Final report for OS19-129
Project Information
Because the majority of vegetable farms in North Carolina are less than 5 acres, with many not relying on herbicides for weed control, it would be useful to understand how organic no-till vegetable production systems perform based on a variety of scale-appropriate equipment, and to define the spatial scale at which each system is profitable. During the 2020 growing season we evaluated the performance (cover crop termination success, weed pressure, and crop yield) of three small-scale, organic no-till vegetable production systems, using equipment appropriate for smaller scales (walk-behind tractor and associated equipment, and two manual methods), alongside their larger-scale counterparts (tractor-based) to determine the spatial thresholds that make no-till production feasible for small-scale vegetable growers. The cover crop was cereal rye (Secale cereale var. ‘Wrens Abruzzi’) and the cash crop was butternut squash (Cucurbita moschata var. ‘Atlas F1’). Cover crop termination equipment included a roller-crimper and a flail mower, drawn or powered by a tractor or walk-behind tractor, as well as a manual crimper and landscape fabric. A tilled and bedded treatment (with plastic mulch) was implemented as a reference using either a tractor or walk-behind tractor. Additionally, rye was crimped at two growth stages (late-flower and late-milk) to test termination success across crimping equipment (tractor, walk-behind tractor and manual), which vary substantially in weight per linear foot. All treatments were replicated four times at CFSA’s Elma C. Lomax Research and Education Farm (Concord, NC) and medium/small-scale no-till treatments (walk-behind tractor and manual) were implemented at Red Scout Farm (Black Mountain, NC; unreplicated). One additional farm, Living Web Farm (Mills River, NC) volunteered to replicate treatments but could not establish sufficient cover crop biomass for weed suppression. Treatments were discontinued at this site.
Cover crop biomass was adequate to suppress most early season weed species across treatments, but was not adequate to suppress ryegrass (Lolium species), brome (Bromus species) and crabgrass (Digitaria species) at Lomax Farm. Cover crop termination was successful (>90%) across all treatments, suggesting that larger-scale (heavier) equipment is not necessary for successful termination via crimping. Weed pressure was lowest in the landscape fabric treatment, and much higher in other treatments (mowed treatments were numerically but not statistically the highest). Butternut squash yield, collected only at Red Scout Farm due to crop failure at Lomax Farm, averaged 27,280 lbs/acre across treatments. Differences in yield were not tested at Red Scout Farm because treatments were not replicated, but average yield across treatments was higher than breakeven yields and therefore profitable.
Production costs, standardized for one acre of production, were driven by the combination of labor, equipment and materials costs, which varied substantially among treatments. Because weeding was performed manually in all treatments, production costs were highest overall in the mowed treatments, where weed pressure was high. In general, however, one-acre production costs were driven by equipment (tractor, walk-behind tractor or manual), with tractor treatments highest, followed by walk-behind tractor treatments, and manual treatments. One-acre cost of production at Red Scout Farm was somewhat higher than at Lomax Farm due to more time spent weeding, but followed the same pattern.
Analysis of spatial thresholds indicated that, at larger acreages (>3 acres), cover crop management method was more important for production costs than the equipment used, with mowed treatments being the most expensive, tilled treatments the least expensive, and crimped and landscape fabric treatments intermediate. At smaller acreages (<3 acres), equipment type was more important than cover crop management method, with tractor treatments the most expensive, followed by walk-behind tractor, followed by manual. The transition from equipment determining total production cost to method determining cost occured between 0.8 and 2.8 acres, depending on the method. Analysis of per-acre production cost, which accounted for economies of scale in tractor and walk-behind tractor treatments, indicated that per-acre costs decreased with increasing acreage in tractor and walk-behind tractor treatments, but not manual treatments. Additionally, per-acre production costs were highest in mowed treatments (above 1 acre), and lowest in tilled treatments (above 2 - 2.5 acres), and intermediate in crimped treatments. Per-acre production costs were lowest in the manual treatments among no-till methods up to at least 5 acres. Finally, maximum farmable acreage as a function of available labor hours was lowest in mowed treatments, highest in tilled treatments, intermediate in crimped and landscape fabric treatments.
