Final report for FW21-375
Project Information
The mango loa project is a continuation of project FW17-034 and will carry on the objectives into the production years.
Hawaii used to have a robust agriculture based economy that has slowly been replaced by tourism. Even before Covid-19, we the people of Hawaii have been voicing the demand to have a more balanced and diversified economy, by rebuilding and growing our agricultural industries. Tree crops like mangoes, avocados, and citruses have been identified as having great potential. According to the most recent national agriculture statistics, Hawaii reported producing 270,000 lbs. of mango in 2017, while importing millions of pounds from Central and South America.
The mango loa project’s goal is to improve Hawaii’s mango industry by incorporating two new innovative high density orchard management systems that have been completely changing tropical fruit production around the world. These systems are the ultra high density plantation and the open Tatura trellis systems.
With the conventional mango orchard, a realistic expectation of production is two to five tons/acre. The two new systems mentioned above have been producing eight to twenty tons/acre. Aside from that, these systems are a more efficient use of land, natural resources, and inputs; it reduces the demand on labor; and has a quicker time to production. Utilizing these high density systems have the potential to double Hawaii’s mango production with just 20 acres.
The project will be disseminated through farm field days, farmer to farmer tours, online events, power point presentations, videos, posters, and networking.
The objectives of this project is to demonstrate two high density orchard management systems and report on the harvest and production of these systems. another object is to demonstrate harvest and post harvest practices to preserve the quality of the produce. The educational objectives is to reach Hawaii's tropical fruit farmers and professionals and make them aware of these new innovative techniques that have been improving the yield and quality of tropical fruit production, improving profitability, and improving the quality of life of farmers.
October 2021 start project
November 2021- Hawaii Ag Conference- PowerPoint presentation, poster, and networking
January 2022- build mango wash station
February 2022- set up the cold storage unit
March 2022- Erect framework for the netting demonstration
April 2022- Field day for the orchard update and new aspects of the project
April 2022- KCC garden fair- poster presentation and networking
June 2022- Document all aspects of the harvest with videos
August 2022- Waipa Mango Festival: networking and poster display.
September 2022- Hawaii Tropical Fruit Growers conference Maui: PowerPoint presentation on project.
November 2022- Post-harvest Pruning video.
April 2023- KCC garden fair: display poster and networking
June 2023- Field day during harvest to update the orchard and demonstrate the different aspects of the project.
August 2023- Waipa Mango Festival: Display poster and network.
September 2023- HTFG Kauai. Update project, display poster, and networking
October 2023- Final
Cooperators
- - Technical Advisor
Research
The mango loa project is a continuation of project FW17-034: it incorporates two high density mango orchard systems on one acre of land. The first system is the ultra high density plantation (uhdp) method; this is a standalone orchard with 310 trees on a little more than a half acre field, this field is three years old and a good harvest is expected this summer, 2021. The second is the open Tatura trellis system that incorporates a unique V-trellis design, and has 300 trees on a half acre field. The trellised field is nearing two years in the ground and the first full season of production is expected summer, 2022.
The first objective of the mango loa project is to observe, compare, and document the progress of the two different high density orchard systems. This includes the pruning and training time requirements; the growth cycle, flushing, flowering, fruit development, and harvest; nutrient and pesticide management; and harvest and post-harvest procedures. Timed observations will utilize a stopwatch, and all other observations will be documented using a notebook, videos, and pictures. Materials needed here will be small tools; pruners, saws, and harvest poles, vinyl tape, trellis clips, wire tensioners, as well as other small miscellaneous tools.
The next objective will focus on protecting the fruit from bird and insect damage. A beneficial factor of the high density systems and the low bearing trees is the ability to cover the orchard with crop-netting, this provides three benefits; it keeps fruit flies away from the fruit, blocks birds pecking and damaging crops, and provides just a bit of shading to reduce excessive sun exposure. We have four major fruit flies in Hawaii that cause millions of dollars in damage to fruits and vegetable crops. There are integrated pest management plans to suppress the fruit fly population around your farm and these will be practiced; this includes trapping, baiting, and sanitation in the field. However, if other farms in the area do not follow the same practices, its’ effectiveness is limited. Kauai has many fruit loving birds that also adversely affect marketable fruits. One in particular is the Rose ringed parakeet, a newly established species that is starting to have devastating effects on many tree crops. Netting the fruit trees may be the only way to truly ensure a high quality crop. We will use crop netting on two trellised rows and two uhdp rows to demonstrate its effectiveness in mitigating damage caused by birds and insects. Materials needed for this objective are: crop netting, poles, concrete, and cables, small hardware will be needed to aid in attaching cable to framework.
The another objective is to mitigate the damage caused by sap burn on mangoes during harvest. Severe sap burn makes the fruit unmarketable, while low level sap burn makes the fruit more susceptible to disease infection and lessens the shelf life of the fruit. It is essential to neutralize the mango sap with a wash at harvest time to prevent losses due to sap-burn. There are two ways to de-sap mangoes; first is to pick the mango and immediately neutralize the sap with a mango wash in the field. This requires a station that will have a tank to hold the wash, a pump and sprayer to facilitate washing, tarps that will be used to guide the washed mangoes into another tank until it is removed and put in crates, ready to go to the packing house. The other way to reduce sap-burn is to pick the fruit with a couple of inches of stem on, this is above the sap ducts and will not ooze sap. The fruit is packed in crates and taken to an area where the stems are removed, the sap is neutralized and allowed to de-sap before it is washed and packed for sale. The mango loa project will build these stations and demonstrate how preventing sap burn. The materials needed to complete this objective are the materials to build the in-field station mentioned above and the objective will be documented with video and pictures.
