Final report for LNE17-357
Project Information
The NE SARE-funded project, “Farmer-generated training and equipment solutions for producing and processing value-added grains,” has just been completed. Begun in the fall of 2017, the project was dedicated to increasing farmer expertise in food-grade grain production, processing, and marketing through a training program for NY, PA, and NJ growers.
The project’s approach to training involved the use of innovative farmers and grain processors as instructors and focused on farmer solutions to the problem of sourcing effective, affordable, and scale-appropriate production and processing equipment. Research was conducted on grain dehullers (essential equipment for the processing of the potentially highly profitable ancient wheats) in which lower cost, farmer-made dehullers were compared with commercially available equipment.
The training was conducted through 15 events, which included field days, workshops, and webinars sponsored by the three organizations overseeing the project (OGRIN, CADE, and NOFA-NJ) and other educational and farmer organizations cooperating with the project. In total, over 750 people attended these events. In addition, one-on-one training and mentoring for farmers was provided by the project’s advisory committee, which consisted of four farmers with expertise in grain production and processing and a small-scale equipment manufacturer, as well as by other expert farmers and project staff. Through evaluations collected during the project and at its end, participants in the project noted that their knowledge increased in one or more of the following areas:
- Types and varieties of value-added grains that may be grown in the Northeast
- Critical management practices, especially timeliness of planting and harvesting
- Essential production equipment needed, especially combines and grain cleaners
- Grain-processing equipment sourcing options, especially farmer-built or modified options
- Grain market quality requirements
- Marketing strategies
Research conducted on three farmer-made abrasion dehullers and a commercially available impact model showed the farmer-made dehullers to perform as well or better than the commercial option in terms of dehulling spelt. A farmer-made dehulling system (farm-made dehuller + purchased destoner) was found to be comparable to a commercially available, industry standard system (dehuller + gravity table) in terms of separation efficiency. Given the cost of the two farmer-made dehullers that are now available for purchase, $4500 or less, as compared to the commercial models, $16,000 to $35,000, the farmer-built machines would seem well suited to small- and medium-scale production and processing of ancient wheats.
A final survey of project participants showed that 14 farmers had met the performance target of an increase in sales of $3,000 in one or both of the last two years of the project due to acquisition of value-added grain production or processing equipment. A further eight farmers increased sales by $1500 or more. The project's organizers will continue to work with farmers to strengthen their production, access further needed equipment, and boost profitability.
The project would especially like to thank its advisory committee members, Nigel Tudor, Weatherbury Farm; Kit Kelley, White Frost Farm; Henry Beiler, Wholesome Acres; Lamar Stauffer; and Joseph Lapp, Sunnyburn Welding, for their tireless sharing of know-how with farmers and project staff.
Thirty-five farmers repair, modify, build or purchase scale-appropriate grain production or processing equipment resulting in 20 new and 15 expanded value-added grain enterprises that lead to an average annual increase in sales of $3,000 per farm.
Value-added grain production provides Northeastern growers with an opportunity to significantly increase farm profitability and enhance agroecosystem function. “Exotic” grains, such as the ancient wheats einkorn, emmer, and spelt, are in increasing demand by consumers, and currently fetch retail prices of $1.50-$7 per pound as locally grown, organic whole berries. Even the traditional small grains crops—when grown for food-grade quality and suitably processed—can sell for high prices: Organic raw rolled oats, e.g., retails at up to $6 per pound and organic rye flour (for which consumer demand is increasing) for around $1.70 pound. The local foods movement, which is fueling this demand and these prices, is forecast to continue to grow. Fortunately, these crops, if managed properly, also maintain and increase soil health through dense ground cover for soil protection and significant biomass (straw) production that is returned as organic matter to the soil. In addition, they serve as spatial niches for soil-enhancing forage legumes in the rotation: Legumes can be interseeded with spring/summer grains or frost-seeded into winter grains with no or minimal effect on grain yield.
Value-added grain production has great potential for growers who are limited in land and must therefore concentrate on optimizing profitability per land unit area. These would include many farmers in NY, PA, and NJ where farm size averages <140 acres. Vegetable farms would additionally benefit from the inclusion of a grain enterprise because grain crops (as grasses) can serve as break crops for diseases and insect pests in otherwise predominantly broad-leaved crop rotations. Farms with livestock can benefit not only from the grain products produced for sale but can utilize grain not meeting food-grade standards for feed and crop byproducts (straw, empty hulls) for bedding.
