Final report for FNE16-854
Project Information
The purpose of This project was to develop alternatives to tote bag drying and storage for farm-grown grains in the Northeast.
In our study, we constructed 4 black plastic grain bins, made out of a 42 inch culvert mounted to a plastic pallet, with a perforated floor inside to allow for ventilation and drying. We constructed 2 of the bins with slanted floor and roof and 2 with flat roof in floor for comparison to see if they allow easier flow out the bottom door. Both versions had the same material cost around $750 dollars per bin, but the slanted roof bin had more than double the time 24 plus hours vs 12 hours on the flat roofed bins which are also stackable (while the slanted bins are not stackable).
The finished bins performed excellently in drying grain in tough, humid conditions as compared to plastic totes (or wood bins). With an added fan, the grain can be dried down to the levels that buyers want at shipping.
The Pros:
-
- Ability to add Heat
- Do not need a forklift to hold up for filling
- Stackable
- Rodent proof
- Even dry down with faster dry down rate
- Will not degrade in sunlight
The Cons:
- Cannot empty grain all the way without assistance ( approximately 5 minutes with broom or shovel)
For outreach during this project I reached out to many of my local grain farmers to let them know of my project and I have a steady 'trickle' of farmers bringing grain to be custom cleaned in my facility who learned about the project.
I also presented at the 2019 Maine grain conference as well as posting over an hour of video documentation with construction instruction, list and cost of parts, and dry down comparison of different blowers, on my YouTube channel RustedRoosterFarm. The links to these videos are also provided with this project in the Project Product area.
For myself, I will also continue to use these and post any new ideas/updates to them on my YouTube channel. Viewers and readers here are encouraged to send me an email at RustedRoosterFarm @gmail.com for questions or suggestions.
Current mobile grain bin plans are pallet mounted wooden grain bins posted on farm hack.com, and a trailer mounted metal bin designed by Jack Lazor of Butterworks farm in Vermont and plans can be found in his book “The Northern Grain Grower”.
Our proposal utilizes the versatility of pallet mounted storage units while adding aeration for drying and mostly pre-made components for ease of assembly and outside all weather storage.
- The proposed solution is to to manufacture a reusable pallet mounted grain bin constructed from plastic culvert and pre made components for ease of assembly. Versatile Permanent storage provide opportunities to store small hi-value commodities with built-in dry down capabilities to protect and preserve quality in crops harvested at higher moisture making early harvest for quality reasons more profitable. The farmers involved in this project including project leader Sean O'Donnell of Rusted Rooster Farm in Parkman, Maine. Collaborating farmer Dorn Cox of Tuckaway farm in Lee new Hampshire . Effectiveness was measured in terms of cost of and ease of construction, grain loss due to spoilage, rodents, stackability, dry down time and ease-of-use.
2018 objective update I no longer expect to get the whole group of farmers ( originally had two other cooperating Farms) together as some have not been in contact with me as well as one started a full-time job doesn't have time. We do however have a new objective due to the difficulties of drying in Tote bags with the bins being airtight we should be able to recirculate the air with a dehumidifier to constantly dry during cloudy weather or even winter months. The ability to very easily add supplemental heat in the form of a space heater which did improve fall and winter drying vastly.
2019 update originally we were supposed to cooperate with two other farmers but could not get schedules to line up and they ended up not being able to be involved, which is worth noting for future projects. There was also more Construction than I anticipated as I was unable to purchase satisfactory caps for the culvert. I was successful in building the bins and documented it very well in video form which is posted on my YouTube channel Rusted Rooster Farm the video links will be available in the product section of this report
The problem we found arises from the lack of long-term storage options for the small scale diversified grain farms.
Current storage options include large silo type steel bins which cannot be cost justified for farms growing ten or
less acres of each crop,larger metal bins are not designed for smaller volumes of diverse varieties and crop types
that are typical of direct market grain bean and oil seed markets.
On my farm in 2015 I cropped 60 acres with 18 separate crops. Current storage consists of plastic tote bags
though inexpensive are less than ideal for long term storage as they are easily chewed through by rodents, are
not weatherproof proof and have to be stored inside. Tote bags have a usable lifespan of one year which creates
plastic waste and is an added annual expense, these problems provide a significant risk to grain and seed quality
impacting farm profitability.
Wooden bins on pallets using plywood require a substantial amount of time and skill in building a rodent proof
enclosure and and are not suitable for outside storage.
Metal are bins are less than ideal because of expense of materials, weight and condensation issues and have to
be stored inside.
