Final report for LNE19-387R
Project Information
Barriers to the acceptance and implementation of coated sand made from acid mine drainage (AMD) sludge as a phosphorus (P) sorbent in the horticultural industry included concern about leaching of heavy metals from the coating, and the lack of documented procedures for use intercepting pot leachate or incorporation within potting media. Leaching experiments documented that heavy metal concentrations were below drinking water limits for all metals except As, Cr, and Sr. As the composition of acid mine drainage is highly variable, it is suggested that sources containing As, Cr, and Sr not be used to create coated sand.
Coated sand was very effective at removing P from pot leachate. P sorption was evaluated using three species which received different levels of fertilization and required different lengths of time to reach marketable size. Coated sand reduced P concentrations by 51% for petunia, 55% for pansy and 46% for chrysanthemum.
Coated sand was also highly effective at retaining P within the pot. Potting media was mixed with 10 to 40% coated sand to determine the optimal percentage in terms of plant performance and P retention. Controls included plain sand amendments and a no sand treatment. Plants were fertilized with a complete fertilizer or fertilizer without P. Three species, pansy, petunia, and chrysanthemum, were grown to market size.
Neither petunia nor pansy, the two species under cultivation for the shortest period displayed any sign of nutrient deficiency or lower biomass even in the treatments that did not receive phosphate. However, the chrysanthemums in the phosphate-free treatments had significantly less biomass and did show signs of nutrient deficiency. The higher the proportion of coated sand in the potting media the greater the amount of P was sorbed. All coated sand treatments removed P from the leachate throughout the experiment. This indicates that, while the coated sand may become saturated, as plant uptake removes P from the coated sand, it retains the capacity to sorb additional P. The 20% coated sand was determined to be the optimum percentage as fresh weights were the highest for that media.
The next experiment was designed to determine the optimum level of P fertilization needed when growing plants in potting mix amended with coated sand. Chrysanthemum was grown in potting mix amended with 20% coated or plain sand with a potting mix control and fertigated with fertilizer at 25, 50, 75, or 100% P. Overall, the plants grew best when fertigated with 25% P. Leachate P concentrations were lowest from pots containing coated sand and mirrored the P concentration in the fertilizer.
The final experiment was designed to determine if the presence of coated sand impacted biomass accrual or tissue mineral nutrient concentrations during the production cycle. This was evaluated for a short (petunia) or long production cycle species (chrysanthemum). Plants were grown in potting mix amended with 20% coated or plain sand with a potting mix control and fertigated with a commercial fertilizer. There was little difference in fresh or dry biomass between short-term plants grown in potting mix and plants grown in media amended with coated or plain sand. This experiment is still in progress.
Overall, this project demonstrated that heavy metal leaching from coated sand is negligible if care is taken regarding the composition of the AMD source used to coat the sand. More than 50% of P in pot leachate was sorbed by coated sand when leachate was passed through coated sand. Plants grown in potting media amended by coated sand did not display any adverse effects even at the highest percentage. Amending potting mix with 20% coated sand provided the best plant growth while maintaining substantial P retention within the pot. The amount of P in fertilizer can be reduced to 25% and still retain excellent growth when plants are grown in media amended with 20% coated sand. Experiments in progress will give insight into the effect of coated sand on biomass accrual and mineral nutrient concentrations.
- Determine if heavy metals present in some AMD sources would be incorporated into the coating and characterize their leaching potential;
- Determine the operational parameters for the use of coated sand in the horticultural industry; and
- Quantify any additional benefits from using coated sand in potting media such as improved root structure, increased flowering and improved post-production success.
Research
Coated sand, made from AMD, is a cost-effective phosphate sorbent that will allow the capture and reuse of dissolved phosphate in the greenhouse/nursery industries. This will result in reduction in fertilizer application and non-point source phosphate inputs to aquatic systems while reducing the amount of AMD sludge to be disposed of. It will also provide a constant source of phosphorus during production and post-production that will lead to increased profits for the growers.
