Final report for FNE17-862
Project Information
The project was focused on building a hydraulic press powerful enough to make a fuel brick out of livestock manure on a small farm. These bricks have been made in the past by hand and do not have the BTU’s required to burn at a rate that can produce a brick acceptable for a fuel standard. There are larger bio mass machines on the market in US but not applicable for a small farm operation. We worked on using different mixtures of fresh manure and bedding to come up with acceptable ratios of moisture and matter content. The press we developed is a prototype and could still use improvements but we tested it and manure/bedding/water recipees.
The press cost $2,374.63 to construct which included all new materials except for tires. The cost could be considerably less if on farm equipment already in hand would have been used. One could also, with welding skills, modify a wood splitter to have a dual purpose machine. A typical briquette size is: 7” high x 9” wide x 9” long. The dry weight is approximately 3 lbs. for a briquette that size. Estimated cost per 1 hour of production includes: cost of gasoline to run the engine @ $1.80 for estimated half gallon; $.30 for hydraulic and motor oil = $2.10 per hour. One hour of production would yield approximately 30 - 3 lb. briquettes = 90 lbs of fuel burning material. Estimated cost per lb. to produce is $.023.
Based in these results we conclude that livestock manure briquettes are a feasible fuel for the small farmer who has more manure than she/he knows what to do with and a willingness to handle this type of solid fuel and associated ash cleanup.
Introduction:
Most small livestock keepers have more manure than they know what to do with. For years I would look at my growing manure piles and wonder what else I could do with them. We use the manure to make soil, we sell it to others to make soil, we grow millions of worms! We still have more manure than we can use for our land base and number of cattle. Making fuel bricks has been a desire of mine for many years. I saw how it was done on a large scale, and a very small by-hand scale. But those methods would not help me. I needed a press that I could manage myself. One that will make a denser fuel brick than what can be made by hand. A brick that will, in theory, attempt to hold a fire as well as a wood log. We designed our livestock manure press on these ideas.
Our objective was to design, document and build a small livestock manure press that would sufficiently compress a raw manure/bedding mix into brick form to be used as a heating fuel. It had to be affordable to assemble for a small farmer who has more manure than can be used on the farm.
Once the press was built, we would work to determine ingredient rations for best briquette formation, and document pre and post drying methods that achieve the best compromise of heating value and briquette durability. Samples would be tested for moisture content to establish highest BTU/lb for longest burning time and quality.
The stated issue is that a small farmer who raises livestock may have a surplus of livestock manure on the farm. The farmer may ponder ideas for what to use it for beyond the typical s such as: fertilizing a field, mulching, composting, harvesting worms, selling it or giving it away.
The rational for making fuel bricks comes from my fascination with cultures that use every aspect of the cow...from meat to manure for fuel to making paints and cosmetics to heating their homes. As I would look at my wonderful manure piles I would imagine all the things I could make with it. Our planet and our farms become more fertile places to live in with the active use of livestock manure projects. This SARE grant proposal began with the idea to make a fuel briquette a little faster than can be done with a brick mold or a hand pressed product.
Cooperators
Research
Initial research for this project began before the proposal was written and helped us to write the application to SARE. I researched all the various methods livestock manure has been and is currently used around the world to create fuel blocks for cooking and heating, building blocks for housing, as a stucco finish for exterior siding in construction, for ingredients for medicinal purposes, and simply for inspirational art and mural making. For me as a small farmer living in the northeast, I wanted to find a functional use for my ever growing cow manure pile. My goal was to make an easy to use hydraulic press to compact the most dense brick possible.
Finding an innovative and interested fabricator who could share an interest in a small farming technique would be necessary as I do not have welding and machinist skills. After inquiring among several local small farmers, I found one! Steve Lonsky was described as a very creative welder by many people I spoke with. An innovative small farmer himself. While meeting with him at his home to discuss this project he showed me many things that he had fabricated out of stainless steel. He made a maple syrup vat, a hood for his cooking range, a wood stove...and decorative items as well. Impressive work and beautiful to look at, all with the handicap of only having two fingers on each hand. He has a great imagination and right away he started his inventive thinking process with the design of the livestock manure press.