The final objective will be to build a simple cold storage unit that will delay the ripening of fruit and allow the farmer to extend its’ shelf life, allowing more time to sell their fruit. The cold storage unit will be built out of an insulated shipping container, with a window air conditioner, and a Cool Bot external thermostat used to regulate the temperature of the air conditioner. Mango ripening can be delayed if stores at 50-55 degrees Fahrenheit. This is important to maximize profitability. Peak mango season lasts about six weeks and there is usually a surplus of fruit on the market. During heavy cropped years the price plummets forcing farmers to undervalue their crop. Mangoes can be stored for as long as 6 to 7 weeks, however there will be some diminished fruit quality. This added time will give farmers the flexibility to delay sales during a surplus time and release their product when the demand increases. A cold storage unit is also critical to farmers who wish to process their fruits into value added products, giving them the ability to ripen the fruits depending on what they can process.
The ultimate goal of the mango loa project is to improve Hawaii’s mango industry by incorporating new innovative high density orchard management systems that have increased the yield and quality of harvested fruit. However, increasing production is not enough, equal importance must be placed on proper protection, harvesting and storage of the fruit to maximize profitability and reduce waste. This is what the mango loa project aims to accomplish.
A Quick Project Recap of The Mango Loa Project , click the link for the entire playlist for more details.
The Ultra High Density Plantation (UHDP) techniques were developed in India, where they started a program to train new farmers using this orchard management system; however other areas have incorporated these practices such as Australia, Israel, South Africa, Japan, Florida, California, and Mexico. There is no set density that makes an orchard high density or ultra high density, but the principal investigator considers anything above 300 trees per acre as ultra high density.
The open Tatura trellis system was developed in Australia for temperate zoned fruits and began being adapted to tropical fruits in the early 2010’s. This system consists of two posts set 20 inches apart forming an open “V” and trees are planted along each side of the trellis.
The search for an alternative orchard management system for Hawaii’s fruit growers was driven by the desire to take advantage of the popularity of mangoes and to increase our mango production to meet this rise in demand. It was important to find a system designed for small farmers that may lack the labor force, the large expensive equipment, or land and natural resources that the larger mango orchards across the world have access to. One of the most attractive aspects of high density orchard management systems is that it reduces the demand on labor; most work is on the ground with hand tools and can be managed by one person. Also, these systems have shown to improve the quality and yield of the harvest for small farmers. We will evaluate this point and a few others that were identified at the beginning of the project and the results after 5 years.
The conventional mango orchard has a tree spacing of 25 feet by 25 feet or 50 trees per acre and the mango trees are maintained at a 15 to 20 feet height. Yields are around five tons per acre.
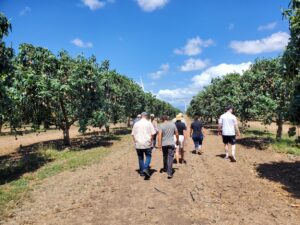
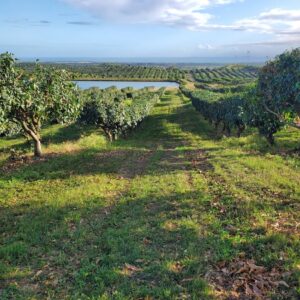
The uhdp field consists of 310 trees on a .7 acre field, for a density of 450 trees per acre. The spacing is 8 feet in row by 10 feet between rows and the trees are maintained at a height of 8 to 10 feet. The orchard is in its’ fifth year and most of the trees are full size, except for trees that needed to be replaced.
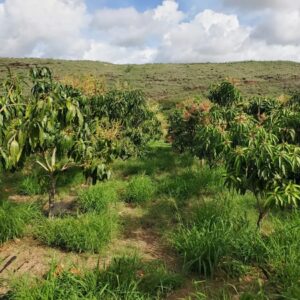
The open Tatura trellis field has 300 trees planted on a half acre for a density of 600 trees per acre. The trellises are 240 feet long with 30 trees planted on each side of the trellis. Each trellis has five wires that branches are secured along; the top trellis wire is set at an eight feet height and the trees are spaced eight feet apart. The trees in this field are in its fourth year and have been in production for two years.
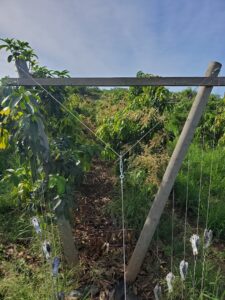
Quicker time to full production
An overview of the uhdp system; part 1 and part 2
The time to full production using the UHDP system is 3 to 5 years where the conventional mango orchard reaches full production at 7 to 10 years. The quicker time to production is due to the high density planting. If you have a one acre field that is planted with 450 trees versus the conventional density of 50 trees per acre, at year three the UHDP field will have about 75% canopy coverage over the acre while the conventional field will have less than 50% coverage. Also, at three years the UHDP trees are at or close to full size and are allowed to set fruit, while in the conventional field, the trees are still developing the structure of the canopy and fruit production is not the priority. Looking at the potential harvest between these two systems after three years; if you average 50 mangoes per tree, the uhdp field has the potential to harvest over 20,000 pounds, where the conventional field will be harvesting around 2500 pounds. However, when the conventional field reaches full maturity the difference in yield becomes less. With that said, there are a lot outside variables that can affect or delay the development of the orchard. In Hawaii, feral pigs are one of those variables.
