Final report for FNE18-888
Project Information
A critical bottleneck to growth and development of the oyster aquaculture industry in New Jersey, is the limitation of hatchery and nursery capacity for seed production. Growers that do not have access to shore-side nursery sites often nursery seed in the field where environmental control is not possible and many challenges persist. Little attention has been paid to optimize strategies for the field nursery of 2-4 mm oyster seed. This study evaluated the performance of field nursery methods for growing out 2 mm oyster seed at a high energy, inter-tidal farm site in the southern Delaware Bay, NJ. A crossed factorial experimental design was used to test the performance of cage type (Low Pro with spat bag and SEAPA with 1 mm sock), position (fixed or floating), and stocking density (2000 and 8000 seed per cage). Survival, growth, and shell morphology were tracked for 12-weeks.
All methods were effective for the field nursery of seed with survival averaging 84%. Overall, seed grown in floating cages grew faster than seed grown on-bottom, likely reflecting the greater amount of time in the water as compared to the bottom cages, which were exposed to air at low tide. Both field methods out-performed hatchery upwellers in respect to growth. Shell shape was influenced by cage type, deployment method, and sometimes density. Fan index (roundness) tended to be higher in seed grown in floating cages, while cup index (depth) tended to be higher in seed held in on-bottom cages. Seed grown in floating cages had a higher proportion of non-normal hinges than those grown on-bottom and in upwellers. Stocking density, within the range evaluated, had little effect, the higher density of 8000 oysters is recommended given savings in gear utilization. SEAPA cages with socks showed little wear, holding up better than spat bags. Careful attention was necessary to control fouling, enhanced cleaning would likely improve survival.
The goal of this effort was to develop new methods to maximize seed performance at an intertidal field nursery. The project examined four key production questions:
- What type of container promotes the best seed performance?
- Is it better to deploy the seed container off- bottom or at the surface of the water column?
- Is better seed performance achieved at high stocking density or low stocking density?
- Which combination of container type, container placement, and stocking density promotes the best seed performance with the least cost?
The development of best field nursery practices for the Delaware Bay will enable Sweet Amalia Oyster Farm and other oyster farms that do not have land or shore-based nurseries to reduce farm risks and enhance product quality and production, and hence farm profitability.
One of the biggest challenges facing growth and development of the shellfish aquaculture industry in the mid-Atlantic, and likewise in New Jersey, is the limitation (bottleneck) in seed production and nursery capacity. The Rutgers University New Jersey Aquaculture Innovation Center (AIC) is presently the only hatchery in New Jersey that regularly produces oyster seed, and many of New Jersey oyster farmers rely on this seed source. In an effort to meet the increasing demand for seed of a rapidly growing industry, the AIC stopped selling larger field ready seed in order to produce a greater number of seed, shifting nursery production to growers. Few industry members have appropriate waterfront properties to establish typical land-based upweller and raceway nursery systems. Direct planting of small seed to the field, particularly to intertidal rack and
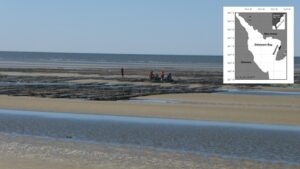
bag farm sites such as those in Delaware Bay, NJ presents significant risks (Figure 1). The required fine mesh bags for handling very small seed quickly become fouled and silted increasing the potential for mortality and reducing the growth. Additionally excessive wave action can impact growth and shell shape. Early nursery practices set the growth trajectory, size, and shape characteristics that will define market qualities during the 1.5 to 2 year production cycle. This is particularly important for product designated for the half-shell market. Seed purchases are a large cost input for oyster farms so it is critical that survival, growth and quality of seed are maximized.
Factors affecting the nursery phase include: food quality, stocking density, flow rates, and wave energy. From a farming perspective, choices with respect to gear and handling practices must be developed specifically in response to local conditions and the best farm management practices that can be deployed are those developed for local conditions.