Leaching of AMD coating
Coated sand is made using acid mine drainage (AMD) which may contain toxic heavy metals such as lead, copper or arsenic. The procedure used to make coated sand will exclude many of the toxic heavy metals. Additionally, heavy meals that are in the coating could be bound to the sand and are not at risk of leaching into aquatic and terrestrial environments. However, it is essential that we understand which, if any, of the toxic heavy metals in the AMD might be present in coated sand and whether they can be leached from the coating. In this experiment we added any of the heavy metals not already present in the AMD to the highest concentrations found in the literature and followed our standard coating procedure. Both the sand and leachate were evaluated for heavy metal concentrations.
Seventy-five liters of raw AMD was collected from the Omega mine site south of Morgantown. The raw AMD was spiked with heavy metals at concentrations found in the literature. The pH was adjusted and the precipitated metals allowed to settle overnight. The supernatant was siphoned off and the precipitated was applied to sieved sand in the standard coating procedure. Supernatant and sludge samples were analyzed for aluminum (Al) , arsenic (As), calcium (Ca), cadmium (Cd), cobalt (Co), chromium (Cr), copper (Cu), iron (Fe), magnesium (Mg), manganese (Mn), nickel (Ni), lead (Pb), antimony (Sb), selenium (Se), and zinc (Zn) via ICP-OES to determine the partitioning of metals.
Coated sand (250 ml/414 g) was placed in each of six 2 inch pots and watered with 250 ml tap water to thoroughly wet the sand. On subsequent days the sand was watered daily with 100 ml tap water. Leachate was collected on day 1, 14, 28, and 42 and analyzed for the metals listed above. Tap water was also analyzed for the same metals to differentiate between the contribution from the sand and what existed in the tap water.
A second leaching experiment was done with both coated sand spiked with heavy metals (n=2) and coated sand that had not been spiked (n=3). In this experiment we monitored leachate pH, sulfate, Fe, Al, Ca, Mg, and Mn concentrations.
Phosphate Sorption
Four experiments were performed to assess the efficacy of using coated sand to reduce phosphorous (P) concentrations in horticultural effluents: outside-pot sorption (objective 2) and three in-pot sorption experiments (objectives 3, 3b, and 4). The first, outside pot sorption, evaluated how well the coated sand removed P from pot leachate. In the three in-pot sorption experiments, coated sand was incorporated into the potting mix and plain sand was used as a control. An additional control consisting of potting mix without any sand was included.
Outside-Pot Sorption
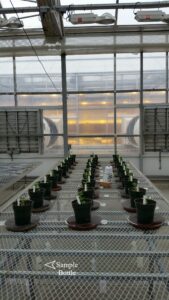
Phosphate sorption of leachate by coated sand was assessed by placing a tray of plain or coated sand beneath a pot planted with pansy, petunia, or chrysanthemum. Each tray was filled with 1 L (1,400g) of either plain or coated sand and covered with landscape fabric to prevent plant roots from colonizing the sand. Each tray had a drain that allowed the pot leachate to flow through the sand and drain to a sample bottle (Figure 1).
Pots were initially irrigated with deionized water. All subsequent irrigations included commercial fertilizer 15N–2.2P–12.5K (Peter Excel Cal-Mag; Everris NA, Marysville, OH) at three rates 150, 200, and 250 ppm nitrogen (N) for pansy, petunia, and chrysanthemum, respectively. The pots were fertigated as needed. Each species was grown until it reached a marketable size. Leachate volumes, nitrate, ammonia, phosphate, sulfate, chloride, calcium, magnesium, iron, aluminum, and manganese concentrations were measured after each watering.
