Final report for FW17-048
Project Information
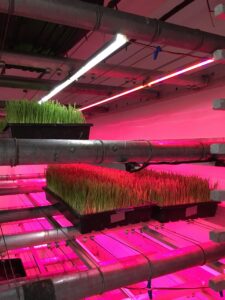
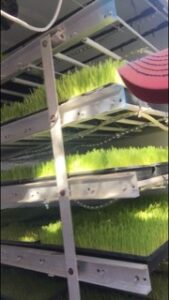
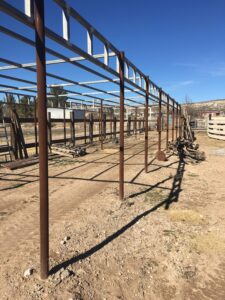
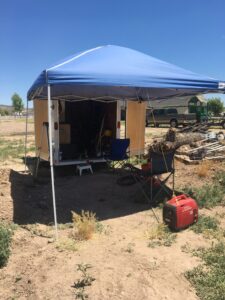
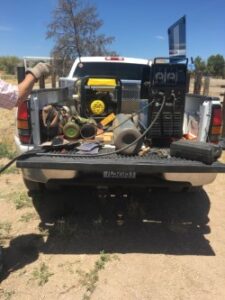
Cooperators
- (Educator)
Research
I decided to conduct more research into other systems, already designed and built. I compared two systems. The first being in Bicknell, Utah built by Glen and the second, in Ramona, California built by Russ Horton.
The unit in Utah was a well built system. The Owner, Glen, uses a consistent temperature of around 68 degrees and uses sprinkler heads to irrigate the trays. He oaks his barley seed for 24 hours prior to seeding the trays to help with germination. His system uses a lot of air flow to combat mold.
The Ramona California Unit was by far my favorite of all systems I have researched on the internet as well as systems we have visited. This unit was so well built and insulated.
The owner, Russ Horton of Fodder Nation, has a genius idea and invented sprouting/growth racks for the first 3 days of germination. There are 30 trays in the racks, which save about 20 square foot of space and these racks require no light.
We ended up purchasing most of our fodder materials from his company. We purchased the exterior box, growth trays, racks and power control panel; assembled everything back at our place in Camp Verde during the months of September, October, November of 2017. Initially we believed we could plug the unit into an outlet on the side of our house but kept flipping breakers. In the end, we ended up trenching from the north side of our home to the south side and designating the unit to its own breaker. We also ran the water line underground due to our winter temperatures dropping below freezing.
.
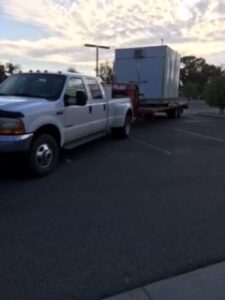
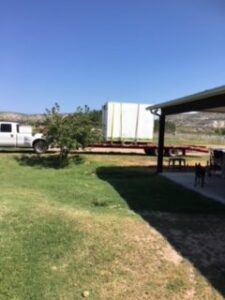
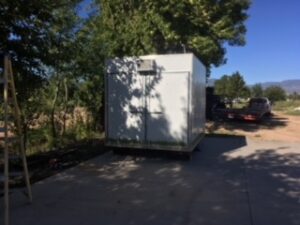
