Final report for ONE19-346
Project Information
The premise of this project was to build a mobile device that would produce clean bedding for poultry and other animals. The bedding needed to match characteristics determined in previous SARE projects. We needed to take switchgrass plant stems that can exceed six feet in length and reduce them to less than 1.5 inches in length. In addition, the bedding needed to be free of dust. The completed machine needed to be small enough to fit on a 12 foot trailer for portability so it could be shared by multiple farmers and operated by a single operator at their own farm. We were fortunate enough to have a farmer in the group who was a mechanical engineer. He did the majority of the design and assembly of the unit. He utilized a "U" design for the material flow. The raw material entered the processing unit at the same end of the trailer where the finished material was discharged. A significant event occurring during a project trial demonstration was a fire that melted a staging bin and destroyed a primary drive gasoline engine. That fire should have been avoided, but it was a valuable learning event in the overall design and safe operation of the machine. As a result of the fire damage, we tried and evaluated a couple of options for replacing the gasoline engine power source such as an electric engine powered by a portable generator, but we ultimately settled on redesigning the machine to run from a PTO driven source of power to eliminate or reduce the potential danger of fire and the unit operation has been demonstrated successfully since then. The unit was show cased and demonstrated at Penn State University's annual Ag Progress Days Exhibit. It was viewed in operation by hundreds of show attendees generating inquiries about the machinery and increased interest in the use of switchgrass for poultry bedding. Lancaster Farmer published two articles about switchgrass bedding and distributed it to over 60 thousand subscribers. One of our participating farmers processed 27 ton of switchgrass at his farm using a Rotochopper. He is currently selling switchgrass bedding through 10 retail outlets.
This project seeks to demonstrate standardized, efficient production of poultry bedding with warm season grasses. We fabricated a trailer mounted machine system to produce and package bedding. Unprocessed warm season grass will enter the equipment at one end and drop into an environmentally friendly (paper) bag at the other end. The unit is available through the Association of Warm Season Grass Producers be moved from farm to farm processing and packaging poultry bedding. The machine will be demonstrated at agriculture events. The prototype unit can also be demonstrated to manufacturing firms encouraging them to replicate production. We proposed to meet the standards cited in GNE 16-127. We also produced a mechanized process for filling the paper sacks to thirty pounds. Poultry farmers will benefit from a more eco-friendly yet cost effective bedding material, while warm season grass farms can successfully produce comparable or greater revenue than other perennial crops for smaller, market garden farms.
Historically, sawdust and wood chips have been a prime bedding for “back yard” chicken producers. As the market for wood fuel pellets increases, the demand for sawdust and wood chips increases and the market price of the wood products goes up. Biomass Magazine predicts pellet demand will increase 10 times over the next 5 years. TreeSource Magazine notes that the U.S. exports more than 6 million tons of wood pellets a year globally, with the European Union strategy to reach 20 percent renewable electricity by 2020. They are currently at 13.2%, indicating continued growth of wood pellet and other biomass fuel usage. There is a better alternative to wood products for poultry farms. As wood decomposes, it produces acid. Landfills restrict the dumping of large quantities of sawdust. Using chicken manure with sawdust on a backyard garden does more harm than good, as fecal material of chickens likewise is highly acidic. Disposing of chicken manure wood mix, then, becomes difficult.
Previous SARE projects have demonstrated the benefits and advantages of using warm season grass for poultry bedding. Warm Season Grass must be processed properly to be useful as bedding. Warm season grass grows to six feet or taller. It must be reduced in size to 1.5 inches or less. The dust must be removed. It must be packaged in a manageable container. The container cannot produce condensation or the material will rot. Part of the challenge then is to address these processing issues in a cost effective method, increasing availability to poultry farmers. The Penn State Extension notes that currently the Northeast region is underdeveloped for biomass crop acreage and widespread availability of processing equipment.
The complete mechanical system to produce acceptable poultry bedding does not exist. SARE project FNE17-865 found some farmers have some of the equipment. Where partial processing exists, it is very labor intensive. The bedding produced often does not address all the characteristics listed above.