Two major constraints to developing profitable value-added grain enterprises in the Northeast are lack of expertise in food-grade grain production and difficulty in finding affordable, scale-appropriate grain production and processing equipment. Because food-grade grain production had largely left the Northeast by the beginning of the 20th century, growers in the region are likely to have experience growing small grains only as cover crops or feed crops. However, food-grade production requires additional management techniques and equipment to achieve needed crop quality. The ancient wheats pose special management considerations from planting seed in awned hulls to dehulling the grain after combining. Smaller-scale grain production equipment, especially harvesters, has not been produced in the U.S. in decades. The same situation applies to smaller-scale processing equipment: The only commercially available dehullers in the U.S., e.g., are large-capacity models requiring a substantial initial capital outlay (>$20,000) for purchase and installation.
This project addressed the lack of expertise in food-grade grain production and processing through a training program for NY, PA, and NJ growers. The topics for the training program were selected by the farmers themselves through a survey conducted in the fall and winter of 2015/2016 and included both management practices and equipment critical for high-quality grain production. As requested by the farmers surveyed, the training program included instruction on marketing and distribution strategies. Instruction for the training was provided largely by innovative farmers and entrepreneurs who have been working over the past decade to develop viable value-added grain production and processing systems and took place as much as possible on farms or at processing facilities.
The training program also incorporated solutions generated by farmers themselves to the problem of sourcing effective, affordable equipment. For example, a major strategy has been to refurbish or renovate used equipment. This has been particularly successful in terms of the air-screen seed cleaner, an essential piece of equipment for producing food-grade grains. While new cleaners sell for $4500 to $25,000, farmers have been able to purchase and repair used air-screen cleaners at costs ranging from $100 to $1000 and to successfully clean grain with them. In terms of needed dehulling capacity, farmers’ solutions have included modifying existing farm equipment to create dehullers, building dehullers from scratch, or sharing dehulling equipment. The research component of the project evaluated both farmer-made dehullers and commercial models for functionality and cost-effectiveness. The training program ended with an opportunity for participants to develop individual equipment projects (e.g., repairing a used air screen cleaner, modifying a hammer mill to dehull grain, or constructing an aspiration system) for which they received one-on-one consultations with mentors provided by the project.
This approach provided farmers with the management techniques and low-cost equipment options needed to start up or expand value-added grain production and processing.
Cooperators
- (Educator)
- (Educator)
- (Educator and Researcher)
Research
Dehulling equipment available to smaller-scale growers and processors of ancient grains varies in effectiveness and cost. Systematic testing of this equipment will provide farmers with options best suited to their individual enterprises and equipment budgets.
The five-member advisory committee, each of whom is experienced with the dehulling process, met in December 2017 and again in January 2018 to consider the methodology for the research. The following methods were developed in consultation with the committee.
Dehulling machines tested included a commercial impact dehuller (Codema), a commercial abrasion dehuller (Horn), and three farmer-made abrasion dehullers (see Table 1). With partial funding from a Northeast SARE farmer grant, Nigel Tudor (Weatherbury Farm) designed and built a smaller and more affordable version of a Horn-type abrasion dehuller. Henry Beiler (Wholesome Acres) made modifications to the Tudor design to create the Beiler mill. He also designed and built a smaller version, the Trumpet mill, that can both dehull and mill grain.
Each dehuller was tested using one or both of the ancient wheats spelt and emmer. For each crop, the same variety was used, each grown in the same year at the same farm. Varieties used were Oberkulmer (winter spelt) and Lucille (spring emmer). Because of the difference in dehulling chamber size between dehullers, sample size varied (see Table 1). Four of the dehullers (the three farmer-made models and the Codema) allowed for testing of the dehuller itself, before grain is sent through a finishing step in which dehulled kernels are separated from undehulled kernels. The Horn model, however, is a closed system in which the dehulled grain is automatically sent through a gravity table for separation. The Horn was therefore tested against the Tudor dehulling system, which consists of the Tudor dehuller and a purchased destoner.
Throughput time was determined with a stopwatch. For each crop tested, four separate samples were run through each dehuller. After throughput, each sample was weighed and then a 100 g subsample taken which was separated by hand into empty hulls (as needed), undehulled, dehulled, and cracked grain fractions. Dehulling efficiency was calculated as a ratio of mass of dehulled kernels (whole and broken) to whole sample mass minus empty hulls. Percent broken kernels was calculated as the ratio of mass of broken kernels to mass of whole plus broken kernels. (Broken kernels can reduce the grain's marketability.) Each measurement parameter was analyzed using one-way ANOVA followed by mean separation using Tukey’s test.