Open Tatura trellis videos: trellis and trellis pruning
The open Tatura trellis system began production earlier than the uhdp field. One reason for the quicker time to production is because the damage caused by feral pigs in the trellised field was less extensive than the uhdp field. After two years, the bottom two to three wires were completely filled out and were allowed to carry fruit, even though the remaining two wires were still filling in the space. So, overall the open Tatura trellis field began production earliest, but still needed more time to completely fill in the allotted space.
Increased quality and yields per acre
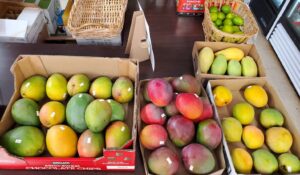
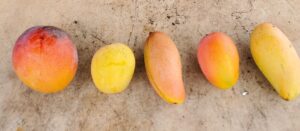
Many factors attribute to improved quality and increased yields; water and nutrient management, increased sunlight and airflow through the canopy, pest management, harvest and post harvest practices to name a few. Pressurized irrigation is a requirement for the UHDP system. Having a drip or spray system is the most efficient and is necessary for the fruit to develop optimally. The irrigation system is also used to deliver water soluble nutrients directly to the root zone, which is more economical and requires less labor than broadcasting granular fertilizers. Increased sunlight distributed evenly throughout the canopy stimulates flowering, provides the energy needed for proper fruit maturation, and enables the development of the great colors that make mangoes so attractive. Pruning to open up the canopy for better airflow through the orchard can reduce damage caused by powdery mildew, anthracnose, scales, mealy bugs, and other pests and diseases that can find shelter within the canopy. Harvesting by hand at eye level allows for better selection for ripeness and avoids the incidental damage caused by the mango picker. So, ultimately it takes a highly efficient well organized orchard management system to improve the quality and yield of mango production, and the high density orchard management systems are that. However, the opposite is also true. If the irrigation and nutrient management is subpar, if pruning is insufficient, or if pest management is inadequate, then this system will not work and quality and yield will be depressed. Here are a few pictures of damaged fruit.
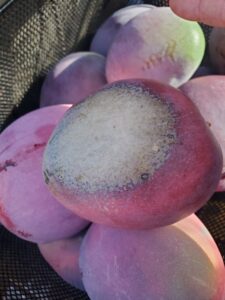
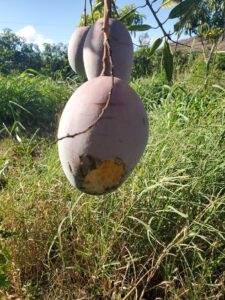
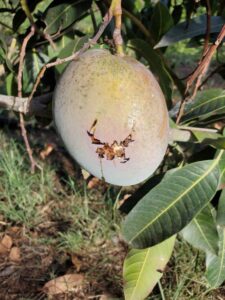
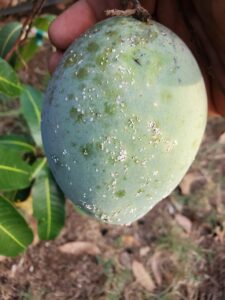
Improves canopy observation and management
Maintaining the trees at 8 to 10 feet allows the farmer to observe and manage the canopy of the orchard in a way that conventional mango farmers are not able to do. This is true for every aspect of the UHDP and the open Tatura trellis system from planting to harvest.
Reduced demand on labor
A major factor for adopting the Ultra High Density Plantation system as well as the open Tatura trellis system is a reduction in the demand on labor, in that one person can maintain multiple acres singlehandedly. All work is done from the ground with hand tools and no heavy equipment is needed in the process other than a lawnmower. Pruning is intensive, time consuming, and time sensitive. So, while no expensive specialized equipment is needed in maintaining the UHDP orchard, it is still a lot of work hand pruning and at this point on the farm, it is a challenge for one person to get through three acres of mangoes in a timely matter. In this trial, the open Tatura trellis system requires more work training the branches on the wire and shaping the trees into the two dimensional canopy that is desired, but once the branches are secured along the wires, the difference in time to manage the uhdp field versus the open Tatura trellis field becomes less significant.
Easier harvest and post harvest management
The most significant difference between the high density orchard systems versus the conventional orchard is in harvesting. Picking mangoes is fast when done by hand. The ability to hand pick allows the picker to be very selective, ensuring that the fruit is at the right maturity level. In Hawaii, there can be as much as three different sets of fruit on the tree at the same time and the harvest spans over a three to five month period. Harvesting by hand reduces damage caused by scratching the fruit and knocking down adjacent fruit by the pickers. So, there is a tradeoff between the demands on labor needed to maintain the pruning of the orchard for the lessened demands on labor during the harvesting period.
The ability to protect the trees using netting
An important factor that emerged during the trial is the need to protect the crop from fruit eating birds, insects and mammals. More farmers are beginning to incorporate netting in the orchard to protect their crops from birds. In the last couple of decades, Hawaii has seen the population of the rose-ring parakeet explode and the tropical fruit farmers are facing the brunt of the damage caused by these birds. As a result, farmers have been reducing the height of some of the taller fruit trees like mango, lychee, longan, and avocados in order to cover the trees with netting.