Overall, among no-till methods compared, crimping was preferable to mowing, as weed pressure and associated labor cost were high in mowed treatments. It is likely that if no-till-specific cultivation equipment (high-residue cultivator) were used with a tractor and walk-behind tractor, total production costs would decrease dramatically, making these methods more competitive with manual methods at smaller acreages (<5 acres). Finally, the fact that tilled treatments out-performed no-till treatments by most metrics - owing to the efficiency with which plastic mulch can be applied for season-long weed suppression - highlights the need for improvements to organic no-till production systems. We recommend that soil testing should be routine practice before sowing cover crops in order to identify potential soil fertility issues that will impact cover crop biomass. We advocate that, in addition to adopting existing technology for high-residue cultivation, a new technology is developed to mechanize the application of landscape fabric or similar material, which could bring per-acre production costs for landscape fabric use down substantially to costs that are comparable to tilled with plastic mulch. We believe that without this technology, organic no-till vegetable production will always be limited by weed pressure and the labor required to address it, and will never be cost-competitive with tillage-based systems.
This research project tested the performance of three organic no-till cropping systems alongside a conventional-tilled one at two on-farm locations, using equipment appropriate for three spatial scales: tractor, walk-behind tractor, and manual equipment for large, medium and small scales, respectively.
Our objectives were to quantify:
1) cover crop termination success,
2) weed pressure (dry lbs/acre and/or time spent weeding),
3) butternut squash yield,
4) total production costs ($/acre spent),
5) profitability (net $/acre earned), and
6) spatial thresholds of production costs, profitability, and farmable acreage across equipment types and methods.
Cooperators
- (Researcher)
- (Researcher)
Research
Study Design and Implementation
The three organic no-till cropping systems consisted of a cereal rye cover crop that was terminated by crimping, by mowing, and by crimping followed by landscape fabric. These cover crop and weed management systems were implemented using a tractor, walk-behind tractor, or implemented manually. Mowing was not implemented manually, and landscape fabric was only implemented manually, owing to the lack of commercially available equipment for these purposes. Additionally, a conventional-tilled system (bedded with plastic mulch) was implemented using a tractor and walk-behind tractor as reference treatments, as these are the industry standard for butternut squash production.
The project was initiated In October, 2019, with the establishment of cereal rye (Secale cereale var. ‘Wrens Abruzzi’) at three locations: at CFSA’s Elma C. Lomax Research and Education Farm in Concord, NC (hosting institution; Figure 6), Red Scout Farm in Black Mountain, NC (cooperating farm; Figure 7), and Living Web Farm (Mills River, NC). Target seeding rate at all locations was 110 lbs/acre (approx. 1.98 million seeds/acre; 45 seeds/ft2). Rye was seeded with a drill at Lomax Farm, and broadcast seeded and raked-in by hand at Red Scout Farm and Living Web Farms. The project was discontinued at Living Web Farms because rye biomass at anthesis was extremely low (<1000 lbs/acre) and insufficient for weed suppression. Sufficient cover crop biomass was achieved at the other two locations.
Butternut squash (Cucurbita moschata var. ‘Atlas F1’) seeds were started in greenhouses in mid to late April or early May depending on location; approximately 2 weeks before the early rye termination date. A second round of squash seeds was started shortly thereafter, approximately 2 weeks before the second planting date (late-crimped treatments only).