There were 2 phases to this project. 1. Build the press that makes the bricks. 2. Make the bricks. Dry the bricks. Burn the bricks. Test the bricks for content and moisture percentages for best burn quality.
I have included are photos of the building phase with captions detailing the process. The livestock manure press is now completed. Anyone interested can contact the fabricator for more details or questions.
The total cost of equipment and materials is listed here:
Honda OHV engine 270cc GX series 8.5 hp was recommended for enough power to compress the blocks. 557.98 There are certainly many other choices.
Hydraulic cylinder - 3000 PSI 2” bore, 10” stroke to open the door to let the brick out of the press: 97.99
Hydrauluc cylinder - 3000 PSI 5” bore, 24” strike to press the bricks: 309.99
Hydrauluc pump: 189.99
Spool lever operated valve to move the cylinder: 204.21
Hoses and parts: 67:18
Steel parts and Spindle: 477.66
Bolts, nuts, washers, coupling spider, couplings: 67.87
Ball hitch: 17.98
Cans of black paint: 6.42
Steel for fabrication: 120.00
Hoses and parts: 67.18
Oil filter and misc. parts: 27.59
Pipe and fender washers: 12.62
Clamps etc. 41.07
Stainless steel for hydraulic fluid tank: 60.00
parts for hydraulic set up: 42.53
Notebook for manual: 6.37
Fabricator labor for 146.5 hours for making and assembling parts: 3,662.50
Here are a few photos of assembly of the press.
In the second phase we practiced making manure bricks and to developed recipes that would meet the standards of a brick designed for maximum burn density. The basic ingredients are livestock manure, bedding such as straw, or wood shavings, and water. I will document the process to find what works best. Next the bricks were dried for 2-3 weeks in an environment free from rain. In this case, under tarps on racks. A hoop house would be ideal, which we intended to do but have moved to our new farm where there is no hoop house.
The best sample was sent to a bio mass testing lab for analysis of moisture and matter content.
In early 2017 we began designing the press. All set to build and my fabricator Steve Lonsky fell from his tractor and broke his foot. The building of the press was postponed until August. We built the press, and by early November we had one on-farm demonstration of the press with a mixed group of small farmers and interested residents. We made a few trial bricks to primarily test the functioning of the press.
We were fortunate to complete the press and have one successful demonstration before my husband, myself, 12 cows, 8 chickens, 6 dogs and 2 cats and all our cheese making and farm equipment moved to Texas from New York state where the project started.
We collected manure from the stall floors and lane ways of our micro-dairy barn in New York state to use in the press as well as at our new farmstead in Texas, where we moved in November 2017. Heating value of livestock manure is known to be comparable to grass/wood/other biomass materials used in commercial fuel bricks. We had hoped to set benchmarks for contents and drying standards for the briquette. High heating value (BTU/lb.) is required to provide a long lasting fire in a wood stove.
When we arrived in late November, 2017 we realized we did not have enough manure from our cows to make the bricks. But by diligently using our “poop scoop” we accumulated a decent enough pile including straw bedding to proceed.
We want to emphasize that we were fortunate that Fabricator Steve Lonsky took on this project with fervor and produced a physically strong and capable piece of machinery that did what we set out to accomplish.
In an ideal world, I would be a trained mechanical engineer and would describe the process as if taking it to the patent office. That is beyond the scope of this SARE grant unfortunately. But hopefully we have detailed the construction of the press Enough so that it can be reproduced. We can be reached for questions at [email protected] and Steve Lonsky can be reached at [email protected]
In the second phase, we are trying to make the best fuel brick for the purpose of burning in a wood stove or fire place for heat or for cooking, documenting all work and publishing the results so that other interested farmers and homeowners with a beautiful abundance of livestock manure can make their own press.
We began with several trial runs. Mixtures of different amounts of dry manure with bedding, fresh manure and water to make the manure briquette. The criteria for excellence is that, number one, the briquette must hold together so that it can be handled and set to dry. If too moist they will not survive the pressing, if too dry, or not well mixed, containing pockets of dry and wet, they will crumble during handling as they exit the press.