The purpose of this project is to provide a solution for small farms looking to dry their valuable niche grain crops viably in the Northeast without having to purchase large very expensive bins. As well as providing a superior alternative to tote bags that has been the norm for small grain farms in the Northeast. Let's little deeper look into some of the drying dilemmas that we have in the Northeast that has been forgotten by the grain industry. The experience of drying down grain in higher humidity environments that Southern and Midwestern states don't have experience drying in. I first encountered this problem when I started drying grain I was not able to get enough air flow to the tote to properly dry, I thought there must be a better way and I believe there is over the years I've also become more experienced drying in a tote bag adding larger more powerful fans getting decent results as well as learning the unavoidable pit fall of drying in a tote bag including uneven grain drying IE the corners in the bottom don't dry well the ability to only dry when humidity is low which doesn't happen very often in the Northeast as well as vulnerability to pests and the inability to store outside.
I believe this project will give insight into a field where there is no information available as I have successfully dried grain down from 22% moisture to bread quality wheat Which is far above the recommended Harvest moisture.
Now after Construction and testing I am confident that these Bins will improve my grain drying and handling immensely, I was able to dry grain from 16% moisture to 12% moisture in about 8 hours with a little supplemental heat I would have been unable to accomplish that with drying in a tote bag. The other upsides include not needing a forklift to hold the bag up for filling, they are stackable and rodent-proof.
Cooperators
- - Technical Advisor
Research
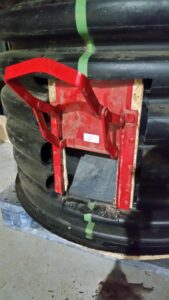
Slanted roof grain bin
May 2016. Purchased Culvert caps from a company called caplugs, after finding out Culvert caps that size are not readily available. Caps arrived were kind of cheesy, we decided to use them for the the bottom but not the top and would suggest just using a piece of plywood for the bottom of the future.
October 2016 over the summer purchased the culvert, plastic pallets, and grain Gates. Also remembered how busy summer season gets and didn't have a chance to work on it other than accumulating the supplies.
May 2017. Purchased perforated flooring from a company called McNichols who proved to be the cheapest source, it was very good quality, we ordered galvanized so that wouldn't be a problem with rust in the future.
Fall 2017. After things not working out over the summer because of busy season for farmers, I decided to set a date of December 2nd and 3rd for bin Construction and who ever showed up could help.
December 2nd and 3rd I worked on the bins the 2nd and Dorn Cox showed up to help on the 3rd at the end of which Dorn was able to take home a mostly finished bin that he is going to finish at his house.
After some of the problems we ran into I decided to finish Construction of the remaining three bins by myself so I can refine the process one bin at a time. 2018 Constructed another Bin struggled to make it and efficient Construction due to the angles on the roof and the flooring complicating assembly. video taped multiple construction steps just to find a easier way to do it. I decided I will be constructing the other two bins with flat tops and flat floors and was able to present specific specs and measurements as to how to build the Bin. I was not able to accomplish that with the slanted floor version it seems like you had to be advanced mathematician to get the slanted oval standardized and I ended up just custom cutting each piece one of the time. Dorn Cox of New Hampshire was also able to finish the bin that we sent with him last fall and is preparing to test it out also. I have finished constructing the last two Bins, as well as documenting the difference in construction time in difficulty between the flat bottom and the slanted bottom as well as posting a how to step-by-step Construction directions via a video posting on my YouTube channel. January March 2019. I started drying down grain that I was unable to dry with the tote bag method that fall as well as documented the differences in dry down time. I am also experimenting with some drying options including dehumidification which I update on my YouTube channel when I get it to work right, and adding supplemental heat which worked quite well. March 2019. Presented my experience at the maine grain conference. I will be posting the results on the neeograin list serve when this project is complete .
At the time of construction we decided on a slanted roof to shed rain snow it can also overhang to protect the grain gate from the elements. Because of that we had to cut the Culvert at an angle, we decided to use the same angle for the roof and the floor. By sectioning a culvert in four pieces we were able to cut it in half first, then cut the remaining two pieces at an angle to produce two pieces each with an angle on one side.
Cutting the Culvert on an angle presented to be more trouble than we thought I first used a piece of flashing to measure a 1 foot drop from 5'6" to 6'6" on the opposing side over the culvert. I bent the flashing around the culvert to use as a straight edge the problem with this method was it ended up with the Peak at the top High Valley at the bottom, after that we moved on to making a square out of wood they could be placed over the culvert and a straightedge traced up to the edge and We re cut it, after finding it was still not even enough for the roof to seal against it. From there we decided to cut a plug out of foam board to match the angle of the floor and the ceiling then put that inside of the culvert and spray-painted one side.
This proved to be the best method because then we were able to cut the cover from the inside and eliminate the Sawzall blade from waving up and down as it went through the different layers of the culvert at least we had a clean cut on the inside ceiling surface.
After which we were able to use the same plug to lay out on the perforated flooring and cut the oval to match the angle. Next we use two by fours as legs just to support the floor cross members we laid the Culvert on its side and pushed it up against a straight wall, which made it easy to climb inside and secure the stringers to match the first one then used a straight edge to make sure they were all even after which the floor was set on top and screwed down then the lower cap could be put on I used spray foam around the edge to seal it.