The rye cover crop was terminated in April and May, 2020, using a mid-sized tractor (Lomax Farm only), a walk-behind tractor (10-15 HP), or performed manually. Rye termination methods consisted of mowing or crimping in all eleven treatments. However, in addition to simply mowing or crimping the cover crop, one treatment used supplemental cover (landscape fabric) after crimping manually, and two treatments were tilled and bedded with plastic mulch after mowing (reference treatments). Two flail mowers were used to implement the mowing treatments: one powered by a tractor (5’ mowing width) and one powered by a walk-behind tractor (2’ mowing width). Flail mowers were also used to terminate rye in the tillage (reference) treatments. Similarly, two roller-crimpers were used to implement two of the three crimping treatments: one drawn by the tractor (5’ width; 1200 lbs total; 240 lbs/ft) and on by the walk-behind tractor (2.5’ width; 500 lbs total; 200 lbs/ft; custom-built for this project; Figure 8). A manual crimper (1.5’ width; 180 lbs total; 120 lbs/ft; Figure 9) was used to implement the third, manual crimping treatment as well as the landscape fabric treatment. The manual crimper consists of 1.5” angle iron fastened to an 18” length of 2x6 lumber, which is attached to a rope held by the operator. Manual crimping is performed by stepping on the 2x6 (angle iron facing down), which is lifted and dropped underfoot repeatedly in 6”-8” intervals by the operator; thus, the down pressure (lbs/ft) is determined by crimper width and the operator’s weight. The smaller roller-crimper and the manual crimper were fabricated at Lomax Farm for this project. Additionally, crimped treatments were implemented at two rye growth stages to test for differences in termination success across crimper types, which vary substantially in down pressure (lbs/ft); early-crimped treatments were implemented at late flower to water ripe growth stage of rye (Zadoks 68-71), and late-crimped treatments were implemented at late milk to early dough rye growth stage (Zadoks 77-83).
The mowed and early crimped treatments were implemented May 1 at Lomax Farm and May 12 at Red Scout Farm. Late-crimped treatments were implemented May 14 at Lomax Farm and May 29 at Red Scout Farm. In the tillage treatments (Lomax only), rye was mowed once and roto-tilled twice in April, then bedded with plastic mulch on May 1. Squash was transplanted within one day of cover crop termination (no-till treatments) or making beds (tillage treatments). Treatments were replicated four times at Lomax Farm, although two replicates were lost to higher-than-expected weed and insect pressure. Treatments were not replicated at Red Scout Farm. Plot sizes were 30’ x 5’ at Lomax Farm and 20’ x 5’ at Red Scout Farm. Between-row spacing was 5’ and in-row spacing was 2’.
Rye biomass was collected immediately prior to termination from two 5.38 ft2 quadrats per plot, and was dried at 120⁰F for 30 days, then weighed. Rye termination success (%) was determined visually in each plot at one, three and six weeks after termination. Weed biomass was collected at Lomax Farm (July 23 for peak season weed biomass), but was not collected at Red Scout Farm due to different weed management strategies (ie. zero tolerance policy at Red Scout Farm, which minimized weed biomass at Red Scout Farm). In-crop weeding was performed with a string trimmer at both Lomax Farm and Red Scout Farm, with follow-up hand weeding at Red Scout Farm; time spent weeding was recorded for each plot for each weeding event. Butternut squash was harvested August 13 and 20 at Lomax Farm and August 20 and September 4 at Red Scout Farm. However, yields at Lomax Farm were very low due to a suite of production challenges - from early-season nitrogen limitation, to unexpectedly high abundance of Lolium, Bromus and Digitaria weed species, and to pressure from squash bugs (Anasa tristis) - essentially resulting in a crop failure, and therefore yield data from Lomax Farm were not used in the analysis.
Data Analysis
The cost of production was broken into three categories: 1) labor ($12/hour), 2) materials, fuel, and equipment maintenance, which scale with acreage, and 3) equipment, which does not scale with acreage. Labor was composed of cover crop establishment and subsequent management (including bed preparation in tilled treatments), squash seeding and transplanting, pest management (weeds, insects and disease), irrigation set up and management, harvest time, and field breakdown (removal of irrigation, landscape fabric or plastic mulch). Materials, fuel and maintenance costs consisted of all materials and fuel consumed in the squash production process, which scale with acreage, as well as equipment maintenance costs, which increase somewhat with increasing acreage. Equipment costs assumed a given purchase price and lifespan to calculate the annual cost of equipment ownership (minus maintenance costs, which are accounted for elsewhere). All production costs were annual, and were standardized on a one-acre basis, which is different from a “per acre” basis, because per-acre production costs decrease with increasing acreage as economies of scale are achieved with a tractor and walk-behind tractor.
Potential income from butternut squash sales was calculated using at $2/lb (a common direct-to-consumer price in North Carolina as of 2020), $1/lb, and $0.50/lb (approximate wholesale value), from which breakeven yields (lbs/acre) were calculated per treatment. Where yield data was collected and reported (Red Scout Farm), overall profitability was calculated for each treatment.