Trial runs and results (note that measurements were not exact or perfect, but approximate.
#1. 6 shovels of dry manure/bedding
6 shovels fresh manure
1 gallon water
Mix together in a wide mouth feed bucket and stir until you have a well blended mix.
This trial made us aware of the importance of water in the mix. The water should be enough to hold the briquette together but not more. The drying happens after the briquette is pressed and set to dry. That is an important point because too little water will cause the brick to crack and break.
Result: these bricks held together fairly well although they appeared too loosely knit for the drying period. Also we did not use full compression.
Two briquettes were made.
#2. 4 shovels of dry manure/bedding
1.5 shovels of fresh manure were wetted down with with additional water prior to adding to dry.
1 gallon of water.
The mixture was hand formed before dropping into the hopper. Then we used almost 100% compression.
This pressing was wetter than the first one and we were made aware of issues with the manufacturing of the press. Where the top of the expulsion door of the press meets the mold box, there is a space that should have been filled in. Because we moved we could not ask Steve, our fabricator to weld a piece to tighten up the hole, so we began to improvise using wood and plastic objects to block the space so the manure mix would stay in the box and not squish out. We also started covering it with a tarp as we pressed because a manure shower was not so welcome!
#3. Same mix as in #2.
Wood shims were put into the hole on the press. Less compression. The briquette did not hold together well. Too much moisture. We lost much of it through the intentional spaces of the press designed to let out moisture.
#4. 3 shovels dry manure/bedding
2 shovels fresh manure
1/2 gallon water
We made one large briquette with this trial. It did not hold together well due to size and lack of water. We realized during this trial it is better to make a briquette 4” - 5” thick rather than 7” - 8” thick. Easier to form and handle. The down side of this is that the briquette will not have as much burn time.
#5. Sifted dry manure/bedding and mixed with water: 1 to 1 ratio. Mixed well . Add to fresh manure in this trial was a few days older than previous trials.
I put on my gloves and mushed it all together as if making bread. It was important to make sure all moisture touches all dry ingredients so no cracking and breaking.
A mechanical mixer would be great for this process to expediate mixing. There are mixers available. They are typically used in animal feed production. I found some available online, but only sold in other countries.
we ran one trial with half a batch and it was too moist. So we added more dry and fresh manure. The second batch and got a really nice small briquette.
Because in all these trials we were hesitant to use full compression because of the fault in the expulsion door area allowing too much mixture to escape, we tried putting the contents of the mixture in a plastic bag to contain it and prevent lose of moisture. It formed better briquettes that held together better.
The plastic bag has limitations in that air pockets form and pop, defeating the purpose of containment.
We tried fabric screening with better results.
our best results were when the contents of ingredients were thoroughly mashed. When doing large volumes of material it is advisable to use a mixer.
After several attempts to wrap each briquette in a fabric screening, the best result we achieved was to place the screen across the end of the press to trap the solids inside the pressing chamber and also allow the excess liquid out of the press.
The results were considerably more consistent and the quality of the briquette was denser and more uniform.
Drying the briquettes:
Drying the briquettes can take many forms. Ideally you want good air flow, sunshine for drying and no rain interfering with the process. We set up the wet briquettes on a screen so that they had air flow from beneath as well as on the sides and top. The weather was very dry during the drying periods at first. This was excellent and produced very dry results. We had difficulty when the weather changed. We covered the bricks with a tarp to keep them out of the rain and figured that would be sufficient to keep them dry until sunnier days arrived, but unforeseen issues arose when we checked the briquettes after a few weeks during the rainy period. They did not get wet, but because we placed the rack to close to the ground, approximately 1 ft. above the ground, we had an infestation of red ants, grubs, centipedes, as well as mushroom spores and other microbial growth. That was a shock! We savaged the best samples to send off for testing. Moral of the story is: put your briquettes up high to dry, preferably dry them in a greenhouse or hoop house if you can away from moisture, and turn the often.
The challenges faced with faults in the press manufacture (described above) have influenced the expected results. The hope was to get a very dense briquette and to be able to rapidly replicate the product. A denser briquette would yield a longer burn time. Consistency in brick formation also was compromised because of the large spaces in the press that had to be filled in so materials would stay in place and withstand full compression. This issue will have to be corrected if one is to copy the design of this press.