Four dehullers were tested using Oberkulmer spelt in which samples were collected after running through the dehuller (before any separation process). Table 2 shows that all four dehullers performed similarly in terms of the percent grain (undehulled plus dehulled plus cracked fractions) recovered after the dehulling process. On average, about 25% of spelt sample weight was lost in the dehulling process, presumably through loss of the hulls. In terms of percent grain dehulled, the Tudor, Beiler, and Trumpet dehullers had a higher hulling efficiency than the Codema machine. Percent cracked grain was highest using the Codema. The Trumpet dehuller also had a higher cracked grain percentage than the Beiler and Tudor models.
Two dehullers were tested using Lucille emmer; again, the samples were collected after dehulling but before the separation process. The Codema had a higher dehuller efficiency (85%) as compared to the Tudor dehuller (74%). Percent cracking was significantly higher with the Codema dehuller than the Tudor model (12 % vs 1%, respectively).
In terms of dehulling systems, both the Horn and the Tudor systems produced samples essentially free of undehulled kernels (0% vs. 0.5%, respectively). The Horn system had significantly more cracking (8%) than the Tudor system (1%).
Timing the throughput of the samples proved difficult: It was hard to determine exactly when all the material had exited the dehuller. The average throughput calculated for the Codema (1946 kg/hr) was in keeping with manufacturer specifications (2000 kg/hr) for oat dehulling. On the other hand, the calculated throughput for the Horn (224 kg/hr) was far lower than the manufacturer's rating of up to 1500 kg/hr. The slow rate may have been due to the need to handfeed individual samples into the machine instead of using the auguring system. Calculated throughputs for the Tudor model (460 kg/hr) and for the Beiler dehuller (361 kg/hr) are high compared to operator experience and need to be verified. The small Trumpet dehuller was found to average around 35 kg/hr.
Table 1: Dehuller models |
||||
Dehuller |
Type |
Location |
Sample size |
Crops dehulled |
Tudor |
abrasion |
Farm, Avella, PA |
10 kg |
Spelt, emmer |
Beiler |
abrasion |
Farm, Watsontown, PA |
10 kg |
Spelt, einkorn |
Codema VSH 2096 |
impact |
Mill, Halifax, PA |
10 kg |
Spelt, emmer |
Trumpet |
abrasion |
Farm, Bainbridge, NY |
1 kg |
Spelt |
Horn DVC 2 |
abrasion |
Farm, Topeka, IN |
45 kg |
Spelt |
Table 2: Spelt through dehuller |
|||
Dehuller |
% grain recovered |
% grain dehulled |
% cracked grain |
Tudor |
75 |
94a* |
1.7a |
Beiler |
76 |
96a |
3.3ab |
Codema |
73 |
86b |
14.9c |
Trumpet |
72 |
97a |
6.0b |
p value |
0.676 |
< 0.001 |
< 0.001 |
*Values followed by the same letter are not statistically different according to Tukey’s test. |
The above results suggest that the farmer-made abrasion dehullers trialed in this experiment can perform better than the Codema impact dehuller in terms of spelt dehulling efficiency and fraction of cracked grains. The Tudor dehulling system (dehuller + destoner) performed on par with the Horn (dehuller + gravity table) in terms of spelt separation. The Codema was superior to the Tudor dehuller, however, in dehulling efficiency with emmer. It also had a throughput several times that of the Tudor and Beiler models.
The good performance of the farmer-made dehullers is especially significant given their affordability: Beiler, $1950 (without motor); Trumpet, $1375 (without motor); and Tudor dehuller, ~$13,000. This is compared to the cost of the Codema and Horn models ($16,000 and $35,000, respectively). The Beiler and Trumpet dehullers are now being manufactured and can be purchased. CAD drawings for the Tudor dehuller are available through OGRIN.
The Tudor and Beiler dehullers would seem well suited to in small- and medium-scale production and processing of ancient wheats. The Trumpet mill appears to be a good fit for micro production and processing enterprises.