Participants in SARE project ONE-18 320 attended a number of agriculture based events. Crop farmers and poultry farmers at Ag Progress Days, Harrisburg Farm Show, Bloomsburg Fair, 5 smaller county fairs and Keystone Farm Show expressed interest in using warm season grass poultry bedding. Members of the Association of Warm Season Grass Producers are interested in producing warm season grass bedding to further develop their market.
Three previous SARE projects explored warm season grass poultry bedding. GNE16-127 Renewable alternative bedding for commercial broiler chicken production demonstrated that warm season grass, properly processed, works well as poultry bedding. It established a set of standards for optimum bedding performance: the smaller the cut, the better (less than 1.25 inches), avoid particles larger than 2-3 inches, and avoid and reduce dust.
FNE17-865 Single-producer-scale preparation of warm-season grass for poultry bedding explored techniques to properly process warm season grass for poultry bedding. It explored various grinding techniques. It looked at dust removal, and it examined what packaging worked and what doesn’t. Multiple samples were sent to a lab at Penn State University. The samples were tested with a particle analysis device. The analysis looked for dust content and oversize pieces. The project, however fell short due to the only ‘in-field’ processor (New Idea Uni-Processor) being discontinued. We are exploring mechanized filling of the bags in order to reduce cost. Many farmers already have some of the necessary equipment. Few farmers have all the equipment. If not properly configured, the process can be very labor intensive. If not properly configured the resulting bedding will not meet the ideal characteristics identified by GNE-16 127 or the reduced cost for end-user consumption. We are proposing a processor that is portable and will meet these standards.
ONE18-320 Developing Markets for Warm Season Grass within the Pennsylvania Farm Community demonstrated poultry producers would use it, if they could get it. Grant participants attended various agriculture events and spoke about warm season grass poultry bedding. There was a great deal of interest by both crop farmers and poultry farmers. As noted in the Final Report of FNE17-865, “every time we showed people warm season grass poultry bedding, they wanted to know where they could purchase some.” Additional issues were condensation (use of clear bags for transport and storage may have aided the issue), loading of super sacks for transport, and transportation to farms. As noted in the final report, “unless the material is available to poultry farmers for purchase, the market will never develop.” The market could be a lucrative one for farmers growing warm season grass with the resolution of these issues.
In terms of condensation, a lesson learned from FNE 17-865 was that plastic sacking material may not be the best product. We propose to use paper sacks and have arranged through Target Corporation to purchase custom printed sacks at a reduced cost of $0.60/bag. The bags have a capacity to hold thirty pounds. The sacks will be stored at each farm used for the harvesting of the grasses, and transportation for distribution in the beginning of the project will be the responsibility of each partner farm, where the grass is harvested. We have held discussion with All Shred for CDL transport as the project progresses.
This project seeks to demonstrate standardized, efficient production of poultry bedding with warm season grasses. We will fabricate a trailer mounted machine system to produce and package bedding. Unprocessed warm season grass will enter the equipment at one end and drop into an environmentally friendly (paper) bag at the other end. The unit will be moved from farm to farm processing and packaging poultry bedding. The machine will be demonstrated at agriculture events. The prototype unit will be demonstrated to manufacturing firms encouraging them to replicate production. We propose to meet the standards cited in GNE 16-127. We also propose a mechanized process for filling the paper sacks to thirty pounds. Poultry farmers will benefit from a more eco-friendly yet cost effective bedding material, while warm season grass farms can produce greater revenue than other crops for smaller, market garden farms.
Cooperators
- (Researcher)
- (Researcher)
- (Researcher)
- - Producer (Researcher)
- - Producer (Researcher)
Research
The engineering drawing of the portable poultry bedding processor is self explanatory. It shows all 8 components of the system. There is a top view showing their positions on the trailer. There is a side view showing the horizontal layout of the components. The estimated system height is 7 feet. The estimated system weight is 1800 pounds.