This fits right in with the high density orchard management systems. Both the uhdp and the open Tatura trellis system with the make it easier to cover the trees in order to protect the fruit from birds. The netting being used is citrus netting that has 2mm eyelets and not only does this netting protect the fruit from birds, but the small eyelets are enough to also keep out fruit flies, which is another pest that plagues Hawaii’s fruit farmers. An additional benefit of this netting is that it can provide a little bit of sun block for newly planted trees, giving them relief from the hot summer sun when establishing itself in the ground. The Open Tatura trellises have the framework already built in and it is fairly easy to cover the entire trellis. The uhdp field can also be covered with the netting sitting right on the trees or “T” frames can be erected every 50 to 60 feet with cables running along the outside keeping the netting off of the trees, therefore reducing damage that may be caused by the netting, like rubbing.
Production
As stated earlier, the easiest way to increase production is to choose a productive variety. There are thousands of named varieties of mangoes throughout the world, but only a small number has the characteristics needed to be profitable to the farmer. The uhdp orchard is effective at growing mangoes, but will not make an unproductive variety productive. The global average for mango production is 3.5 tons per acres and in the conventional mango orchard 5 tons per acre is a reasonable expectation.
Ideally one variety of mango would be planted in each block, however for this trial we wanted to test a few varieties to see different results. In the uhdp field there are four rows of “Keitt”, three rows of “Rapoza”, and three rows of “Manzanillo” mangoes. The open Tatura trellis field has two rows of “Keitt”, three rows of “Nom dok mai”, and five rows of “White Pirie”. This has given us the ability to see how different varieties do in the high density setting.
The “Keitt” is a Florida variety, is one of the most widely grown mangoes around the world, and has many good characteristics for commercial production, namely it is a late season mango, has good shelf life, it regularly bears fruit, is very consistent, and productive. I’ve visited a conventional mango orchard that was harvesting 8 to 10 tons per acre, triple the global average. In my fields, the “Keitt” mango has been the most productive variety of mango averaging over 60 mangoes per tree. In the high density orchard system, this would be over 16 tons per acres, a pretty significant increase over the conventional orchard.
the “Rapoza” is a Hawaiian variety that has become the most widely grown commercial variety in the islands. It is a moderately growing tree that produces large beautiful mangoes, is a regular bearer, and is resistant to some of the diseases that effect mango production. This mango is really consistent and usually has two harvests a year, one large harvest in the summer and a smaller harvest in the winter. These trees have averaged around 40 mangoes per tree. This equates to over 10 tons per acre.
“Manzanillo” is a seedling from a "Haden" mango that was selected in Mexico. This variety produces large beautiful fruit with gorgeous coloring, has no fibers, and a small seed. It is not widely planted in a commercial setting, maybe due to the large size about 2.5 pounds per fruit, but is a high quality mango. So far, the production has been very similar to the "Rapoza", averaging about 40 mangoes per tree.
The “Nom dok mai” is a very compact, slow growing mango tree. is is a high quality Thai mango the is commercially grown throughout the world. This mango also has two harvest seasons, produces a beautiful yellow fruit that is very sweet, has little to no fibers, and a paper thin seed. This variety has been a little inconsistent but when it does bear fruit, it has anywhere from 30 mangoes to 200 mangoes, so has the potential to be a prolific producer.
The “White pirie” is a West Indies mango that came to Hawaii in the late 1800's and has been a local favorite ever since. This tree produces a medium sized yellow fruit that is very fragrant and exceptionally sweet. It is known to be a shy bearer and is susceptible to powdery mildew and anthracnose, two diseases that can severely reduce production. This mango tree has been the most work to set fruit, needing multiple applications of fungicide during the flowering season. So, far this mango tree averages about 25 fruit per tree, but is a smaller mango, so produces maybe 4 to 5 tons per acre. This is better than the global average, but significantly less than the other varieties in this trial. The "White Pirie" is an example of a mango that has exceptional flavor and is beloved, but would be a challenge to turn a profit.
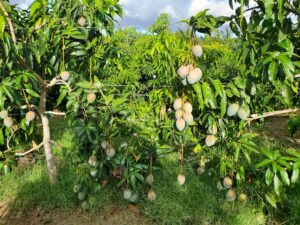
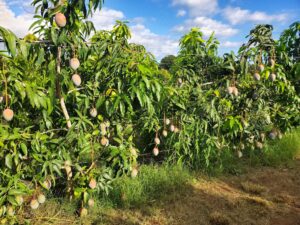
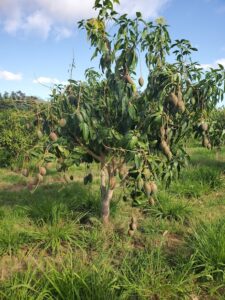
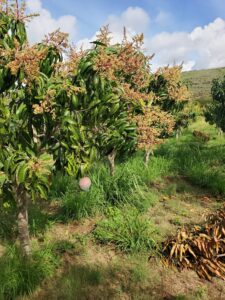
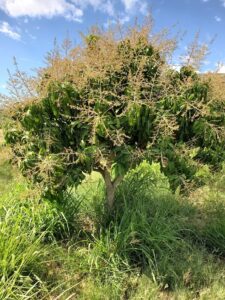
Research Outcomes
2023 Final
Hawaii has never been able to develop a significant mango industry; in fact, here is a report on mangoes http://www.ctahr.hawaii.edu/oc/freepubs/pdf/B-12.pdf done in 1906 that outlines the steps we would need to take to establish a mango industry that is still mostly relevant today. In my opinion, one of the primary reasons Hawaii has not been able to get a mango industry going is that most of the prime agricultural land was locked up by the sugarcane plantations and the only lands available were marginal lands that were too rocky for sugarcane with no irrigation. Now that the sugar industry is gone, there are prime agriculture lands available and diversifying into mangoes seems like a realistic pivot.