Education
The training program consisted of a series of workshops and field days facilitated by farmer/processor experts and OGRIN, CADE, and NOFA-NJ staff that occurred across eastern NY, NJ, and central and eastern PA at farms, processing venues, farmer conferences, and, in one case, a university experimental farm. To help plan the educational program and the equipment research (see research section above), an advisory committee was formed, consisting of four farmers with extensive experience in value-added grain production and processing (Henry Beiler, Watsontown, PA; Kit Kelley, Danville, PA; Lamar Stauffer, New Holland, PA; and Nigel Tudor, Avella, PA) and Joseph Lapp (Airville, PA), a welder and grain equipment developer. Together with the project coordinator, the advisory committee developed a list of training topics to be covered, including best field practices, post-harvest handling, processing, accessing needed equipment, and marketing.
From 2018 the 2020, the project held 15 training events (see Milestone 3 for details). The following topics were covered at multiple events (number of events in parentheses):
- Best field practices (6)
- Combine operation (2)
- Grain quality standards (4)
- Low-cost drying/storage options and pest management strategies for grain storage (4)
- Grain-cleaning equipment (5)
- Grain-processing opportunities (11)
- Accessing affordable equipment (9)
- Marketing (7)
One planned topic, dehuller research results, was not included in the training events because dehulling trials were delayed, first, due to difficulty in sourcing adequate ancient wheat seed lots for replicated research, and, second, by the covid pandemic. Nevertheless, single-replicate results of dehuller efficiency were presented at several events. The pandemic also necessitated the use of webinars with embedded video for the last three trainings in October/November 2020.
In addition to the training events, a tasting event of grains and grain products was held for several hundred members of the public (see Milestone 3).
Milestones
1000 Northeast farmers learn of the project’s training opportunities through project partners’ email lists, listserves, postings to on-line farmer communities, electronic newsletters, and direct mailings.
1000
1500
March 30, 2018
Completed
February 26, 2019
In addition to postings on the project cooperators’ websites, information about the project and opportunities for grower participation was disseminated through multiple 2018 events: presentations at the NOFA-NJ Jan 2018 annual winter conference, the Feb 2018 Hudson Valley Grain School, the Feb 2018 annual meeting of the Vegetable Growers’ Association of New Jersey, a June field day and an August annual tasting event at Rutgers Snyder Research Farm (over 540 attendees total). A featured article on the project in the Winter 2019 Pennsylvania Certified Organic newsletter Organic Matters (which has a distribution of ~1500) has further disseminated information on the project to area farmers.
200 return on-line or direct mail surveys detailing their on-hand equipment and its condition as well as their equipment and training needs.
200
118
December 01, 2018
Completed
November 02, 2020
A survey that documents farmer current practices and farmer information and equipment needs was developed and distributed electronically and through the mail. The survey was also distributed and collected at all training events throughout the project.
118 surveys have been completed.
250 attend one or more intensive short courses and workshops on best production practices, postharvest grain handling equipment and its use, and marketing strategies.
250
756
September 30, 2018
Completed
November 02, 2020
Training events:
- Improve Your Crop Rotation and Increase Profitability with Grains and other High-Value Crops(presenter: Elizabeth Dyck, OGRIN), Jan 28, 2018, NOFA-NJ winter conference, New , Brunswick, NJ: high-value grain crop options, best management practices, essential production equipment, processing equipment options (52 participants).
- Specialty Grain Markets(presenters: Lauren Melodia, Center for Agricultural Development and Entrepreneurship, and Elizabeth Dyck, OGRIN), Jan 28, 2018, NOFA-NJ winter conference, New Brunswick, NJ: profit potential of high-value grains, market quality requirements, marketing strategies (28 participants).
- Grow and Process Value-Added Grains(presenter: Elizabeth Dyck, OGRIN), Feb 7, 2018, NJ Vegetable Growers’ Association annual meeting, Atlantic City, NJ: benefits of including grains in rotation, market requirements, essential production and post-harvest handling (30 participants).
- The Ancient Wheats(presenters: Elizabeth Dyck, OGRIN, Sharon-Burns Leader, Bread Alone Bakery), Feb 9, 2018, Hudson Valley Grain School, Coxsackie, NY: best management practices, essential grain equipment, processing opportunities, whole grain and bread tasting (65 participants)
- Grow, Process, Market, Eat Value-Added Grains(presenters: farmers Kit Kelley, Washingtonville, PA, Teena Bailey, Germansville, PA, and Lamar Stauffer, New Holland, PA; Joseph Heckman, Rutgers; Elizabeth Dyck, OGRIN), June 26, 2018, Rutgers Snyder Research Farm, Pittstown, NJ: tour of demonstration plots of 30 fall-and spring-planted grain types and varieties and einkorn N fertility experiment (with discussion of essential management practices), demonstration of grain cleaners and small-scale oat roller and dehuller, blind tasting of whole cooked grains, products made from local grains by four bakeries/crepe makers. (68 participants).