Like many shellfish farms, Sweet Amalia Oyster Farm, does not have access to a suitable
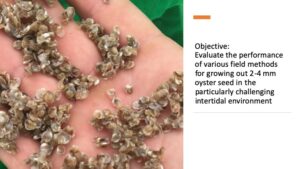
location to place a land-based or shore-side upweller or raceway nursery system. Hence, it is necessary to plant seed directly from the hatchery to the field. Studies in Alabama have demonstrated successful field nursery practices, the results of which were dependent on site location specifics. No studies have been conducted in Delaware Bay where conditions include high energy wave action and heavy fouling. Herein we conducted a scientific evaluation of several different field nursery systems and stocking densities on survival, growth, and quality (shell shape) in order to optimize field nursery practices in the Delaware Bay.
Sweet Amalia Oyster Farm was started in 2012 and is located in Cape May County, NJ along the
intertidal Cape Shore area of the southern Delaware Bay. Owner, Lisa Calvo farms part-time. The farm grows hatchery reared eastern oysters using rack and bag culture systems. The high quality hand-raised oysters are directly marketed to restaurants in Philadelphia and southern New Jersey. This project enabled us to evaluate new methods to field nursery our small seed. Optimization of field nursery methods enables us to improve the survival and quality of our seed, the first and most critical phase of the production cycle, which will influence the shape and quality of our final product. In-kind contributions to this project included equipment and crew time.
Cooperators
- - Technical Advisor (Researcher)
Research
It was necessary to modify the original project design to adjust for the fact that seed availability was limited due to a hatchery production failure. Only two of the proposed three cage types were evaluated and stocking densities were reduced. The evaluated cage types included: (1) SEAPA baskets which are injected molded cylindrical cages that

offer the benefit of having a snap together design and caps and doors that allow quick and easy access to oysters contained within. They are available in a range of mesh sizes and can be deployed in a varied of ways, most often on long lines. The cylindrical shape promotes a tumbling of oysters, which helps clean and shape the oysters; and (3) Low Pro containers, which are low profile wire mesh tray grow-out system for oysters that can be positioned on bottom or floated (Figure 3).
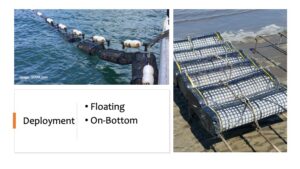
For Low Pro cages the seed was first placed into 1 mm seed bags containing a pvc frame inside to keep the bag stretched open. Cages were either secured to a longline (floating) or fixed approximately 8-12” off-bottom to a rebar rack (Figure 4 and 5). Stocking densities were low (approximately 2000) oyster per cage and high (approximately 8000 oysters per cage). In addition to field plants, three replicate upweller silos were established, each containing approximately 8000 seed at the Aquaculture Innovation Center, Rutgers University. The experimental design is expressed in table form below (Table 1).
Table 1. Experimental treatments.
Gear Placement |
Cage Type |
Stocking Density (seed/cage) |
Replication |
Floating |
SEAPA |
High (8000) |
3 |
Floating |
SEAPA |
Low (2000) |
3 |
Floating |
Low Pro |
High (8000) |
3 |
Floating |
Low Pro |
Low (2000) |
3 |
Rack |
SEAPA |
High (8000) |
3 |
Rack |
SEAPA |
Low (2000) |
3 |
Rack |
Low Pro |
High (8000) |
3 |
Rack |
Low Pro |
Low (2000) |
3 |
Land |
Upweller |
High (8000) |
3 |
Two hundred thousand, 2 mm seed were received via overnight shipping on June 9, 2018. Upon arrival the seed was placed in the field with equal volumes being placed in five SEAPA cages lined with a 1 mm SEAPA sock. Seed was distributed into the various treatment cages and the experiment was initiated on June 12. Samples to assess seed performance were collected on July 13, August 13 and September 3, 2018. All the field planted seed
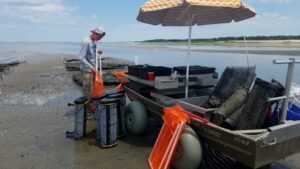
was suitable size for transfer to 9 mm bags by September 3 and at that time the experiment was terminated with all seed being transferred to rack and bag for grow out. On each sample date several parameters were assessed as follows:
- Seed mortality based on number of boxes (empty shells) and live seed.
- Shell height, length, and width (measured in mm using digital calipers).
- Total seed volume (measured dry).
- Seed volume (measured based on water displacement of 25 oysters).
- An index of fan-shape ratio (calculated as ratio of shell length to shell height.