Briquette drying time and method will require conditions that will be different with respect to local. In the northeast the racks will Best be located in a hoop house or green house so that rain and humidity can be controlled. They need to be turned frequently and when completely dry, stacked away from moisture high enough off the ground to prohibit mold growth and insect infestation.
The first few briquettes were extremely wet. We were surprised when the press, in all its strength, shot wet manure up into the air, then rained down a manure shower on all recipients heads during our first demonstration! Many squeals could be heard! Those first samples were too wet. We refined the recipe many times using less water, more manure and bedding which yielded variations of briquettes that were too firm, would crack and not hold their shape. Initially unmixed manure was put into the press hopper and pushed down to meet the hydraulic press. This method of preparation did not work. It was too dry and clumpy. Manure with less bedding (consisting of straw and hay stepped on by our cows in their corral) was tried and stirred to make a more consistent concoction in a bucket so that it is more uniform going through the press.
TESTING
After discussing with Twin Lab tech what sample type to send for analysis, I sent various pieces of briquettes from different pressings representing different densities and dryness, weighing a total of 4lbs.
Twin Labs tested for:
1. Moisture: We test for moisture because water does not burn. Any moisture in a fuel brick product will lower the efficiency of the fuel and the BTU value. A good reason to “season” wood or livestock Manure briquettes before burning.
The lab tested for total moisture by weight percentage of the “as received” sample. Because I sent sample material that was 71% moist, not as dry as it should have been, but because I wanted a well represented sample, the “as received” sample moisture content was higher than it should have been. (A home drying process, explained later, was done to get a more true value of moisture content in the briquette sample and thus, BTU value for the livestock manure briquettes). Twin Labs did achieve a BTU value based on a fully dry sample, zero moisture, because they dried all sample matter before getting their sample results.
2. Ash: Ash is what is left over when you burn a fuel briquette. As with moisture, we measure ash by weight percentage of sample. This test tells us that for every lb. of fuel we burn, we will have to clean out a percentage of ash from the fire pit, stove or whatever burning equipment we use. It impacts maintenance.
3. Sulfur: Sulfur levels are of concern for those who have to meet emission standard requirements to filter out sulfur dioxide gassed from fuel material. It is measured as a weight percentage in the sample.
4. Gross Caloric Value: This value represents the actual heating value in the sample on an “as received” basis, and a moisture free (dry) basis.
5. Chlorine: Chlorine in a sample is measured in mg/kg (parts per million). Chlorine is of concern because it changes to Hydrogen Chloride when it is combusted, which forms Hydrochloric acid when it condenses into parts of a stove /boiler/any cooking vessel. This acid corrodes the furnace and can cause premature failure of the system if the furnace equipment is not built to withstand it.
The test results and analysis are included in the Research Conclusion.
The first step in this project was to fabricate the livestock manure press based on a need to make functional use of livestock manure that may be more abundant than needed on a small farm. Based on research, help from my tech advisor Chris Callahan, and my ingenious fabricator Steve Lonsky, the hydraulic press has been completed except for the installation of the small hydraulic cylinder that opens and closes the door where the manure brick expels from the press. The press is functional, we have had a successful demonstration of the making and operating of the press.
Following are photos of the completed press in detail:
Pump, fluid reservoir and engine attachment all attachments mounted on fabricated plate mounted on I Beam
The second part of this project was to make briquettes and evaluate them as a fuel source.
TEST ANALYSIS AND RESULTS:
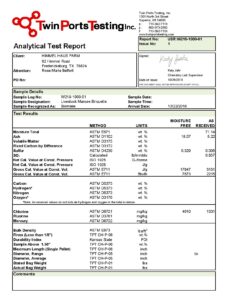
As stated above, Twin Ports Lab tested for:
Moisture: The “as received” sample moisture percentage was 71.14%. Very high because of the sample I submitted. The BTU value at this percentage is 2215/lb. They also tested for moisture after they dried the sample resulting in zero moisture. BTU value is 7,673 BTU/lb. A significant increase yielding a much more eglfficient burn.