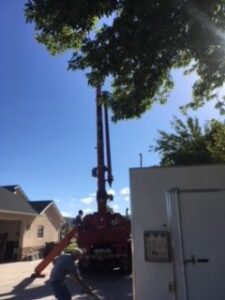
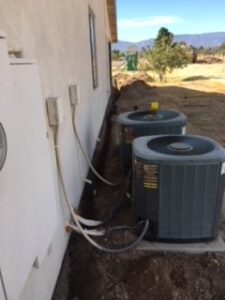
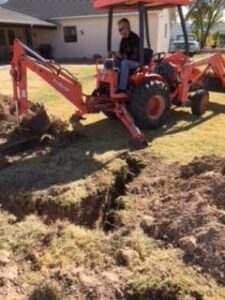
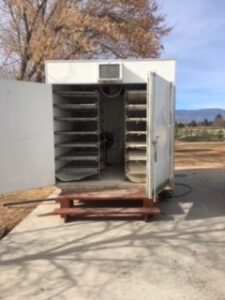
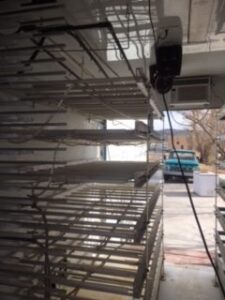
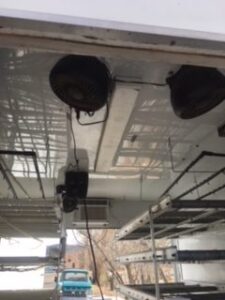
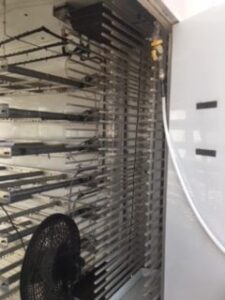
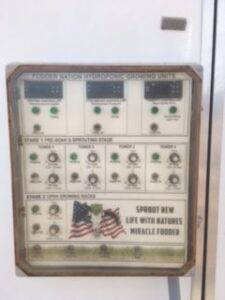
One thing about projects like these is there is one constant element: change.
After feeding our few batches of fodder, it came to our attention that we would need to separate the control group of traditionally fed steers from those primarily being fed fodder, so we designed up a plan for pens located at the back of the property. We estimated that the total project will cost us an additional $4000 dollars.
Materials purchased are the 3" pipe, cut in 8' sections, concrete, roof trusses, corrugated sheet metal and gates. This figure is low for we plan on performing most of the labor ourselves. I recruited my Father and Father-in-law to help us set all the posts and weld.
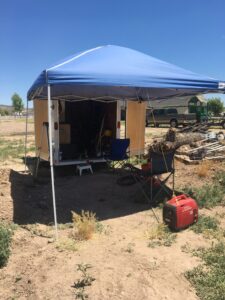
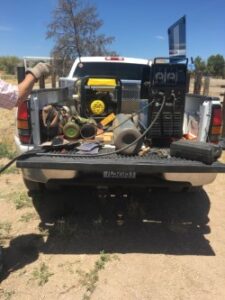
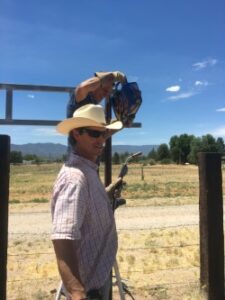
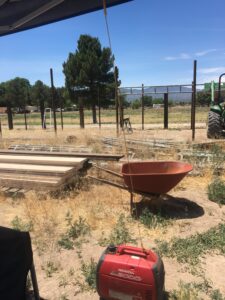
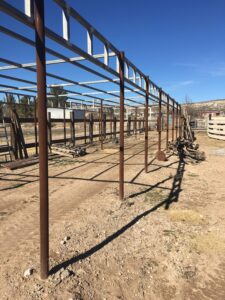
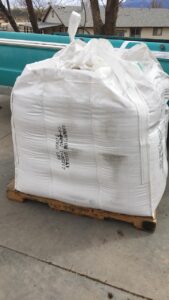
In January of 2018 I was able to locate a company which sells feed grade barley seed; that which is able to be sprouted. We had seed delivered, but the shipping process for such a small amount was a challenge. The seed we purchased was around $800 dollars itself and the shipping was an additional $300. The challenge was finding a shipping company headed this direction that could include our order without charging us for use of the whole truck. Patience and 8 weeks delivered our seed; we finally got the seed on March 27th.
April-2018
Finally, we were back in business!
That is until we needed to change out the lighting and 4 water pumps in the system.