Finally, spatial thresholds were analyzed by scaling per-one-acre costs from 0.1 to 10 acres for all treatments, which allows some costs to remain constant regardless of acreage (ie. equipment) while allowing other costs to increase with increasing acreage (ie. materials and labor). This analysis captures economies of scale reached with larger-scale equipment, and identifies the acreage at which one equipment/method combination becomes more or less costly to implement than another.
For replicated data (cover crop termination, cover crop and weed biomass, and weeding time), differences among treatments were tested by linear mixed-effects model ANOVA, and means separated by Estimated Marginal Means using R v4.0.4.
Cover Crop Termination
Cover crop termination was successful (>90%) across all equipment types and termination methods 3 weeks after the late termination date, although termination success was somewhat higher in late-crimped treatments compared to early-crimped treatments (99% vs. 95%; p<0.001). The result that termination success was uniformly >90% across treatments indicates that - at least in this location and year - larger-scale (heavier) equipment was not necessary to achieve successful rye termination, and that delaying termination (eg. from late flower to late milk) is not required for small-scale equipment, thus opening up the cropping season by approximately two weeks. Earlier cash crop planting may or may not result in a yield benefit for all crops, but is generally thought of as a way to increase marketable yields across the season by enabling the use of longer-season varieties (often higher-yielding) or by increasing the harvest window before pest pressure limits yield.
Weed Pressure
Weed pressure at Lomax Farm, measured by both peak weed biomass (sampled in July) and time spent weeding, was not affected by equipment type (tractor, walk-behind tractor or manual) because weeding was performed manually across treatments. Interestingly, weed pressure was not affected by termination timing (early vs. late-crimped), despite somewhat higher cover crop biomass in the late-terminated treatment (7408 lb/acre vs. 6710 lb/acre, p=0.0099). However, weed pressure was strongly affected by cover crop & weed management method (crimp, mow, landscape fabric or till), where weed biomass was, unsurprisingly, lower in plots treated with landscape fabric (143 lbs/acre) compared to other methods (983-1168 lbs/acre; p=0.008). It was somewhat surprising that weed biomass in the tilled treatments averaged 1047 lbs/acre, where weeds grew only along plot edges where soil was tilled but not covered in plastic mulch. Time spent weeding at Lomax followed a similar trend: weeding time was lowest in the landscape fabric treatment (14 hours/acre), highest in crimped and mowed treatments (179 and 281 hours/acre, respectively), and intermediate in tilled treatments (35 hours/acre; p<0.0001). Weed biomass was high relative to weeding time in tilled treatments because weeds grew only along plot edges, making their control quicker than in crimped and mowed treatments, where weeds were evenly distributed.
Weed pressure at Red Scout Farm followed a similar pattern to Lomax Farm, although weeding time was substantially higher on a per-acre basis, owing to a zero weed tolerance policy at Red Scout Farm in combination with a much smaller study area that was more manageable with limited staff. Weed biomass was not quantified at Red Scout Farm as a result of this policy. Time spent weeding was lowest in plots with landscape fabric (15 hours/acre) and much higher in other treatments, especially mowed treatments (494 hours/acre). In contrast to Lomax Farm, weed pressure at Red Scout Farm appeared to be influenced by termination timing, with early-crimped treatments requiring more time to maintain weed free (357 hours/acre) compared to late-crimped treatments (241 hours/acre). While treatments at Red Scout Farm were not replicated (although crimping timing was effectively duplicated and consistent across walk-behind & manual methods), and results should be interpreted cautiously, the difference in weed pressure between early- and late-crimped treatments at Red Scout Farm suggests that in some years or locations - particularly where weed pressure is high - growers may benefit from delaying crimping to maximize cover crop biomass, possibly reducing weed pressure over the course of the season.
Finally, regarding time spent weeding across treatments: weeding was performed manually across all treatments, including treatments based on tractor or walk-behind tractor use, and it’s likely that weeding time could be reduced in those treatments if a suitable high-residue cultivator was used for weed control. Because weeding time drove total labor hours (see below), the ability to take advantage of existing tractor-scale equipment (or custom-built equipment for a walk-behind tractor) could dramatically improve the profitability and spatial thresholds for tractor and walk-behind tractor production systems.