The main activity during the latter part of 2019 was to collect the primary components needed to assemble the mobile poultry bedding processor. Participant, Len Reggie did the component selection. He passed the information to Wes Ramsey, Executive Director of Penn Soil Resource Conservation and Development Council. Wes contacted the source of the item, placed the order, provided delivery instructions, and paid for the item. Some of the items were shipped directly to the Reggie farm shop where assembly will take place. Other items were picked up by another member of the team. Primary components have been obtained.
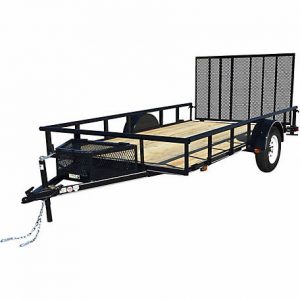
The component making the system portable is the 7’ x 12’, flat bed, wood deck trailer. It was ordered online from Tractor Supply. It arrived at the store in less than a week. Store policy requires pick up within 7 days of arrival at the store or the item is returned. Store policy also requires the trailer to be registered and tagged prior to removal. Will Brandau obtained a truck with a trailer hitch. He went to the store and obtained the sales slip and vin number. From there he went to a registration and tag facility in Wilkes-Barre. The trailer was registered in the name of the Association of Warm Season Grass Producers. The State Tax and registration was paid by credit card. With a temporary registration and a license plate he went back to Tractor Supply to pick up the trailer. When he arrived he discovered the trailer hitch ball was the wrong size. So, he purchased one that fit, hooked onto the trailer and headed to Len Reggie’s farm. It was about an hour later that he arrived and dropped off the trailer in the yard outside the shop.
The hammer mill was from the MacKissic Company distributed by Canns-Bilco Outdoor Power Equipment. Len Reggie arranged the purchase. He passed the purchase details to Wes Ramsey who paid for the unit and arranged shipment to the Reggie Farm. The unit arrived without incident. Hammer mills from MacKissic are manufactured as trailer mounts with two places material can be inserted. Len will disconnect the unit from the small trailer to which it is attached, close the side entry point and mount it on the 7’ x 12’ trailer. The plan calls for the hammer mill to be powered by the gas engine that came with the unit.
We found from past experience hammer milling switchgrass produces a large amount of dust and small particles. This must be removed. The trommel screen will accomplish that. The unit we are using in this project is one built as part of a previous SARE FNE-17 865 project. It was in use at the Trombower Farm. They were dedusting poultry bedding. Dedusting is a cleaning process to remove dust and fine impurities by screening or other pneumatic means. They approached Len Reggie to build a slightly larger unit for them. Len built the unit and when delivering the new unit he picked up the smaller screen for use in this project. It is now at the Reggie farm ready to integrate into this system.
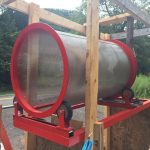
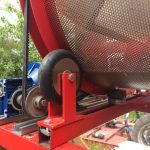
The system is dependent on the ability to move the material from one process to the next. The varied length conveyors will accomplish this. Len has constructed many conveyors. The chain is a key part of these units. The 6 chain sections will be used to construct the needed units. We are not sure if these conveyors will be electrically powered or hydraulically powered. We have an available gas powered hydraulic pump unit capable of driving hydraulic motors on the conveyors. These motors could be “tuned” to transmit material efficiently from each process at an appropriate speed.
All the parts in our possession need to be mounted on the trailer. The conveyors need to be assembles and mounted. The bale buster needs assembly and mounting. The bagger needs assembly and mounting. We need to decide how to power the conveyors, electric or hydraulic. Hydraulic will reduce the electrical requirements for the whole unit.
Assembly of the unit is complete and the unit has been tested successfully. Due to the COVID-19 Pandemic, the demonstration and evaluation phase of the project has been slowed down somewhat, although we continue to make modifications and tweaks to the operation of the process. It is currently stored for the winter in the garage at the farm in Wapwallopen. User training will be scheduled for next spring and summer. The unit will be hauled to Ag Progress Days next August for demonstration purposes.