Unfortunately, our water is so hard here in Camp Verde, that those parts weren't functioning correctly. The LED lighting on the growing racks were dimmed from calcium build up and the water float valves in the germination stations weren't able to move up and down, so we decided to stop seeding the system and replace each part.
Amazon had all the LED lighting and I was able to purchase each strand for $39 each; we purchased 5 sets.
Home depot was our source for the 4 float valves and each were $10.99.
May-2018
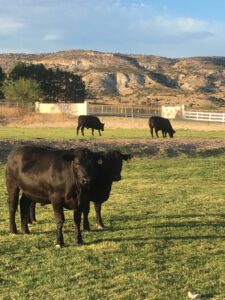
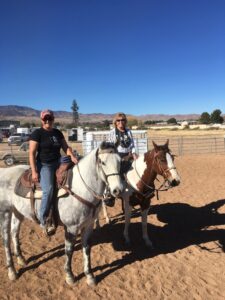
While were getting ready to move our cattle and take 2 into the processor, I got bucked off my horse. Unfortunately, I broke my collar bone, 6 ribs and the top of my hip. With a lung punctured twice and severe nerve damage to skin covering my right hip, I spent 3 days hospitalized.
Since my release from the hospital, I have spent the last 8 months in physical therapy and doing everything within my power to heal. I am so thankful to be alive and am proud to report that I have made a full recovery!
(Yes, I sold the horse;/)
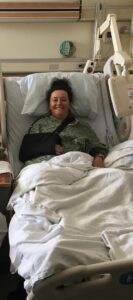
December-2018
Finally released to go back to work from my doctor and resumed where I had left off on replacing equipment on the fodder system. Finished the LED lighting, cleaned the entire unit and installed the new float valves.
Now that the temperature is warming up, I plan to seed the fodder unit starting January 20th, 2019.
January-May 2019
Working our machine daily.
I have decided to seed and grow 18 trays daily. I feel it would benefit my whole herd to eat live sprouted feed during the winter months while our pastures are dormant.
We have separated 2 of our black Angus calves to feed them only fodder and 1 bale of Alfalfa per week. Upon speaking with other ranchers that feed fodder, the one bale of alfalfa helps the digestive system move through the husk of the fodder seed, preventing any back up.
We started them on a pro dominant fodder diet February 1st., Each weighing approximately 700 pounds.
The daily routine of feeding fodder:
First, I pull all the trays that are done. I am currently seeding 18 trays per day and they are reaching full maturity at 8 days. I am keeping the temperature at 68 degrees and trying to keep the humidity low but am still combating mold. I have gone to cracking the exterior door to release some of the moisture if the outside temperature is above 50 degrees and this seems to be helping.
The total process to pull the trays, feed, seed the new trays, soak the seed for the next day, and wash the used trays is about an hour daily.
Comparing this to The traditional methods of feeding that I have used, feeding fodder takes an additional 45 minutes daily.
So far, the cattle that are being fed primarily fodder have a sleeker coat and their muscle growth has been .5 pounds of gain more than the steers being traditionally fed.
I have also noticed that they don’t get “hay belly” after feeding.
I have measured their daily intake of water and feeding fodder has lessened their water consumption by 3-5 gallons per day due to not having to process a dry feed through their system.
Overall I am viewing better overall health of each steer, less water consumption and a daily gain of .5 pounds more than the steers on traditional feed.
With the steers gaining at this rate, I project that they will be finished one month earlier than those on traditional feed.
June 2019
Our steers being fed traditionally still need 100 pounds until they are ready to render.
Our fodder steers are finished and their overall health and body condition is better that those that were traditionally fed. We have already scheduled the appointment with our processor!
The system:
In Summary, the system design and layout is perfect for fodder production.
The water system on the other hand completely failed and copper lines are not useful in this system. We have had 5 lines split/crack which stop our daily production and it’s been extremely frustrating as well as costly.
