Final report for FNE23-038
Project Information
This project evaluated the efficacy of elevated rack height as a strategy to control mud worm (genus Polydora) biofouling on an intertidal oyster farm employing rack and bag culture methods. During the study oyster production and cost data was collected for oysters grown at each rack height (15", 20" and 30") in an experimental field trials. This information along with past business records for the rack and bag farm operation was used to inform an economic cost model. The economic assessment included a producer-level enterprise cost of production budget for a typical “rack-and-bag” oyster operation which uses standard height (15”) racks; which served as a baseline for comparing the costs and benefits of changing to one of the new rack heights on trial.
Rack height had a significant effect on growth during the course of the experiment with higher rates of growth occurring with decreasing rack heights. Extrapolating growth rates to market size oysters grown at 20" and 30" required 2 and 8 weeks of additional growth compared to those grown at 15." Oyster mortality was higher at a 15" (21%) rack height than at 20", and 30" which remained at or below 5%. Biofouling associated with P. cornuta (mud worms) significantly increased with decreasing rack height resulting in increases in time spent washing. Oyster condition, shell strength, shell height, shell width, and shell depth did not significantly differ among rack heights.
Overall, the economic analyses indicates that each rack height is practicable and can be financially viable. In the field trials, some labor was saved because of reduced biofouling on elevated racks, however, labor increased overall because of the increased time to grow-out on the elevated racks. However, higher capital and labor costs, and lower growth rates associated with higher rack heights were more than offset by significant increases in survival, thus increasing overall revenue and profits for higher rack heights. Sensitivity analysis shows that methods to reduce biofouling on rack and back intertidal farms would dramatically shift profit margins. The economic model presented here suggests that even small improvements in survival can greatly improve profitability. Conversely, even small reductions in survival could lead to serious cash flow problems. In this instance gross revenues increased for 20” and 30” racks by $61,794 and $55,708, respectively; representing a significant profit for a small farm.
- Evaluate the efficacy of elevated rack height in controlling biofouling of Polydora in oysters grown on a mid-Atlantic intertidal oyster farm
- Evaluate the effect of rack height on survival, growth, disease, and condition of oysters grown on a mid-Atlantic intertidal oyster farm
- Examine the economic costs and benefits of elevated rack height for the control of Polydora biofouling on a mid-Atlantic intertidal oyster farm
- Share the results of this project with shellfish farming, extension, and research communities.
Commonly referred to as mud worms, members of the genus Polydora are ubiquitous polychaetes that are recognized as important pest on shellfish farms worldwide. Along the east coast of the U.S. two species – Polydora cornuta and Polydora websteri are widespread. Polydora cornuta settles on the exterior of oysters and forms thick mats of mud that inhibit oyster growth and cause oyster mortality. Polydora websteri burrows through the oyster’s shell, weakening the shells and causing unsightly blisters on inner shell surfaces that are unappealing to consumers and decrease marketability.
Oyster farming methods vary greatly from place to place largely dictated by the particulars of the farm’s environment. In the southern Delaware Bay, New Jersey farmers employ rack and bag oyster culture methods, rearing hatchery-raised seed in mesh bags that are secured to low lying rebar racks. The oyster racks are situated on intertidal flats that are exposed to the air at low tide. The proportion of time the oysters are exposed to the air is dependent on rack height relative to the tide and the tidal amplitude. The time the oysters are aerially exposed will impact their ability feed, as the oysters must be submerged to have access to the naturally occurring plankton in the water. With increased aerial exposure one would assume growth may be reduced as potential feeding time is limited. Regulations to protect horseshoe crabs require farms in the Delaware Bay to maintain racks at 14” off bottom, hence racks are typically constructed with 14-15” legs.
The Delaware Bay is well suited for P. cornuta and P. websteri. Farm management strategies involve washing oysters using high-volume trash pumps. During the summer months “mudding” associated with P. cornuta requires oysters to washed on a weekly basis. Labor costs associated with Polydora mitigation for a midsize farm (250,000 market oysters) are approximately 700 person-hours, and equipment and supplies cost about $2,000 annually - nearly 30% of production costs.