Another reason we have not developed our mango industry is that our population is small with 1.3 million people across seven islands and 1 million people on Oahu alone. We are also rural and there are many mango trees being grown in people’s yards as well as along the sides of the roads that provide for our local communities. What has changed today is that we have a thriving tourist industry that brings in over 10 million visitors throughout the state annually. Kauai Island, where this project was conducted has 65,000 residents and around 30,000 tourists visiting each day. The demand for mangoes and other tropical fruits is continuing to increase, and visitors to our islands want to eat locally grown tropical fruits during their stay.
So, we know that there is a high demand, by the amount of mangoes being imported and sold through box stores like Costco, and we know that we can grow a better product than any mango that is shipped to Hawaii. However, our tropical fruit farmers have developed a less than good reputation for poor quality fruits as well as an inconsistent supply, and there is a lack of trust between the local farmers and the fruit distributors. We are also on the low end for mango production. The FAO says the world average for mango production is 3.5 tons/acre, and with great practices and varieties you can expect 5 or more tons/acre. In Hawaii it may range from 0 to 5 tons/acre depending on the weather. The goal of the Mango Loa Project was to introduce techniques that can help our farmers consistently produce upwards of five tons/acre of high quality mangoes.
The Mango Loa Project began in 2017 with the goal of improving Hawaii’s mango industry by demonstrating an alternative orchard management system to increase production mango loa project phase 1. Two different high density orchard management systems were used: the ultra high density plantation (UHDP) technique and the open Tatura trellis system. These two systems have shown to increase the yield and quality of the mango harvest in other parts of the world, while reducing the demand on labor; all work is done from the ground, only requires hand tools (prune and saw), and hand harvest at eye level or with a short picker. The trial began by planting 310 trees on a little over a half acre using the UHDP method. That was followed up the next year by planting 300 trees on 5 open Tatura trellises on a little under a half acre. This was phase 1 of the Mango Loa Project; planting 2 half acre fields of both high density orchard management systems and evaluating the installation and management of the orchard over 3 years leading up to harvest. Phase 2 of the project was to continue on with the evaluation through years 4 and 5 of the orchard, with the hope of having a good harvest to observe.
Here are some quick takeaways from the project:
- Both the UHDP and the open Tatura trellis system were viewed as equal, in terms of management and demand of labor. The open Tatura trellises were slightly more productive, however they require a $25,000/acre upfront installation cost that is hard to justify for a little better production.
- The best season was year 4 with a harvest of 8,000 lbs of Keitt mangoes, which represent around 1/3 of an acre. With that, I believe it is reasonable to infer that a full acre of Keitt mangoes could have the potential to produce 12 tons per acre, significantly more than current standards and world averages.
- One change that I would make is adding more space in between the rows. The spacing for the UHDP field was 10 feet between rows and the trellised field was 15 feet between rows. Moving forward I would recommend 20 feet between rows for the UHDP field and 25 feet between the trellises. The current spacing in the field can easily accommodate a riding mower, but is too dense for a tractor and the thickness of the canopy is making the field too shady and the air stagnant. Widening out the rows will make operating in the field more comfortable for the tractor and for harvesting, and will allow for better airflow and sunlight exposure.
- There is a fatal flaw with the high density system and that is feral pigs. Low hanging fruit is easy to harvest for the farmer, but is also easy for the pigs. In the early years of the orchard, years 2 and 3, the pigs ate as much as 80% of the mangoes as well as broke all the low branches on the trees. A perimeter fence is a necessity for this orchard management system, and if you cannot fence out feral pigs then high density orchard systems will not be as successful as the conventional mango orchard.
- Improving Hawaii’s mango industry is more complex than improved orchard management; it will also require a comprehensive approach to reducing losses along the entire mango supply chain.
If I had to guess, I would say that 50% of the mangoes we produce for the market make it to the market, and it may be much less than that. Currently we have too many losses along every stage of the supply chain and reducing these losses through better practices will be the key to building a thriving sustainable mango industry.
Pre-harvest
The pre-harvest stage is anytime from planting to yearly management leading up to the harvest. The orchard system is chosen at this time as well as the varieties picked for the market. What orchard management system will be used? Will it be conventional, high-density, or something in between. The most important thing is that it is well organized and efficient. The best varieties for commercial production are not always the best tasting mangoes, but must have a number of good characteristics that make them better than other mangoes such as: size, color, shelf life, even ripening, and taste. The tree itself has to be easily managed, a heavy bearer, a consistent yearly bearer, and disease resistant. These two choices will have a very significant impact on the overall productivity of the orchard and whether or not it will be sustainable. Pre-harvest is the stage where most losses occur and is also where most losses can be prevented through better management.