In-pot Sorption
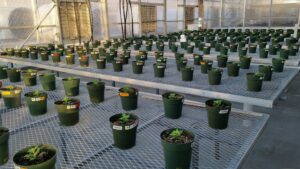
In the first in-pot sorption experiment, P-saturated coated sand or plain sand was mixed with the standard potting mix at a ratio of 10, 20, 30, or 40%. A plain potting mix control was included for a total of nine treatments. Pansy, petunia, or chrysanthemum seedlings were transplanted in a 6” pot with five replications. Pots were initially irrigated with deionized water. At all subsequent irrigations, pots were fertigated with Hoagland’s fertilizer solution made either with or without P. Pot leachate was collected from each pot and the leachate volume was determined. Phosphate, chloride, sulfate, calcium, magnesium, and manganese concentrations were determined on the leachate at each irrigation. Electrical conductivity, pH, and concentrations were determined every two weeks.
In the second in-pot sorption experiment, we wanted to determine whether the presence of coated sand would permit reducing the P level in the fertilizer without harming plant performance. We selected the percentage of coated sand that performed the best in the previous experiment. Four amended media types were used: P-saturated coated sand, unsaturated coated sand, P-saturated plain sand, and unsaturated plain sand were mixed with potting mix at a ratio of 20% for all substrates. Unlike previous experiments, both the coated sand and plain sand were saturated with 1,000 mg/L P instead of 200 mg/L P which resulted in greater P saturation of the coated sand. A plain potting mix control was included for a total of five substrate treatments. Chrysanthemum seedlings were transplanted in a 6” pot with 4 replications. After the initial irrigation with deionized water, each substrate treatment was irrigated with Hoagland’s fertilizer solution made with 0, 25, 50, 75, or 100% P. Pot leachate was collected from each pot and the leachate volume was determined. Phosphate, chloride, sulfate, calcium, magnesium, and manganese concentrations were determined on the leachate at each irrigation.
In the third in-pot sorption experiment, we evaluated whether growing in coated sand affected biomass accrual, tissue nutrient concentrations, growth index, and after-market success of a short production period crop (petunia) and a long production period crop (chrysanthemum). Potting mix was mixed with 20% P-saturated coated sand or 20% plain sand, and a potting mix control was included. The objective was to evaluate biomass accrual and nutrient concentration of plugs grown in the three media. Petunia seedlings were transplanted in a 4” pot and chrysanthemum seedlings were transplanted in a 6” pot. Five replications were used for both crops. After the initial irrigation with deionized water, the petunias were irrigated with 20-10-20 NPK fertilizer at 100 ppm N and the chrysanthemums were irrigated with 20-10-20 NPK fertilizer at 300 ppm N. Pot leachate was collected, and leachate volume and phosphate concentration determined.
Production for petunias was 5 weeks in 4” pots. Plants were then transplanted into 1-gallon pots with potting mix and irrigated with tap water for the post-production cycle, which was 6 weeks long. Production for chrysanthemums was 10 weeks in 6” pots and is ongoing. Destructive harvests for petunia were performed weekly during production and biweekly post-production; destructive harvests for chrysanthemum were performed biweekly during production and are ongoing. Fresh and dry weight of above and below ground tissue were determined. Mature leaves, immature leaves, and root tissue samples were collected for mineral nutrient analysis. The petunia tissue from one harvest during production and one post-production harvest was analyzed via ICP for phosphorous, potassium, iron, magnesium, manganese, sodium, copper, zinc, sulfur, boron, and selenium.
Metals partitioning
The metals in AMD were primarily Fe (42%), Ca (26 %), Al (20%), and Mg (8%). The percentage of these metals changes when the pH is adjusted during the precipitation process. Fe was still the predominant metal accounting for 63% while Al accounted for 31% of the mass. The metals partitioning between supernatant and precipitate was metal-specific. The metals Ca, Co, Mg, Mn, Ni, Sr, and Zn remained predominately in the supernatant while the metals Al, As, Cd, Cr, Cu, Fe, Pb, and Sb were predominately in the precipitate. Despite being major components of the AMD, Ca and Mg accounted for just 1.7 and 0.6% respectively of the precipitate mass. The majority of the As, Cr, Cu, Pb, and Sb precipitated; however, due to low concentrations in the raw water, they comprised just 3.6% of the mass of the precipitate. These results likely over estimate the percentage of metals precipitated as we used the highest concentrations reported in the literature. Additionally, there may have been interactions between metals that would not naturally occur as they would not be found together.