The material buster knives and hammer mill are both controlled by a single gas engine. The conveyor belts and trommel mill work off electric motors. They get power from a 4000 watt generator purchased with Association funds. The generator attaches to a control panel. The first conveyor has a fold out table attached to serve as a work area. The conveyor moves raw material into the holding tub Where knives shred the material and feed it into the hammer mill.
The hammer mill has a screen with one inch holes. The material is processed until it is small enough to fit through the holes. A small percentage will slip through the holes length wise resulting in a longer stem. There are so few they are not an issue. The material exits the hammer mill onto a second conveyor. That conveyor moves the material into the trommel mill for dust removal.
screen
The material is packaged in either super sacks or 30 gallon (4 cu. ft. content) paper bags. Super sacks are transported with the four corners drawn together. Paper bags are neatly folded and glued shut with a hot glue gun. A piece of cardboard cut to the dimensions of the bag is inserted prior to folding and gluing. This provides a firm base for the gluing process. A weight is placed on top of the bag to help hold the parts in place till the glue dries.
Items in need of change adjustment or creation.
The black guard on top of the tub was removed. (completed) Material coming up the conveyor would catch on it and obstruct the flow of material. The black guard on top of the tub was adjusted and reinstalled. It no longer catches the material going into the white tub.
The tub and drive belt needs to be dropped down using the 4 adjustment screws. This will allow the knives to cut deeper into the material. This was completed. It was an easy adjustment. There are four points for adjustment. They are circled in the picture. Turning them after dropping the pully wheels allowed the knives to cut deeper.
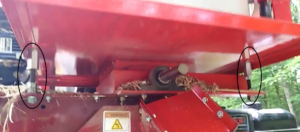
The opening from the hammer needs to be enlarged. Material hangs inside and does not get picked up by the conveyor. This was completed.
Install screen over gas motor air intake to prevent damage. This has not been completed.
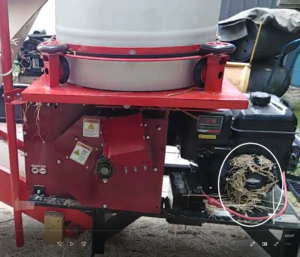
Resolve weed material wrapping around knife shaft. This has not been a problem since the initial trial run. The weed was "mile-a-minute". An application of 2,4-D herbicide in the field where it was growing solved the issue.
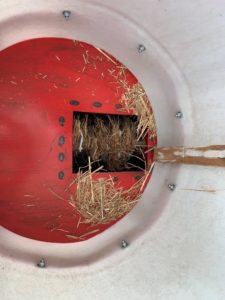
An insert inside the spark plug wire needs to be re-glued. The old glue was removed. Special high temperature tolerant glue is needed. This will be re-glued in warmer weather. Gluing the parts did not work. We purchased a replacement wire. It came as a unit with the coil. The engine was taken to the Briggs and Stratton machine shop for the installation. During the training session held in October 2021, the new unit broke just like the original unit and needs to be repaired or replaced before it is used again.
Len built a "box" to house the bag while it is being filled. It will hold two bags. When a bag is filled a switch is thrown. It reverses the direction the trommel mill to place bedding in a second bag while the first one can be removed.
Install drum switch on trommel mill motor. This will allow motor to rotate both directions allowing two bag filling station to function. i.e. One bag can be filling while second bag is being sealed. This was completed and works well. The trommel mill reverses direction to fill the second bag.
Adjust tent legs to cover trailer mounted equipment while on the job at individual farms during the demonstration and evaluation phase of project.
We sought to build a portable unit that would produce dust free bedding from switchgrass. We met our objectives although we experienced some challenges along the way. We did not find a company willing to take our design and commercialize it. They felt wood products were and would dominate the bedding market. Based on reviews from farmers using our product, we plan to change that.
Education & Outreach Activities and Participation Summary
Participation Summary:
Ag Progress Days 2021
Rodney Leighow hauled the unit to Pennsylvania Furnace for Ag Progress Days. We went out on a Monday and left on Thursday. We did 4 to 6 demonstrations per day. In total, we had over 400 individuals view our demonstrations. We talked to at least half of the folks who viewed the demonstrations. Here is a link to a picture video from Ag Progress Days.
