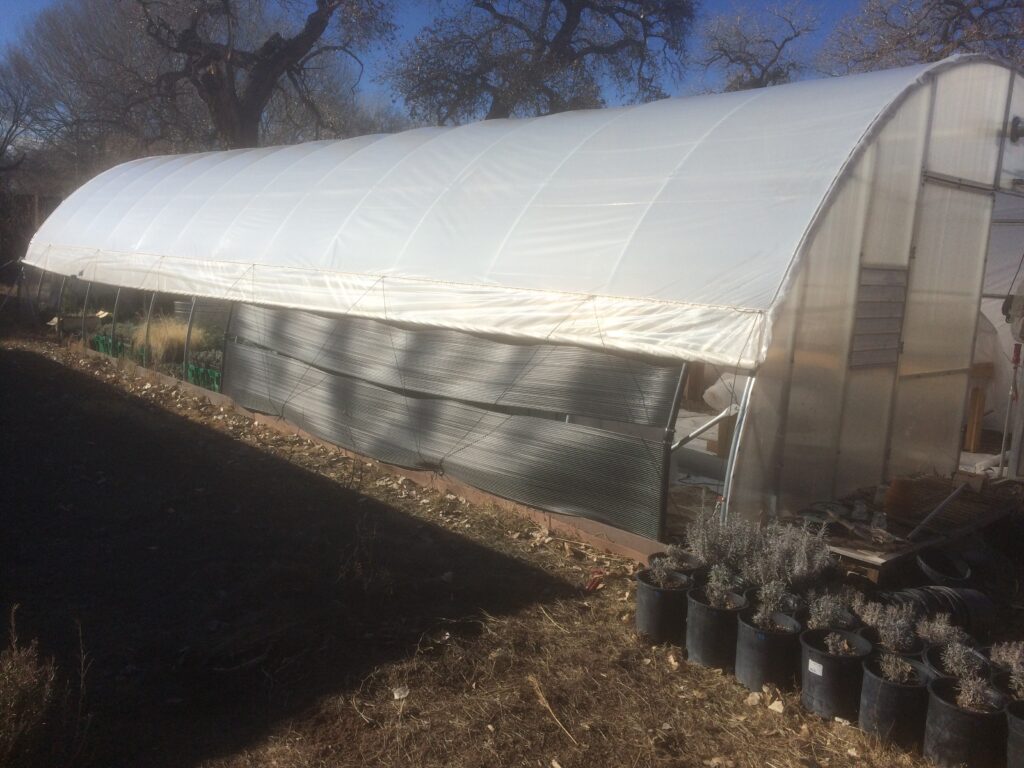
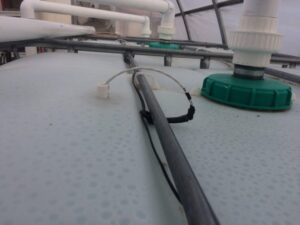
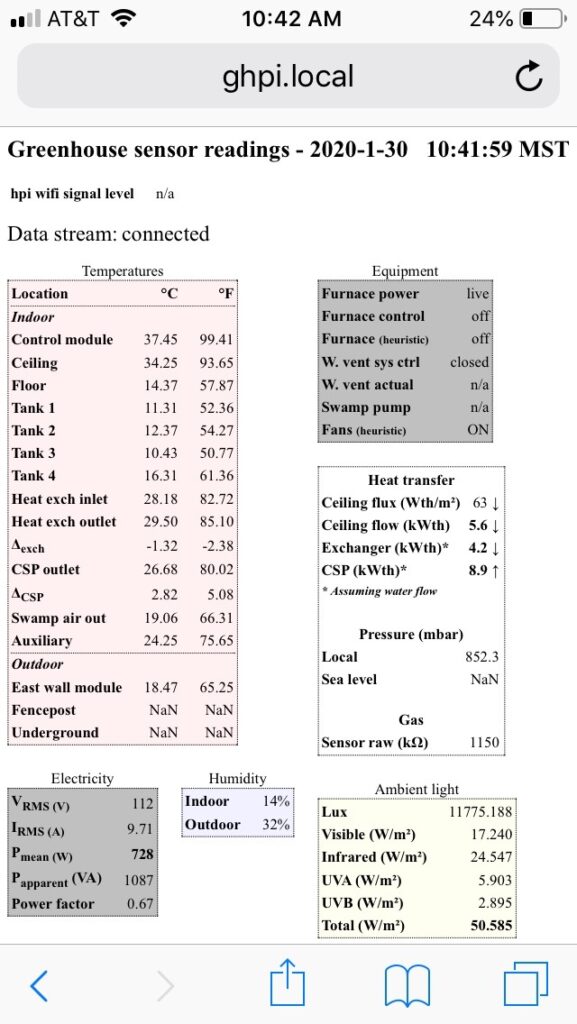
2018
We setup an initial test of the system in June 2018 which provided a 40F temperature reduction from the air at the top of the greenhouse (115F) to the air released after the heat exchanger (75F). A single 275 gallon IBC tote was filled with 58F water and cycled through the 3x3 ft. heat exchanger for 2 hours with the cooling effect during the day. It increased the temperature of the water to 80F.
The 2 hours of operation allowed for a 1.2 kilowatt reduction of energy to operate the centrifugal fan (500 watts) and 1/25 HP circulation pump (82 watts). This is compared with the normal energy consumption to cool by powering two exhaust fans (500 watts/ea.) and a water pump (190 watts) for the evaporative cooler. This is a 51% reduction in energy consumption over the conventional cooling system for the greenhouse.
2019
The rebuilt air-to-water system was logged and proven to be able to provide 1 therm of cooling during the day and 1 therm of heating at night. To operate the system the water pump and fan collectively used 181W / (1000W/kW) * 24hours/day * $0.15/kWh = $0.65/day of electricity to operate.
It was calculated that the energy savings of the system by reduce usage of the exhaust fans (1000W for 3.45 hours = 3.45kWh * $0.15/kwh = $0.52/day) during the day for cooling and reduced usage of the gas heater at night by 1 therm (100,000 BTU). The operating cost for that therm by the gas heater was calculated at $.03 for electricity to run heater fan plus $0.59 for the gas consumed = $0.62/day.
The total cost of energy saving was $1.14/day minus $0.65/day for operation equals a cost savings of $0.49/day in energy usage. The overall saving of the system is $178.85/year.
Research Outcomes
Education and Outreach
Participation Summary:
The data from the custom built logger and sensor array will be shared online and we will be working towards publishing the designs of the system and sharing this for an article. It was hoped that the electronics could be offered as open source designs but they proved to be fairly complicated that it may be hard to replicate without a solid understanding of electronics and soldering.
Education and Outreach Outcomes
Without data monitoring it's very difficult to understand energy consumption within a greenhouse.