- An index of shell cup shape ratio (calculated as a ratio of shell width to shell height).
- Degree of fouling (qualitatively scored as none, light, moderate, and heavy).
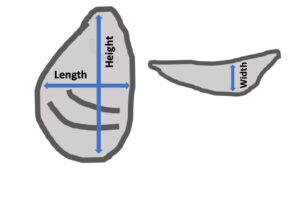
August and September samples were also examined for hinge curvature. Hinge curvature of 50 individual oysters from each replicate treatment group was ranked on a qualitative scale incorporating degree and direction of curve. Categories were normal, moderately curved back, severely curved back, moderately curved forward, and severely curved forward. For analyses these categories were collapsed to normal and abnormal.
Statistical analysis was conducted using RStudio. Shell height, fan and cup were examined using a 3-way Anova and Tukey HSD multiple comparison tests.
A fully crossed experiment was conducted to assess the effects of stocking density (2000, 8000), cage type (Low Pro and SEAPA), and deployment method (floating and on-bottom rack) on the performance of oyster seed grown at an intertidal site in Delaware Bay, NJ. The performance of seed grown in the field was compared to that grown in a land-based upweller system. There were three replicates for each treatment at the start of the trial. Response variables for the evaluation of seed performance in each grow out method included growth (shell height, length and width), survival (based on counts of live and dead), shell shape (fan and cup), hinge curvature, and fouling. These parameters were assessed at 3 to 4 week intervals from June through September. In September seed had grown out of the "nursery" phase and the trial was terminated.
Shell height
Two millimeter hatchery-produced seed was deployed directly to the field and upweller nursery treatments on June 9, 2018. The seed grew well under all grow out conditions during the course of the study. Mean shell height of field grown seed ranged from 10.8 to 14.1mm in mid-July, 18.0 to 26.9mm in mid-August, and 26.2 to 29.3mm in early September (Figure 7).
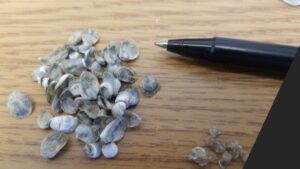
Growth of seed in field treatments exceeded that of seed held in upwellers. Box and whisker plots comparing shell height across all treatments on each sample date are shown in Figure 8. Consistent throughout this report, box plots show the distribution of data with the area within boxes portraying the central 50% of the data. The bars within the boxes show the median, whiskers point to maximum and minimum values and circles indicate outliers. Three-way ANOVAs were conducted on data for each sample month to assess the statistical significance of the effects of each of the three factors and their interactions on shell height. Deployment (floating, rack/on-bottom) and the interaction of density and cage differed significantly for all months, while the effect of cage and the interactions of interactions of cage and deployment, density, cage, and deployment differed significantly only in August and September (Table 2). The effects of each factor for each month are shown in Figure 9. Given the high degree of interactions and variation in effects between sample dates it is challenging to determine a "winning" field nursery system. All systems performed relatively well with respect to growth as indicated by shell height. During the first four weeks in the field, the seed in the floating cages experienced a significant growth advantage. This difference may be explained by the fact that on most days the floating cages remained in water, while the on-bottom cages were exposed to air for 3-6 hours during each low tide. Hence, seed in floating cages had more opportunity to feed. This advantage seemed to disappear by August and September as the growth of seed held on bottom generally seemed to catch up to that in floating cages. Potential explanations for this trend are that mid-summer water temperatures in shallow sloughs became too warm, stressing the floating oysters and slowing their growth.
Stocking density had little effect on shell height, suggesting that both densities were below the threshold density at which food becomes limited or oysters become stressed.
All field nursery methods out performed the upweller system in the hatchery facility. In September, seed held in upwellers were 30% smaller than those grown in the field.