Leaching
The pots of coated sand were watered daily with tap water with samples being taken on days 1, 14, 28 and 42. Metal concentrations in the pot leachate were highest on the first day with most metals decreasing in concentration over time (Table 1). The metals with the highest concentrations were Ca and Mg with concentrations of 6,501 and 18 mg/L, respectively on day 1. These concentrations decreased rapidly over time with concentrations around or below tap water concentrations by day 42. Fe, the metal making up most of the coating had concentrations of around 0.1 mg/L through the entire experiment. Concentrations of Al ranged from 0.7 to 1.0 mg/L. Concentrations of most of the other metals were less than 0.05 mg/L with Cd, Co, and Cu concentrations generally below detection. However, As concentrations ranged between 0.20 – 0.45 mg/L, Cr concentrations were initially 0.8 mg/L but dropped quickly and most troubling, initial Sr concentrations were 10 mg/L. These results indicate that AMD that contains heavy metals such as Al, Fe, Mn, and Co can be used to coat sand without concern as they are either not incorporated into the coating or they do not leach. However, AMD that contains Sr, Cr or As should not be used.
BDL – Below Detection Limit, *reported value is from the one sample in five that was above the detection limit
A second leaching experiment was done where pot leachate was collected daily to examine how leachate varied over shorter time periods. We used the remaining spiked coated sand (2 pots) and regular coated sand (3 pots ) and measured pH, and sulfate, Fe, Al, Ca, Mg, and Mn concentrations.
The pH of the leachate varied between 7.5 and 8.8 with a mean of 8.2. The pH of tap water ranged between 7.5 to 8.0. Initial sulfate concentrations were between 434 to 494 mg/L and then increased to a maximum of 2443 mg/L on day 5. The concentrations decreased such that by day 18 the sulfate concentrations were 170 to 300 mg/L. Sulfate concentrations continued to decrease but at a slower rate and were 70 mg/L at the end of the 30 day experiment. Tap water concentrations ranged between 55-75 mg/L.
Initial calcium and magnesium concentrations were extremely high on the first day, 8899 and 534 mg/L, respectively. Calcium concentrations decreased to around 100 on the next 3 days before increasing again to a high of 610 mg/L on day 8 after which concentrations decreased slowly to 116 mg/L by day 20. Concentrations at the end of the experiment were comparable to tap water at 30 mg/L. Magnesium concentrations followed the same pattern with concentrations around 30 mg/L on days 2 through 5 increasing to 40 on day 8 and they decreasing to 19 by day 11. Concentrations decreased to 7.3 by day 22 and then increased to 12 at day 30.
Fe, Al, and Mn were all at low concentrations. Initial iron concentrations were 0.57 mg/L but dropped to 0.35 mg/L by day 3 and further decreased to 0.10 mg/L by day 10. From day 20 to day 30 concentrations were 0.03 to 0.05 mg/L. Aluminum concentrations varied between 0.23 to 1.1 mg/L with no apparent pattern. Initial manganese concentrations were 0.24 but dropped to 0.03 mg/L on day 2 and remained less than 0.06 for the remainder of the experiment with an average concentration of 0.02 mg/L
The leaching experiments demonstrated that the coated sand needs to be rinsed before use to remove sulfate, calcium and magnesium which leach at high concentrations. The rinsing will also remove heavy metals that are loosely bound. The pH of the leachate was generally stable. The experiments confirmed previous experiments where the major metals in AMD (Fe, Al, and Mn) were retained within the coating with insignificant losses to the leachate. A washing protocol for the coated sand has been developed to avoid the initial flush of metals when the coated sand is used. Leaching analysis will be done on washed coated sand that was spiked with heavy metals to ascertain efficacy of the procedure in removing those metals. Additionally, SEM will be done on both washed coated sand and washed coated sand spiked with heavy metals to evaluate the presence of metals within the coating.