Control of Polydora biofouling on oyster farms has been the focus of numerous studies including NESARE Farmer Grant projects in New Jersey and Maine (Haskin 2013 and Leach 2011). Saturated brine, ice slurries, heat, and 2-day drying episodes have shown some success in reducing infestations; however, the logistical challenges of implementing these strategies precludes practical farm-scale application (Cox 2012, Martinelli et al 2022, Morse 2015, Littlewood et al 1992, Hadley et al 1997, Hooper 2011, Nel et al 1996).
In 2021, Zoe Schaedle, a student intern on our farm conducted a three-week experiment to explore rack height as potential control of Polydura sp. Zoe placed clean oysters on racks at four heights – 15, 20, 25, and 30” and after two weeks she assessed relative fouling by weighing the mud on the oysters. Zoe’s results were interesting as the amount of fouling decreased with rack height (Figure 1).
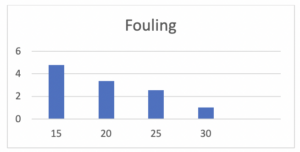
The questions addressed in this project are: (1) can I reduce biofouling, and the cost of mitigating biofouling by using higher racks? And (2) what are the other production costs and or benefits that might be associated with employing higher racks? As it is critical to understand these tradeoffs from an economic perspective, an important aspect of this study is the development of an economic model to help visualize how a change in gear could affect farm profits.
Mud worm biofouling has been the most significant problem for my farm. In the height of the growing season biofouling control requires 2-4 workers and multiple pumps. The costs of labor are significant and as the farm has expanded production, it has been impossible to keep the fouling at bay. New strategies for managing this biofouling are essential to the future growth and sustainability of the farm. Effective new strategies will allow us to realize improved productivity, reduced labor costs and increased net farm income. This project evaluated potential of rack height as a new management strategy for controlling infestations of polydorid worms on an intertidal oyster farm. The study includes an economic assessment of the costs and benefits of elevated rack heights. This enhanced understanding better informs our decisions as to how we can best manage this issue and achieve our long-term production goals. This problem is not unique to our farm and we believe this study will be relevant to farms here in New Jersey, across the northeast region, and around the world.
Our farm was established in 2012. We farm on a six acre intertidal area located in the southern Delaware Bay, New Jersey, USA. We employ rack and bag cultivation methods. We produce high quality eastern oysters Crassostrea virginica for the half-shell and directly distribute to markets along New Jersey's coastal shore and Philadelphia. Annual production is less than 500,000 oysters.
Cooperators
- - Technical Advisor
- - Technical Advisor
Research
1. Evaluate the efficacy of elevated rack height in controlling biofouling of Polydora in oysters grown on a mid-Atlantic intertidal oyster farm
Three rack height treatments, 15”, 20” and 30”, were evaluated for efficacy in controlling mud worm biofouling. The 15” height represents the standard rack height currently used on the farm. Racks were constructed using ½” rebar. For each treatment four replicate two-rack units were deployed in paired rows in one research block section of the farm. The treatment units were randomly assigned a location within the research block. Four bags containing approximately 150 like-age (approximately 1-year old), size, and stock oysters were secured to each of the racks at the start of the experiment in May 2024. The racks were monitored weekly through August for P. cornuta biofouling/mud-build-up. Photos of one randomly selected bag from each replicate of each treatment were be taken to document degree of fouling. The selected bags were qualitatively scored (percent coverage) for the degree of mud present. All treatments were washed every 7-10 days using a high-volume trash pump dispensing ambient seawater. The time required to wash each replicate treatment unit was recorded. This provided a basis for estimating labor costs associated for each rack height treatment. Water temperature data loggers (Hobo Pendant MX 2201) were deployed on one replicate rack for each treatment. Relative time out of water/air exposure will be inferred from the temperature data. Statistical analyses included chi-square test for percentage data (fouling scores) and ANOVA for comparison of total washing hours.
2. Evaluate the effect of rack height on survival, growth, disease, and condition of oysters grown on a mid-Atlantic intertidal oyster farm
At the termination of the experiment in August 2024 samples were collected to assess oyster performance metrics. One bag of oysters from each replicate was sampled at the initiation the experiment and shell height of 50 oysters was measured using digital calipers. At the end of the study the number of dead and live oysters were counted, shell height was measured as above, and 10 oysters from each treatment replicate were sampled for condition assessments.