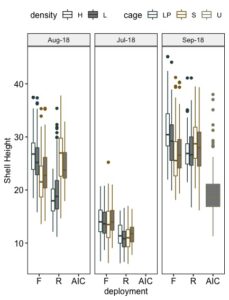
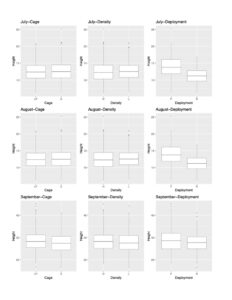
Shell Shape Fan
Shell shape is recognized as an important factor when assessing oyster market quality. Fan was calculated as the ratio of shell length to shell height, a perfectly round oyster would have a fan index equal to 1, while a long and thin oyster would have a fan ration closer to 0. Differences in fan index between grow out methods were most pronounced in July, at which time seed grown on-bottom exhibited higher fan ratios than that grown in floating cages (Figure 10). The effects of deployment, density, cage, and the interactions of cage and deployment, and cage, density, and deployment all differed significantly in fan index (Table 3, Figure 11). Overall the SEAPA cages produced a better fan shape than seed held in the Low Pro cages, seed in lightly stocked cages had greater fan ratios than that in heavily stocked cages, and seed in floating cages had a higher fan ratio than those in on-bottom cages. As the study progressed the differences due to cage type disappeared, while the differences due to density and deployment remained (Table 3). Seed grown in the field, regardless of system, had greater a fan ratio than seed grown in upwellers.
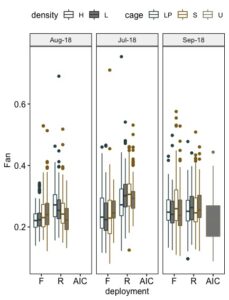
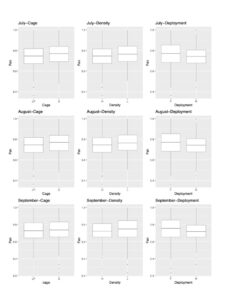
Shell Shape Cup
Like fan, shell cup is also an important attribute in respect to oyster quality, with deep cupped oysters being more desirable than flatter oysters. Cup is calculated as the ratio of shell width to shell height. So higher ratios indicate a deeper cup. Grow out method had a significant effect on the cup of the seed. The relative effect of the three factors, cage, stocking density, and deployment and their interactions varied by sample date (Figure 12 and 13). In July, cage, deployment and the interaction of all three factors differed significantly in cup ratio (Table 4). Seed maintained on-bottom had deeper cups than seed grown in floating cages. Density had no effect on cup ratio. SEAPA cages produced deeper cupped oysters than Low Pro cages. In July neither density nor cage had a significant effect on cup; however, once again cup ratio differed among deployment methods with on-bottom oysters having deeper cups than those in floating cages. Cage and the interaction of density and deployment differed significantly in cup ratio. All field methods produced significantly deeper cupped oysters than the upweller treatment.
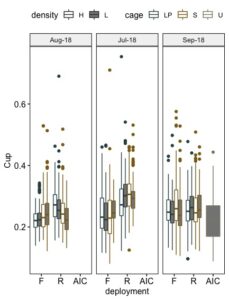
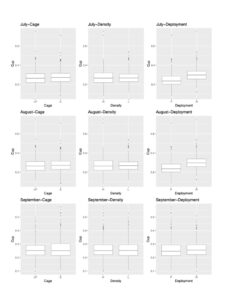
Hinge Curvature
Curved-back and curved forward hinges are often present in aquacultured oyster stocks. These abnormal hinge morphologies significantly impact oyster "shuckability", presentation, and hence market quality. Studies have shown such traits are heritable (Whiteside et al. 2019). This study demonstrates an environmental influence on this shell deformity. Individual seed oysters were scored for degree of shell curvature. The percent of oysters with a normal shell curvature differed significantly among nursery grow out methods. In September, at the termination of the experiment, the effects of density (p<0.005), cage (p<.009), deployment (p<0.00003), and the interaction of cage and deployment (p<0.0005) differed significantly for shell deformity. Abnormal shell curvature was most prevalent in seed held grown in floating low pro cages, while upwellers had the highest percentages of normal shells (Figure 14 and 15). Differences between on-bottom and upwelller treatments were not significantly different, while the percentage of normal shells in both on-bottom and upwellers significantly differed from seed grown floating cages.