P sorption
Outside Pot Sorption
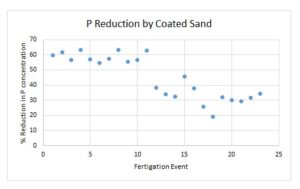
Coated sand was effective at sequestering substantial amounts of phosphorous. Pansy, receiving the lowest fertilizer concentration, had 56% of the P removed, while petunia, receiving a medium fertilizer concentration, and chrythanthemum receiving the highest concentration of fertilizer, removed 51% and 41% of the P, respectively. Through the first eleven fertigations, the coated sand removed 59% of the P, while, it removed 33% of the P in the remaining twelve fertigations (Figure 3).
There does not appear to be any sorption of either nitrate or ammonium by the coated sand (data not shown). Conversely, 80% of the manganese in the leachate was removed by the coated sand. Initial calcium and magnesium concentrations were five and two times higher in the coated sand samples, respectively. Over the course of the experiment, calcium and magnesium concentrations gradually decreased. Iron and aluminum concentrations were comparable between the plain and coated sand indicating that the AMD coating was not breaking down and releasing either iron or aluminum. Data analysis is ongoing.
In-pot Sorption
The first in-pot sorption study was initiated in December 2020 and lasted 16 weeks for a total of 16 fertigations following the initial irrigation with deionized water. Petunia reached market size after 42 days and required five fertigations, pansy reached market size after 59 days and required six fertigations while chrysanthemum reached market size after 116 days and required 16 fertigations. Neither petunia nor pansy, the two species under cultivation for the shortest period displayed any sign of nutrient deficiency or lower biomass even in the treatments that did not receive phosphate. However, the chrysanthemums in the phosphate-free treatments had significantly less biomass and did show signs of nutrient deficiency.
Leachate dynamics were very similar between all three species. The data presented below are from chrysanthemums, which were under cultivation for the longest time. The coated sand very effectively retained P within the pot. Even at the lowest percentage, coated sand removed at least 80% of the P in the leachate at the initial watering. The higher the proportion of coated sand in the potting media the greater the amount of P was sorbed. In the initial fertigation, in pots with 10% coated sand and receiving fertilizer with P, 35% to 38% of the P was sorbed, and increased to 86% to 91% in pots with 40% coated sand. P sorption decreased with each subsequent fertigation. All coated sand treatments removed P from the leachate, including the last fertigation event. This indicates that, while the coated sand may become saturated, as plant uptake removes P from the coated sand, it retains the capacity to sorb additional P. It is estimated that the 10% coated sand retained 109 mg/L P per pot while the 40% coated sand retained 348 mg/L P per pot in the chrysanthemum treatments.
In pots receiving fertilizer without P, the P in the potting media itself is mostly retained within the pot. In pots with 10% coated sand, only 2% to 6% of the P was present in the leachate. Pots with higher proportions of coated sand retained more P. The P supplied by the potting mix and present in the leachate decreased with each fertigation.
Leachate concentrations of calcium, magnesium, manganese, chloride, and sulfate were all elevated in the coated sand treatments, with higher concentrations in the treatments with higher percentages of coated sand. Concentrations decreased rapidly for all analytes with magnesium and sulfate concentrations similar in all treatments by the fourth fertigation. Manganese concentrations were similar by the sixth and calcium by the eighth fertigation. Chloride concentrations remained slightly elevated throughout the experiment. Data analysis is ongoing.
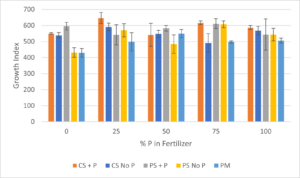
The second in-pot sorption experiment was initiated in November 2021 and lasted for 91 days with 13 fertigations. Growth index was determined for chrysanthemums grown in the different media types (coated sand +P, coated sand no P, plain sand + P, plain sand no P, and potting mix) fertigated with Hoagland’s solution at different P concentrations (0, 25%, 50%, 75%, and 100%) (Figure 4). Growth index by media type was highest for coated sand + P (589), followed by plain sand + P (575), coated sand without P (547), plain sand without P (527), and potting mix with the lowest (496). Growth index by fertilizer P concentration was highest for 25% P (569), followed by 75% P (565), 100% P (550), 50% P (541), and 0% P with the lowest (509).