Shell length (measured from Umbo to growing edge), fan width and cup depth were taken using digital calipers. After initial measurements, oysters were shucked, and meat from each oyster was dehydrated in drying ovens for 10 days, after which dry weights were taken. Dry weights and lengths of the shells were used to calculate condition, based on the oyster condition index, used to assess the quality of oysters ((Dry meat weight/shell length) *100). The dry weight of the shells was also taken. The inside of the shells were individually examined for mud blisters associated with P. websteri, and the percent coverage of the shells was estimated. All oysters were also examined for the presence of female pea crabs. Shell strength of the right (cupped) valve of each shell was estimated as the maximum force required to break the shell (LaBarbera and Merz, 1992; Roy et al., 1994) using an Instron 3400 Series Single Column Table Model at a rate of 2.54 mm/min. The maximum force (kiloNewtons, kN) applied in the middle of the shell at which the shell begins to break was assumed the force required to break the shell. Shell breaking strength was standardized to the dry weight of each shell (N/g).
Disease analyses of oysters from each of the treatment groups was performed by Rutgers University. Tissue samples of rectum and mantle from each oyster were incubated in Ray’s Fluid Thioglycollate Medium (RFTM) for 7 days, stained with Lugol’s iodine and examined to detect Perkinsus spp. Infection levels were scored 0 – 5 according to the Mackin Scale. A cross-section of each of these oysters was preserved in Davidson’s fixative, processed into slides using standard histological methods, and stained with hematoxylin and eosin Y. These slides were examined for any parasites, aothogens, and pathological conditions, as well as reproductive status and digestive tubule atrophy as an indicator of general health.
All data was statistically analyzed using Rstudio. Box plots were created to illustrate differences between rack height treatments with median values represented by the center line on each of the box plots. The 25th and 75th percentiles are represented by the lower and upper box boundaries. ANOVA’s and Tukey tests were used to determine if differences between treatments were statistically significant (p ≤ 0.05).
3. Examine the economic costs and benefits of elevated rack height for the control of Polydora biofouling on a mid-Atlantic intertidal oyster farm. Economic assessment included a producer-level enterprise cost of production analysis (Ahearn and Vasavada 1992) for each of the three rack height treatments. During the course of the study records were kept on gear costs, labor costs, and yield associated with production at each rack height. This enabled a comparison of the benefits that might be gained with reduced labor associated with reduced biofouling, with potential losses such as reduced growth rate associated with reduced feeding opportunity associated with elevated racks that remain exposed to air for longer durations. The economic model was developed by economist Kevin Sullivan, Rutgers University.
4. Share the results of this project with shellfish farming, extension, and research communities.
Results have been shared in a report/article format for posting to various email lists targeting New Jersey and east coast shellfish growers.
Field Results
The rack-and-bag system is a common approach to oyster culture. Hatchery-reared disease resistant 2mm seed oysters are put in mesh bags, which are secured on rebar racks. The racks, positioned in the intertidal zone, keep the oysters suspended approximately off the bottom at standard height (15”) so the oyster bags air-dry during low tide. Each bag holds the same volume of biomass, but different numbers of oysters depending on size (i.e., stage of grow-out period). The racks are easily accessible at low tide, easy to service, and relatively low cost. The oysters are tended for 16 to 30 months, harvested and sold at market size (generally 2 ½ to 3 inches or 64 and 76 mm, respectively). Fifteen inch tall racks are commonly employed on oyster farms located in the southern Delaware Bay, New Jersey. This project compares production and economic metrics on oysters grown on 15", 20" and 30" racks.
The experiment was conducted from early June through mid-August 2024. Rack height had a significant effect on growth during the course of the experiment with higher rates of growth occurring with decreasing rack heights. Differences were statistically significant between the 30" and 15" rack heights (p-value 0.045). Mortality of oysters from the initiation to the end of the experiment was 21%, 4%, and 5% at 15", 20", and 30" rack heights respectively Fig_1. Despite the large spread, the differences were not statistically significant at p value <0.05. Differences between 20-15" and 30-15" were nearly significant with respective p-values of 0.11 and 0.12.