My advisor, Chris Callahan suggested we do a home dry process to get a more realistic value. In real life it would be difficult to achieve a zero moisture value, and most likely on the other end of the tested spectrum, one would not be burning a fuel briquette with 71.14% moisture retained. So we used a known process to dry the sample at home.
I weighed the initial small crushed sample of dry livestock manure briquette that we processed. 0.095 lbs. starting wt. The sample was heated in a microwave oven at 1 minute intervals 3 times, and then for 3 second intervals until the wt. stayed the same for 4 weighings to make sure the wt. was stable. The final wt. was 0.085. Moisture content was 0.01 lbs. = 10.5% moisture content of sample.
Resulting Heating Value of briquettes from this test:
For each lb. of briquette produced based on this sample test (see chart below):
There is 0.11 lbs. water in sample. 0.89 lbs of sample is dry wt.
We know that a 100% dry briquette sample will have a BTU/lb. value of 7,763. In this home processed sample, due to the percent dry matter displaced by the percent moisture, we lose 817 BTU’s, and we also lose 105 BTU/lb. that are needed to evaporate the water off the briquette. That leaves a BTU/lb. value of 6,841. As we can see, the dryer our fuel is before burning, the better.
Compared to dry wood which can range anywhere from approximately 2,000 BTU/lb. down to 5,000 BTU’s, livestock manure pressed briquettes rate very well. Compared to some other fuels, including other biomass fuels, tested in a bioenergy initiative study by Chris Callahan at the University of Vermont, the BTU/lb., or energy density value for livestock manure is low in comparison to other fuels he has tested. But the energy cost ($/million BTU/lb.) to produce is fantastic for a small farm already rich in livestock manure (see calculation in summary below).
A few BTU/lb. values from Chris Callahan’s study, assuming all values are based on 100% moisture free samples:
Wood pellets: 8,600
Switchgrass pellets: 8,353
Reed Canary pellets: 7,898
Mulch Hay pellets; 7,952
Livestock Manure briquettes: 7,763
See chart regarding above discussion:
Moisture Testing | ||
Initial Sample Weight | 0.095 | lbs, at the very start, as produced using your methods |
Final Sample Weight | 0.085 | lbs, after drying for this test, once the measured weight no longer changes |
Moisture content | 0.01 | lbs of water in initial sample |
Moisture content | 10.5% | % moisture content in initial sample (as produced using your methods) |
Heating Value of Bricks | ||
BTU/lb | 7,763 | when 100% dry, lab result from Twin Ports |
% mc | 10.5% | as produced using your methods, using your % mc test result |
For each pound of brick as produced | ||
You have | 0.11 | lbs in water |
So you have | 0.89 | lbs dry |
You lose | 817 | BTU's due to the dry matter displaced by the water |
and also lose | 105 | BTU's that are needed to evaporate the water in the brick |
You are left with | 6,841 | BTU's per pound of brick as produced. |
BTU/lb | 6,841 | as produced using your methods |
SUMMARY:
This project, Livestock Manure Press Design and Manufacturing of a Fuel Briquette, demonstrates the ability to make a fuel product that can make use of surplus livestock manure on a small farm. A design to construct a press, a method to produce the briquette, a BTU/lb. value, and cost of production have been established and shown in pictures and a list of parts for fabrication with costs.
Challenges we faced were in the design of the press primarily. We did not account for the intense pressure the hydraulics put on the briquette, causing too much liquid to escape the press. Smaller spaces should have been in the area where the livestock manure is pressed so that the briquette could have maintained its shape. The solid materials were squeezing out of the spaces that were too large. We addressed these issues by using household objects to block up the holes. Theoretically we should have had denser briquettes, and perhaps our BTU/lb. values could have been higher.
Briquettes were sufficiently dried to achieve a fairly competitive BTU/lb. value compared to other biomass fuel products. Challenges associated with drying were unexpected weather challenges and insect infestation. But overall, a firm, dense briquette form was achieved.
Samples of briquettes were sent to the Twin Ports lab for analysis. Standards were set for the briquette we manufactured (see lab results chart). The Ash level (18% dry weight) is a bit high and will require more clean up when compared values for cord wood or wood pellet fuels.
