Progress report for LNE23-479R
Project Information
Our project will validate the feasibility of using organic alternatives to plastic aquaculture gear to eliminate or reduce pollution from use of plastic buoys in oceans. Farmers are aware of the environmentally harmful effects of plastic flotation devices, but are not aware of any organic alternatives that would be as effective. With tight bottom lines, they can’t afford to risk losing product by using experimental materials for flotation.
The study will test the hypothesis that buoys constructed with mycelium and agricultural byproducts, “mycobuoys”, can be as effective as traditional plastic flotation devices for use in oyster cultivation.
By designing, growing, deploying, and monitoring 433 “mycobuoys” in phase one across 7 farms in Maine, we will be able to observe the performance of the buoys in practical aquaculture applications. Buoy shape and dimensions will be dictated by the needs of participating farmers, with whom we will work closely throughout the project. Our experiment will use four treatments for comparative analysis; our control group will have no coatings applied to the buoys, two groups will each receive a different organic coating, and the final group will be treated with traditional lobster buoy paint.
Buoys will be monitored bi-weekly by participating farmers, with data collected using standard methodologies to ensure comparability. At the end of the five-six month oyster season, results will be compiled and disseminated; if successful, our team will produce 1,000 of the top performing myco buoys in 2024.
Mycelium-based buoys will be grown, formed, and deployed in practical aquaculture applications, where they will be monitored for rate of degradation, buoyancy, and surface fouling.
Ultimately, we aim to optimize and replace harmful plastic buoys which produce micro and nanoplastics, contributing to the death of marine life and the pollution of waterways.
If successful, our pilot group of 7 participating farmers and the Downeast Institute of Maine will demonstrate to aquaculturists and fishermen throughout the Northeast that there are effective alternatives to plastic flotation which do not degrade into environmentally harmful byproducts.
Farmers are aware of the environmentally harmful effects of plastic flotation devices, but are not aware of any organic alternatives that would be as effective. With tight bottom lines, they can’t afford to risk losing product by using experimental materials for flotation. Our research project intends to demonstrate that mycelium-based buoys can be as effective for flotation as traditional plastic buoys by engaging with 7 oyster farmers and the Downeast Institute along the Maine coast who have agreed to test “mycobuoys”.
In 2015, Van Hook deployed strings of mushroom buoy prototypes testing 2 buoy shapes, 8 agricultural byproduct combinations and 6 waterproof coatings at the East Boothbay Nature Center, Hurricane Island Center for Science and Leadership, and at a homeowners dock in North Haven, Maine. Concurrently prototypes were tested in New York Harbor as part of the Billion Oyster Project in conjunction with high school students at the New York Harbor School on Governors Island. These trials enabled selection of one agricultural byproduct and two strains of fungi as optimal candidates to advance the research with this SARE project.
If widely adopted, this project could immediately benefit the more than 150 family owned oyster farms and over 100 owned kelp farms along the Maine coast. From small, recreational Limited Purpose Aquaculture license holders to large industrial operations, the opportunity to reduce or eliminate the use of non-biodegradable plastics could benefit every sea farm as versatile mushroom buoy design advances to accommodate other fisheries.
Farmers in the Northeast care deeply about the health of the ocean, and are constantly striving to improve their practices to be better stewards of natural resources. The main obstacle to any change in practice is the risk of financial losses from deploying untested equipment. We’ve found that farmers are excited by the idea of using organic flotation devices, but are skeptical of long-term durability. The goal is to lower the cost of mycobuoys to where they can be deployed for a minimum of one season and be composted or last 2-4 seasons with one of the test coatings.
2023 Updated version:
Introduction
As far as we are aware, Sue Van Hook is the only researcher in the United States who has been involved directly with the actual growth and deployment of mycelium buoys. Other researchers have just recently explored the potential for the success of agricultural byproduct and mycelium buoys, such as Manan et. al. “Synthesis and applications of fungal mycelium-based advanced functional materials” (2021), but their practical application has yet to be thoroughly tested. No results were returned in the National SARE project database when searched for “buoys” or “mycelium”, and a review of “aquaculture” projects demonstrated that our project is breaking new ground.
Early in the last decade, Van Hook conducted scores of experiments involving the optimization of fungal strains in combination with agricultural byproducts. She tested two fungal strains against eight fiber and husk combinations searching for the ideal buoy composite. Van Hook field tested strings of these combinations using four different toggle buoy shapes and sizes in Maine waters in the summers of 2014 and 2015 (Figures 1-3). Her early flotation experiments in the lab guided a partnership between Ecovative and NOAA’s DART program to design mycelium buoys that would cushion the impact of tsunami detection devices launched from ships and then subsequently break apart and degrade in the marine environment (Figure 4). These were meant to replace rings of Styrofoam™ being used by NOAA which were non-retrievable after launching. News of Ecovative’s prototype mushroom buoys spread to Massachusetts where Salem Sound Coastwatch engaged Van Hook to grow a larger barrel-shaped buoy to support a transmitter and canvas tube for their ocean drifter buoys to monitor ocean currents in 2015 (Figure 5). Deployments of this buoy required added wooden structure to support the small computer, but the buoy successfully transmitted data and was retrieved at the end of the trial.