A good Integrated Pest Management (IPM) plan is necessary to reduce losses in the orchard caused by mammals, birds, insects and other pests, funguses, and all the other infestations and diseases that will affect production. Losses caused by pigs, birds, fruit-flies, anthracnose, and powdery mildew can damage as high as 90% of the harvest every year if it goes unmanaged. So, having an IPM plan in place will be critical in reducing losses leading up to harvest. A good percentage off losses can be attributed to the lack of a proper spray management program beginning from the pre-flower stage to post-flower.
Orchard management is also very important to production. Pruning to increase the sunlight exposure and increased airflow is important for a healthy orchard. Irrigating during fruit production will increase the size of the fruit and will minimize fruit drop and irrigating after pruning will speed up the new leaf flush. Getting the correct nutrients into the plant at the correct growth stage will increase production. These are the components that need to be fine tuned in the orchard and are necessary to maximize production.
High density orchard management systems allow the farmer to visually inspect the canopy of the tree for infestations, it is easier to see the growth stages’ from leaf flush to flowering, and you can see the flowers and the pollinator activities within the canopy. Spraying can be managed with a backpack sprayer or a small utility vehicle. Overall it is easier to inspect and manage trees that are 8 to 10 feet tall rather than 15 to 25 feet.
Harvest
Minimizing damage during the picking is critical; scratching fruit with the picker, knocking down adjacent fruit, and picking immature fruit are some examples. The high density orchard and the short trees allow the picker to fully observe the fruit to ensure that it is at the right maturity level for harvest and to carefully pick the fruit without damage. Picking in the cool morning hours and keeping the fruit in the shade while picking will keep the internal fruit temperature down, which will slow down the ripening process. It is also important to limit the amount of sap that touches the fruit skin, which will cause burns and blemishes making the fruit unmarketable.
To prevent sap-burn, harvest the fruit with an inch or two of stem still attached to the fruit until you can get to a cool area, then break the stem and place the fruit stem end down so the sap can fall off without touching the skin. Another method to reduce sap-burn is to use a mango wash, which is a mixture of lye, detergent, and water. Dunk the fruit into the mango wash or expose it to a spray of mango wash within a few seconds of picking to neutralize the sap. There are a few mango wash products on the market from Australia, but they may not be available in Hawaii or the U.S.
Picking the fruit, de-sapping, and keeping the fruit as cool as possible before arriving at the packing house as quickly as possible are the goals during the harvest stage.
Post Harvest
The post-harvest stage is where a lot of losses occur because our local farmers don’t have access to cold storage and there is no way to cool the fruit to slow down the ripening, thereby extending the shelf life. A lot of fruit is lost simply because it becomes overripe. During this stage the mango is washed, sorted, packed, and cooled. This is where you also see the losses from the pre-harvest and harvest stage: bug damaged, bird damaged, anthracnose, rub marks and scratches, and immature fruit are culled from the harvest and set aside.
Mangoes should be picked green mature or at first color break and allowed to ripen on the counter to get the best quality and consistency, at room temperature this will give you a shelf life of 4 to 7 days. Mangoes that are picked fully ripe on the tree are often overripe and the quality of the fruit may be inconsistent, at this point the shelf life is 2 to 4 days. Mangoes should be cooled to 55°F to slow down the ripening process, giving the farmer and the retailer more time to sell the fruit. Fully ripe mangoes can be stored for 7 to 10 days while maintaining quality, and green mature mangoes can be stored for even longer periods, however through studies we know that the acids in the fruit start to break down after 14 days and the quality diminishes the longer it is in storage. Properly cooling mangoes will extend the shelf life of the fruit and will give the farmer, wholesaler, and retailer the most time possible to get the fruit into the hands of the consumer. The reality is that prefabricated cool storage units are very expensive, need the space to house the unit, and access to electricity. This makes it simply unaffordable for the small farmer. However, over the last few years more examples of a do-it-yourself cold storage unit have been popping up, and this has been made possible by the CoolBot, which has been around since 2006.
The CoolBot is an external thermostat that can convert a window AC into a refrigerator and can lower the temperature into the low 40°F, cold enough to store tropical fruits at the optimal 55°F. This device provides an affordable way for the small farmer to build a cold storage unit using a shipping container or spare room at a fraction of the cost of a prefabricated cold storage unit. The unit can be built on-site and can be powered with solar panels if needed, making it affordable and convenient.
Logistics
Logistics is the process of getting the fruit from the packing house to the retailer in the most efficient way while maintaining the cold chain of command. This is especially important when shipping fruits off island, where the fruit will have to be trucked to the harbor, put on a barge to Oahu, then back on another truck to the wholesaler or retailer, while maintaining the 55°F temperature. Good communication and relationships are important to limiting losses caused by logistical problems.
Wholesaler, retailer, fruit processors, and consumers
Ideally, once your product is delivered to the wholesaler and retailers the chain of command has been passed on, they will continue the same practices to ensure a high quality product. These are your business partners, and trust is paramount. The fruit distributors need to trust that the farmer is providing a high quality product and the farmer has to trust them to do their best to sell the product.