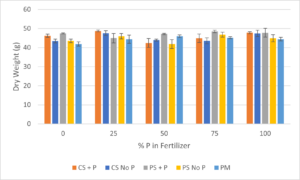
Dry aboveground biomass was also measured for the chrysanthemums (Figure 5). Dry biomass by media type was highest for plain sand + P (47 g), followed by coated sand + P (46 g), coated sand without P (45 g), plain sand without P (44 g), and potting mix had the lowest dry weight (44 g). Dry biomass by fertilizer P concentration was highest for 100% P (46 g), followed by 25% P (46 g), 75% P (45 g), 0% P (44 g), and 50% P fertilizer had the lowest dry biomass (44 g).
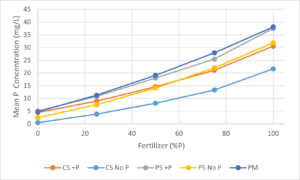
Leachate P concentrations mirrored the P concentration in the fertilizer with the lowest concentrations in the No P fertilizer and the highest concentrations in the fertilizer with 100% P (Figure 6). The potting mix supplied an initial amount of P to all treatments including the No P fertilizer treatment. The lowest leachate P concentrations occurred in the coated sand no P (CS No P) media. Leachate P concentrations in the coated sand +P (CS +P) and plain sand no P (PS No P) media were similar as were the plain sand +P (PS +P) and potting mix (PM) media.

The reduction in P loading (i.e., the total amount of P exported in the leachate) as compared with the amount exported from the potting mix treatments yielded similar results. The CS No P media had the greatest reduction in leachate P loading (Figure 7). The greatest reduction was with the No P fertilizer where 93% of the P leached from potting mix was retained. This dropped to 50% with the 100% P fertilizer. Surprisingly, the PS No P media was more effective at retaining P in the low P fertilizers (0 and 25%) however, the CS +P was more effective in the higher P fertilizers (50, 75 and 100%). It appeared as if both the CS +P and the PS +P sand were highly saturated at the beginning of the experiment. As coated sand has a greater sorption capacity for P it was able to sorb more as the experiment progressed and the plants took up the sorbed P.
The third in-pot sorption experiment was initiated in June 2022 with petunia and in July 2022 with chrysanthemum. For the pansy, plugs were grown in 4” pots for 34 days with six fertigations and five destructive harvests. The plants were then transplanted to 1-gallon pots and grown for an additional 36 days. For the chrysanthemum, plugs were grown in 6” pots for 63 days with nine fertigations and four destructive harvests. At this point it became apparent that light pollution was inhibiting flower initiation and the plants were terminated. Additional chrysanthemum plugs were acquired, and they were transplanted into 6” pots in October 2022. This experiment is ongoing.
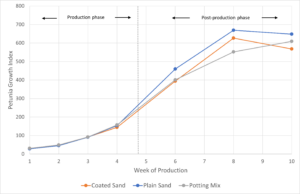
Growth index for petunias, calculated at each destructive harvest and at the end of 10 weeks of production, was highest for plain sand, followed by potting mix, and lowest for the coated sand (Figure 8). As seen in Figure 3, the growth index between the three media types did not begin to diverge and display differences until the post-production environment.
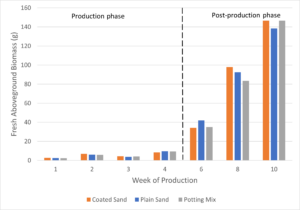
Both fresh and dry aboveground biomass were determined for petunias at each destructive harvest. At the end of 10 weeks, fresh biomass was highest for petunias grown in potting mix, followed closely by coated sand, with plants grown in plain sand having the lowest fresh biomass (Figure 9). There was little difference in fresh biomass between short-term plants grown in potting mix and plants grown in media amended with coated or plain sand.