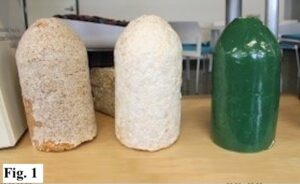
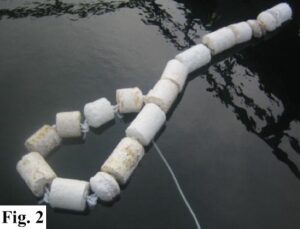
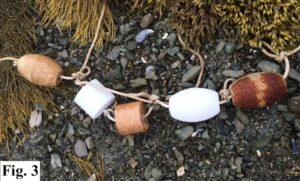

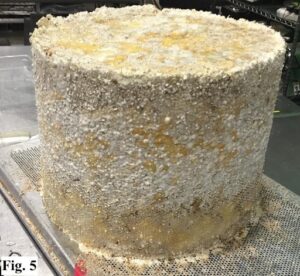
Between 2014-2016, Van Hook grew and tested large 4x4 and 4x6 foot rafts of myceliated biocomposite material to float established marsh vegetation in a wetland restoration project in Kings County, Washington (Figure 6). The raft samples lasted 5 months degrading just after the marsh vegetation had time to grow through the rafts and create their own floating mat.

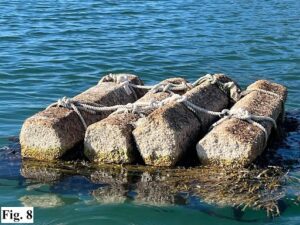
In 2018, Van Hook supported a student at New York Harbor School in conjunction with the Billion Oyster Project in their study “Testing Different Types of Mycelium Buoys’ Durability and Longevity” (Bell). A total of 12 mycelium buoys were tested on oyster cages in the Harlem River for a year. These buoys were submerged completely and were treated with different coatings than are being used in this study.
In short, there is a basis of knowledge that mycelium buoys should function, but a lack of practical experimentation to provide data and proof of concept.
In 2022, Van Hook, in partnership with Severine Fleming, designed and produced 19 prototypes that were deployed on 3 farms in Maine (Figures 7-8). The buoys lasted about 2 months in practical use before degrading to a point where they no longer could support the weight of an oyster cage. Buoys with a soy paint treatment lasted longer than the control buoys with no treatment. The surface texture of the coarser agricultural inputs led to shorter lifespan for these initial larger prototypes. Access to myceliated finer particles that resulted in Van Hook’s earlier success testing net floats has been resolved going forward for this project. The finer particles will result in a smoother surface that can accept and retain the soy paint, pine tar and lobster buoy paint.
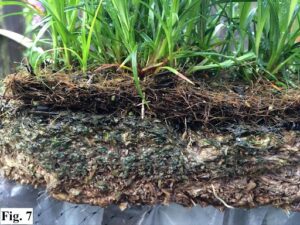
In Maine, the lobster industry alone generates $1 billion per year in supply chain revenue within the state (Donihue, 2018). Fishermen accounted for about 4,500 jobs as of 2021, making up 64% of the total fisheries supply chain workforce (SEAMaine, 2022). We aim to develop, test, and refine a viable, cost-effective alternative to plastic flotation devices that can be widely adopted for use in aquaculture, including lobster buoys, in the state and beyond.
Research
Our research objective is to determine a minimum viable MycoBuoy™ product for three oyster aquaculture gear types using three buoy designs and one all natural waterproof coating against untreated and commercially treated controls. Farmers in the educational program will be deploying, monitoring, scoring and reporting on the viability of the buoys biweekly. Participating farmers will gain first hand experience with MycoBuoys as an ecologically compatible alternative to replace plastic buoys that contribute to ocean acidification, warming and toxic pollution. The circularity of the mycelium/plant based MycoBuoy means no EPR costs versus the unaccounted for EPR health costs of plastics today.
Treatments
The primary factor in the success of the myco buoys is how long they are able to last in a dynamic ocean environment. The treatments will test one waterproof 100% bio-based coating against an uncoated control and a commercial marine paint. Previous field trials have indicated potential seasonal longevity for uncoated buoys if they were allowed to grow longer than one week enabling the strain of fungus used to further develop its own hydrophobic outer layers. Our hope is that this may satisfy the five-six month season used to float oysters near the ocean surface. If sealants are required to guarantee longevity of mycobuoys for oysters, we strive for 100% biocompatibility in the coatings such that any future composting or degradation of the buoys will not harm marine ecosystems. In fact, our goal is to compost the buoys as added nutrients on land at the end of their useful marine life. A third treatment using a proven lobster buoy paint will serve as a control to see if the mycelium-based biocomposite can replace carcinogenic polystyrene and polypropylene. Biofouling for each treatment will be recorded to ascertain the antifouling properties of the coatings used. Based on prior testing, we have determined that the following treatments are most likely to yield comparative data that will inform future iterations.
1. Uncoated - grown for 2 weeks before drying (Control) These were grown between 9 and 12 days before drying with the "flip" day occurring on days 5 or 6.
2. Two coats soy paint - two coats are necessary to maintain surface integrity
3. One coat commercial sealant - current practice for lobster buoys. Two coats were needed to completely seal irregular edges of all three buoy designs.
Methods
From prior research, testing, and farmer input, we have identified three unique buoy designs that serve the needs of farmers in aquaculture. A second orange-pigmented fungal strain will comprise a fourth subset of 24 buoys for the 12" spherical mooring buoys to affirm Van Hook’s earlier successful research with this species. In the first phase of this project, we are focusing on buoys for oyster cultivation applications. In year one, 430 buoys will be grown and deployed per farmer's needs and experimental design rigor. For purposes of data analyses, a random selection from each design will be selected for an equal sample size, N=8.