The fruit processors are a major component of the mango supply chain. Having an outlet for off-grade fruits that are marked or blemished, but still good for processing is necessary in order to reduce losses that occur in the pre-harvest/harvest stages. Currently the outlets for off grade fruits are limited and often enough these fruits are left to rot. There will always be off-grade fruits and the more mango we produce the more off-grade fruits we will have, to the point that as farmers we need to be able to use or sell our off-grade fruits for value added products, to capture the most revenue as possible. Our ability to export mangoes outside of Hawaii is restrictive because of logistical reasons; unless you use airfreight (the most expensive) it would be really difficult to get mangoes from the farm to port, let alone the consumer, within 14 days, therefore we would lose our advantage over other mango producers and be just another commodity product with inconsistent quality. Even with the additional 10 million visitors to the islands each year, we would still be limited by fresh fruit sales. In order to really expand our mango production, we will need mango processors that have the ability to process millions of pounds a year to make the numerous delicious products from mangoes.
We can’t forget about the consumer. Providing a consistent supply of locally grown mangoes picked to ripen into the deliciously sweet fruit we all love will keep consumers returning to buy more local grown mangoes over imported mangoes throughout the season. There are no comparisons to the sweetness of our Hawaiian mangoes that practically sell themselves.
Research and Innovation
A thriving mango industry will require the ability to innovate and adapt in order to improve efficiency. We need to know if there are new practices, varieties, or products that can help improve production. Farming is very dynamic, always interacting with the environment and the climate. Fortunately for the mango growers, there is a lot of research that has been conducted on mango production that we can apply in Hawaii.
Conclusion
It is hard to put a real number on the percentage of losses that occur along the supply chain, but we know that it is a lot. On my farm I would say at least 50% of the harvest is lost through bird damage, bug damage, anthracnose, and overripe fruit. My goal is to reduce these losses to 20% or less through better management and practices along each stage of the supply chain. Increasing production by planting more trees and reducing losses through better management will be the changes needed to really build our mango industry.
At the Start of the Mango Loa Project in 2017, there was one small demonstration of the open Tatura trellis system on the island of Maui. Today, there are ultra high density plantation mango orchards and open Tatura trellises on each of the major islands. I have consulted with multiple farmers from each island and one thing they have in common is the plan to plant more mango trees. Hawaii State has made it a priority to increase our food production and is opening up more prime agricultural lands to farmers. These farmers recognize mangoes as a viable crop; as we are seeing more plantings throughout the state, of grafted mango trees selected for their high quality good producing mangoes. This is reflected by the most recent crop reports for tropical fruit production in Hawaii, conducted by the national agricultural statistics, in 2018 and 2021. According to the report between the years 2018 to 2021, the total number of mango trees reported doubled from 15,100 to 33,500 trees and harvested trees nearly quadrupled from 6,600 trees to 24,600. The total production increased by 60,000 pounds and the number of new trees planted has doubled. I expect this upward trend for mango production in Hawaii will continue to grow as farmers plant more trees and mango consumption continues to increase around the world, especially in the U.S. and Europe, two of the largest demographics that visit our islands annually. With that, there are many positive signs that Hawaii’s farmers are on the right track to having a sustainable mango future.
Open Tatura Trellis System Vs. The Ultra High Density Plantation Method
I have emphasized that the uhdp and the open Tatura trellis systems, as it is trialed in my project, is most suited for small farms with limited land, available labor, and will most likely be managed by hand. In which case, this system is excellent and has been very productive. However, the work is constant and intensive and can get overwhelming for a single person to manage. I would guess that a single farmer, utilizing the ultra high density plantation system could manage three to five acres independently while a four-man crew could probably manage as much as 20 acres. However, even at 20 acres, the farmer will need to consider time and labor saving practices like mechanization. In large conventional orchards, tractor pruners are the standard. In order to incorporate tractor management in the high density orchard, the rows will need to be widened to accommodate the machine and the trees can be allowed to grow slightly higher, 12 to 14 feet, to get the fruit higher off the ground.
A significant factor to consider when determining if you want to plant a high density orchard is the ability to protect the fruit from ungulates and birds. In Hawaii we have feral pigs, goats, deer, cows, chickens, and franklins that eat mangoes, damage trees, or both. If the orchard cannot be fenced in, the uhdp orchard will not be successful. In the first two years of the uhdp field, feral pigs broke over 100 trees, killing some. In the third year in the ground and the first year with fruit, pigs and birds ate 90% of the crop, while breaking off lower branches on dozens of trees. The field was fenced in after the third year and as a result we were able to have a decent harvest before pigs once again found its way in and damaged about 30% of the harvest. This wouldn’t be nearly the issue in a conventional mango orchard where the majority of fruit is out of reach from the ground animals. Low hanging fruit is not only a benefit to the farmers, but also for everything else.
High density orchard systems need to be adapted specifically for Hawaii. My experience with this technique so far leads me to believe that more than 300 trees per acre can be problematic. First it creates a really dense canopy that can reduce the airflow in the orchard, making the trees susceptible to infestations of insects like aphids, scales, mealybugs, and mites; all of which damage the fruit. Stagnated airflow can also lead to powdery mildew and anthracnose damage as well. The thick canopy also restricts sunlight from achieving optimal penetration, which will also diminish the quality of the fruit. Pruning one time after harvest is not enough to create sufficient airflow and sunlight distribution and five months post-pruning, when the flowering season begins the canopy is just as dense as it was before the pruning (this is true on the trellis as well). Multiple pruning sessions in a year is time consuming, runs the risk of pruning off flowering wood, or if you prune after fruit set, it is possible to sunburn the fruit.