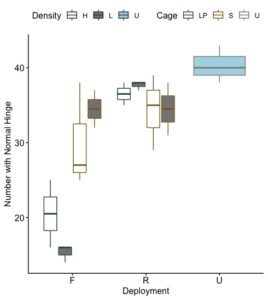
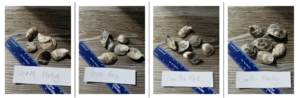
Mortality
Seed losses were associated with cage failure (complete loss of cage and escape) and with general conditions within the cages, most likely caused by silting and mud worm infestations. In respect to cage issues: (1) one SEAPA cage was lost on the first day of the trial due to a lack of properly securing the cage to the rack and (2) holes were found in two seed bags within the Low Pro cages resulting in seed escape. Both conditions were resolved by altering the means of securing cages and reducing the the size of the pvc frames placed within the seed bags to reduce corner wearing and by ensuring that metal rings securing the outer cage mesh did not have rough edges that could prick the seed bags. More attentive attention to assessing bag wear, could have prevented such escape. Mortality related to fouling and other conditions was assessed by counting live and dead in subsamples of oysters randomly selected from each treatment replicate. During the first month of the trial minimal mortality was detected. All grow out systems performed well with respect to seed survival. Fouling was not a problem during this initial nursery phase. Fouling by the mudworm, Polydora cornuta became a problem in July and August and a transition from SEAPA cages with a 1 mm sock to 3 mm cages was met with some challenges in respect to keeping the seed clean, particularly in the floating cages. On bottom cages, which were exposed to air during low tide, had less fouling than floating cages. All cages were regularly washed on the farm using high volume pumps to remove mud, but it was difficult to visually inspect the inside condition of the 3 mm SEAPA cages without opening the lid and fouling inside the cage was overlooked causing a significant spike in mortality. It should be emphasized that our deployment method was not consistent with that advised by SEAPA, installations using posts or rack suspensions would have kept cages at a higher level off bottom, which likely would have better controlled fouling and mudding. Including these losses, overall survival accounting for losses associated with cage loss and failure averaged 84% across all field treatments. Mean mortality of seed based on live and dead counts ranged from 0 to2% in July, 0 to 33% in August, and 0 to 20% in September. Floating cages experienced significantly higher mortality than on-bottom cages (Figure 16 and 17). It is likely that survival could be improved with cleaning regime and or deployment modifications.
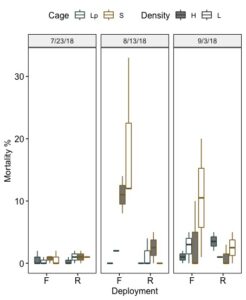
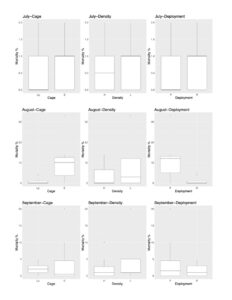
The goal of this project was to optimize methods to maximize seed performance at an intertidal field nursery. The project sought to examine four key production questions:
1. What type of container promotes the best seed performance?
2. Is it better to deploy the seed container off- bottom or at the surface of the water column?
3. Is better seed performance achieved at high stocking density or low stocking density?
4. Which combination of container type, container placement, and stocking density promotes the best seed performance with the least cost?
Modifications to the proposed project scheme were required as we experienced a problem with seed acquisition due to larval mortalities at our source hatchery. Key findings are highlighted below; however, several considerations should be kept in mind when transferring the methods and or comparing to other locations. (1) Site specific field conditions will modulate nursery success. The location where this study was conducted is a moderate salinity, high energy, intertidal site with high turbidity loads and intensive biofouling caused by mudworms. (2) Cage systems were deployed in a manner that utilized existing equipment, not necessarily as optimally designed by the manufacturer. (3) Stocking density was limited by the availability of seed at that time. Higher stocking densities should be evaluated. Optimization of stocking density will be important in order to obtain the best quality oyster possible, while reducing handling costs.
- All methods were effective for the field nursery of seed, survival averaged 84%
- Nearly all seed was ready for transfer to 9 mm bags at 12 weeks post deployment in the field and >75% of the seed was large enough for transfer at 8 weeks.
- Overall, seed grown in floating cages grew faster than seed grown on-bottom.
- Differences in growth between seed grown in floating (higher growth) v. fixed on bottom (lower growth) cages is likely due to longer time underwater, which would allow for more feeding time.
- All field nursery methods out performed the upweller nursery system in respect to growth.
- Shell shape was influenced by cage type, deployment method, and sometimes density.