Training
A training session was held at the Leighow Farm. Len Reggie lead the session. Here is a link to the picture video of the session.
Lancaster Farming Article
Tom Venesky, a report for Lancaster Farming attended the training at the Leighow Farm. He published an article about the project. LF article
He is also writing a followup article about the project, however it has not been published as of the date of this report.
Learning Outcomes
We were preparing material for the Harrisburg Farm Show on December 28, 2021. The request for material arrived late; two weeks before they wanted the material. We needed 40 bags, about 160 cubic feet of poultry bedding for demonstration purposes. We completed about half of the order. Grass had collected around the gas engine. The hot engine ignited the dry grass. Because we were at the opposite end of the unit, we were not immediately aware of the fire. By the time we saw the fire, it had melted the engine gas line and gasoline was fueling the fire. There was no fire extinguisher on site so we had to go to another building to get one. The extinguisher quickly put out the fire.
Describing the pictures above:
The engine was a complete loss.
The board above the engine to deflect material did not burn. We found this very strange as it is directly above the engine.
The white barrel melted completely.
The wood conveyor that feeds the barrel was only slightly damaged.
All the drive belts were melted. You can see the belt dangling below the guard.
Excess material had accumulated all over the trailer bed.
The melting barrel dripped into the knives and became hard.
We plan to redesign and rebuild the machine to reduce potential safety hazards. Clean up may be difficult. The melted plastic barrel dripped down and inside the shredding knives and into the hammer mill. It will need to be chiseled and removed from all areas. We will not use a gas motor to power the shredding knives and the blades in the hammer mill. Instead, we will design a PTO drive. That way a tractor can attach and provide the power to drive those units. Until we clean up the plastic and open up to the lower unit, we will not know what else we need to replace. Shafts and bearing may need attention or replacement. Cost of necessary repairs and/or redesign are currently being evaluated and investigated. Once those costs are determined, our project budget will be reviewed and may need revision as we move the project forward to completion.
There were a number of lessons learned from this experience which will result in development of an updated safety protocol for operation of the bedding processing machine. Keep a fire extinguisher with the unit at all times. Then, we can respond quickly in the event of an emergency and prevent as much damage as occurred this time. Take time from processing to clean material off the deck. If material is allowed to accumulate, a fire is more likely to occur. Some changes in the overall processor design may be made to avoid using devices such as gas engines that produce heat and can ignite the grass. This may include the generator. It may need to be placed off the trailer, away from grass on the trailer, or design a better protective shield for heat sources. A fact sheet containing an updated safety protocol will need to be developed for the safe operation of the machine once the redesign has been completed and tested.
Project Outcomes
Possible Flax Bedding Replacement
Because of the Lancaster Farming article we were contacted by a vendor in Lancaster County. He was importing flax bedding from Canada. He reported he imported 40 tractor trailer loads a year. His source left Canada and relocated in Europe. When he saw the article in the Lancaster Farmer edition he thought switchgrass bedding might be a suitable replacement for the flax bedding that was no longer available. We are in negotiations with him.
Trumbower Farm Project
Bruce Trumbower ran the machine at his farm and also at Ag Progress Days. He saw the potential to expand his switchgrass farm operation. He replicated the portable machine with a stationary machine at his farm. When that unit was too slow to keep up with demand, he rented a Rotochopper from Shenk and Sons. The chopper processed 27 tons of material in 3.5 hours. Before bagging he runs the material through a trommel mill to remove the dust. As of this writing, he is distributing through 10 retail stores. Delivery and processing time cost less than $1500
Rodney Leighow Project
Rodney also ran the machine at Ag Progress Days and saw the potential. Rodney's project is similar to the Trombower project but, on a smaller scale. Rodney uses the portable processor to process material into super sacks. From the super sacks he bags material into smaller bags for distribution. He supplies local farm product distributors with switchgrass bedding. He also supplies bedding to the Bloomsburg Fair.