24 8" diameter cylinder by 31" height, 8 with each treatment.
212 24 x 16"x 3" rectangles, 43 with each treatment
130 32 x 4 x 3" half domes, 25 with each treatment
24 12" diameter spheres, uncoated only
Buoys will be monitored by Key Individuals on a bi-weekly basis. This interval is congruent with the regular operations of oyster farmers, who flip and check their cages bi-weekly.
Based on our results in year one, we will apply only the top one or two performing treatments on the 1,000 buoys produced in year two. Buoy types will be dictated by farmer need, and may be on a case-by-case basis.
Data Collection
The cost per pound of buoyancy is a key metric for farmers to determine whether or not they can support their oyster cages or bags using mycobuoys. A subset of 3 replicates for each treatment of mycobuoys will be sent out to accredited materials testing laboratories for compressive and tensile strength, and buoyancy analyses in conjunction with field testing. These results will permit calculation of cost/pound of buoyancy.
Data collected during monitoring will include:
a) Measured changes in buoy dimensions -length, width, height
b) Scoring of surface degradation of mycelium buoys
c) Presence or absence of biofouling on immersed buoy surfaces
d) Ranking performance among surface treatments 1 through 3
Datasheets for field measurements will be provided to Key Individuals to monitor buoys biweekly for the season and submitted to Van Hook on a monthly basis for analysis.
Data Analysis and Presentation of Results
We anticipate variation in data due to the geographic and microhabitat differences between participating farmers such that Van Hook will pool and analyze all data using Three-Factor Anova tests to determine statistically significant differences among different oyster farms, means for shapes and treatments for each set of data (a-c). Post Hoc Tukey’s tests will be conducted to ascertain where significant differences between treatments lie.
Results of the project will be submitted for publication to these peer-reviewed journals such as the North American Journal of Aquaculture, Journal of Aquatic Animal Health, Earth and Planetary Science Letters, ICES Journal of Marine Science, and Frontiers in Marine Science. In addition, results will be shared in public media with two major Maine newspapers (The Bangor Daily News and the Portland Press Herald), smaller coastal newspapers (Maine Coastal News, The Penobscot Pilot, Quoddy Times, The Courier-Gazette), marine organization newsletters (The Island Institute, Maine Coast Fisherman’s Association, Maine Aquaculture Association, The Basin Oyster Project, Maine Seaweed Council, Seaweed Commons), national organizations (Ocean Conservancy, SeaAhead, Oceana, The Nature Conservancy and others).
Digital media will include video footage of all seven farms and farmers demonstrating the use of mycobuoys for their oyster operations. These media will be shared throughout the course of the project on social media sites maintained by participating farmers and related marine health organizations. A promotional video will be produced at the culmination of the project to inform aquafarmers of the availability of mycobuoys for 2024 should we succeed.
Results will also be presented live by one or more of the Key Individuals at the international Seagriculture Conference and at the Northeast Regional Aquaculture Conference and Exposition in 2024.
2023 Updates:
Revised Methods
Tooling for all three designs presented a set of challenges. The 50 plastic tubs with lids that were ordered for making the rectangular flat buoys arrived but did not come close to meeting the measurements reported on the label. We ordered 400 feet of 2x4 lumber and assembled 36 wooden frames with 24 x 16" inner dimensions. A consequence of this change was that the outer dimensions increased to 24 x 18" so our grow racks could fit only two buoys per shelf rather than three. Our growing capacity was therefore brought down from 50 to 36 buoys. The frames were primed with white enamel paint so that they could be washed between uses (Figure 9). We fashioned bottoms by taping mylar plastic between uses, and lids by taping a 3 ml plastic film taut across the top of the frames. Two 1.5-inch wide hemp fabric straps, to serve as attachments to cedar crate oyster cages, were evenly spaced lengthwise across the bottom and short ends of the frame before filling them (Figure 10). We poked needle-sized holes at 3-inch intervals across the upper film to allow for air exchange (Figure 10). All components were washed and sterilized in a 10% bleach bath between uses. This greatly increased the time spent to make each buoy from the anticipated 10 minutes to 45 minutes. We made a total of 80 rectangular flat buoys distributed between two oyster farmers using the cedar wooden crates design, Smithereen Farm received 15 and North Haven Oysters received 60. A third of these were left uncoated after drying as a control, a third were painted with two coats of red soy paint, and a third were painted with two coats of yellow or orange lobster buoy paint (Figure 11).