Cost of production: The press cost $2,374.63 to construct which included all new materials except for tires. The cost could be considerably less if on farm equipment already in hand would have been used. One could also, with welding skills, modify a woodsplitter to have a dual purpose machine.
A typical briquette size is: 7” high x 9” wide x 9” long. The dry weight is approximately 3 lbs. for a briquette that size. Estimated cost per 1 hour of production includes: cost of gasoline to run the engine @ $1.80 for estimated half gallon; $.30 for hydraulic and motor oil = $2.10 per hour. One hour of production would yield approximately 30 - 3 lb. briquettes = 90 lbs of fuel burning material. Estimated cost per lb. to produce is $.023.
Based in these results we conclude that livestock manure briquettes are a feasible fuel for the small farmer who has more manure than she/he knows what to do with and a willingness to handle this type of solid fuel and associated ash cleanup.
One thing that delights me in end result is the firmness of the briquette. After 6 weeks of drying the briquette holds together much better than expected and would hold up in a racquet ball game I’m sure. When trying to make a small sample for the home drying process I had to take a hammer to the briquette to break off a sample wt. piece. That’s a good quality to have for storing briquette after the drying period.
When burning the briquettes give off a very earthy and pleasing smell. One thing we thought to do was to add juniper leaves or other aromatic plants that would be available in the farm so to add to the aroma while burning.
Education & Outreach Activities and Participation Summary
Participation Summary:
When the livestock Manure press was completed in November of 2017 we had an educational demonstration/tour for 4 farmers and several other members of the community on our farm in King Ferry NY. The farmers present were a dairy farmer, hay producer, beef producer and honey producer. It was not advertised or public ally announced. The group came together by word of mouth. Fabricator Steve Lonsky was there to discuss the design and build of the press. He did our first brick making session with a mixture of manure from our Dexter cows and bedding straw. The percentage of moisture was very high and the bricks were too soft. There was no pre-calculation involved regarding ratio of water to manure and straw. The presentation was meant to be an initial run through to primarily demonstrate the building and use of the press.
A press release* was circulated with a link to this report to:
-Cornell Small Farm Journal, Deliberate Agrarian blog by Herrick Kimball, Acres USA, Advisor Chris Callahan’s blog, Farm Energy Facebook page. It is being uploaded to FarmHack and has been sent to at least one Farm Show in the Northeast.
*Briquetting-a-Better-Burnable-Cow-Patty
Learning Outcomes
Four farmers were at our initial presentation/tour/educational demonstration of our livestock manure press. They we’re very interested in the concept of making use of manure to create a functional product. It was a foreign idea to most of those who were there, but one farmer was familiar with practices using manure in other countries. There was peaked interest in the design of the press and it’s capability to hydraulically have enough power to form the bricks in relation to engine size and power. This press is also designed to split logs and has a splitter blade that can be installed when not using it to make bricks. We also discussed the potential ability to make and dry bricks for structural uses on the farm, such as for sheds or housing for small livestock. Well have to wait for feedback from educational outreach when we have more product to demonstrate before we know what impact it will have on a small farming community.
Project Outcomes
We now are using this press on our farm in Texas.
Here are some pages that could go in a manual:
This set of photos is from a rudimentary manual that we put together during the building process of the press. Addtional photos and videos will be added to support the design process to assist others who might want to build a similar press. The level of detail described to design the press is limited, and not what would be expected from a mechanical engineer perspective or for patent requirements. We do hope a creative farmer/welder can extrapolate from this model enough detail to build one similar to this press. More details on Fabricator Steve Lonsky’s concepts of pressure may be required to make a compressed brick later. More info will be added.
The livestock manure press has been completed except for the small hydraulic cylinder that opens and closes the door that releases the brick from the press. The door can manually be opened and closed with pins, but is cumbersome and not an efficient process.
The press has been demonstrated to a small group of interested farmers and others to work as expected. We are now fine tuning the recipe to create an optimum brick for fuel burning.
We have successfully relocated our farm to Texas along with our Dexter cattle business, now called Himmel Haus Farm at Quarry Hill.