Machine Redesign
After the fire, the Association discussed how to redesign the unit to limit the possibility of another fire. One idea was to power the unit with an electric motor with electricity supplied by a large generator. Another redesign idea was to mount a PTO unit to drive the chopper and hammer mill. Both options are being evaluated and tested. The machine should be functional by early spring of 2023.
Redesign outcome
We applied both ideas to the machine. First, we obtained a 7.5 horse power 220 volt electric motor. We calculated the necessary pully size to achieve the proper rotation speed for the chopper and hammer mill. We mounted the motor, connected the drive belts, connected the motor to an inside power source. Everything ran as expected. The only problem was the machine needed to be connected to an existing 220 volt inside power source. That was an issue. The process produced dust and we considered if it should cause a fire there could potentially be damage to the building it was in. But we knew the 7.5 hp motor could do the job. Next we hooked the motor to a DuroMax XP13000E 13,000 Watt Portable Gas Powered Generator. The portable power would enable us to run the machine anywhere outside, we thought. We attached the motor's power cord to the 220 outlet on the generator. When we started the generator and turned on the power to the motor the 40 volt breaker on the generator blew. Every time we reset the breaker and tried to run the motor the breaker would blow. We couldn't run the machine this way.
We stripped the motor and generator off the trailer and started over. The conversion to a PTO drive was beyond our engineering skills. We took the unit to W & R Equipment. They are located close to where the unit was located and are friends of the Association. They calculated the pulley sizes to achieve the necessary rotation. They ordered the pulleys and built a frame with bearings and shafts upon which they mounted the pulleys. We were delayed due to a backorder on two of the pulleys. They eventually arrived an the unit was assembled. We didn't expect what happened when the machine ran off a tractor PTO. Instead of chopping the material and feeding it into the hammer mill, the material came flying out of the plastic bucket above the shredding blades. The pulleys were running backwards. Once the pulleys were moved to the other side of the shaft the unit ran perfectly.
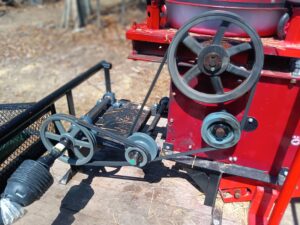
Past SARE Projects
The primary reason this project succeeded was because of past SARE Projects. We had a set of proven standard that were established in previous projects. We knew what we had to achieve to produce quality bedding. We knew what equipment was needed to produce quality bedding. We worked with all the various components in previous SARE Grants. We just never put them together to achieve an end to end process.
Material workflow
The biggest challenge was to achieve a material flow that could be managed by the least amount of workers. We chose a workflow model drawn from Kazan studies in manufacturing. The material went into the machine and came out of the machine at the same end. The challenge was to make that happen. We used a "U" design that facilitated that work flow.
Did we "answer the question"
Yes, we answered the question. We built a machine that converted 6'-8' grass stems into pieces <1.5". We anticipated a fire disaster but, did not act soon enough to prevent it from happening. We realized we needed a "grass guard" around the gas engine. We knew we should have a fire extinguisher in close proximity. We just never took the time to build the guard or get an extinguisher. We were too busy making bedding. The PTO driven unit will work well to run the grinder and hammer mill but does not eliminate the need for an extinguisher.
Will we continue?
Yes, we will continue. As more farmers growing switchgrass see the opportunity to produce quality, dust free bedding from switchgrass they will replicate the Trombower farm process. The portability of the unit allows us to expose more farmers to the process and the requirements to produce the bedding.
Who will benefit from this work?
Producing quality, dust free bedding is an opportunity for warm season grass farmers to implement a new cash flow operation on their farm. We have learned the bedding is ideal, not only for poultry but, also for cattle, rabbits, dogs, horses and any other live stock in need of bedding.
Information Products
- Portable Poultry Bedding Machine Handout (Conference/Presentation Material)
- Large Scale Poultry Bedding Production (Video)
- Testing the machine (Video)
- Portable Poultry Bedding Machine at Ag Progress Days (Video)
- Initial Training Session Photos (Video)
- Reworked machine with PTO drive (Website)