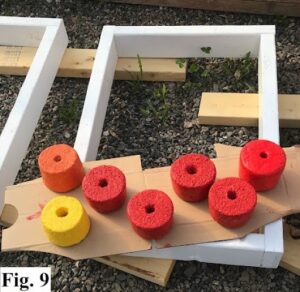
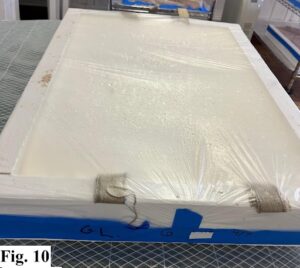
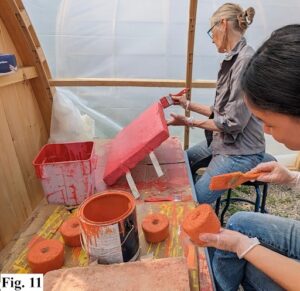
The forms for the large hollow cylinder buoys were constructed using aluminum sheet metal taped together along the seam for the outside and mylar cylinders internally supported by two adjustable metal rings. The cavity between the two cylinders, measuring 8″ at the outer diameter and 31″ in height (Figures 12,13), was filled with 4 ⅓ bags of inoculated substrate atop a perforated metal tray. The trays were placed upright in a baker’s rack beneath a plastic humidity tent and were allowed to grow for 6 days. On the sixth day the inner mylar cylinder was gently removed to allow for complete colonization inside the cylinder. The cylinders were removed from the baker’s racks on the 13th the remaining contents as it could not be evenly distributed into the buoy mixture. An average of 5 bags were discarded per day due to poor colonization or evidence of bacterial contamination (Figure 14).
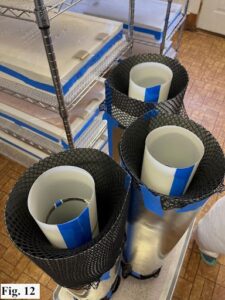
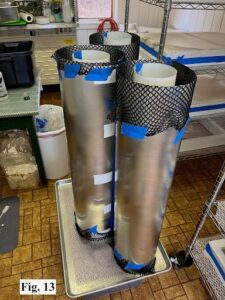
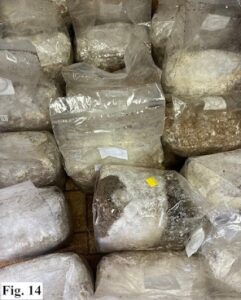
For the flat rectangular buoys, the assembly and disassembly and cleaning of these forms added many hours to production. We spent an average of 45 minutes per day to begin air-drying.
The half-dome buoys were all grown at the North Spore facility between April 25th and May 18th. A supply chain delay for commercial metal rain gutters forced us to fabricate alternative forms from aluminum sheeting held with two galvanized steel end caps (Figure 15). Buoys were removed from their forms at irregular intervals as a result of staffing availability between 5 and 8 days and placed flat side down on racks within a humidity tent to allow for full colonization on all surfaces (Figure 16). After 12-14 days of total colonization, the buoys were placed on racks and rolled to the boiler room for drying where the average temperature was 110°F.
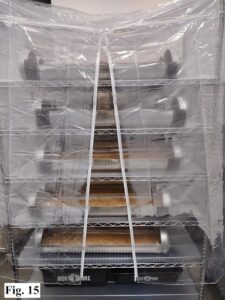
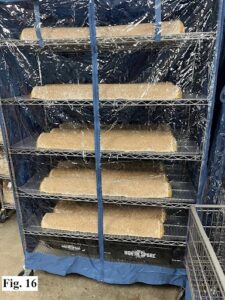
Mooring buoys were grown in the Myco Lab in Pembroke using stainless steel restaurant bowls in three different sizes. Half-inch holes were drilled in the center of the bottom of the bowls to accommodate placement of manila rope. Two of the first three buoys were grown using 4 bags of substrate of the GL strain in 13 quart bowls and the third in the 8 quart bowl using 2.33 bags of material (Figure 17). Buoys 4-6 were grown in the same bowls using the same quantities of the TC orange-pigmented strain. We placed 16 oz Eco Choice compostable paper soup cups inside the bowls atop the substrate and even with the upper surface with a short dowel rod inserted to maintain a central opening for the manila rope to pass through after colonization was complete for the second round of making mooring buoys (Figure 18). The buoy halves were grown for 6 days before being mated and returned to the humidity tent to grow together along with a length of manila rope passed through from one end to the other (Figure 19). After an additional 7 days, the buoys were air-dried.
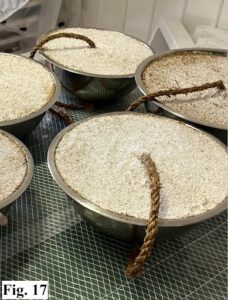
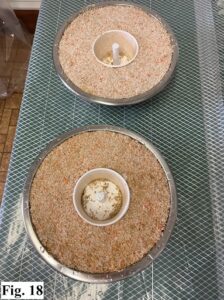
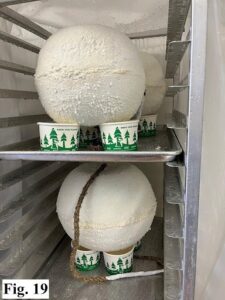
Air-drying the buoys was a prolonged process due to inadequate facilities and wet spring weather conditions. Air-drying took place in three locations according to availability on an active farm in the spring season. In all three locations, heaters, fans and dehumidifiers were run to hasten the drying process that averaged three weeks (Figures 20-22). Buoys made in Pembroke were determined fully desiccated when the mass did not change over 3 successive days as measured on a Globe GS30 30 lb capacity scale.