- Value-Added Grain Production in New Jersey(Presenters farmers Kent Kimball, Belvidere, NJ; Scott Morgan, Hillsborough, NJ; Tom Zeng, Flemington, NJ), Jan. 26, 2019, NOFA-NJ 2019 winter conference, New Brunswick, NJ: Farmer panel discussion on establishing a value-added grain enterprise, crop selection, storage options, markets, grain prices, and current constraints (30 participants).
- On-Farm Processing: A Small-Scale Farmer’s Success Story(Presenter Henry Beiler, Wholesome Acres, Watsontown, PA), January 26, 2019, NOFA-NJ 2019 winter conference, New Brunswick, NJ: Farmer/processor Henry Beiler gave an overview of his grain enterprise that is built around the ancient wheat einkorn, displayed the small-scale dehulling machine that he has built and now offers for sale, discussed the benefits and challenges of becoming a registered seed seller of einkorn, and offered participants a taste of einkorn bread and other baked products (26 participants).
- Assessing and DevelopingMarkets for Value-Added Grains (Presenters Mark Fischer, Castle Valley Mill; Scott Morgan, Morganics Family Farm; Brad Estabrooke, Breuckelen Distilling; Dennis Nesel, Hudson Valley Malt; Lauren Melodia, CADE; Elizabeth Dyck, OGRIN) Feb.1, 2019, 5th Annual Hudson Valley Value-Added Grain School, Coxsackie, NY: Small- and medium-scale grain-processing enterprises; market outlook and grain quality requirements for the value-added milling, distilling, and malting markets; accessing capital, and using marketing toolkits and enterprise budgets (63 participants).
- Grain Lollapalooza(Presenters Thor Oechsner, Newfield, NY; Paul Koch, Earth’s Harvest Farm; Mike Hozer, Leonard Bussanich, Larry Mahmarian, River Valley Community Grains; Elizabeth Dyck, OGRIN) Aug 28, 2019, Earth’s Harvest Farm, Morris, NY: Sourcing and using a combine, developing a small-scale grain processing enterprise, demonstrations of small-scale grain cleaner, oat roller, dehuller, and hammer mill, grains and grain products tasting. Co-sponsored by CADE and OGRIN (36 participants).
- Going with the Grain(Presenters Amy Halloran; Aaron McLeod, Hartwick College Center for Craft and Food Beverages; Walter Riesen, Star Route Farm; Elizabeth Dyck, OGRIN) Sept.29, 2019, Danforth Jersey Farm, Jefferson, NY: Grain production, grain quality parameters and testing, current markets, demonstrations of oat roller, mill, and dehuller; tasting of grain and grain products. Co-sponsored by Jefferson Main St, CADE, and OGRIN (34 participants).
- Small-Scale Specialty Grain Production (Presenters Henry Beiler, Wholesome Acres; Kit Kelley, Whitefrost Farm, Lamar Stauffer, Stauffer Farm; Elizabeth Dyck, OGRIN) Feb 7, 2020, PASA Annual Conference, Lancaster, PA: Optimum management practices, sourcing seed and needed equipment, critical grain-quality parameters and how to meet them, processing and marketing options, and current wholesale and retail prices. (45 participants)
- Small-Scale Grain Processing Equipment (Presenters Henry Beiler, Wholesome Acres; Lamar Stauffer, Stauffer Farm; Joseph Lapp, Sunnyburn Welding) Feb 7, 2020, PASA Annual Conference, Lancaster, PA: Presentations of equipment for grain cleaning, dehulling, oat-rolling, and milling. (25 participants)
- Grain Production with a Focus on Harvesting: Webinar and field video (Presenters Tom Zeng, Zeng Farm; Scott Morgan, Morganics Family Farm; Elizabeth Dyck, OGRIN) Oct 19, 2020, NOFA-NJ webinar series: The harvesting process. (103 participants) (https://www.youtube.com/watch?v=OW9rea2Nl68&feature=youtu.be;https://www.youtube.com/watch?v=6W4m2rviKRg&feature=youtu.be)
- Cleaning, drying, storage (Presenter Aaron Gabriel, Cornell Cooperative Extension) Oct 26, 2020, NOFA-NJ webinar series. (82 participants) https://www.youtube.com/playlist?list=PL3L-lOCA5wsQOVjrCdm299WHKVj4forOS
- Processing and Marketing: Webinar and field video (Presenters Leonard Bussanich and Larry Mahmarian, River Valley Community Grains; Henry Beiler, Wholesome Acres; Joel Steigman, Small Valley Milling; Elizabeth Dyck, OGRIN) Nov 2, 2020, NOFA-NJ webinar series: Small- and medium-scale grain processing and retail and wholesale marketing options. (69 participants) (https://www.youtube.com/watch?v=-_bL6qedk7E&feature=youtu.be)
Project event for consumers:
- Value-Added Grains Tasting(presenters: Elizabeth Dyck, OGRIN, NOFA-NJ volunteers), Aug 29, 2019, Annual Snyder Farm Great Tomato Tasting, Pittstown, NJ: blind tasting of cooked small grains and breads made with heritage and modern wheat varieties, other breads, salad, and dessert made with value-added grains (~300).