- Stocking density had little effect within the range evaluated. The higher stocking density (8000 oysters) is recommended given savings in gear utilization. Further studies should be conducted to optimize stocking density.
- Fan index tended to be higher in seed grown in floating cages, while cup index tended to be higher in seed held in on-bottom SEAPA cages.
- Field nursery method was found to be a key determinant of abnormal hinge curvature.
- Seed grown in floating cages had a higher proportion of non-normal hinges than those grown on-bottom and in upwellers.
- The most uniform shell shape resulted in SEAPA cages that were fixed to racks.
- SEAPA socks were more resistant to wear than spat bags.
- Careful attention was necessary to control fouling, enhanced cleaning would likely improve survival.
The development of best field nursery practices for the Delaware Bay will enable Sweet Amalia Oyster Farm and other oyster farms that do not have land or shore-based nurseries to reduce farm risks and enhance product quality and production, and hence farm profitability.
Education & Outreach Activities and Participation Summary
Participation Summary:
This work was presented as a poster at the 40th Milford Aquaculture Seminar, January 13-15, 2020 in Shelton, Connecticut. Two hundred and twenty participants attended the meeting representing farmers, extension agents, researchers, and governmental agents. The abstract will be published in the Journal of Shellfish Research. The results have been summarized in a poster, which will be displayed at the Haskin Shellfish Research Laboratory.
The results were presented to New Jersey shellfish farmers at a Rutgers University Shellfish Grower's Forum on February 7, 2020 at the Haskin Shellfish Research Laboratory in Port Norris, NJ. Annotated slideshow is attached.
The field nursery systems were demonstrated to several farmers with interest on three occasions during the summer of 2018.
Learning Outcomes
Enhanced production techniques for growing post hatchery oyster seed directly in the field.
Project Outcomes
As a result of this project, we have improved field nursery handling of oyster seed. Additionally, the data collected allowed us to model production costs and weigh the cost and benefits of using smaller seed. We will continue to purchase 2 mm seed, both enhancing biosecurity of out-of-state seed importations, and reducing direct seed costs. Even given the likelihood of elevated mortality in 2 mm seed as compared to 4 mm+ size seed, we estimate cost savings to be about 40%. This project has enabled us to optimize nursery handling and produce better shaped oysters. This ultimately effects the number of oysters meeting our premium market standards. Next steps will be to optimize stocking density - evaluating densities higher than those used here, and to modify rack structure to enable SEAPA cages to suspend from rack cross bars. We believe this will further improve field nursery outcomes.
In summary, the goal of this effort was to develop new technologies to maximize seed performance at an intertidal field nursery. The project examined four key production questions:
- What type of container promotes the best seed performance?
- Is it better to deploy the seed container off- bottom or at the surface of the water column?
- Is better seed performance achieved at high stocking density or low stocking density?
- Which combination of container type, container placement, and stocking density promotes the best seed performance with the least cost?
All field nursery methods evaluated proved effective for this early phase of production; however, there were differences in respect to growth rate and shell shape. The value of each of these attributes will likely be weighted differently by different growers—there was not one outstanding best performing method. The key project questions were addressed and this work can help others optimize their methods for their sites and their desired product attributes. Optimization of field nursery practices for the Delaware Bay will help Sweet Amalia Oyster Farm and other oyster farms that do not have land or shore-based nurseries to reduce farm risks and enhance product quality and production, and hence farm profitability.
It was necessary to modify the study approach at the onset as a consequence of constraints in the availability of hatchery seed due to a hatchery-side production failures. The study design was modified and the stocking densities evaluated were lower than proposed. Overall the project was successful and has led to changes in the way we purchase and nursery seed - shifting to smaller 2 mm seed and field nursery. As with any farm methodology, modifications are made as experience is gained. Moving forward we will continue to optimize our field nursery methods. This project afforded us the ability to weight the costs and benefits of a field nursery system, through this exercise we have gained confidence in field nursery methods. This will reduce seed costs and reduce biosecurity risks associated with out-of-state hatchery seed importations, a benefit to our farm, and to our neighboring farms. As we optimize our field nursery system, we plan to: (1) modify racks so that SEAPA cages can be suspended and move with wave action, (2) improve husbandry by cleaning more effectively and frequently and sieving (size sorting) seed regularly, and (3) conduct additional evaluations to optimize stocking density.