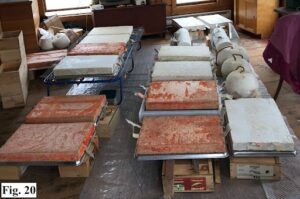
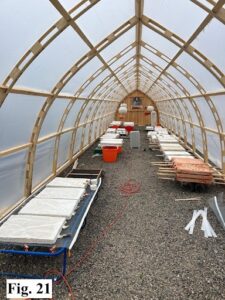
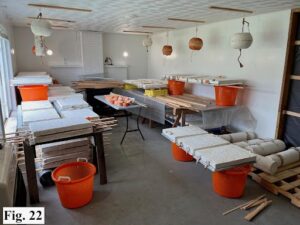
Flat rectangular, large hollow cylindrical, and mooring buoys were first lightly sanded on all exterior surfaces and with attention to rounding the edges. They were then coated with two coats of either the red soy paint or yellow or orange lobster buoy paint in the greenhouse in Pembroke (Figure 23). The paint was allowed to dry fully for 24 hours before the second coat was applied. The half-dome buoys were sanded and painted at North Spore’s facility in Westbrook (Figure 24). Prior to painting, large fungal primordia were cut off the half-dome flat surfaces.
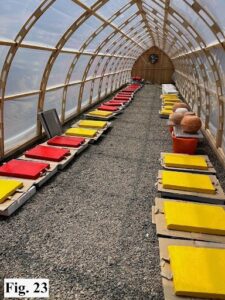
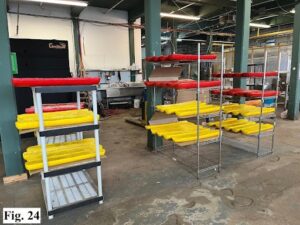
All buoys were assigned numbers using a random selection and a random group generator program. Buoys were tagged with their corresponding strain and number codes before distribution to the 8 oyster farmers on June 19th and 20th.
Farmers reported results using the data collection sheet provided to record and photodocument the damage and biofouling every two weeks.
Our research objective to determine a minimum viable buoy composition and design during the first year of the study was not reached due to near-immediate failure of the three buoy designs and all treatments.
We discovered during the buoy production phase between April 3 and May 12 that the inoculated substrate provided by North Spore spawn company in Westbrook, Maine was not a comparable substitution for the substrate used by Van Hook during the original research and development. The former company uses a different fungal strain, pasteurization process and inoculation method than Ecovative Design’s product. However, Van Hook was not able to obtain an allotment of the original material from Ecovative in 2023 due to the expansion of their spawn production overseas. The material was provided by North Spore in four shipments of 700-800 pounds, as cardboard boxes of 3.5 lb plastic filter patch bags, at weekly intervals beginning March 31, 2023. These were stored in an outdoor shed where temperatures varied between 35-60°F according to the weather. Colonization rates as well as bacterial contamination varied per batched shipments. Bags took 3-4 weeks to reach 90% colonization, compared to 4 days with Ecovative’s mycocomposite substrate, largely due to the differences in pasteurization processes and different delivery and percentage of inoculum used. Most of the North Spore bags had a thick layer of pure mycelium covering the upper surface (Figure 25). This layer had to be removed prior to using the remaining contents as it could not be evenly distributed into the buoy mixture. An average of 5 bags were discarded per day due to poor colonization or evidence of bacterial contamination (Figure 26).removed prior to using the remaining contents as it could not be evenly distributed into the buoy mixture. An average of 5 bags were discarded per day due to poor colonization or evidence of bacterial contamination (Figure 26).
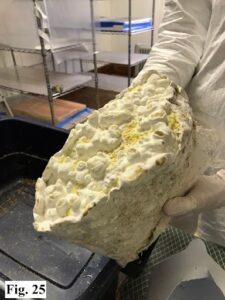
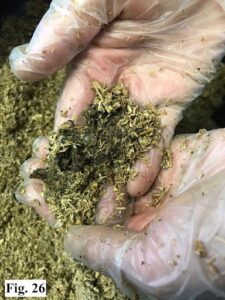
For the flat rectangular buoys, the assembly and disassembly and cleaning of these forms added many hours to production. We spent an average of 45 minutes to make each buoy, 15 minutes to flip each buoy mid-growth and 10 minutes to extract each buoy from the frames, requiring 70 minutes of handling time per buoy (Figures 27-29).

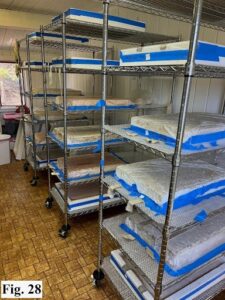
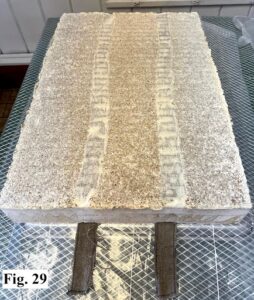
Likewise, the large cylindrical buoys required 30 minutes of set up, 20 minutes to fill, 10 minutes to remove the central mylar inserts at midgrowth, 10 minutes to extract the buoys from the tooling, 10 minutes to fasten two 1″ wide hemp straps around the cylinder, and 10 minutes to remove them from the humidity tent, totaling 90 minutes of handling time per buoy.
Mooring buoys took an average of 20 minutes to fill, 20 minutes to mate and thread the rope through before they were returned to the humidity tent for the second growth phase.
Half-dome buoys took an average of 30 minutes of handling time per buoy.
Each of the 6 oyster farmers field tested 24 half-dome buoys, with 8 of them uncoated, 8 of them coated with two coats of the red soy paint and with 8 of them coated with two coats of yellow or orange commercial lobster buoy paint. One of the six farmers also tested a total of 6 large hollow cylinders. The Wooden Boat School in Deer Isle set out 4 of the mooring buoys and two others went to two oyster farmers.