Yields
Butternut squash yields at Lomax Farm are not reported due to a near crop failure that resulted from a suite of production challenges, primarily pressure from Lolium, Bromus and Digitaria weed species and from squash bugs (Anasa tristis). Yields at Red Scout Farm, however, were much higher, and ranged from 3.5 - 8.8 lbs/plant (15,125 - 38,100 lbs/acre; average of 27, 280 lbs/acre) across treatments. Yield was highest in the landscape fabric treatment (38,100 lbs/acre), and lowest in late-crimped treatments (17,105 lbs/acre averaged across manual and walk-behind). Yield in mowed and early-crimped treatments were intermediate (25,385 and 33,000 lbs/acre, respectively). It is not clear why yields were low in both late-crimped treatments (walk-behind tractor and manual), where weed pressure was low. Because treatments were not replicated, yield data from Red Scout Farm were averaged across treatments in the subsequent economic analysis, and no yield data from Lomax Farm was used.
Production Costs
The cost of butternut squash production (for one acre, per year) for each system at Lomax Farm varied widely from $4,317/1-acre - $8,145/1-acre (Figure 1A). These production costs were driven, first, by labor costs ($1544/1-acre - $4365/1-acre), which in turn were driven by time spent weeding (Figure 2), and therefore were strongly influenced by treatment. Labor costs were lowest in the tilled treatments ($1,688/1-acre, averaged across tractor and walk-behind tractor), where beds could be set up efficiently and where weed pressure was low on account of plastic mulch. While time spent weeding was lowest in the landscape fabric treatment, labor costs were somewhat higher ($2,611/1-acre) than in tilled treatments because the application and breakdown of landscape fabric is not mechanized and must be performed manually, unlike plastic mulch in the tilled treatments. Labor costs were highest in the mowed treatments ($4,290/1-acre, averaged across tractor and walk-behind tractor) due to time spent weeding, and intermediate in the crimped treatments ($3,147/1-acre, averaged across all six crimped treatments). Equipment costs were the secondary driver of total costs for one acre per year, where the annual cost to own a tractor and associated equipment was the most expensive ($2,912/1-acre averaged across tractor-based systems), especially equipment for the tilled system ($3,375/1-acre). The annual cost to own a walk-behind tractor and associated equipment was approximately half that of a tractor ($1,412/1-acre averaged across walk-behind tractor-based systems), and the cost of equipment for the tilled system was highest in this category as well ($1,725/1-acre). Among manual treatments, the cost of the manual crimper was negligible ($2/1-acre) compared to tractor- and walk-behind tractor-based systems. The cost of materials, fuel and maintenance was consistent across all crimped and mowed treatments (average of $1,068/1-acre), but higher for tilled ($1,500/1-acre) and landscape fabric ($1,760/1-acre) treatments, owing to the cost of plastic mulch and landscape fabric. Total cost of production at Red Scout Farm was higher overall due to more time spent weeding, but followed a similar pattern across treatments, with overall costs similar among manual treatments (crimped and landscape fabric), highest in mowed, and intermediate in roll-crimped treatments (Figure 1B)
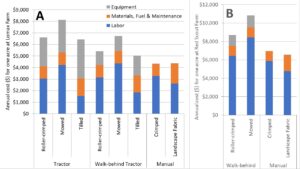
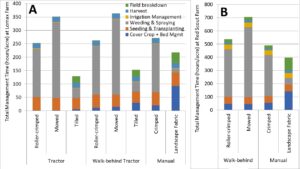
Breakeven Yields and Profitability
Breakeven yields, based on butternut squash value of $2/lb, ranged from 2,159 - 4,073 lbs/acre at Lomax Farm, were lowest in manual treatments (due to low production costs), and highest in the tractor-based treatments (due to high production costs). Breakeven yields in mowed treatments were higher than all other treatments (4,073 and 3,365 lbs/acre for tractor and walk-behind tractor treatments, respectively). Breakeven yields were higher at Red Scout Farm due to the higher cost of production (from weeding time), ranging from 3,270 - 5,415 lbs/acre, and followed a similar pattern across treatments. Because achieving $2/lb squash value may be limited to direct-to-consumer markets, where 1+ acre of a single crop is not often grown, two other $/lb scenarios were used to determine breakeven yields: $1/lb and $0.50/lb. In these scenarios, breakeven yields ranged from 4,317 - 8,145 lbs/acre ($1/lb) and 8,635 - 16,290 lbs/acre ($0.50/lb) at Lomax Farm. While yields were only reported for Red Scout Farm, butternut squash yields were substantially higher than breakeven yields, averaging 27, 280 lbs/acre across treatments. Because of this, butternut squash could be valued much lower to breakeven at 27,280 lbs/acre - as low as $0.40/lb in the most costly-to-produce treatments, mowed.