I feel fortunate that we were able to complete the project and get the steers fed out to market maturity, because the entire watering system needs to be replaced with PEX water lines. This will run about $600 in matierial and $500 plus in labor. All operations are at a halt due to the water system failure.
We ran our first set of trays through the fodder system on an 8 day growing cycle; 5 trays total and they came out perfect. No mold and they were 9 inches tall with a 3 inch root mat and weighed 9-10 pounds each. It was so exciting! The cows went absolutely crazy over it and would almost tackle me to get at the fodder mats in our side by side!
The next two batches did not turn out as well. We grew a bit of mold and the stench of the moldy mats could knock you over. Despite the little bit of mold and stench, the cows still LOVE it.
I cleaned the system thoroughly and adjusted the temperature two degrees to 70 degrees F. No difference and mold still grew rampantly. I changed the temperature again to 68 degrees F and lessened the amount of irrigation in the trays and still no change; lots of mold. Frustrated, I called Russ Horton regarding the mold we are growing. There are usually 2 reasons mold will grow. The first being a dirty outer shell of the seed. Although I soaked the seed for forty minutes prior to seeding the trays, I had noticed a white residue remaining. Russ had mentioned that most seed mills clean their silos by running corn kernels through them. This can leave a residue which can stick to the outside shell on the Barley seed. This is partly why the seed needs to be soaked prior to seeding the trays, but also lowers the germination rate of the barley seed by contamination.
I am researching other seed distributors as I write this. I may have found a distributor in Casa Grande, Az. that will sell it to me at a much cheaper price bulk rate than purchasing it in the bags from Wheatland Mills in Utah. I plan to make the trip the first week in February and once I have the money to purchase the seed.
December-2017 through March 2018
We located a barley seed distributor located in California that is willing to ship us feed grade barley seed, priced as bulk, but under 2 tons worth. we had to wait 8 weeks or more on the shipping, but at $300 for the shipping, it was worth it!
January - 2019
We are moving to growing full time with the fodder machine and will be feeding it to 2 steers that are separated from our control group which are fed traditional feed.
January-June 2019
We separated 2 steers from those being fed traditionally.
Each had an increased daily gain of .5 pounds than those not being fed fodder. Their overall health and body condition is better than those being fed traditionally. They were ready to render one month before those being fed traditionally.
Project Summary:
Overall body Condition and daily weight gain is beneficially worth the daily time to grow the fodder. The system cost is way more than feeding traditional feed. This is why it is not used at most cattle operations. The unit definitely needs a water filtration system if using copper lines for water lines. Daily feeding time is increased by 45 minutes if feeding fodder.
I will continue to use the unit and feed fodder even though this project is completed and once I replace the water system with a whole new PEX system. There is a certain comfort provided in having the ability to produce your own feed for your herd. Also, I have enjoyed watching the growth process, daily, of the trays as well as the obvious better overall condition of my steers.
I am truly appreciative of WSARE to afford this experience to my family and I.
CFB053C0-DAB4-4FDF-9E45-83FBBBEA847A1
Research Outcomes
Education and Outreach
Participation Summary:
Education and Outreach Outcomes
Growing fodder is equally rewarding and frustrating. Mold is a constant battle when you are using a fully enclosed system. For our elevation we have found that keeping the temperature inside the unit at 68 degrees with lots of air flow to combat humidity was key to growing fodder successfully, but a certain amount of mold within the trays was always present. The mold was not enough to have a negative effect on our cattle but I would have liked to have eliminated it completely.
I enjoyed watching the growth of the fodder, daily and our cows certainly LOVE eating the finished product. The time spent daily to grow in the unit is comparable to growing, watering, and harvesting traditional alfalfa.
Our project was successful in producing beef steers that gained more weight daily and had better overall health and body conditioning than those on traditional feed.
We did have multiple system failures and it was extremely costly to run and repair the system.
Feed production.
Learning alternative methods to feed production.
Small scale sustainability
Cost Effective alternative methods versus traditional feed.