The 6 oyster farmers testing the half-dome buoys on polyethylene mesh bags reported that the buoys failed within 1-2 weeks of deployment, with the majority failing within 2-5 days (Table I). The two farmers testing flat rectangular buoys did not deploy them (Table I). Mooring buoys tested at The Wooden Boat School and Black Point Oysters also sank within 8 days (Table I).
Table I. Results of Deployed Buoys among 8 oyster farms. Buoy type codes are Gu - half-dome (“gutter”), Fl - flat rectangles, Cyl - large hollow cylinders, and Mo - mooring. Photos tags are used to denote subsequent figures of the deployed and failed buoys.
Farm |
Buoy Type/# |
Treat-ment |
Day Zero |
Day Fail |
Photo Tags |
Comments |
Hurricane I |
Gu/24 |
U,S,L |
6/22 |
6/27 |
R1-3 |
All submerged 3-10 ft, broke up upon handling |
LovePoint |
Gu/24 |
U,S,L |
7/12 |
7/17 |
R4-6 |
Soggy and breaking up |
Pemaquid |
Gu/24 |
U,S,L |
6/20 |
6/27 |
R7 |
All soggy,broken, submerged |
Sister I |
Gu/24 |
U,S,L |
9/13 |
9/20 |
R8-9 |
Failure of all buoys 1 week later |
Love Cove |
Gu/24 |
U,S,L |
7/13 |
7/17 |
R10 |
Broken, soggy, sinking |
|
Cyl/6 |
U,S,L |
7/17 |
9/5 |
R11-15 |
Coatings cracked, sunk |
|
Mo/1 |
S |
|
|
R16 |
|
DEI |
Gu/24 |
U,S,L |
7/2 |
7/6 |
R17-18 |
Removed all 8 U’s, 4 L’s, failed |
|
|
|
7/2 |
7/19 |
R19-20 |
Removed the remaining buoys |
Smithereen |
Fl/15 |
U,S,L |
N/A |
|
R21 |
Never deployed |
North Haven |
Fl/60 |
U,S,L |
N/A |
|
R22 |
Molded stacked outside before deployed, composted them |
Wooden Boat |
Mo/4 |
U,S,L |
6/19 |
6/27 |
R23- 27 |
TC-4-L and GL-1-L chipped and soggy, GL -3-S and GL-11-U with algal biofouling lower surface |
Black Point |
Mo/1 |
|
|
|
|
|









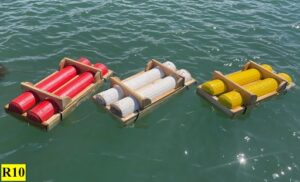
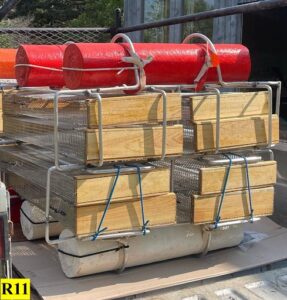
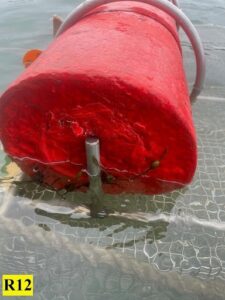
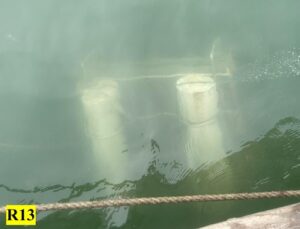
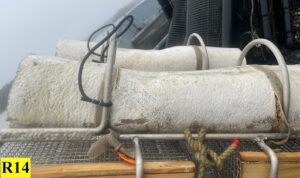
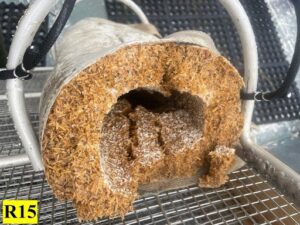
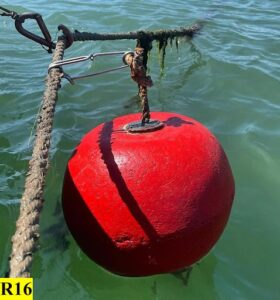
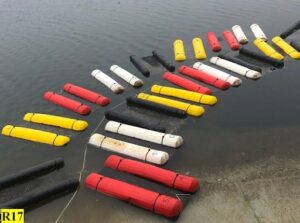
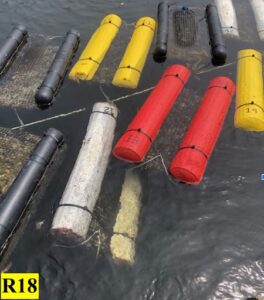
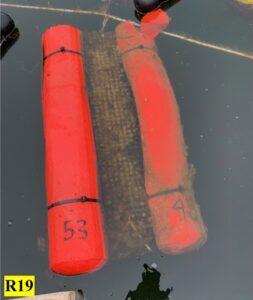
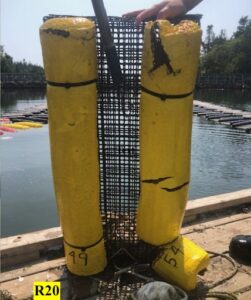
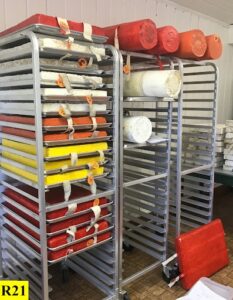
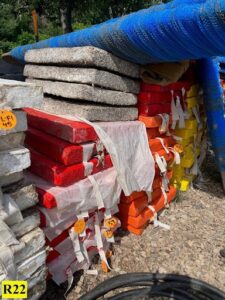
Educational outreach for the project has included workshops and presentations at Skidmore College and two high schools in 2023. The Skidmore ES 206, Environmental Engineering and the Science of Sustainability class designed, grew and floated the first hollow cylinders (Figures 30-34). Two of these buoys were placed in a freshwater pond at Cambridge Central School by high school students in Mr. Butz’ environmental science class, each suspending a 6 lb weight (Figure 35, 36). Both buoys were uncoated and floated high from April 24 - July 2, when I checked on them (Figure 37, 38). The students removed both buoys on October 20th. One was still intact and the second fell apart upon removing it from the pond. The one buoy lasted 6 months and is being dried and weighed for changes in biomass.