Profitability (net $/acre), determined only for Red Scout Farm due to crop failure at Lomax Farm, ranged from $43,730/acre - $48,019/acre, using average squash yield (27,280 lbs/acre) and squash valued at $2/lb. Similar to analysis of breakeven yield, we explored two other valuation scenarios to determine profitability when squash is valued lower: $1/lb and $0.50/lb. In the $1/lb scenario, profitability ranged from $16,450/acre - $20,739/acre, and under the $0.50/lb scenario, profitability ranged from $7,810/acre - $7,100/acre (based on average yield value of 27,280 lbs/acre).
Spatial Thresholds of Production Costs and Time
The spatial analysis indicated that, overall, when scaled from 0.1 - 10 acres, the total cost of production increased linearly with acreage for all treatments, but increased the most per acre in mowed treatments, and the least per acre in tilled treatments, owing primarily to differences in time spent weeding. At larger acreages (greater than approximately 3 acres), cover crop and weed management methods (crimp, mow, landscape fabric or till) were more important for total production costs than the equipment used (tractor, walk-behind tractor or manual), with mowed treatments being the most expensive, tilled treatments the least expensive, and crimped and landscape fabric treatments intermediate (Figure 3A). At smaller acreages (less than than approximately 3 acres), equipment type was more important for total production costs than cover crop and weed management methods, with tractor treatments the most expensive, followed by walk-behind tractor, followed by manual (Figure 3B). This transition in the importance of equipment at smaller acreages to method at larger acreages occurs between 0.8 and 2.8 acres, depending on method or equipment (Figure 3B). Thus, the critical farm acreage for selecting equipment and method (based on total production costs) ranges from approximately 1-3 acres, depending on preferred method or equipment.
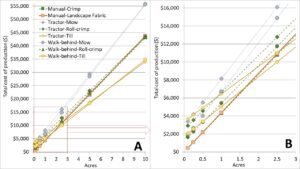
When cost data are expressed on a per-acre basis (distinct from total cost, presented above), per-acre costs decreased with increasing acreage for tractor- and walk-behind tractor-based treatments, as economies of scale are achieved and the cost of equipment is spread across increasing acreage. In contrast, per-acre costs of manual treatments remained essentially the same with increasing acreage, because economies of scale can not be achieved without equipment (Figure 4). Similar to total production cost results, per-acre costs were highest in mowed treatments, lowest in the tilled treatments (above 2 - 2.5 acres), and crimped and landscape fabric treatments were similar (above 3 acres) and intermediate between these. These results indicate that per-acre costs are more sensitive to cover crop and weed management methods (crimp, mow, landscape fabric and till) than to the equipment used (tractor, walk-behind tractor, and manual) above 2 acres (although per-acre costs of mowed treatments were highest regardless). Results also indicate that manual methods are surprisingly efficient ($/acre spent) and competitive with tractor- and walk-behind tractor-based technologies: they’re cheaper per acre than roller-crimper (mechanized) treatments up to at least 5 acres, and consistently cheaper per acre than mowed treatments, regardless of acreage. Similarly, walk-behind tractor treatments were cheaper ($/acre) than their tractor-based counterparts to at least 5 acres. These results indicate that per-acre costs of tractor-based treatments are more expensive than manual or walk-behind treatments up to at least 5 acres. It should be reemphasized, however, that production costs were driven by time spent weeding, and weed control in tractor and walk-behind tractor treatments was performed manually; thus, it’s likely that production cost could be decreased substantially in these treatments if equipment-based weed control (using high-residue cultivation) could be implemented.