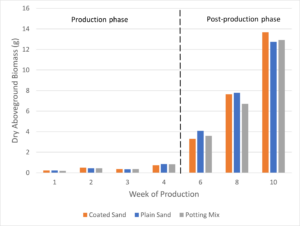
Dry biomass was measured after plants were dried for approximately 72 hours in a drying oven at 55 ºC. After 10 weeks of growth, petunias grown in coated sand had the highest dry biomass, followed by plants in potting mix, and plants grown in plain sand slightly lower than the potting mix group (Figure 10). In both fresh and dry biomass, petunias in the plain sand were the lowest out of the three treatment groups at the end of 10 weeks (138 g and 12.7 g, respectively) while petunias in potting mix were slightly highest (147 g) for fresh weight and in the middle (12.9 g) for dry weight. Petunias grown in the coated sand were in the middle for fresh weight (147 g) and had the highest dry weight out of the three treatment groups (13.7 g).
Data for petunia and chrysanthemum leaf and root tissue mineral nutrients via ICP is still being collected and analyzed.
This project demonstrated that:
- Most metals found in AMD either were not incorporated into the coated sand or were strongly bound and did not leach. However, AMD sources containing Sr, Cr, and As should not be used.
- Coated sand was an excellent phophate sorbent which can be used to either remove phosporous from leachate or be mixed with potting media to retain phosphorus within the pot.
- No detrimental effects on any of the plant species were observed even when the potting media contained 40% coated sand.
- Using coated sand as part of the potting media retained phosphorus within the pot allowing reduction in the amount of phosphorus applied in fertilizer.
- Experiments in progress will quantify effects on above and below ground biomass and mineral tissue concentrations.
Education & Outreach Activities and Participation Summary
Participation Summary:
In February of 2020, we attended the West Virginia University Small Farms Conference and surveyed consumer perception of iron-coated sand. We had 48 respondents. Of those respondents, nearly half were crop producers: farmers (33%), high tunnel (8%), and greenhouse (4%) producers. Home gardeners consisted of about one-third (31%), while 23% of respondents identified themselves as other. The majority of the respondents, 81%, felt that controlling phosphorus runoff is important. Also, 60% of the respondents indicated they were likely to use the iron-coated sand. When the respondents were asked how likely they were to purchase plants grown in coated sand, 77% indicated they were likely to purchase these plants. A small group (8%) of respondents would like to see an alternative source of iron for coating the AMD. In general, most of the respondents supported using the AMD iron-coated sand in the agricultural industry.
Additional Information on Why Participants Chose Their Answers:
- Of the 77% that indicated they were likely to purchase plants grown in coated sand, 25% cited environmental concerns as their primary reason (the most common reason), 22.2% cited crop quality as their primary reason, and 16.6% cited being open to trying something new as their primary reason.
- Of the 33% that were not likely to purchase plants grown in coated sand, 83% of those respondents said their primary reason was that they did not purchase plants (they grew from seed or cuttings). The remaining 17% said they needed more information before considering purchasing.
- This indicates that no one was directly opposed to the iron-coated sand.
- Of those 8% that wanted an alternative source, half said they needed more information on AMD before accepting it as a source.
- When asked if they would use iron-coated sand in their current operation, 26.7% were neutral towards the idea, and 2/3rds of those people cited needing more information on effects or costs as their primary reason.
- This indicates that education and research could influence more people to use the sand.
In August 2022, an oral paper entitled ‘Evaluation of an In-pot Phosphate Sorbent Produced from Acid Mine Drainage’ by Karen M. Buzby, A. Rhiannon Newton, Nicole L. Waterland and Lian-Shin Lin was presented at the American Society for Horticultural Science in Chicago IL.
Learning Outcomes
Not a part of this project