The most significant difference between these two systems is the additional cost and labor to install the trellises; the management practices have been similar as well as the production. The cost per acre for the trellises is around $20,000 which would be a real impediment for a small farmer and while the production may start earlier and be slightly better than the uhdp system, it would be hard to justify that upfront cost. There are a few concerns with managing the trellised field; one is the ability to manage the vigor in the orchard. The Tatura trellis system was developed for temperate-zone fruits, like apples, pears, and peaches; and temperate zone fruits have the benefit of a dormant period during the winter where there is no growth, couple that with heavy production during the growing season and the vigor of the trees become more manageable. Also, many of these fruit trees have dwarf varieties which ultimately make growing fruits on the trellises successful. At this point, it is difficult to maintain a two-dimensional canopy, through a single pruning while multiple pruning sessions may eventually effect the flowering cycle. Also multiple leaf flushes before flowering often puts the fruit on the ground and more effort is needed to keep the fruit in its designated space. Lastly, the longevity of the wood posts is a concern. I have seen wood post fail within two years, most likely due to inadequate treatment of the wood, making it susceptible to termite damage, which was the cause of the failure in this case. While a benefit of the trellis is that it can protect the tree limbs from damage during a storm, if a trellis does break, it may be an insurmountable challenge to fix. Of course, a solution to this problem may be to use metal or concrete posts, but that would just raise the already high cost of installation.
With all that said, the most important recommendation would be to widen out the spacing in both the uhdp field and the open Tatura trellis field. This is the direction that I’ve already begun to move toward and the most recent field was planted at a density of 250 trees an acre, as opposed to the 450 tree density that was planted for this project. This is a spacing of 10 feet by 20 ft, compared to the 8 feet by 10 ft spacing of the uhdp field. This will leave plenty of space for the tractor and other machinery to operate. This would also open up the orchard to more airflow and sunlight and improving the quality of the fruit. As for the open Tatura trellis field, the recommendation would be to widen the space between the trellises. The trellises for the project were spaced 15 feet apart, which does not leave enough space for a midsize tractor to go through. Spacing the trellises 20-25 feet apart will ensure there is enough room to work in. it would be really difficult to manage with a tractor pruner, but I think it is possible. At least the outsides of the trellises; the insides of the trellises might not have enough space to safely maneuver. A recommendation may be to use an espalier style trellis as an alternative to the open Tatura trellis. I would also recommendation widening out the spacing between trees on the trellis from 8 feet to 10-12 feet; this would allow for more air and light into the orchard and would reduce the demand on the farmer to produce grafted trees. The last recommendation would be to start the bottom trellis wire at 36 inches instead of 24 inches; this would be to get the fruit higher off the ground.
Education and Outreach
Participation Summary:
2023 Final
The final outreach event for the project was a zoom webinar held October 24th. 42 people registered and 32 logged on to the webinar. YouTube video views for 2023 were 40,600.
2022-2023 Consultations in person, over the phone or a messaging app continue with about 6 per year. We had one farm field day with 26 attendants, HERE is a clip from that day. I presented my project at the Hawaii Tropical Fruit Growers Conference and had an article published in the CTAHR newsletter. We also had a grafting workshop and a pruning workshop that drew a lot of people, while it was not specifically about high density orchards, we do end up talking about that subject quite a bit throughout the day. The Mango Loa Project Youtube channel continues to be my most successful outreach outlet. We have 1400 subscribers and our videos have generated over 122,000 views.
2021-2022 This project began in October and due to Covid restrictions all planned outreach activities have been postponed or canceled, however the restrictions have been lifted and we are hopeful we can schedule in person events moving into the summer/ harvest season, where the focus of this project is. Upcoming, there is a garden fair at the community college in April that I will have a presentation and poster display; There is a field day planned in June; the project will be featured in the University of Hawaii CTAHR newsletter for the summer edition; and the Hawaii Tropical Fruit Growers Conference in November, where I will have a power point presentation
The Mango Loa Project YouTube channel has been the best outreach effort so far, with a total of 78,000 views. Based on the amount of feedback I have received through emails and messaging, there is real enthusiasm for high density orchard systems. Four new videos were produced with a focus on post-harvest pruning of the two different high density techniques, ultra high density plantation and the open Tatura trellis system, that are demonstrated in this project. At this point, the four new videos have a total of 1400 views.
https://youtu.be/52tHcCioK08
https://youtu.be/MnIth4-d0DQ
https://youtu.be/5E6vplneB6s
https://youtu.be/HmjUqo1c4qA
Education and Outreach Outcomes
On farm demonstrations and field days were an effective way to disseminate information on my project, but because I am on a small island with a limited population it didn't take much to reach most interested stakeholders on island. As a result, social media like Facebook and my Mango Loa Project Youtube page became the most effective way to reach people off island and abroad. Through the interactions on Youtube and Facebook, I got the impression that there was real interest in high density orchard techniques both for farming and backyard growing, as the vast majority of responses were positive. I believe through the series of videos that were produced, we managed to thoroughly cover the subject of high density orchard management systems for mango production and contacts through social media also allowed me to interact with people, through messaging and video calls, that were interested in installing high density orchards on their farms and made one on one consultations easy.
Overall awareness of high density orchard systems