100 attend an intensive short course on dehulling and sourcing or creating dehulling or other grain processing equipment and identify a specific equipment need that the project could help them address.
100
253
December 01, 2019
Completed
November 02, 2020
To better accommodate farmers across the region, six workshops (see full descriptions under Milestone 3) were held (in New Brunswick, NJ, Coxsackie, Morris, and Jefferson, NY, Lancaster, PA, and through a webinar (NOFA-NJ series) which featured grain-processing presentations and demonstrations. Individual equipment projects are ongoing (see Milestone 5).
70 farmers contact project staff or farmer experts for additional assistance on individual equipment projects or download/request mailings of materials generated by the short courses and the project’s research on scale-appropriate processing equipment.
70
73
April 30, 2020
Completed
May 31, 2021
In 2018, 21 farmers contacted OGRIN directly for help with equipment needs. Of these, 14 projects are currently underway. Eight involve dehulling equipment; one, construction of a prototype aspirator; one, testing of a grain cleaner; and four, development of oat-rolling capacity.
The oat-rolling projects illustrate the range of farmer equipment needs and strategies used by the project to address these needs. OGRIN had previously identified several oat-crimper machines developed in the Amish community that might be used to roll raw oats. OGRIN helped a PA farmer purchase one of these models in 2017, which the farmer had motorized and mounted (see Figure 1).
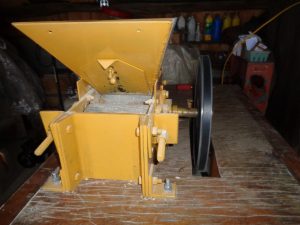
However, in 2018 the farmer requested help in increasing throughput of the machine, which was accomplished by a project mentor advising the farmer on belt replacement and roller adjustment. Three others wanted an oat roller, but wanted a more standard product (flat rolled oat) than the oat crimper could deliver. Two project farmer mentors worked with the original oat-crimper maker to develop an oat roller with two improvements: 1) lightly knurled rather than indented rolls and 2) both rollers attached to the drive chain. A prototype of the machine was successfully tested at the project’s field event in June, and three improved oat rollers have since been manufactured and purchased. Two farmers have motorized and mounted the machine themselves (see Figure 2, e.g.). A third entity, a new small-scale mill whose operators do not have mechanical backgrounds, has had the project identify local experts to produce a ready-to-use product (see Figure 3).
In addition to the improved oat roller, the project has helped develop a small-scale, abrasion type dehuller
In 2019, 23 regional farmers contacted the project on value-added grain production and received mentoring on production, harvesting, and storage techniques and help in sourcing seed and accessing markets. Eight farmers received assistance on equipment projects, involving combines (2,) dehullers (4), and oat rollers (2).
In 2020, 21 regional farmers contacted the project on value-added grain production and received mentoring on production, harvesting, and storage techniques and help in sourcing seed and accessing markets. Six farmers and two processing facilities received assistance on equipment projects, including seed cleaners (3), oat rollers (2), dehullers (1), puffers (1), and mills (1).
In 2021, a further eight growers contacted the project for assistance on production techniques, marketing, and sourcing of seeds and equipment, including seed cleaners (1), combines (3), and dehullers (4).