The final component of the spatial analysis is the effect of each treatment on maximum farmable acreage as a function of available labor hours (40 hours/week for the 5-month production period is approximately 850 hours). Maximum acreage achievable in this 5-month full-time equivalent scenario was, among no-till treatments, highest for the landscape fabric treatment (3.8 acres), followed by crimped treatments (3.2∓0.2 acres), followed by mowing treatments (2.4∓0.1 acres; Figure 5). Maximum farmable acreage in the tilling treatments was highest (5.6 acres, walk-behind tractor; 6.6 acres, tractor). Similar to total cost and per-acre cost results, if suitable weed control equipment were used in tractor and walk-behind tractor treatments, then the maximum farmable acreage could increase substantially.
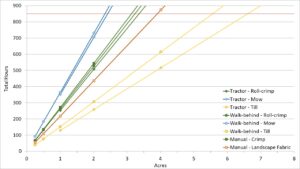
Conclusion
In conclusion, among the no-till methods compared in this study, it is clear that crimping was preferable to mowing, given the intense weed pressure and resulting drag on both profits and yields. In this particular year at Lomax Farm, where weed pressure was high and weeding was performed manually across all treatments, the cost of weeding drove economic and spatial results, making manual methods efficient ($/acre and hours/acre invested) and profitable, and competitive with their mechanized counterparts (especially below 3 acres). Additionally, the relatively low hours/acre invested when using landscape fabric enables more acreage to be covered (3.8 acres in 850 hours) compared to crimping and mowing (2.4 - 3.2 acres in 850 hours), and if higher yields on landscape fabric (as demonstrated at Red Scout Farm) are consistent across locations and years, it may prove to be the most profitable no-till method - limited perhaps by available labor hours and not upfront costs.
Finally, the fact that tilled treatments outperformed no-till treatments by most metrics (weed pressure, costs per acre, scalability) - owing mostly to decreased weed pressure, resulting in less time invested and higher yields per acre - highlights the need for improvement in organic no-till systems.
We see two options for improving organic no-till vegetable production:
Option 1) To mechanize weed control in crimped or mowed systems - with a strong preference for crimping to mowing - to drive down overall production costs by decreasing time spent weeding, and to potentially improve yields. Cover crops should also be managed to ensure high biomass and consistent termination for good weed suppression, and soil nutrients should be managed to account for nitrogen tie-up and the slow release of nitrogen by cover crops upon decomposition. While fertigation technology can address in-crop nitrogen limitation imposed by slow-to-decompose cover crop mulches, and hand weeding can be used in high-value crops, it is our opinion that crimped and mowed systems for most vegetable crops will always be hamstrung by limitations in in-crop weed control (especially by in-row weeds), regardless of whether high-residue cultivation can be implemented. This is because in crimped and mowed systems there is a high risk of weeds setting seed in any given year, leading to higher weed pressure and ever-more-challenging weed control in subsequent years.
For this reason we are in favor of Option 2) development of a new technology to mechanize the application of landscape fabric or similar material to provide season-long weed suppression and improve nutrient supply to crops from more rapid decomposition of cover crop mulches. A technology such as this, if affordable like many plastic mulch layers, could bring successful organic no-till vegetable production within reach for many more farmers, and have similar yield and economic benefits that plastic mulch had several decades ago, as well as significant benefits to soil health and on-farm conservation.
Thus, we advocate that agricultural engineers and the agricultural equipment industry work to develop and deploy such a technology, as we see it having multiple benefits to soil health, natural resource conservation, and bottom lines compared to other methods and equipment tested in this project. However, in the meantime, we advocate for the use of better in-crop weed control (high residue cultivation) and skillful weed and nutrient management outside of the crop production window covered by this project.
We are looking forward to a second year of this project, to be implemented during the 2021 growing season (funded separately).