Biofouling associated with P. cornuta (mud worms) increased with decreasing rack height and differences were statistically significant for all comparisons (p-value<<0.005) Fig_2. Wash time recorded during routine maintenance significantly differed, decreasing with increasing rack heights reflecting the differences in mud associated with mud worms - lower racks had more biofouling (more mud) than higher racks. Statistically significant differences between 30” and 15” treatments (p-value = 0.0045) were observed, however, there was no significant difference between the 30” and 20” (p-value = 0.0635) 20” and 15” rack (p-value = 0.2437) Fig_2.
Mud blister intensity and prevalence on shell interiors also varied among rack heights Fig_3 and Fig_4. Significant differences between the 20” and 15” (p-value = 0.0008351), 30” and 15” (p-value = 0) and 30” and 20” (p-value= 0.0007551) were observed.
Oyster condition index (calculated as (Dry meat weight/Shell length) *100)) remained consistent across rack heights as there was no significant difference among treatments Fig_5. Similarly shell strength remained the same across treatment groups with no statistically significant differences between rack heights Fig_5. Rack height did not significantly effect shell height, shell width, shell depth (cup), or shell dry weight (p-value > 0.05) Fig_6.
Significant differences in Dermo disease were observed with the 30" treatment having significantly lower weighted prevalences of P. marinus than the 20" treatment (p-value= 0.001) Fig_7. No differences in MSX disease were observed. No differences in the prevalence of pea crabs was observed (p-value > 0.05). Means and standard deviations for all measured parameters are shown in Table 1.
Economic Cost Model
Enterprise Budget
The results of the field experiment were used to inform the development of an economic cost model. The economic analysis performed is a producer-level partial budget analysis as described in Kay et al. (2012), and Ahearn and Vasavada (1992). The economic assessment includes a producer-level enterprise cost of production budget for a typical “rack-and-bag” oyster operation which uses standard height (15”) racks. This is the baseline used for comparison; changes to the enterprise budget arising from changes in the operation (in this case, changing to a new rack height) are isolated and quantified. In this study, a change from standard height racks (15”) to 20” racks and to 30” racks are evaluated.
Table 2 summarizes the production, cost, and marketing assumptions used in the baseline (15”) intertidal rack-and-bag economic model. The analysis is based on a medium-sized oyster farm with annual desired production of approximately 270,000 oysters on one acre (average yearly harvest area). The model assumes that 85% of oysters survive the first season, and 79% of the remaining oysters grow-out to harvest. Based on desired production, 400,000 2-mm seed oysters are purchased for $0.01 each and planted directly to the field. The number of months to reach harvest size ranges from 16-30 months, with higher proportions of harvest occurring between 22-30 months. The model uses a grow-out average of 26 months.
The average yearly fuel cost of $2,800 is allocated between production costs ($300 for ATV operation) and post-harvest marketing ($2,500 for local truck delivery). With regard to labor costs, the model uses three general laborers who work 24 hours per week for 40 weeks per year at an average rate of $17. One crew manager provides supervisory tasks 40 hours per week year-round at a rate of $25 per hour.
Business liability insurance is estimated at $1,090 per year. Workers' compensation, an insurance program that provides benefits to employees who suffer job-related injuries or illnesses, is legally required for all employers. For this study, the workers compensation insurance rate is estimated at 5% of labor costs.
Lease costs are $100 plus $0.50 per acre per year ($101). Licenses include three harvest licenses for crew members at $50 each per year. Permit fees include a yearly $500 New Jersey Department of Environmental Protection Tidelands fee.
Overhead charges (2% of operating costs) include costs such as accounting, legal, payroll services, office supplies, local taxes, telephone, travel, and utilities. Repairs to capital equipment are estimated to be 2% of capital equipment value yearly. It is assumed that there are no loans needed to operate the business.
Regarding post-harvest marketing, the model assumes 100% of harvested oysters are sold to half-shell market to retailers at a price of $1.10 per oyster. Bags which hold 100 oysters cost approximately $.005 each. Marketing expenses are assumed to be $2,100 per year. Post-harvest facility rent including utilities is $1,000 per month. A refrigerated van is used to deliver oysters locally. Post-harvest labor (i.e., washing and packing) entails two workers, each paid $17 per hour for approximately 20 hours per week, 40 weeks per year. Many rack and bag operations market oysters through wholesale channels, which can command substantially lower price. In those cases, post-harvest costs can be significantly less expensive. Table 2
Capital costs for the rack-and-bag operation are shown in Table 3. Racks (including bungees, hooks and labor) cost $70.20 per rack. Bags cost $6.00 each. An ATV with a tow-cart ($8,000) is used to access the oyster farm and to transport equipment and oysters. Two trash pump washers ($600 each) are used to clean the racks and bags on the farm, and two power washers ($350 each) are used for washing oysters post-harvest. A refrigerated van ($25,000) is used to transport harvested oysters to buyers. A computer is used for record keeping.