In 2018, after struggling with the slanted floor bins, we decided try to flat roofed bins thinking it did make the construction process much faster. Bins are still be weather tight accomplished by using a solid piece 4 foot plywood for the flat roof as well as a small Hood over the grain gate we have modified the bottom sealing method from spray foam 2 polyurethane seal which will also be used for sealing for ease of deconstruction to clean underneath perforated floor. Flat roofs will also enable stacking the bins. We were able to overcome the lack of slanted floor by securing it to the Fork carriage via strap or chain to tip it for emptying the final contents. We did test the two bins against each other to see if there is any irregularities and drying the slanted floor one with uneven grain depth there was no difference. I made a video on the cost breakdown and source of materials to construct this bin the time on the flat Roof bin was 12 hours versus 20 + on the slanted roof one.
In retrospect it was probably a little optimistic to think that I would be able to arrange for all the farmers to get together in the same place all at once we all tend to have pretty busy schedules. Because of that I think it's in the best interest of the project for the farmers that want to construct their bins do that. The only one that opted to do that was Dorn Cox. I did finish the other bins allowing me to figure out the fastest way to construct them.
I also received a $1000 grant from the Maine grain alliance to construct a bin out of a infiltrator im-540 water tank which will be more expensive materials but easy to construct. I will post a comparison on my youtube channel upon completion of that project.
In summary I was successful at building reusable bins which are very user-friendly. I intend to continue to build Bins of this style for use on my Farm as they are an ideal modular way to store 1500 pound grain Lots which will make drying and storage a single task adding much needed efficiency to that part of the process.Education & Outreach Activities and Participation Summary
Participation Summary:
At Rusted Rooster Farm during the 2017 grain walk I showed the attendees the Culvert and the other Construction Supplies and outline to them the construction process.
I posted all the videos of how to Construction on my YouTube channel which is rustedroosterfarm, there are six videos under the Sare Grant grain bin playlist.
The Maine grain conference in March 2018 was canceled due to weather, I did have attendees at my farm tour but no farmers that were at the point of needing this type of grain storage, most others were to attend due to busy Farm schedules. At this time I feel the best Outreach will be done over the internet and posted multiple step Construction and testing videos on YouTube. I will be posting that link on the neeograin listserv as well as my website opon completion of this report. I hope I have covered the whole process well but if anyone has questions, comments or improvements you can always contact me at rustedroosterfarm gmail.com
March 2019. Presented results at 2019 Maine grain conference.
Learning Outcomes
- It turned out to be decent size project with more construction and I was anticipating too build the slanted floor bins 20 + hours vs 12 hours for the flat bin. You have to be willing to do some construction and I would not advise building the slanted floor Bin as it was very complicated.
In hindsight I think a plywood bin will be able to be built about as easily but probably not the have the upside of stackability outdoor storage and lasting forever like the plastic one as well as easy cleaning ability.
Project Outcomes
In 2018, with the wet rainy season around Harvest that we had this year, we had some challenging drying conditions in which I was unable to dry the grain all the way down to 12% moisture in the tote bags the majority of my Harvest went into the winter with about 15% moisture, after completing the bins I was able to use them to dry 1500 pound batches down to 12% moisture using supplemental heat in the middle of winter which was something it impressed me very much including making me much more comfortable growing corn and beans to get harvested just before the first snow usually around here (Maine )
When drying with supplemental heat I used a 40000 BTU space heater supplying 80f-90f to dry 2 bins in 6-8 hours, it is very important to monitor the temperature if you are trying to Market your product as seed or bread quality, you do not want the temperature to go 110 degrees or damage will occur. To accomplish this I used a pocketlab weather sensor which I would highly recommend for monitoring while adding supplemental heat. There is a detailed video drying options and monitoring in the products section of this report.
I think the largest obstacle was trying to get so many farmers to work together in hindsight it might have just been easier to just build good prototype bins for an example and not worry so much about trying to get everybody to cooperate. Possibilities for different drying and storage include, being able to pipe a dehumidifier into the loop and dehumidifier the same air over and over again as it passes through the grain allowing for drying in any condition. Also the closed loop what allow for a quantity of dry ice to be placed in the loop it would kill any pests inside of the grain by carbon monoxide poisoning and then could just be vented with the top open when the procedure was complete. I believe we did address the issues with tote bag drying in this study, the bins are far superior in all way to tote bags, however do have a larger cost as well as construction time. I believe the trade-offs are well worth it at least to have the number of these on the farm it broadens your possibilities takes a lot of frustration of the drying and storage process. I am hopeful that the grain Alliance Grant Ben will be much easier to construct although I already know it is going to be harder to clean the grain out of the bottom because of only having a 24-inch opening in the top. It will also have a storage capacity of around 3000lb if you are interested that project you can subscribe to my YouTube channel and I will be posting that construction process as well as outcomes there when it's finished. Most Diversified Farms in the Northeast this size tend to be less concerned with a little extra cost and drying if we can keep the quality good with the unfavorable weather we sometimes have.