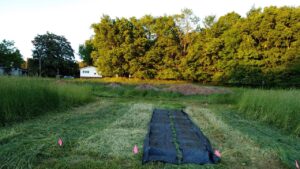
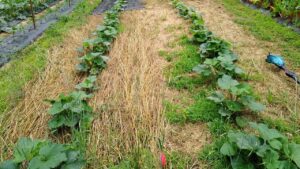
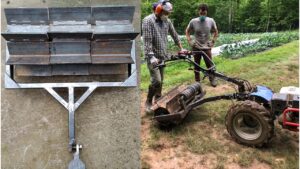
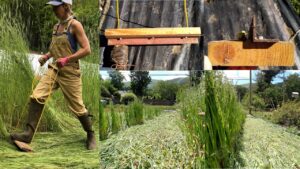
Educational & Outreach Activities
Participation Summary:
One hundred and ten total participants attended two virtual workshops: “Small-Scale No-Till: Successes, Challenges & Financials” webinar presented at CFSA’s 2020 Sustainable Ag Conference in collaboration with Mary Carroll Dodd and Howard Allen (Nov. 5, 2020; 83 participants); “Small-Scale No-Till: Methods, Profits and Scalability” webinar (Mar. 31, 2021; 27 participants). Study findings will be publicized in CFSA's email newsletter, "Expert Tips", in May of 2021.
Learning Outcomes
Project Outcomes
Project outcomes:
- Cover crop termination was successful (>90%) across all treatments, regardless of method used or termination timing (late flower vs. late milk). This suggests that early termination or the lighter equipment used in smaller-scale production is sufficient for successful cover crop termination.
- Weed pressure was lowest in the landscape fabric treatment, and much higher in other treatments. Weed pressure in mowed treatments was numerically but not statistically the highest; this was likely not significant due to the lack of statistical power (n=2) to identify differences.
- Unfortunately, butternut squash yield data was collected only at Red Scout Farm due to crop failure at Lomax Farm. While differences among treatments can’t be tested with this unreplicated data, the average yield across treatments was higher than the highest calculated breakeven yield, indicating profitability regardless of treatment.
- Production costs, standardized for one acre, were highest overall in the mowed treatments, where weed pressure was highest. In general, however, costs were highest for tractor treatments, followed by walk-behind treatments, followed by manual treatments. Within each equipment type (tractor and walk-behind tractor), one acre production costs for crimped and tilled treatments were approximately the same.
- When production costs were expressed per-acre and scaled from 1 to 10 acres, which accounts for economies of scale from using equipment and the strong influence that manual weeding had on economic results, tilled treatments cost the least to implement overall, and less than manual treatments above 2 - 2.5 acres. Mowed treatments were consistently the highest. Per-acre cost to implement manual treatments was the same regardless of acreage, and the manual crimped treatment was cheaper to implement the mechanized counterparts (tractor and walk-behind tractor) up to at least 5 acres.
- Similarly, the total cost of production (as opposed to per-acre), scaled from 0.1 to 10 acres was highest overall for mowed treatments and lowest for tilled treatments (>3 acres). At smaller acreages (<3 acres), equipment type (tractor, walk-behind tractor and manual) was more important for total production costs than method (crimp, mow, landscape fabric and till), with tractor treatments the most expensive, followed by walk-behind tractor, followed by manual. The change in importance from equipment type at small acreages to method at larger acreages occurs between 0.8 and 2.8 acres, depending on the method/equipment.
- Maximum farmable acreage, as a function of available labor hours, was lowest in mowed treatments (2.4∓0.1 acres), highest in tilled treatments (5.6 - 6.6 acres), and intermediate in crimped (3.2∓0.2 acres) and landscape fabric (3.8 acres) treatments. This metric was influenced mostly by time spent weeding, highlighting the need for mechanized weed control (high residue cultivation) in tractor and walk-behind tractor plots.
Recommendations (for future study):
- Further research should investigate the impact of mechanizing weed control in no-till treatments (ie. high-residue cultivation) on weed pressure, crop yield, production costs, profitability, and spatial thresholds. It is with this critical information that we will better be able to determine how tractor- and walk-behind tractor-scale methods compare to manual ones, and the acreages at which each equipment/method combination are more or less costly to implement or profitable.
- Further research should also investigate the feasibility of engineering and fabricating equipment that can mechanically apply and remove landscape fabric in order to overcome the constraints of manual application/removal, which make landscape fabric much more costly. We believe that without this innovation, organic no-till vegetable production will always be limited by weed pressure and the labor required to address it, and will never be cost-competitive with tillage-based systems.