50 farmers return project post-surveys documenting increased expertise in grain management, use of grain equipment, individual equipment projects, new or expanded grain enterprises utilizing this equipment, and impact on farm sales. July 2020
50
31
September 30, 2020
Completed
August 30, 2021
Out of 42 contacted by mail, email, or phone, 31 submitted a completed questionnaire.
35 farmers repair, modify, build or purchase scale-appropriate grain production or processing equipment resulting in 20 new and 15 expanded value-added grain enterprises that lead to an average annual increase in sales of $3,000 per farm. August 2020
35
29
November 30, 2020
Completed
August 30, 2021
Of the 31 participants, 29 verified that they had repaired, modified, built, shared, or purchased scale-appropriate grain production or processing equipment. Of these 17 were new operations and 11 farms who had expanded due to the sourcing of equipment.
Milestone Activities and Participation Summary
Educational activities:
Participation Summary:
Learning Outcomes
Critical topics on which knowledge, attitudes, skills, and awareness increased:
- Types and varieties of value-added grains that may be grown in the Northeast
- Critical management practices, especially timeliness of planting and harvesting
- Essential production equipment needed, especially combines and grain cleaners
- Grain-processing equipment sourcing options, especially farmer-built or modified options
- Grain market quality requirements
- Marketing strategies
Performance Target Outcomes
Target #1
35
Repair, modify, build or purchase scale-appropriate grain production or processing equipment
20 new and 15 expanded value-added grain enterprises
average annual increase in sales of $3,000 per farm
29
Repaired, modified, built, shared, or purchased scale-appropriate grain production or processing equipment
17 new and 12 expanded value-added grain enterprises.
14 of the 29 farmers had an increase of $3,000 in sales in 2020, in 2021 (to date), or in both years.
A final survey was developed to verify benefits received from the project, including training and information transfer on value-added grain production, processing, and marketing; equipment sourcing and acquisition, and increases in sales. A draft questionnaire that was phone tested on three project participants was modified to allow different methods of reporting an increase in sales by year from 2018 to 2021: Respondents could report specific figures or report in terms of a series of dollar ranges (e.g., $1500-$2000,$2000-$2500, etc.). The final version (eight questions, three pages) was distributed by email, mail, and fax.
Of the 42 surveys distributed, 31 were completed and returned by email, mail, fax. In three cases, the respondent requested that the questionnaire be filled out by project staff during a phone call. In terms of the sales data (the measurable benefit in the performance target), although a few respondents reported specific figures, most opted for the range approach, likely because they were estimating amounts, although in one case a respondent said he was opposed to providing specific figures on ideological grounds.
The project did not reach its goal of 35 farms reporting an increase of sales of $3000 due to equipment repair, modification, building, purchase, or sharing of equipment. (The sharing of equipment was added to the performance target when an additional grant allowed for the setup of a mobile grain processing unit that OGRIN has been circulating to farmers in a 60-mile radius of OGRIN's office.) Instead, the surveys documented that 14 farmers increased sales by at least $3000 in 2020, 2021 (to date), or in both years. Eight farmers reported increases of $1500 or above in one or both of those years. Seven of the respondents reported increase in sales of $500 or less in one or both of those years. In the latter category, five were new farmers who have not yet marketed their crops or who, in one case, had lost the crop due to flooding.
Among the 14 respondents who met the performance target, there were few discernible trends. Half of the respondents had new operations, and half were expanding their grain enterprises. Increase in sales was sometimes attributed to a single piece of equipment (typically an oat roller or dehuller), but sometimes to multiple acquisitions. Among the 8 farmers reporting an increase of $1500 in sales, a majority showed a steady increase in sales over time, an encouraging sign. Of the 29 respondents, 28 indicated that they will continue with value-added grain production and processing in 2022.
Two factors likely contributed to the project's failure to reach the performance target. First, although the questionnaire did not document yield (in an attempt to limit its length), conversations with multiple farmers over the years of the project reveal that most growers continue to produce low yields. For example, 15 bu/A of spring wheat and 30 bu/A of winter wheat are typical for growers. For the highly profitable crop einkorn, which has a yield potential of around 2800 lb/A in our region, average yield is around 500 lb/A. Second, although, as documented in the survey, multiple farmers have benefited from marketing support from the project, most farmers are not aware of or reaching diverse markets. More work is needed to help farmers increase yields of value-added crops using sustainable management techniques and access diverse markets. We need more success stories like the farmer who reported an increase in sales attributed to work with the project of over $33,000 in three years.