Table 4 shows the enterprise budget for one cohort of 400,000 oysters. To simplify the analysis, it is assumed that all 268,600 marketable oysters are harvested after a 22-month grow-out period (this is a weighted average, which spans several months as oysters reach marketable size of 2.5 to 3 inches). Because the model attempts to isolate costs for one cohort of oysters, the year prior to harvest includes no revenue. The traditional breakeven price, which covers fixed and variable costs, is $0.50 per oyster. Including the additional $0.20 per oyster post-harvest costs (including delivery) raises the breakeven price to $0.70 per oyster. When sold at a wholesale price of $1.10 per oyster, the profit (before taxes) is $0.40 per oyster.
Partial Budget Analysis
Differences in capital costs for the three rack heights are displayed in Table 5 below. The operation uses 300 racks at a cost of $21,060. The additional costs associated with 20” and 30” racks are $450 and $1,350, respectively. The rack costs are depreciated over a six-year period Table 5.
A breakdown of general labor costs for the three rack heights are displayed in Table 5 below. As the table shows, washing times were slightly reduced with higher rack systems. However, because the higher rack heights decreased growth rates, general labor involved with setting up and breaking down equipment as well as washing increased in season 2. Overall, increased rack heights involved additional labor costs of $170 for 20’ racks and $2,040 for 30” racks. Not shown in the table are small increases in employment taxes and workers compensation of $22 and $258, for 20” and 30” rack systems, respectively Table 6.
Mortality rates for the three rack heights are displayed in Table 7 below. As the table shows, mortality during the first season is identical. However, mortality during season 2 through growout improved dramatically for the higher racks. This is due mainly to improved mortality during the warm temperature season when biofouling associated with polydorid worms is highest. Overall, increased rack heights reduced mortality in season 2 from 21% to 4.38% in the 20’ rack-height system, and from 21% to 5.33% in the 30” system Table 7
The substantial difference in yields translate directly to gross revenue as all three rack heights are assumed to yield similar quality oysters and bring the same price received per oyster. Table 8 summarizes gross revenues, costs and net income under each rack height. As the table shows, net income is substantially higher under the 20” and 30” rack systems.
Partial budget analysis involves quantifying economic changes into four categories: additional costs, reduced revenue, reduced costs, and additional revenue. These incremental differences in net income associated with the heightened rack systems is itemized and displayed in Table 9 below. For a single cohort of 400,000 oysters, the costs increased by $390 and $2,922 under the 20” and 30” rack heights, respectively. The large share of the cost increase was due to increased labor hours associated with a longer growing period to market. It should be noted that in the experiment all bags were washed within a wash cycle according to the study design; however, some washes were not necessary at the higher rack heights and could have been skipped entirely realizing additional cost savings. There were no cost-savings associated with either the 20” or 30” rack heights. On the positive side, gross revenues increased for 20” and 30” racks by $62,183 and $58,630, respectively. The overall change in net income was an increase of $61,793 and $55,708 for 20” and 30” racks, respectively. Table 9
Sensitivity Analysis
This study illuminates the impact of oyster mortality rates on rack and bag operation revenues. Further, the field trials showed that mortality rates caused by mud worm biofouling (especially in the final months before grow-out) can be influenced by altering rack heights. To illustrate the influence of oyster mortality on revenues at varying price levels, sensitivity analysis is presented in Table 8. The table displays the estimated income (before taxes) of the standard 15” rack-and-bag operation under several different survival and price levels. The table is centered on the price and yield assumptions in the baseline cost model for any given year after harvests begin (i.e., after year 1), and measures sensitivity to the season 2 survival rate (holding 1st season constant at 85%) in 7% increments and price received in $0.05 increments. The table illustrates how net income is highly sensitive to changes in oyster mortality. For example, holding price constant at $1.10 but increasing survival by 7% (to 86%) yields additional income of approximately $26,000.