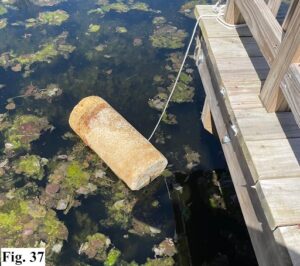
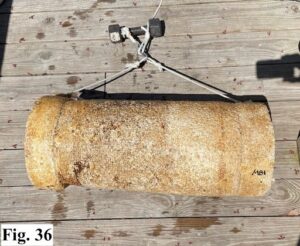
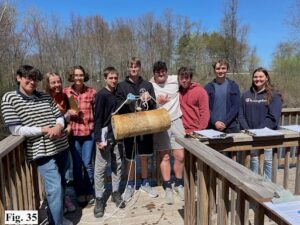
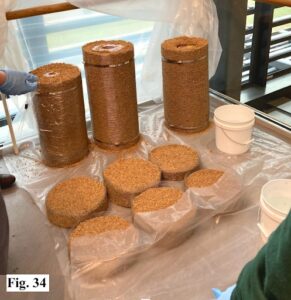
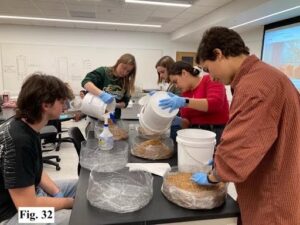
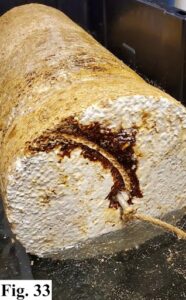
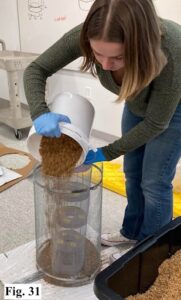
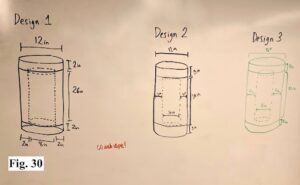
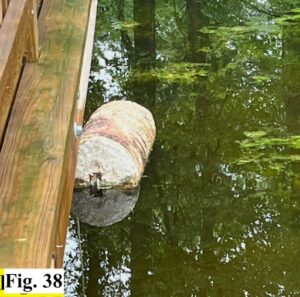
The CCS students also tested the release of nitrogen and phosphorus from buoy fragments in a freshwater aquarium in their lab between May 21 and June 8th. Phosphorus concentration continued to increase from an initial 0.62 ppm to 4 ppm over the 18 days of the study (Table II, Figure 39). Nitrogen, measured as nitrate, decreased from 0.18 ppm to 0.01 ppm during the same time period (Table II, Figure 39). Students noticed a thin layer of mycelium had formed on the surface of the water. Van Hook postulated that the mycelium absorbed the nitrate in the water to grow. Phosphate would be a breakdown product of decomposition of the plant substrate in the mycocomposite. Turbidity increased from 0 to 18 following the increase in phosphate release (Figure 39).
Table II. Release of Phosphate and Nitrate versus turbidity changes from fragments of buoys tested in a freshwater tank in the CCS lab.
Date |
Phosphate (ppm) |
Nitrate (ppm) |
Turbidity |
5.21.23 |
0.62 |
0.18 |
0 |
5.22.23 |
0.66 |
0.13 |
|
5.26.23 |
1.46 |
0.12 |
|
5.27.23 |
1.52 |
0.01 |
|
6.6.23 |
1.59 |
0.01 |
|
6.8.23 |
4.00 |
0.01 |
18 |
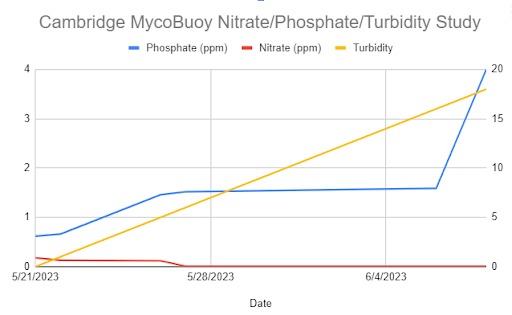
Van Hook has also spent two lab periods on March 21st and November 27th with Environmental Science students at Traip Academy in Kittery, Maine where she presented the project goals and asked students to grow their own bottle and barrel buoys using Ecovative’s material to field test buoys in the Piscataquis River (Figures 40-43). Over the summer, the instructor, Susan Johnson, applied and obtained a lease permit to grow kelp. They filled and grew larger buoys in cylinders to secure the ends of the kelp lines and will test uncoated buoys against those coated with two coats of soy paint.