Summary Discussion
Mud worms are ubiquitous polychaetes that are recognized as important pest on shellfish farms worldwide. This project, conducted on the east coast of the U.S. in the southern Delaware Bay, New Jersey sought to establish a strategy to control two mud worm species – Polydora cornuta and Polydora websteri on an intertidal oyster farm employing rack and bag oyster culture methods. Polydora cornuta settles on the exterior of oysters and forms thick mats of mud that inhibit oyster growth and cause oyster mortality. Polydora websteri burrows through the oyster’s shell, weakening the shells and causing unsightly blisters on inner shell surfaces that are unappealing to consumers and decrease marketability. To date farm management strategies have involved washing oysters using high-volume trash pumps. During the summer months “mudding” associated with P. cornuta requires oysters to washed on a weekly basis. This project looked at the potential of elevated rack height as means to reduce biofouling and the arduous and costly labor involved in controlling polydora biofouling on the farm. The idea being that the elevated heights might enable dessication of the worms or perhaps position the oysters above optimal recruitment and activity zone of the mud worms. The proportion of time the oysters are exposed to the air is dependent on rack height relative to the tide and the tidal amplitude. It was appreciated that the time the oysters are aerially exposed will also impact their ability feed, as the oysters must be submerged to have access to the naturally occurring plankton in the water. With increased aerial exposure one would assume growth may be reduced as potential feeding time is limited.
The questions addressed in this project was: (1) can I reduce biofouling, and the cost of mitigating biofouling by using higher racks? And (2) what are the other production costs and or benefits that might be associated with employing higher racks? As it is critical to understand these tradeoffs from an economic perspective, an important aspect of this study was the development of an economic model to evaluate how a change in gear could affect farm profits.
Our findings demonstrated that biofouling associated with P. cornuta and shell blisters caused by P. websteri can be significantly reduced by elevating rack heights from 15" to 20" and 30". This also led to reduced wash times and labor costs. While oyster condition was not shown to be negatively impacted at the elevated rack heights, growth rate was reduced adding approximately two more weeks of growth at 20" and 8 weeks at 30" relative to the oysters grown on 15" racks. It is presumed that the longer air exposure at the elevated heights reduced feeding opportunity. The oysters did not appear to compensate for the lost time underwater by feeding at a greater rate once under water. Despite the slight decrease in growth condition, meat weight, and shell strength were not affected.
The most significant finding was relative to survival. Oysters grown on the 20" and 30" racks exhibited lower mortality than those grown on the 15" racks. Despite the lack of statistical significance, the results are important from a production standpoint as demonstrated by the economical model developed and employed to illustrate the costs and benefits of the potential new biofouling management strategy.
Overall, the economic analyses indicates that each rack height is practicable and can be financially viable. However, higher capital and labor costs, and lower growth rates associated with higher rack heights were more than offset by significant increases in survival, thus increase overall revenue and profits for higher rack heights. Sensitivity analysis shows that methods to reduce biofouling on rack and bag intertidal farms would dramatically shift profit margins. The economic model presented here suggests that even small improvements in survival can greatly improve profitability. Conversely, even small reductions in survival could lead to serious cash flow problems.
This project evaluated the efficacy of elevated rack height as a strategy to control mud worm (genus Polydora) biofouling on an intertidal oyster farm employing rack and bag culture methods. During the study oyster production and cost data was collected for oysters grown at each rack height (15", 20" and 30") in an experimental field trials. This information along with past business records for the rack and bag farm operation was used to inform an economic cost model. The economic assessment included a producer-level enterprise cost of production budget for a typical “rack-and-bag” oyster operation which uses standard height (15”) racks; which served as a baseline for comparing the costs and benefits of changing to one of the new rack heights on trial.
Overall, the economic analyses indicates that each rack height is practicable and can be financially viable. In the field trials, some labor was saved because of reduced biofouling on elevated racks, however, labor increased overall because of the increased time to grow-out on the elevated racks. This stems from reduced growth rates associated with reduced feeding opportunity on elevated racks. However, higher capital and labor costs, and lower growth rates associated with higher rack heights were more than offset by significant increases in survival, thus increasing overall revenue and profits for higher rack heights. Sensitivity analysis shows that methods to reduce biofouling on rack and back intertidal farms would dramatically shift profit margins. The economic model presented here suggests that even small improvements in survival can greatly improve profitability. Conversely, even small reductions in survival could lead to serious cash flow problems. In this instance gross revenues increased for 20” and 30” racks by $61,794 and $55,708, respectively; representing a significant profit for a small farm.
Given these findings, we will begin to integrate 20" inch racks on the farm during the growing season. As racks 15" wear out they will be replaced with 20" racks. In the short term racks will be positioned high on the sand bars, essentially elevating the existing 15" racks, gaining on the order of 3-5" of height. Lower racks will still be needed for the winter season to reduce arial exposure to severe winter temperatures.
The project was eye opening and exceeded our expectation of how it will inform our future farm operations. Beyond guiding our biofouling management strategies the enterprise budget enables us to take a more wholistic view on our business supporting our growth, sustainability, and profitabilty.
Education & Outreach Activities and Participation Summary
Participation Summary:
Journal article (in preparation)
Poster (displayed at the Haskin Shellfish Research Laboratory, to be shared at the Northeast Aquaculture Conference 2026)Poster
Two page project summary Research_Note_Rack_Height_Oyster_Farm (shared with New Jersey oyster farmers, n-=40)
Learning Outcomes
We learned that by increasing the height of our racks by a 5" we can significantly reduce biofouling and associated oyster mortalities which in turn will enhance our profitability. The benefit of enhanced oyster survival outweighed the cost of slower growth associated with the employment of higher racks.
Moving forward elevated rack height will be adopted as a management strategy to control mud worm biofouling.
Economic modeling has provided an in depth understanding of the vulnerabilities of our farm business, such understanding will serve to inform decisions relating to all aspects of the business, positioning us to be more resilient and creating a path for sustainable and profitable growth.
Our findings underscore the the sensitivity of our farm to oyster mortality. Even small improvements in survivability will have profound impact on profits, while slight increases in mortality can readily lead to cash shortfalls.
Project Outcomes
Moving forward elevated rack height will be adopted as a management strategy to control mud worm biofouling.
Economic modeling has provided an in depth understanding of the vulnerabilities of our farm business, such understanding will serve to inform decisions relating to all aspects of the business, positioning us to be more resilient and creating a path for sustainable and profitable growth.
Our findings underscore the the sensitivity of our farm to oyster mortality. Even small improvements in survivability will have profound impact on profits, while slight increases in mortality can readily lead to cash shortfalls.
Aside from the output of the economic model, which is in itself a phenomenal asset, the process of putting together data to drive the model forced a careful look at our enterprise budget. Working collaboratively with agricultural economist, Dr Kevin Sullivan as he built the model was an immensely valuable exercise that gave me a deeper understanding of the business from an economic standpoint. As a farm owner operator its easy to get overwhelmed by the day to day tasks ignoring the hard deep dive into the farm's financials. I feel very fortunate to have had the opportunity to conduct this research and receive the benefit of expert collaborators.
Within the funding constraints and my own time constraints I believe this project was conducted with appropriate rigor to answer the questions at hand. There are many variables across the farm that can impact the results including but not limited to genetic origin of stocks, changes in bottom topography, and placement of gear. Increasing the number of replicates would have made the experiment more robust and more statistically significant differences may have been observed. Estimates of labor costs could be better refined. We washed all racks on every wash cycle. Had we set some threshold of when to wash, we may have not washed the higher racks if fouling was insignificant. This would have lowered the labor invested to wash the elevated racks.
The question we set out to answer was addressed through this work and as a result we will alter our biofouling management strategies as a consequence. That alone is fantastic, but we learned so much more in conducting this study. The results have meaning well beyond our expectation and developed enterprise budget we ground all of our future decision making.
A beneficial follow up project would re-envision the rebar rack structures. Ideally the farm needs a rack that is high in the growing season, but low in the winter. I'd love to see a convertible rack system, made of new materials that don't degrade like the currently employed steel racks.
This work is relevant to oyster farmers working intertidal areas world-wide. Here in the US there are intertidal farms in many states and mud worm infestations have proven to be a significant challenge threatening oyster survival and quality.