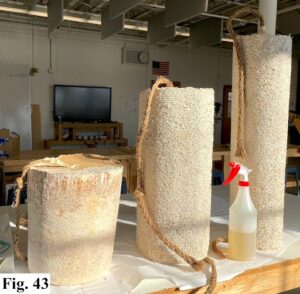
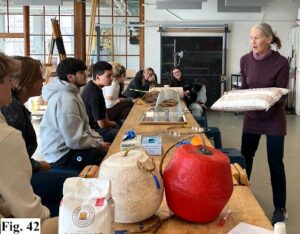
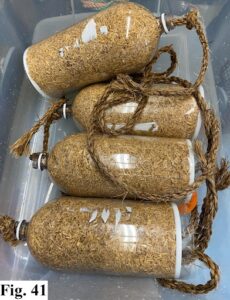
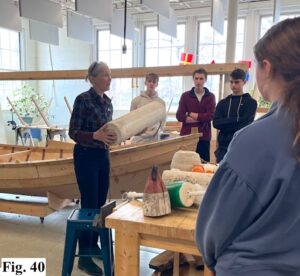
We are excited for the second year of the project knowing that Ecovative’s mycocomposite substrate will greatly prolong the life of the MycoBuoys compared to our results the first year using North Spore’s substituted material. One large 65L kelp buoy made prior to the start of the grant was deployed on September 22nd (Figure 44), and is seen here after floating for 3 months with two coats of the soy paint at the DEI facility in Beals, Maine (Figure 45). Additionally, four cylindrical uncoated buoys made at the Smithereen Farm workshop in April, 2022 successfully floated a plastic-coated wire oyster farm for 5 months (Figure 8).
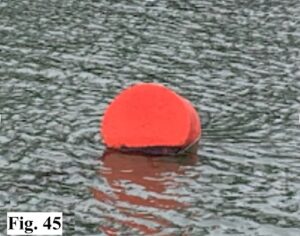
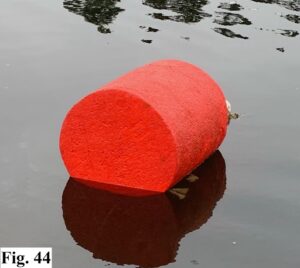
A new facility has been rentedfor the second year that has temperature controlled cold storage to house 6600 pounds of Ecovative’s mycocomposite material that was received on December 1, 2023 (Figure 46). An 8x10x8 foot Flow Clean Room was purchased and erected to create a HEPA-filtered space for mixing and filling the three shapes of buoy forms. Van Hook ordered new tooling for the three designs (flats, half-domes and hollow cylinders) from the Construction and Engineering Research Lab (CERL) at the University of Maine, Orono (Figure 47). To remedy the prolonged air drying time, MycoBuoys purchased a Convection Drying Oven that will allow us to control temperature and humidity cycles to fully dry the material within 2-3 days instead of 2-3 weeks.
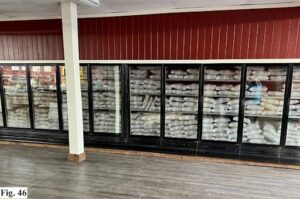
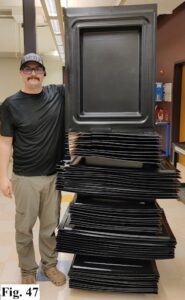
One critique MycoBuoys received after presenting at Ocean Exchange Neptune Finalists business competition in Fort Lauderdale, Florida on October 23rd (Figure 48) was that the business was too focused on Maine aquaculture. Van Hook has enlisted other oyster growers from the University of North Carolina, the Billion Oyster Project in New York harbor, Fishers Island Oyster Farm in NYC, and the Darling Marine Center of the University of Maine to add to six of the previous year’s farmers who will field test buoys for the 2024 season. Van Hook will engage additional participants while attending and presenting at the Northeast Aquaculture Conference and Exposition January 10-12, 2024 in Providence, R.I.

Education & Outreach Activities and Participation Summary
Educational activities:
Participation Summary:
Consultation with Emma Macfarlane for her graduate dissertation on sustainable businesses at London School of Economics, July, 2023.
Consultation with Natasha Kopeck, junior Coastal and Marine Environmental Science major at Maine Maritime Academy, Castine, Maine for a case study in environmental leadership.
Maine Policy Review: Commentary. in press. Van Hook, S. 2024. Reducing Plastic Pollution in the Ocean: MycoBuoys as a Potential Solution.Maine Policy Review Commentary , January 23, 2024 (digital version) March, 2024 hardcopy.
Greenlight Maine TV business competition presentation of MycoBuoys, June, 2023
Ocean Exchange Neptune Award business competition. Awarded as a finalist. Presented in Fort Lauderdale, FL, October 22-24, 2023.
Lab instruction at Skidmore College, ES 206. March, 2023 - Design and construction of first hollow cylinder buoys. Two 3 hour labs. Two 3 hour labs with high school students at Traip Academy, Kittery, Maine on making lobster and kelp buoys, March, 21 and November 28, 2023. Lab with Cambridge Central School environmental science students to test P and N release from buoy material and field test the hollow cylinders grown by Skidmore students.